Bedeutende Meilensteine in der Entwicklung der Elektronik kann man auch im Schweizer Museum für Kommunikation erkennen
Bedenkt man nur: Wer in den 1950er-Jahren einen Computer möchte, der muss ihn selbst entwickeln.
leiterplatten lexikon
Begriffe im Zusammenhang mit dem Leiterplattenentwurf
Entwickeln Sie elektronische Geräte und suchen nach einem Partner für Prototypen oder Kleinserien? Wir begleiten Sie von der Ideenfindung über die Entwicklung bis zur Fertigung und dem funktionsfähigen Muster. Erfahren Sie auch, welche Schritte erforderlich sind, um den Fertigungsprozess effizient zu gestalten.
Unabhängig davon, ob Sie Leiterplatten entwerfen oder bestellen: Die Vielzahl an Begriffen im Zusammenhang mit dem Leiterplattenentwurf und der Produktion kann oft unübersichtlich und verwirrend sein.
Deshalb möchten wir Ihnen eine Hilfestellung bieten: Unser neues Leiterplatten-Lexikon erklärt die wichtigsten Begriffe und macht den Sachverhalt auch im Zusammenhang verständlich.
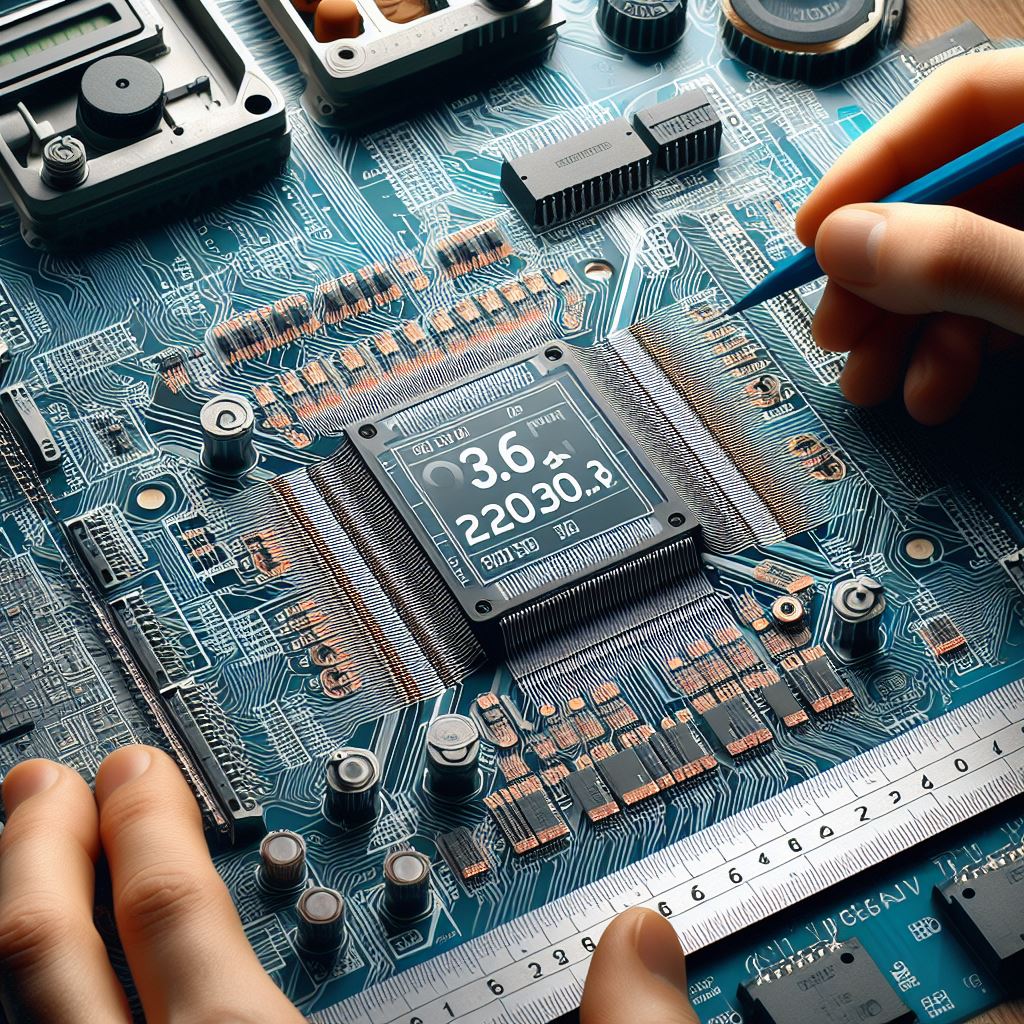
- A – Z
- ABFASEN
- ABSCHIRMUNG
- ABZIEHLACK
- ADAPTERTEST
- ÄTZEN
Abfasen bei Leiterplatten bezieht sich auf einen Bearbeitungsschritt, bei dem die Kanten einer Leiterplatte abgeschrägt oder abgerundet werden. Diese Technik wird verwendet, um scharfe Kanten zu entfernen und die Leiterplatte zu schützen oder zu verbessern. Hier sind die wichtigsten Aspekte des Abfasens:
Zweck des Abfasens
Schutz vor mechanischen Schäden:
- Entfernung von scharfen Kanten: Abfasen hilft, scharfe Kanten zu entfernen, die beim Umgang mit der Leiterplatte oder beim Einbau in Gehäuse zu Beschädigungen führen könnten.
Vermeidung von Kurzschlüssen:
- Schutz der Leiterbahnen: Durch das Abfasen wird das Risiko reduziert, dass Leiterbahnen oder andere empfindliche Teile der Leiterplatte beschädigt oder kurzgeschlossen werden.
Erleichterung der Montage:
- Bessere Passform: Abfasen kann dazu beitragen, dass die Leiterplatte besser in Gehäuse oder Montageschlitze passt und so die Montage erleichtern.
Verbesserung der Ästhetik:
- Optische Verbesserung: Abgerundete oder abgeschrägte Kanten können das Erscheinungsbild der Leiterplatte verbessern und eine professionellere Optik verleihen.
Abfasentechniken
Mechanisches Abfasen:
- Schleifen oder Fräsen: Mechanische Werkzeuge wie Schleifmaschinen oder Fräsmaschinen werden verwendet, um die Kanten der Leiterplatte abzuschrägen. Dies kann manuell oder automatisiert erfolgen.
Chemisches Abfasen:
- Ätzen: In einigen Fällen kann ein chemischer Prozess verwendet werden, um die Kanten abzurunden. Dies erfolgt durch gezielte Ätzung der Kanten, um eine abgeschrägte Form zu erhalten.
Prozess des Abfasens
Designüberlegungen:
- Festlegung der Kantenbearbeitung: Bereits in der Designphase sollte entschieden werden, ob und wie die Kanten der Leiterplatte bearbeitet werden. Dies kann durch entsprechende Designregeln und Spezifikationen in der Leiterplattendokumentation erfolgen.
Bearbeitungsverfahren:
- Wahl der Methode: Die Wahl der Abfasentechnik hängt von den spezifischen Anforderungen der Leiterplatte, dem Material und der geplanten Anwendung ab. Mechanisches Abfasen ist die gängigste Methode.
Qualitätskontrolle:
- Überprüfung der Kantenbearbeitung: Nach dem Abfasen sollten die Kanten auf Gleichmäßigkeit und Qualität überprüft werden, um sicherzustellen, dass die Bearbeitung den Anforderungen entspricht.
Vorteile des Abfasens
- Erhöhte Sicherheit: Abgerundete Kanten reduzieren das Risiko von Verletzungen oder Beschädigungen beim Handling und Einbau der Leiterplatte.
- Verhinderung von Abrieb: Abgefasste Kanten können helfen, Abrieb an Gehäusen oder anderen Komponenten zu vermeiden.
- Bessere Montage: Die Kantenbearbeitung kann die Passgenauigkeit und den Montagekomfort verbessern.
Nachteile des Abfasens
- Zusätzliche Kosten: Das Abfasen fügt zusätzliche Schritte und Kosten im Herstellungsprozess hinzu.
- Komplexität: Bei sehr präzisen Anforderungen oder komplexen Leiterplattenlayouts kann das Abfasen zusätzliche Herausforderungen mit sich bringen.
Anwendungen
- Gehäusemontage: Besonders wichtig bei Leiterplatten, die in Gehäusen oder Befestigungssystemen montiert werden, um eine bessere Passform und Sicherheit zu gewährleisten.
- Prototypen: Oft bei Prototypen verwendet, um mögliche Designfehler oder Kantenprobleme vor der Serienproduktion zu identifizieren und zu beheben.
Zusammengefasst ist das Abfasen eine wichtige Bearbeitungstechnik in der Leiterplattenfertigung, die darauf abzielt, Kanten zu glätten, mechanische Schäden zu vermeiden und die Montage zu erleichtern. Es erfordert sorgfältige Planung und Ausführung, um die besten Ergebnisse zu erzielen.
Abschirmung bei Leiterplatten ist eine Technik zur Minimierung der elektromagnetischen Interferenzen (EMI) und zum Schutz empfindlicher Schaltungen vor äußeren Störungen. Sie dient dazu, die Leistung der Leiterplatte zu verbessern und die Signalqualität zu sichern, indem sie elektromagnetische Störungen kontrolliert oder verhindert.
Ziele der Abschirmung
Reduzierung der elektromagnetischen Interferenzen (EMI):
- Schutz vor externen Störungen: Verhindert, dass externe elektromagnetische Störungen die Leiterplatte beeinflussen und die Funktionalität der Schaltungen beeinträchtigen.
- Vermeidung von Störungen: Reduziert die Abstrahlung von elektromagnetischen Störungen durch die Leiterplatte selbst, die andere elektronische Geräte beeinflussen könnte.
Signalqualität verbessern:
- Minimierung von Signalverlusten: Schützt empfindliche Signalübertragungen vor Störungen und Verzerrungen, die die Signalintegrität beeinträchtigen könnten.
Einhalten von Vorschriften:
- Compliance mit Standards: Sicherstellt, dass die Leiterplatte den gesetzlichen Vorschriften und Normen für elektromagnetische Verträglichkeit (EMV) entspricht.
Methoden der Abschirmung
Abschirmungen durch leitfähige Schichten:
- Metallische Abdeckungen: Eine häufige Methode besteht darin, eine leitfähige Schicht oder Abdeckung auf die Leiterplatte aufzubringen. Dies kann durch ein vollständig umschließendes Metallgehäuse oder durch spezifische Abschirmbleche geschehen.
- Abschirmfolien: Aufgebrachte metallische Folien (wie Kupfer- oder Aluminiumbeschichtungen) können auf der Leiterplatte oder um sie herum angebracht werden, um Störungen zu verhindern.
Abschirmung durch Leiterbahn-Design:
- Ground Plane: Die Verwendung einer Ground-Plane oder Massefläche auf der Leiterplatte kann helfen, elektromagnetische Störungen zu reduzieren, indem sie als eine Art Abschirmung wirkt und gleichzeitig die Signalqualität verbessert.
- Störabstand: Strategisches Routing von empfindlichen Signalen und Platzierung von Bauteilen kann dazu beitragen, Störungen zu minimieren.
Abschirmung durch Gehäuse:
- Metallgehäuse: Die gesamte Leiterplatte kann in ein Metallgehäuse eingebaut werden, das als eine effektive Abschirmung gegen externe Störungen dient.
- Gehäuseabschirmungen: Gehäuseabschirmungen können speziell entwickelt werden, um bestimmte Frequenzbereiche zu blockieren und die EMV-Eigenschaften zu verbessern.
Abschirmung durch spezielle Materialien:
- Absorptionsmaterialien: Materialen wie Ferritabsorbierer oder spezielle Beschichtungen, die elektromagnetische Wellen absorbieren, können verwendet werden, um Störungen zu reduzieren.
- Kombinierte Materialien: Die Kombination von verschiedenen Materialien wie leitfähige Schichten und absorbierende Materialien kann besonders wirksam sein.
Gestaltung und Implementierung
Designüberlegungen:
- Platzierung: Die Platzierung von Abschirmmaterialien und -elementen sollte im Designprozess berücksichtigt werden, um die besten Ergebnisse zu erzielen.
- Thermische Überlegungen: Einige Abschirmmaterialien können die Wärmeableitung beeinflussen, daher sollte dies im Design berücksichtigt werden.
Fertigungsprozess:
- Integration in die Produktion: Abschirmungselemente müssen in den Fertigungsprozess integriert werden. Dies kann die Beschichtung der Leiterplatte oder das Hinzufügen von Gehäusen umfassen.
Testen und Validierung:
- EMV-Tests: Nach der Fertigung sollte die Leiterplatte getestet werden, um sicherzustellen, dass sie den EMV-Anforderungen entspricht. Dies kann durch spezielle Tests wie das Messen der Abstrahlung und der Immunität gegen externe Störungen erfolgen.
Vorteile der Abschirmung
- Verbesserte Leistung: Reduziert die Auswirkungen von EMI und verbessert die Signalqualität und Systemstabilität.
- Einhaltung von Vorschriften: Hilft dabei, gesetzliche Anforderungen und Normen für elektromagnetische Verträglichkeit zu erfüllen.
- Zuverlässigkeit: Erhöht die Zuverlässigkeit und Langlebigkeit von elektronischen Geräten durch Schutz vor Störungen.
Nachteile der Abschirmung
- Zusätzliche Kosten: Die Implementierung von Abschirmungslösungen kann zusätzliche Kosten für Materialien und Fertigungsprozesse verursachen.
- Designkomplexität: Kann die Komplexität des Leiterplattendesigns erhöhen und zusätzliche Planungsaufwände erfordern.
Zusammengefasst ist die Abschirmung von Leiterplatten eine kritische Maßnahme zur Gewährleistung der elektromagnetischen Verträglichkeit und zur Verbesserung der Signalqualität. Durch sorgfältige Auswahl und Integration von Abschirmmethoden kann die Leistung und Zuverlässigkeit von elektronischen Geräten erheblich verbessert werden.
Abziehlack auf Leiterplatten ist ein spezieller Lack, der auf die Leiterplatte aufgetragen wird, um die Entfernung von bestimmten Teilen des Leiterplattenmaterials zu erleichtern, insbesondere während der Herstellung oder Verarbeitung. Er spielt eine Rolle beim Schutz und der Bearbeitung der Leiterplatte in verschiedenen Phasen der Produktion. Bei Wellenlöten oder Schwalllöten werden Abziehlacke gerne eingesetzt.
Funktionen des Abziehlacks
Schutz während der Bearbeitung:
- Vermeidung von Schäden: Der Abziehlack schützt Bereiche der Leiterplatte, die während des Ätzprozesses nicht entfernt werden sollen, vor chemischen Angriffen. Dies verhindert, dass unerwünschte Bereiche des Kupfers entfernt werden und stellt sicher, dass nur die vorgesehenen Leiterbahnen und Verbindungen geätzt werden.
Einfache Entfernung:
- Leichtes Abziehen: Der Abziehlack kann nach der Bearbeitung leicht entfernt werden. Dies ermöglicht eine einfache und saubere Entfernung des Schutzmaterials, ohne die darunter liegende Leiterplatte zu beschädigen.
Verhinderung von Kontamination:
- Schutz vor Verunreinigungen: Während des Bearbeitungsprozesses schützt der Abziehlack die Leiterplatte vor Verunreinigungen, die die Qualität der Leiterbahn und der Lötverbindungen beeinträchtigen könnten.
Arten von Abziehlack
Temporäre Abziehlacke:
- Auftrag und Entfernung: Diese werden aufgetragen, um die Leiterplatte während der Produktion zu schützen und später durch mechanische oder chemische Verfahren entfernt. Sie sind meist leicht abziehbar und hinterlassen keine Rückstände.
Lösemittelbasierte Abziehlacke:
- Lösungsmittel: Diese Lacke enthalten Lösungsmittel, die sie leicht ablösbar machen. Sie werden häufig in der Leiterplattenfertigung verwendet, insbesondere bei der Verarbeitung von Leiterplatten mit komplexen Layouts.
Wasserbasierte Abziehlacke:
- Umweltfreundlicher: Diese Lacke sind auf Wasserbasis formuliert und bieten eine umweltfreundliche Alternative zu lösungsmittelbasierten Lacken. Sie können jedoch spezielle Anforderungen an die Trocknung und Entfernung stellen.
Anwendung des Abziehlacks
Auftragen:
- Verfahren: Der Abziehlack wird üblicherweise durch Sprühen, Streichen oder Drucken auf die Leiterplatte aufgetragen. Die Methode hängt von der Art des Lacks und den spezifischen Anforderungen des Herstellungsprozesses ab.
Bearbeitung:
- Ätzen: Während des Ätzvorgangs schützt der Abziehlack bestimmte Bereiche der Leiterplatte, während andere Bereiche durch das Ätzmittel entfernt werden.
Entfernung:
- Mechanisch oder chemisch: Nach Abschluss der Bearbeitung wird der Abziehlack durch mechanische Mittel wie Abkratzen oder durch chemische Reinigungsmittel entfernt, um die fertige Leiterplatte freizulegen.
Vorteile des Abziehlacks
- Schutz der Leiterplatte: Schützt Bereiche der Leiterplatte vor unerwünschter Entfernung von Kupfer oder anderen Materialien.
- Verbesserung der Verarbeitungsqualität: Hilft, präzise Leiterbahnen und Verbindungen zu erhalten, indem nur die vorgesehenen Bereiche bearbeitet werden.
- Einfache Entfernung: Der Abziehlack lässt sich nach der Bearbeitung einfach und sauber entfernen.
Nachteile des Abziehlacks
- Zusätzliche Produktionsschritte: Der Einsatz von Abziehlack kann zusätzliche Schritte im Produktionsprozess erfordern, einschließlich Auftragen, Trocknen und Entfernen des Lacks.
- Kosten: Kann zusätzliche Kosten für Materialien und Verarbeitung verursachen.
- Verarbeitung: Erfordert sorgfältige Anwendung und Entfernung, um eine vollständige und saubere Bearbeitung der Leiterplatte zu gewährleisten.
Anwendungen
- Fertigung von Leiterplatten: Wird in der Leiterplattenfertigung verwendet, insbesondere beim Ätzen und bei der Herstellung komplexer Schaltlayouts.
- Prototypen: Nützlich bei der Erstellung von Prototypen und in der Forschung und Entwicklung, um präzise und fehlerfreie Leiterplatten zu gewährleisten.
Zusammengefasst ist der Abziehlack ein wesentlicher Bestandteil der Leiterplattenfertigung, der zum Schutz und zur Bearbeitung von Leiterplatten verwendet wird. Er ermöglicht eine präzise Bearbeitung und schützt gleichzeitig empfindliche Bereiche der Leiterplatte vor Beschädigungen.
Vgl. auch → Wellenlöten
Der Adaptertest bei Leiterplatten ist eine Prüfungstechnik, die verwendet wird, um die elektrische Integrität von Leiterplatten nach der Herstellung sicherzustellen. Diese Methode wird häufig in der Fertigung von Leiterplatten verwendet, um sicherzustellen, dass alle elektrischen Verbindungen korrekt sind und keine Fehler wie Kurzschlüsse oder Unterbrechungen vorliegen.
Was ist ein Adaptertest?
Der Adaptertest ist eine Form des elektrischen Tests, bei dem spezielle Adapter verwendet werden, um elektrische Verbindungen zu überprüfen. Diese Adapter sind maßgeschneiderte Vorrichtungen, die auf die spezifischen Anforderungen und Layouts der Leiterplatte abgestimmt sind.
Wie funktioniert der Adaptertest?
Adapterherstellung:
- Design und Fertigung: Ein Adapter wird entwickelt, der genau auf die Leiterplatte abgestimmt ist. Dieser Adapter besteht aus einer Reihe von Nadelsonden oder Kontaktpunkten, die mit den entsprechenden Leiterbahnen auf der Leiterplatte in Kontakt treten.
Testvorgang:
- Konnektivitätstest: Der Adapter wird auf die Leiterplatte aufgesetzt, und elektrische Tests werden durchgeführt, um sicherzustellen, dass alle Verbindungen korrekt sind. Dies umfasst die Überprüfung von Leitungen auf Kurzschlüsse, Unterbrechungen oder andere elektrische Fehler.
- Automatisierung: Der Testprozess kann manuell oder automatisiert durchgeführt werden. In vielen modernen Fertigungsumgebungen werden automatische Testsysteme verwendet, um die Effizienz und Genauigkeit zu erhöhen.
Ergebnisse und Analyse:
- Fehlererkennung: Die Testergebnisse werden analysiert, um festzustellen, ob es Probleme wie Kurzschlüsse, Unterbrechungen oder fehlerhafte Verbindungen gibt. Fehlerhafte Leiterplatten werden identifiziert und aussortiert oder zur weiteren Reparatur und Untersuchung weitergeleitet.
Vorteile des Adaptertests
Hohe Testabdeckung:
- Vollständige Prüfung: Adaptertests ermöglichen eine umfassende Prüfung aller elektrischen Verbindungen auf der Leiterplatte, was zu einer hohen Testabdeckung führt.
Effizienz:
- Schnelligkeit: Adaptertests können oft schneller durchgeführt werden als manuelle Tests, besonders bei großen Stückzahlen von Leiterplatten.
Genauigkeit:
- Fehlererkennung: Da der Adapter speziell auf die Leiterplatte abgestimmt ist, können Fehler genau und zuverlässig erkannt werden.
Nachteile des Adaptertests
Kosten:
- Adapterfertigung: Die Herstellung von Adaptern kann kostspielig sein, insbesondere wenn viele unterschiedliche Adapter für verschiedene Leiterplattendesigns benötigt werden.
Vorbereitungsaufwand:
- Design und Herstellung: Der Prozess der Anpassung und Herstellung von Adaptern kann zeitaufwändig und komplex sein.
Begrenzte Flexibilität:
- Designanpassungen: Adapter sind oft spezifisch für ein bestimmtes Leiterplattendesign und können bei Änderungen im Design möglicherweise nicht mehr verwendet werden.
Anwendungen des Adaptertests
Serienproduktion:
- Massenproduktion: Besonders nützlich in der Serienproduktion, wo große Mengen von Leiterplatten getestet werden müssen.
Prototypenfertigung:
- Fehlerbehebung: Wird auch in der Prototypenfertigung eingesetzt, um frühe Fehler im Designprozess zu identifizieren.
Qualitätssicherung:
- Endkontrolle: Dient als ein wichtiger Schritt in der Qualitätskontrolle, um sicherzustellen, dass nur fehlerfreie Leiterplatten weiterverarbeitet oder ausgeliefert werden.
Fazit
Der Adaptertest ist eine präzise und effektive Methode zur Überprüfung der elektrischen Integrität von Leiterplatten. Durch die Verwendung maßgeschneiderter Adapter kann sichergestellt werden, dass alle Verbindungen korrekt sind und mögliche Fehler frühzeitig erkannt werden. Trotz der höheren Kosten und des Vorbereitungsaufwands bietet der Adaptertest in der Serienproduktion und Qualitätssicherung wesentliche Vorteile in Bezug auf Genauigkeit und Effizienz.
Ätzen ist ein wesentlicher Prozess in der Herstellung von Leiterplatten (PCBs), bei dem unerwünschtes Material von der Leiterplatte entfernt wird, um das gewünschte Schaltmuster zu erzeugen. Hier ist eine detaillierte Erklärung des Ätzprozesses und seiner Bedeutung in der Leiterplattenfertigung:
Was ist Ätzen?
Ätzen ist der chemische Prozess, bei dem überschüssiges Kupfer oder andere Materialien von einer Leiterplatte entfernt werden, um die elektrischen Verbindungen (Leiterbahnen) und die Struktur der Leiterplatte zu formen. Der Prozess erfolgt nach dem Drucken des Schaltplans und dem Aufbringen des Schutzlacks auf die Leiterplatte.
Ätzprozess im Detail
Vorbereitung:
- Bedecken der Leiterplatte: Die Leiterplatte wird zunächst mit einer lichtempfindlichen Schicht (Fotolack) beschichtet, die durch UV-Licht belichtet wird, um das gewünschte Schaltmuster zu erstellen.
- Belichtung: Der Fotolack wird in einem Belichtungsprozess, oft durch UV-Licht, gehärtet, wobei das Schaltmuster auf die Leiterplatte übertragen wird.
Entwickeln:
- Entfernen des Fotolacks: Die belichtete Leiterplatte wird in eine Entwicklerlösung getaucht, die den nicht belichteten Fotolack entfernt. Dies enthüllt das darunterliegende Kupfer.
Ätzen:
- Chemische Ätzung: Die Leiterplatte wird in eine Ätzlösung getaucht, die das ungeschützte Kupfer auf der Leiterplatte entfernt, basierend auf dem Schaltmuster, das durch den Fotolack geschützt wurde. Typische Ätzlösungen sind Ferrichlorid oder Ammoniumpersulfat.
- Überwachung: Der Ätzprozess muss sorgfältig überwacht werden, um sicherzustellen, dass das Kupfer gleichmäßig entfernt wird und keine Schäden an den gewünschten Leiterbahnen auftreten.
Reinigung:
- Entfernen des Fotolacks: Nach dem Ätzen wird der verbleibende Fotolack von der Leiterplatte entfernt, und die Leiterplatte wird gereinigt, um alle Rückstände des Ätzprozesses zu entfernen.
Inspektion:
- Qualitätskontrolle: Die Leiterplatte wird auf Defekte oder Unregelmäßigkeiten überprüft. Hierzu gehören Tests auf fehlende Leiterbahnen, unerwünschte Kupferüberreste oder andere Fertigungsfehler.
Vorteile des Ätzen
Präzision:
- Feinste Leiterbahnen: Ätzen ermöglicht die Herstellung sehr präziser und feiner Leiterbahnen, die für moderne elektronische Geräte notwendig sind.
Flexibilität:
- Komplexe Designs: Der Ätzprozess kann für eine Vielzahl von Leiterplattendesigns verwendet werden, von einfachen bis zu sehr komplexen Schaltungen.
Kosteneffizienz:
- Skalierbarkeit: Ätzen ist eine kosteneffiziente Methode für die Massenproduktion von Leiterplatten, insbesondere in der Serienfertigung.
Nachteile des Ätzen
Chemikalien:
- Umweltauswirkungen: Der Ätzprozess verwendet Chemikalien, die umwelt- und gesundheitsschädlich sein können, wenn sie nicht richtig behandelt oder entsorgt werden.
Materialverlust:
- Kupferabtrag: Der Prozess kann zu einem gewissen Materialverlust führen, was bei sehr feinen und präzisen Leiterbahnen zu Problemen führen kann.
Prozesskontrolle:
- Komplexität: Die Kontrolle und Überwachung des Ätzprozesses erfordert präzise Kontrolle der Chemikalienkonzentrationen und -zeiten, um Defekte zu vermeiden.
Varianten des Ätzens
Nassätzen:
- Ätzen in Flüssigkeit: Der Ätzprozess erfolgt in einer Flüssigkeit, die die Leiterplatte vollständig umschließt und das ungeschützte Kupfer entfernt.
Trockenätzen (Plasmaätzen):
- Ätzen in Gasphase: Hierbei werden ionisierte Gase verwendet, um das Kupfer zu entfernen. Diese Methode ist besonders präzise und wird häufig für hochdichte Leiterplatten verwendet.
Laserätzen:
- Laserablation: Diese Methode verwendet Laserstrahlen zur gezielten Entfernung von Kupfer, um sehr feine und komplexe Muster zu erstellen.
Fazit
Das Ätzen ist ein zentraler Schritt in der Leiterplattenfertigung, der es ermöglicht, präzise elektrische Verbindungen und Strukturen auf der Leiterplatte zu erstellen. Trotz seiner Vorteile, wie Präzision und Kosteneffizienz, sind die Verwendung von Chemikalien und die Notwendigkeit einer genauen Prozesskontrolle wesentliche Aspekte, die bei der Durchführung des Ätzprozesses berücksichtigt werden müssen.
Vgl. auch → Resist
- ATZRESIST
- ALUKERN-PLATINEN
- ALUMINIUM KERN
- ANNULAR RING
- ANTI-PAD
Ätzresist (auch als Ätzschutzlack bekannt) ist ein spezieller Lack, der auf die Oberfläche einer Leiterplatte aufgetragen wird, um bestimmte Bereiche vor dem Ätzprozess zu schützen. Der Ätzresist bildet eine Schutzschicht, die das darunterliegende Material während des Ätzens vor dem Entfernen bewahrt, und ermöglicht so die präzise Herstellung von Leiterbahnen und Schaltmustern.
Funktionen des Ätzresists
Schutz der Leiterplatte:
- Verhinderung der Ätzung: Der Ätzresist schützt die Bereiche der Leiterplatte, die nicht entfernt werden sollen. Er sorgt dafür, dass nur die beabsichtigten Teile des Kupfers oder anderer leitfähiger Materialien entfernt werden.
Erhaltung von Schaltmustern:
- Präzise Muster: Der Ätzresist ermöglicht die präzise Übertragung von Schaltmustern auf die Leiterplatte, indem er die Bereiche abdeckt, die nicht bearbeitet werden sollen. Dies ist entscheidend für die Herstellung von feinen und komplexen Leiterbahnen.
Vermeidung von Fehlern:
- Fehlerreduktion: Durch den Schutz der gewünschten Bereiche hilft der Ätzresist, Fehler und Mängel in der Leiterplatte zu vermeiden, die durch unerwünschte Ätzung verursacht werden könnten.
Arten von Ätzresist
Fotoreaktive Ätzresists:
- Lichtempfindlich: Diese Ätzresists werden durch UV-Licht belichtet. Die belichteten Bereiche härten aus und werden resistent gegen die Ätzlösung, während die nicht belichteten Bereiche durch den Entwickler entfernt werden.
- Verwendung: Fotoreaktive Ätzresists sind weit verbreitet und ermöglichen die präzise Übertragung komplexer Muster.
Sole-Resists:
- Chemische Reaktion: Diese Ätzresists reagieren chemisch mit der Ätzlösung, um die geschützten Bereiche zu erhalten. Sie werden häufig für spezifische Anwendungen verwendet, bei denen Fotoreaktive Ätzresists nicht ideal sind.
Paste-Resists:
- Dicke Schicht: Diese Form des Ätzresists wird als Paste aufgetragen und bietet eine dickere Schutzschicht. Sie ist weniger präzise als Fotoreaktive Ätzresists, kann aber für weniger komplexe Anwendungen nützlich sein.
Anwendung des Ätzresists
Auftragen:
- Beschichtungsverfahren: Der Ätzresist wird durch verschiedene Methoden aufgetragen, darunter Sprühen, Tauchen oder Drucken. Die Wahl des Verfahrens hängt von der Art des Resists und den Anforderungen der Leiterplatte ab.
Belichtung und Entwickeln:
- Belichtung: Bei fotoreaktiven Ätzresists wird die Leiterplatte nach dem Auftragen des Resists in einer Belichtungsmaschine UV-Licht ausgesetzt, um die Schaltmuster zu übertragen.
- Entwickeln: Nach der Belichtung wird die Leiterplatte in einem Entwicklerbad behandelt, um den nicht belichteten Ätzresist zu entfernen und das darunterliegende Material freizulegen.
Ätzen:
- Ätzprozess: Die Leiterplatte wird dann in eine Ätzlösung getaucht, die das ungeschützte Material entfernt, während die durch den Ätzresist geschützten Bereiche erhalten bleiben.
Entfernen des Ätzresists:
- Reinigung: Nach dem Ätzen wird der verbleibende Ätzresist entfernt, und die Leiterplatte wird gereinigt, um alle Rückstände des Ätzprozesses zu beseitigen.
Vorteile des Ätzresists
Präzision:
- Feinste Details: Erlaubt die präzise Herstellung von Leiterbahnen und Schaltmustern, die für moderne Elektronik erforderlich sind.
Fehlervermeidung:
- Schutz: Verhindert die Entfernung von unerwünschtem Material und reduziert die Wahrscheinlichkeit von Fehlern in der Leiterplatte.
Vielfältige Anwendungen:
- Flexibilität: Verschiedene Arten von Ätzresists können für unterschiedliche Anforderungen und Anwendungen verwendet werden.
Nachteile des Ätzresists
Chemikalien:
- Umweltauswirkungen: Der Umgang mit und die Entsorgung von Ätzresistchemikalien erfordert Vorsichtsmaßnahmen, um Umwelt- und Gesundheitsrisiken zu minimieren.
Prozesskomplexität:
- Aufwand: Der Einsatz von Ätzresists kann zusätzliche Schritte im Fertigungsprozess erfordern, einschließlich des Auftrags, der Belichtung und des Entfernens des Resists.
Kosten:
- Materialkosten: Die Qualität und die Art des verwendeten Ätzresists können die Kosten der Leiterplattenfertigung beeinflussen.
Fazit
Ätzresist ist ein kritisches Material in der Leiterplattenfertigung, das es ermöglicht, präzise elektrische Verbindungen und Schaltmuster herzustellen. Durch den Schutz bestimmter Bereiche der Leiterplatte während des Ätzprozesses spielt der Ätzresist eine zentrale Rolle bei der Sicherstellung der Funktionalität und Zuverlässigkeit der fertigen Leiterplatte. Trotz der Herausforderungen bei der Handhabung und den Kosten ist der Ätzresist unerlässlich für die Herstellung hochqualitativer Leiterplatten.
Vgl. auch → Resist
Alukern-Platinen, auch als Aluminiumkern-Leiterplatten oder Aluminiumkern-PCBs bezeichnet, sind spezielle Leiterplatten, die einen Kern aus Aluminium oder einer Aluminiumlegierung enthalten. Diese Art von Leiterplatten kombiniert die elektrischen Eigenschaften eines traditionellen Leiterplattenmaterials mit den thermischen und mechanischen Vorteilen von Aluminium.
Merkmale von Alukern-Platinen
Aluminiumkern:
- Kernmaterial: Der zentrale Bestandteil der Alukern-Platine ist ein Aluminiumkern. Dieses Material sorgt für eine hervorragende Wärmeableitung und Festigkeit der Leiterplatte.
Schichtaufbau:
- Aufbau: Die Leiterplatte besteht typischerweise aus drei Schichten: dem Aluminiumkern, einer thermischen Isolierschicht (oft aus einem speziellen Harz), und einer Kupferschicht, auf der das Schaltmuster angebracht ist.
- Schutzschicht: Die oberste Schicht besteht aus einer Kupferlage, die die elektrischen Verbindungen und Schaltmuster enthält.
Wärmeleitfähigkeit:
- Effizienz: Aluminium hat eine hohe Wärmeleitfähigkeit, was bedeutet, dass es Wärme effizient von den aktiven Komponenten der Leiterplatte ableitet. Dies ist besonders nützlich in Anwendungen, die hohe Temperaturen erzeugen oder wo eine hohe Wärmeabfuhr erforderlich ist.
Mechanische Festigkeit:
- Robustheit: Der Aluminiumkern verleiht der Leiterplatte zusätzliche mechanische Festigkeit, was sie widerstandsfähiger gegen physische Belastungen macht.
Vorteile von Alukern-Platinen
Hervorragende Wärmeableitung:
- Überhitzungsschutz: Der Aluminiumkern leitet Wärme effektiv ab und hilft, die Temperatur von Komponenten zu kontrollieren. Dies kann die Lebensdauer von Bauteilen verlängern und die Leistung verbessern.
Stabilität und Festigkeit:
- Robustheit: Die Alukern-Platine bietet eine robuste Struktur, die weniger anfällig für mechanische Schäden ist.
Geringes Gewicht:
- Leichtbau: Alukern-Platinen sind leichter als viele andere Leiterplattenmaterialien, was für bestimmte Anwendungen von Vorteil sein kann.
Gute elektrische Eigenschaften:
- Leitfähigkeit: Durch die Verwendung von hochwertigem Kupfer für die Schaltmuster wird eine gute elektrische Leitfähigkeit gewährleistet.
Nachteile von Alukern-Platinen
Kosten:
- Höhere Kosten: Alukern-Platinen können teurer sein als Standard-Leiterplatten, da die Herstellung und das Material teurer sind.
Bearbeitungsaufwand:
- Komplexität: Die Bearbeitung von Alukern-Platinen kann komplexer sein, insbesondere wenn es um das Bohren oder Fräsen des Aluminiumkerns geht.
Materialbeschränkungen:
- Flexibilität: Alukern-Platinen sind in der Regel weniger flexibel als flexible Leiterplatten, was ihre Verwendung in Anwendungen mit flexiblen Anforderungen einschränken kann.
Anwendungen von Alukern-Platinen
Leuchtmittel:
- LED-Beleuchtung: Alukern-Platinen werden häufig in LED-Beleuchtungen verwendet, da sie die von LEDs erzeugte Wärme effektiv abführen können.
Automobilindustrie:
- Elektronik: In der Automobilindustrie finden sie Anwendung in Komponenten, die hohe Temperaturen erzeugen, wie z. B. Steuergeräte und Sensoren.
Energieelektronik:
- Stromversorgung: Alukern-Platinen werden in Leistungselektronik eingesetzt, wo eine gute Wärmeableitung entscheidend ist, um die Zuverlässigkeit und Effizienz der Stromversorgung zu gewährleisten.
Medizinische Geräte:
- Hochwertige Elektronik: In medizinischen Geräten, die präzise und zuverlässige Elektronik erfordern, werden Alukern-Platinen verwendet, um die Wärmeentwicklung zu kontrollieren.
Herstellung von Alukern-Platinen
Design:
- Layout: Das Design der Schaltmuster wird unter Berücksichtigung der spezifischen Anforderungen an Wärmeableitung und elektrische Leistung erstellt.
Zusammenbau:
- Schichten: Der Aluminiumkern wird mit einer Isolierschicht und der Kupferschicht zusammengebaut. Dies kann durch Laminierung oder andere Verfahren erfolgen.
Ätzen und Bohren:
- Prozess: Das Kupfer wird ätzen, um die Leiterbahnen zu erstellen, und die Platine wird gebohrt, um Verbindungslöcher oder andere erforderliche Öffnungen zu schaffen.
Endbearbeitung:
- Beschichtung: Die Platine wird abschließend beschichtet und getestet, um sicherzustellen, dass sie den Anforderungen entspricht.
Fazit
Alukern-Platinen bieten durch ihre Wärmeableitungsfähigkeiten und mechanische Festigkeit Vorteile in Anwendungen, die hohe Temperaturen und Robustheit erfordern. Trotz der höheren Kosten und der komplexeren Bearbeitung sind sie in vielen modernen Elektronik- und Beleuchtungsanwendungen unverzichtbar, da sie die Zuverlässigkeit und Leistung von Komponenten verbessern.
Vgl. auch → Durchkontaktieren
Der Aluminiumkern in einer Leiterplatte, oft als Aluminiumkern-Leiterplatte oder Aluminiumkern-PCB bezeichnet, ist eine spezielle Art von Leiterplatte, die einen Kern aus Aluminium enthält. Diese Art von Leiterplatte wird in Anwendungen eingesetzt, bei denen eine effektive Wärmeableitung und zusätzliche mechanische Stabilität erforderlich sind.
Merkmale des Aluminiumkerns in Leiterplatten
Aluminiumkern:
- Material: Der zentrale Bestandteil dieser Leiterplatte ist ein Aluminiumkern. Dieser Kern kann entweder aus reinem Aluminium oder aus einer Aluminiumlegierung bestehen.
- Eigenschaften: Aluminium bietet eine ausgezeichnete Wärmeleitfähigkeit und Festigkeit, was es ideal für Anwendungen macht, bei denen hohe Temperaturen und mechanische Belastungen auftreten.
Schichtaufbau:
- Schichten: Eine typische Aluminiumkern-Leiterplatte besteht aus mehreren Schichten:
- Aluminiumkern: Die zentrale Schicht, die für die Wärmeleitung verantwortlich ist.
- Thermische Isolierschicht: Eine Schicht, die zwischen dem Aluminiumkern und der Kupferschicht liegt und Wärmeübertragung sowie elektrische Isolation ermöglicht. Diese Schicht besteht oft aus Harzen wie IMS (Insulated Metal Substrate).
- Kupferschicht: Die oberste Schicht, auf der das elektrische Schaltmuster und die Leiterbahnen aufgebracht werden.
- Schichten: Eine typische Aluminiumkern-Leiterplatte besteht aus mehreren Schichten:
Thermische Eigenschaften:
- Wärmeableitung: Aluminium hat eine hohe Wärmeleitfähigkeit, was bedeutet, dass es Wärme effektiv von den aktiven Komponenten der Leiterplatte ableitet. Dies ist besonders wichtig für die Vermeidung von Überhitzung und die Verbesserung der Lebensdauer und Leistung von Bauteilen.
Mechanische Festigkeit:
- Stabilität: Der Aluminiumkern verleiht der Leiterplatte zusätzliche mechanische Festigkeit, was sie widerstandsfähiger gegen physische Belastungen und Stöße macht.
Vorteile des Aluminiumkerns in Leiterplatten
Effektive Wärmeableitung:
- Überhitzungsschutz: Durch die ausgezeichnete Wärmeleitfähigkeit von Aluminium können Temperaturspitzen schnell abgeleitet werden, was die Überhitzung von Komponenten verhindert und die Zuverlässigkeit erhöht.
Mechanische Stabilität:
- Robustheit: Aluminiumkern-Leiterplatten sind robust und widerstandsfähig gegenüber mechanischen Belastungen und Vibrationen, was sie ideal für Anwendungen macht, die harte Bedingungen erfordern.
Geringes Gewicht:
- Leichtbau: Aluminium ist leichter als viele andere Materialien, was zur Reduzierung des Gesamtgewichts der Leiterplatte beiträgt und in vielen Anwendungen von Vorteil sein kann.
Hervorragende elektrische Eigenschaften:
- Leitfähigkeit: Die Kupferschicht auf der Leiterplatte sorgt für ausgezeichnete elektrische Leitfähigkeit, die für eine präzise und zuverlässige Signalübertragung sorgt.
Nachteile des Aluminiumkerns in Leiterplatten
Kosten:
- Preis: Aluminiumkern-Leiterplatten können teurer sein als traditionelle Leiterplatten aufgrund der zusätzlichen Material- und Herstellungsaufwendungen.
Bearbeitungsaufwand:
- Komplexität: Die Bearbeitung von Aluminiumkern-Leiterplatten kann komplizierter sein, insbesondere beim Bohren und Fräsen, da Aluminium andere Werkzeuge und Techniken erfordern kann.
Beschränkte Flexibilität:
- Steifigkeit: Aluminiumkern-Leiterplatten sind in der Regel weniger flexibel als andere Leiterplattenmaterialien, was ihre Verwendung in flexiblen oder biegsamen Anwendungen einschränkt.
Anwendungen des Aluminiumkerns in Leiterplatten
LED-Beleuchtung:
- Wärmeableitung: Besonders geeignet für LED-Anwendungen, wo die Wärmeableitung entscheidend für die Leistung und Lebensdauer der LEDs ist.
Automobilindustrie:
- Elektronik: Verwendung in Komponenten, die hohe Temperaturen und mechanische Belastungen ausgesetzt sind, wie z. B. Steuergeräte und Sensoren.
Energieelektronik:
- Leistungsstarke Schaltungen: In Anwendungen, die hohe Leistungen und somit hohe Wärmeentwicklung erzeugen, wie z. B. Stromversorgungen und Leistungsverstärker.
Medizinische Geräte:
- Präzise Elektronik: In medizinischen Geräten, die eine hohe Zuverlässigkeit und Wärmeableitung erfordern, um optimale Leistung und Langlebigkeit zu gewährleisten.
Herstellung von Aluminiumkern-Leiterplatten
Design:
- Layout: Das Design umfasst die Schaltmuster und die Wärmeableitungseigenschaften der Leiterplatte.
Schichtaufbau:
- Zusammenstellung: Der Aluminiumkern wird mit einer thermischen Isolierschicht und der Kupferschicht laminiert.
Ätzen und Bohren:
- Prozess: Das Kupfer wird geätzt, um die gewünschten Leiterbahnen zu erzeugen, und die Platine wird gebohrt, um Verbindungslöcher und andere erforderliche Öffnungen zu schaffen.
Endbearbeitung:
- Beschichtung: Die Leiterplatte wird abschließend gereinigt und auf Qualität geprüft.
Fazit
Aluminiumkern-Leiterplatten bieten durch ihre überlegene Wärmeableitung und mechanische Stabilität erhebliche Vorteile in vielen Anwendungen, bei denen hohe Temperaturen und mechanische Belastungen auftreten. Trotz der höheren Kosten und der komplexeren Bearbeitung bieten sie entscheidende Vorteile in Bezug auf Leistung, Zuverlässigkeit und Langlebigkeit.
Vgl. auch → Alukern-Platinen
Annular Ring (auf Deutsch Ringkante oder Ringkern) bezeichnet ein spezifisches Merkmal in der Leiterplattenfertigung, das in der Umgebung von Durchkontaktierungen (Vias) zu finden ist. Der Begriff beschreibt den Bereich des Kupfers, der den Lochrand einer Durchkontaktierung umgibt.
Merkmale des Annular Rings
Kupferfläche:
- Umgebung: Der Annular Ring ist die Kupferfläche, die den Rand eines Lochs oder einer Bohrung auf der Leiterplatte umgibt. Diese Fläche ist typischerweise kreisförmig und erstreckt sich um die gesamte Bohrung.
- Funktion: Der Annular Ring verbindet die Durchkontaktierung mit den Leiterbahnen auf der Leiterplatte und stellt somit elektrische Verbindungen zwischen den verschiedenen Schichten der Leiterplatte her.
Design-Kriterium:
- Durchmesser: Der Durchmesser des Annular Rings wird durch die Größe der Bohrung und die Breite der Leiterbahnen bestimmt. Ein gut gestalteter Annular Ring stellt sicher, dass die Verbindung zuverlässig und stabil ist.
- Zulässige Toleranzen: In den Designregeln sind bestimmte Toleranzen für den Annular Ring festgelegt, um sicherzustellen, dass die Herstellung der Leiterplatte den Qualitätsanforderungen entspricht.
Funktionen des Annular Rings
Elektrische Verbindung:
- Verbindung zwischen Schichten: Der Annular Ring sorgt für die elektrische Verbindung zwischen den verschiedenen Schichten der Leiterplatte durch die Durchkontaktierung.
- Signalübertragung: Er ermöglicht die Übertragung von Signalen und Strom zwischen den Schaltkreisen, die sich auf unterschiedlichen Schichten der Leiterplatte befinden.
Mechanische Stabilität:
- Festigkeit: Der Annular Ring trägt zur mechanischen Stabilität der Durchkontaktierung bei, indem er eine größere Oberfläche bietet, die die Verbindung zwischen den Schichten verstärkt.
Vermeidung von Kurzschlüssen:
- Schutz: Ein korrekt gestalteter Annular Ring hilft, Kurzschlüsse und andere elektrische Probleme zu vermeiden, indem er eine konsistente und zuverlässige Verbindung sicherstellt.
Design-Überlegungen
Größe und Toleranzen:
- Minimale Größe: Der Annular Ring muss eine Mindestbreite aufweisen, die je nach Leiterplattendesign und -anforderungen variiert. Zu enge Annular Rings können zu Produktionsproblemen oder elektrischen Fehlern führen.
- Toleranzen: Die Fertigungstoleranzen für den Annular Ring sind entscheidend für die Zuverlässigkeit der Leiterplatte. Zu große oder zu kleine Annular Rings können die Funktionalität beeinträchtigen.
Fertigungstechniken:
- Ätzprozess: Während des Ätzprozesses wird der Kupferbereich des Annular Rings freigelegt. Eine präzise Kontrolle dieses Prozesses ist notwendig, um sicherzustellen, dass der Annular Ring den Spezifikationen entspricht.
- Bohrungen: Die Größe und Position der Bohrungen müssen exakt kontrolliert werden, um sicherzustellen, dass der Annular Ring die richtige Größe und Form hat.
Probleme und Herausforderungen
Unzureichende Ringgröße:
- Schwache Verbindungen: Ein unzureichender Annular Ring kann zu schwachen Verbindungen führen, die die Funktionalität der Leiterplatte beeinträchtigen können.
Fertigungstoleranzen:
- Variationen: Variationen in der Fertigung können dazu führen, dass Annular Rings nicht den Designvorgaben entsprechen, was zu möglichen Fehlern in der Leiterplatte führt.
Kosten:
- Herstellungskosten: Präzise Annular Rings können zusätzliche Kosten verursachen, da höhere Genauigkeit und bessere Fertigungsprozesse erforderlich sind.
Fazit
Der Annular Ring ist ein kritisches Element im Leiterplattendesign, das für die elektrische Verbindung und mechanische Stabilität der Durchkontaktierungen verantwortlich ist. Ein gut gestalteter und korrekt ausgeführter Annular Ring ist entscheidend für die Leistungsfähigkeit und Zuverlässigkeit der Leiterplatte. Die Berücksichtigung der richtigen Größe, Toleranzen und Fertigungsprozesse ist wichtig, um eine fehlerfreie und leistungsfähige Leiterplatte zu gewährleisten.
Vgl. auch → Restring
Das Anti-Pad ist ein wichtiges Konzept in der Leiterplattenfertigung, insbesondere beim Design von Leiterplatten mit Durchkontaktierungen (Vias). Es bezieht sich auf die ausgesparte Fläche um eine Bohrung, die im Gegensatz zum Annular Ring steht.
Was ist ein Anti-Pad?
Definition:
- Anti-Pad: Ein Anti-Pad ist die ausgesparte oder unbeschichtete Fläche auf der Leiterplatte, die sich um eine Bohrung oder Durchkontaktierung herum befindet. Es handelt sich um den Bereich, der freigelassen wird, um eine elektrische Isolierung zwischen der Kupferfläche und der Bohrung zu gewährleisten.
Funktion:
- Vermeidung von Kurzschlüssen: Das Anti-Pad stellt sicher, dass es keine direkten elektrischen Verbindungen zwischen der Kupferfläche und der Bohrung gibt, die Kurzschlüsse verursachen könnten.
- Verhinderung von Lötfehlern: Durch das Einhalten des Anti-Pads wird verhindert, dass Lötmaterial beim Löten in die Bohrung fließt und somit elektrische Verbindungen zwischen benachbarten Leiterbahnen oder Schichten verursacht.
Design-Überlegungen
Größe des Anti-Pads:
- Dimensionierung: Die Größe des Anti-Pads wird durch die Größe der Bohrung und den Durchmesser der benachbarten Kupferflächen bestimmt. Ein korrekt dimensioniertes Anti-Pad stellt sicher, dass es ausreichend Platz gibt, um elektrische Isolation zu gewährleisten und gleichzeitig eine stabile Verbindung durch die Bohrung zu ermöglichen.
- Typische Abmessungen: Die Größe des Anti-Pads sollte so gewählt werden, dass sie die Spezifikationen der Leiterplattenfertigung erfüllt und gleichzeitig die mechanischen und elektrischen Anforderungen berücksichtigt.
Abstand zum Kupferbereich:
- Sicherheitsabstand: Der Abstand zwischen der Bohrung und der benachbarten Kupferfläche, der durch das Anti-Pad definiert wird, muss ausreichen, um sicherzustellen, dass keine unerwünschten elektrischen Verbindungen entstehen. Zu geringe Abstände können zu Produktionsproblemen und elektrischen Fehlfunktionen führen.
Fertigungstechnische Aspekte
Ätzprozess:
- Erstellung: Während des Ätzprozesses wird das Kupfer in Bereichen außerhalb des Anti-Pads entfernt. Eine präzise Steuerung dieses Prozesses ist wichtig, um sicherzustellen, dass das Anti-Pad korrekt erzeugt wird und die Leiterplatte den Spezifikationen entspricht.
- Präzision: Die Präzision bei der Herstellung des Anti-Pads ist entscheidend, um die Integrität der elektrischen Isolierung und die Qualität der Leiterplatte sicherzustellen.
Bohrungen und Vias:
- Koordination: Die Bohrungen oder Vias müssen genau positioniert werden, um sicherzustellen, dass das Anti-Pad korrekt um die Bohrung herum platziert ist und keine unerwünschten Verbindungen entstehen.
Probleme und Herausforderungen
Falsche Dimensionierung:
- Kurzschlüsse: Wenn das Anti-Pad zu klein ist, besteht die Gefahr von Kurzschlüssen zwischen benachbarten Leiterbahnen oder Schichten durch das Eindringen von Lötmaterial oder durch ungewollte elektrische Verbindungen.
Fertigungstoleranzen:
- Variationen: Fertigungstoleranzen können dazu führen, dass das Anti-Pad nicht genau den Spezifikationen entspricht, was potenziell die Leistung und Zuverlässigkeit der Leiterplatte beeinträchtigen kann.
Kosten:
- Zusätzlicher Aufwand: Das Design und die Herstellung von Leiterplatten mit korrekt dimensionierten Anti-Pads können zusätzliche Kosten verursachen, insbesondere wenn spezielle Fertigungstechniken oder Materialien erforderlich sind.
Anwendungen
Durchkontaktierungen (Vias):
- Multilayer-Leiterplatten: In Mehrschicht-Leiterplatten werden Anti-Pads verwendet, um elektrische Isolierung zwischen den Schichten zu gewährleisten, wo Vias die unterschiedlichen Schichten verbinden.
Elektronische Baugruppen:
- Feine Leiterbahnen: Bei Leiterplatten mit sehr feinen Leiterbahnen und kleinen Bohrungen sind präzise Anti-Pads besonders wichtig, um die Integrität der elektrischen Verbindungen sicherzustellen.
Fazit
Das Anti-Pad ist ein kritisches Designelement in der Leiterplattenfertigung, das eine sichere elektrische Isolierung und Vermeidung von Kurzschlüssen sicherstellt. Eine präzise Dimensionierung und Fertigung sind entscheidend, um die Leistung und Zuverlässigkeit der Leiterplatte zu gewährleisten. Das richtige Verständnis und die sorgfältige Umsetzung von Anti-Pads sind unerlässlich, um hochwertige und funktionale Leiterplatten zu produzieren.
Vgl. auch → Pad-Freistellung
- AOI
- ARC RESISTANCE
- ASPECT-RATIO
- AU
- AUFBAU
AOI steht für Automated Optical Inspection, also Automatische Optische Inspektion. Bei der AOI handelt es sich um eine Prüf- und Inspektionsmethode, die in der Leiterplattenfertigung eingesetzt wird, um sicherzustellen, dass die Leiterplatten den Qualitätsanforderungen entsprechen und keine Fehler aufweisen.
Was ist AOI?
Definition:
- Automated Optical Inspection (AOI): Eine automatisierte Methode zur Überprüfung von Leiterplatten, bei der optische Technologien verwendet werden, um Fehler auf der Leiterplatte zu erkennen. Dies umfasst sowohl visuelle Inspektionen als auch die Analyse von Bildern, die von Kameras aufgenommen werden.
Zweck:
- Fehlererkennung: Die Hauptaufgabe von AOI ist die frühzeitige Erkennung von Fehlern, wie z. B. fehlende oder falsche Bauteile, Lötfehler, Kurzschlüsse, offene Verbindungen und andere Defekte.
- Qualitätssicherung: AOI trägt zur Sicherstellung der hohen Qualität und Zuverlässigkeit von Leiterplatten bei, indem es Fehler aufspürt, die während der Fertigung auftreten können.
Wie funktioniert AOI?
Bildaufnahme:
- Kamerasysteme: AOI-Systeme verwenden hochauflösende Kameras, um detaillierte Bilder der Leiterplatte aufzunehmen. Diese Kameras sind oft auf den Fertigungsmaschinen montiert und können die gesamte Leiterplatte oder spezifische Bereiche scannen.
- Beleuchtung: Verschiedene Beleuchtungstechniken (z. B. Diffuslicht, gerichtetes Licht) werden verwendet, um die Bildqualität zu verbessern und die Sichtbarkeit von Fehlern zu erhöhen.
Bildverarbeitung:
- Algorithmen: Die aufgenommenen Bilder werden durch fortschrittliche Bildverarbeitungsalgorithmen analysiert. Diese Algorithmen vergleichen die aufgenommenen Bilder mit den Referenzbildern oder den Design-Daten, um Abweichungen und Fehler zu identifizieren.
- Fehleranalyse: Die Analyse kann Fehler wie fehlende Lötstellen, falsche Bauteilplatzierungen, Kurzschlüsse und andere Anomalien umfassen.
Fehleridentifikation:
- Fehlerberichte: Wenn Fehler erkannt werden, erstellt das AOI-System Berichte und Markierungen auf der Leiterplatte, um die fehlerhaften Bereiche anzuzeigen.
- Automatisierte Korrektur: In einigen Fällen können AOI-Systeme auch automatisch Korrekturen an der Leiterplatte vornehmen oder eine Weiterverarbeitung zur Fehlerbehebung initiieren.
Vorteile der AOI
Erhöhung der Fehlererkennung:
- Präzision: AOI-Systeme können sehr präzise Fehler erkennen, die möglicherweise von menschlichen Inspektoren übersehen werden.
Effizienzsteigerung:
- Schnelligkeit: AOI kann schnell große Mengen an Leiterplatten überprüfen, was die Fertigungseffizienz steigert und die Produktionszeit verkürzt.
Kosteneinsparungen:
- Reduzierung von Ausschuss: Durch die frühzeitige Erkennung und Korrektur von Fehlern wird die Anzahl fehlerhafter Leiterplatten reduziert, was zu Kosteneinsparungen führt.
Kontinuierliche Überwachung:
- Echtzeit-Inspektion: AOI-Systeme ermöglichen eine kontinuierliche Überwachung der Produktionslinie, was eine sofortige Reaktion auf auftretende Probleme ermöglicht.
Nachteile der AOI
Kosten:
- Investitionsaufwand: Die Anschaffung und Implementierung von AOI-Systemen kann teuer sein, insbesondere für kleine Unternehmen oder in kleinen Produktionsvolumen.
Falsch-positive Ergebnisse:
- Fehlalarme: AOI-Systeme können gelegentlich Fehlalarme auslösen, bei denen nicht-existenten Fehlern auf der Leiterplatte signalisiert werden, was zusätzliche Überprüfungen und Korrekturen erfordert.
Komplexität der Programmierung:
- Einrichtung: Die Programmierung und Kalibrierung von AOI-Systemen kann komplex sein und erfordert spezifisches Fachwissen und Erfahrung.
Anwendungen der AOI
Fertigungskontrolle:
- Produktion: AOI wird in der Fertigung von Leiterplatten eingesetzt, um sicherzustellen, dass alle Bauteile korrekt platziert sind und alle Lötstellen einwandfrei sind.
Qualitätssicherung:
- Prüfung: AOI wird als Teil der Qualitätssicherungsprozesse in der Elektronikindustrie verwendet, um die Einhaltung von Qualitätsstandards zu überprüfen.
Fehlerdiagnose:
- Analyse: AOI-Systeme helfen bei der Diagnose von Fehlerursachen und unterstützen bei der Verbesserung der Fertigungsprozesse.
Fazit
Die Automated Optical Inspection (AOI) ist eine entscheidende Technologie in der Leiterplattenfertigung, die durch die Automatisierung der Fehlererkennung und -prüfung zur Verbesserung der Qualität und Effizienz beiträgt. Trotz der anfänglichen Investitionskosten bietet AOI bedeutende Vorteile in Bezug auf Fehlerprävention, Produktionsgeschwindigkeit und Kostenersparnis. Durch die kontinuierliche Überwachung und präzise Fehleridentifikation trägt AOI zur Herstellung zuverlässiger und fehlerfreier Leiterplatten bei.
ARC-Resistance (auf Deutsch Bogenfestigkeit oder Bogenresistenz) bezieht sich auf die Fähigkeit von Materialien, insbesondere von Leiterplatten und deren Beschichtungen, gegen die Auswirkungen von elektrischen Lichtbögen oder Überschlägen widerstandsfähig zu sein. Diese Eigenschaft ist besonders wichtig in Anwendungen, bei denen hohe elektrische Spannungen oder Ströme auftreten können, die zu einem elektrischen Bogen führen könnten.
Was ist ARC-Resistance?
Definition:
- ARC-Resistance: Die Widerstandsfähigkeit eines Materials oder einer Beschichtung gegen die physikalischen und chemischen Effekte eines elektrischen Lichtbogens. Diese Eigenschaft beschreibt, wie gut das Material die durch den Lichtbogen verursachten Temperaturen und chemischen Reaktionen übersteht, ohne beschädigt oder beeinträchtigt zu werden.
Wichtigkeit:
- Schutz vor Lichtbogen-Effekten: In der Elektronik und Leiterplattenfertigung ist es wichtig, Materialien zu verwenden, die gegenüber den extremen Bedingungen eines elektrischen Lichtbogens widerstandsfähig sind, um die langfristige Zuverlässigkeit und Sicherheit der elektrischen Komponenten zu gewährleisten.
Eigenschaften und Testmethoden
Eigenschaften:
- Temperaturbeständigkeit: Materialien mit hoher ARC-Resistance müssen hohen Temperaturen standhalten, die durch den Lichtbogen erzeugt werden.
- Chemische Beständigkeit: Die Materialien sollten gegenüber den chemischen Reaktionen resistent sein, die durch die Einwirkung des Lichtbogens entstehen.
- Mechanische Festigkeit: Es ist wichtig, dass das Material strukturell stabil bleibt, auch wenn es den intensiven Bedingungen eines Lichtbogens ausgesetzt ist.
Testmethoden:
- Lichtbogen-Test: Ein standardisierter Test, bei dem ein elektrischer Lichtbogen auf das Material angewendet wird, um seine Beständigkeit zu überprüfen. Der Test simuliert die Bedingungen eines Lichtbogens und bewertet, wie das Material auf die Hitze, den Druck und die chemischen Reaktionen reagiert.
- ISO- und ASTM-Normen: Verschiedene internationale Normen, wie z. B. die ISO- oder ASTM-Normen, definieren spezifische Methoden zur Bewertung der ARC-Resistance von Materialien.
Anwendungen
Leiterplatten:
- Schutzschichten: Leiterplatten können spezielle Schutzbeschichtungen erhalten, um ihre ARC-Resistance zu verbessern und sie gegen mögliche Lichtbogen-Schäden zu schützen. Diese Schichten helfen, die Lebensdauer und Zuverlässigkeit der Leiterplatten zu erhöhen.
Elektrotechnische Geräte:
- Isoliermaterialien: In elektrischen Geräten und Schaltanlagen werden Materialien mit hoher ARC-Resistance eingesetzt, um die Geräte gegen die Auswirkungen von Lichtbögen zu schützen und die Sicherheit zu gewährleisten.
Hochspannungsanwendungen:
- Schaltanlagen: In Hochspannungs-Schaltanlagen ist ARC-Resistance besonders wichtig, um die Isolationseigenschaften der Komponenten zu gewährleisten und die Gefahr von Lichtbogen-Schäden zu minimieren.
Vorteile und Herausforderungen
Vorteile:
- Erhöhte Zuverlässigkeit: Materialien mit hoher ARC-Resistance tragen zur Zuverlässigkeit und Langlebigkeit von Leiterplatten und elektrischen Geräten bei, indem sie Schäden durch Lichtbögen verhindern.
- Erhöhte Sicherheit: Die Verwendung von Materialien mit guter ARC-Resistance kann das Risiko von elektrischen Unfällen und Bränden reduzieren, die durch Lichtbögen verursacht werden könnten.
Herausforderungen:
- Kosten: Materialien, die hohe ARC-Resistance bieten, können teurer sein als Standardmaterialien. Dies kann die Gesamtkosten der Leiterplatte oder des elektrischen Geräts erhöhen.
- Fertigungskomplexität: Die Implementierung von Schutzmaßnahmen zur Verbesserung der ARC-Resistance kann zusätzliche Schritte im Fertigungsprozess erfordern, was die Komplexität und den Aufwand erhöhen kann.
Fazit
ARC-Resistance ist eine wichtige Eigenschaft von Materialien, die sicherstellen soll, dass sie den extremen Bedingungen eines elektrischen Lichtbogens standhalten können. In der Leiterplattenfertigung und bei der Herstellung von elektrischen Geräten ist es entscheidend, Materialien mit guter ARC-Resistance auszuwählen, um die Sicherheit, Zuverlässigkeit und Langlebigkeit der Produkte zu gewährleisten. Durch entsprechende Testmethoden und die Berücksichtigung der Anforderungen an die ARC-Resistance können Hersteller sicherstellen, dass ihre Produkte unter verschiedenen Bedingungen zuverlässig funktionieren
Vgl. auch → Lichtbogenfestigkeit
Aspect Ratio (auf Deutsch Seitenverhältnis) ist ein Begriff, der in der Leiterplattenfertigung verwendet wird, um das Verhältnis zwischen der Länge und der Breite eines Durchkontaktierungslochs (Via) oder einer Bohrung auf einer Leiterplatte zu beschreiben. Es ist ein entscheidendes Maß für die Herstellbarkeit und die Leistung von Leiterplatten.
Was ist das Aspect Ratio?
Definition:
- Aspect Ratio: Das Seitenverhältnis (Aspect Ratio) ist das Verhältnis der Tiefe (oder Höhe) eines Durchkontaktierungslochs zur Breite (oder Durchmesser) dieses Lochs. Es wird in der Regel als Verhältnis oder Bruchzahl angegeben, zum Beispiel 5:1 oder 10:1.
Berechnung:
- Formel: Das Aspect Ratio wird berechnet durch: Aspect Ratio=Tiefe des LochsDurchmesser des Lochs\text{Aspect Ratio} = \frac{\text{Tiefe des Lochs}}{\text{Durchmesser des Lochs}}Aspect Ratio=Durchmesser des LochsTiefe des Lochs
- Beispiel: Wenn ein Durchkontaktierungsloch eine Tiefe von 1 mm und einen Durchmesser von 0,2 mm hat, beträgt das Aspect Ratio 5:1.
Bedeutung des Aspect Ratio
Herstellbarkeit:
- Bohrungen und Durchkontaktierungen: Ein höheres Aspect Ratio (z.B. 10:1) bedeutet, dass das Loch relativ tief im Vergleich zu seinem Durchmesser ist. Höhere Aspect Ratios sind schwieriger herzustellen, da es schwieriger ist, das Material gleichmäßig zu ätzen oder zu bohren, ohne dass das Loch verstopft oder nicht korrekt bearbeitet wird.
Funktionalität:
- Elektrische Leistung: Ein hohes Aspect Ratio kann die elektrische Leistung und die Zuverlässigkeit der Leiterplatte beeinträchtigen, da das Risiko von Durchschlägen oder unzuverlässigen Verbindungen steigt.
Fertigungstechnische Anforderungen:
- Technologische Grenzen: Die Fertigungstechnologien haben Grenzen, wie hoch das Aspect Ratio eines Durchkontaktierungslochs sein kann. Das Design muss diese Grenzen berücksichtigen, um sicherzustellen, dass die Leiterplatte erfolgreich gefertigt werden kann.
Designüberlegungen
Maximales Aspect Ratio:
- Normen und Richtlinien: Die meisten Leiterplattenhersteller haben spezifische Richtlinien und Grenzen für das Aspect Ratio, um die Herstellbarkeit und Qualität zu gewährleisten. Diese Grenzen variieren je nach Fertigungsprozess und verwendeten Materialien.
Materialwahl:
- Leiterplattenmaterialien: Unterschiedliche Leiterplattenmaterialien und -technologien können unterschiedliche Aspect Ratios unterstützen. Beispielsweise können hochwertige Materialien und spezielle Fertigungsprozesse höhere Aspect Ratios ermöglichen.
Kosten:
- Fertigungskosten: Höhere Aspect Ratios können zusätzliche Kosten verursachen, da komplexere Fertigungsprozesse erforderlich sind. Das Design sollte Kosten und Anforderungen abwägen, um eine Balance zwischen Leistung und Kosten zu finden.
Vorteile und Herausforderungen
Vorteile:
- Kompakte Designs: Ein hohes Aspect Ratio ermöglicht kompaktere Designs, da es die Möglichkeit bietet, mehr Verbindungen auf kleinerem Raum unterzubringen.
- Flexibilität im Design: Es erlaubt Designern, komplexe und dichte Schaltungen zu entwerfen, was bei modernen, kompakten Elektronikgeräten besonders wichtig ist.
Herausforderungen:
- Fertigungskomplexität: Die Herstellung von Leiterplatten mit hohen Aspect Ratios kann komplizierter und kostenintensiver sein. Die Präzision bei der Bearbeitung der Löcher muss hoch sein, um die gewünschte Qualität zu gewährleisten.
- Fehleranfälligkeit: Höhere Aspect Ratios können die Wahrscheinlichkeit von Fehlern wie unvollständigen Bohrungen oder verstopften Durchkontaktierungen erhöhen.
Anwendungen
Hochdichte Leiterplatten:
- Multilayer-Leiterplatten: In multilayer Leiterplatten werden oft hohe Aspect Ratios verwendet, um die Anzahl der Verbindungen und Schaltungen auf einem kleinen Raum zu maximieren.
Miniaturisierte Elektronik:
- Kompakte Geräte: In der Miniaturisierung elektronischer Geräte sind hohe Aspect Ratios nützlich, um die Komplexität und Anzahl der Verbindungen zu erhöhen, ohne die Größe der Leiterplatte zu vergrößern.
Fazit
Das Aspect Ratio ist ein kritischer Faktor im Leiterplattendesign und -herstellungsprozess, das die Machbarkeit und Leistung von Leiterplatten beeinflusst. Es beschreibt das Verhältnis zwischen der Tiefe und dem Durchmesser von Durchkontaktierungen oder Bohrungen und spielt eine wichtige Rolle bei der Planung und Fertigung von Leiterplatten. Das Verständnis und die korrekte Berücksichtigung des Aspect Ratios sind entscheidend, um sicherzustellen, dass die Leiterplatte zuverlässig gefertigt werden kann und die gewünschten elektrischen Eigenschaften bietet.
AU Aurum Leiterplatten beziehen sich auf Leiterplatten, die mit einer Goldbeschichtung (im Englischen: Gold Plating oder Gold Finish) versehen sind. „Aurum“ stammt vom lateinischen Wort für Gold und betont die Verwendung von Gold in der Beschichtung. In der Leiterplattenfertigung sind Goldbeschichtungen bekannt für ihre hervorragenden Eigenschaften bezüglich Korrosionsbeständigkeit und Lötbarkeit.
Was sind AU Aurum Leiterplatten?
Definition:
- AU Aurum Leiterplatten: Dies sind Leiterplatten, deren Kontaktflächen, insbesondere die Pads und die Oberflächen von Durchkontaktierungen (Vias), mit einer Schicht aus Gold beschichtet sind. Der Begriff „Aurum“ hebt die Verwendung von Gold hervor, was auf eine hochwertige und langlebige Beschichtung hinweist.
Goldbeschichtung:
- Verfahren: Die Goldbeschichtung wird durch elektrolytisches Goldplattieren erreicht, bei dem eine dünne Schicht Gold auf die Leiterplatte aufgetragen wird. Es kann auch durch chemisches Goldplattieren erfolgen, bei dem Gold ohne elektrischen Strom auf die Oberfläche aufgebracht wird.
Vorteile der Goldbeschichtung
Korrosionsbeständigkeit:
- Langlebigkeit: Gold ist extrem korrosionsbeständig und schützt die Leiterplatte vor Umwelteinflüssen wie Feuchtigkeit und Chemikalien. Dies trägt zur Langlebigkeit und Zuverlässigkeit der Leiterplatte bei.
Hervorragende Lötbarkeit:
- Zuverlässige Verbindungen: Gold bietet exzellente Lötbarkeit, da es nicht oxidiert und eine stabile Oberfläche für das Löten von Bauteilen bietet. Dies verbessert die Qualität der elektrischen Verbindungen und reduziert Lötfehler.
Widerstand gegen Abnutzung:
- Mechanische Stabilität: Die Goldschicht schützt die Leiterplatte vor mechanischem Abrieb und anderen physischen Schäden, die während des Betriebs auftreten können.
Anwendungen von AU Aurum Leiterplatten
High-End Elektronik:
- Kritische Anwendungen: AU Aurum Leiterplatten werden häufig in anspruchsvollen und kritischen Anwendungen eingesetzt, bei denen hohe Zuverlässigkeit und Leistung erforderlich sind, wie z. B. in der Luft- und Raumfahrt, Militärtechnik und Hochfrequenztechnik.
Verbraucherelektronik:
- Hochwertige Geräte: In hochpreisigen Verbraucherelektronikgeräten, wie z. B. in Audio- und Videoequipment, können AU Aurum Leiterplatten verwendet werden, um die Signalqualität zu verbessern und die Lebensdauer der Geräte zu verlängern.
Medizintechnik:
- Medizinische Geräte: In der Medizintechnik werden Goldbeschichtungen aufgrund ihrer Zuverlässigkeit und Langlebigkeit geschätzt, insbesondere in medizinischen Geräten, die präzise und beständige elektrische Verbindungen erfordern.
Nachteile und Herausforderungen
Kosten:
- Teuer: Goldbeschichtungen sind teurer als andere Oberflächenbeschichtungen wie Zinn oder Silber. Dies kann die Gesamtkosten der Leiterplatte erhöhen, was besonders bei großen Stückzahlen oder weniger kritischen Anwendungen eine Rolle spielen kann.
Verarbeitung:
- Komplexität: Der Prozess des Goldplattierens kann komplex und zeitaufwändig sein, was zusätzliche Herausforderungen und Anforderungen an die Fertigung stellt.
Fazit
AU Aurum Leiterplatten bieten signifikante Vorteile durch ihre Goldbeschichtung, insbesondere hinsichtlich Korrosionsbeständigkeit, Lötbarkeit und Widerstand gegen mechanische Abnutzung. Sie sind besonders geeignet für Anwendungen, die hohe Zuverlässigkeit und eine lange Lebensdauer der Leiterplatten erfordern. Trotz der höheren Kosten und der komplexeren Fertigungstechnologie bieten sie eine hervorragende Leistung, die sich in kritischen und anspruchsvollen Elektronikbereichen auszahlt.
Vgl. auch → Gold
Der Aufbau einer Leiterplatte, auch bekannt als PCB (Printed Circuit Board), ist ein komplexer Prozess, der mehrere Schichten und Komponenten umfasst, um elektrische Verbindungen herzustellen und elektronische Schaltungen zu unterstützen. Hier ist eine detaillierte Übersicht über die verschiedenen Phasen und Komponenten, die den Aufbau einer typischen Leiterplatte ausmachen:
Design und Planung
Schaltplan-Erstellung:
- Elektronische Schaltung: Der Schaltplan ist eine schematische Darstellung der elektrischen Verbindungen und Bauteile in der Schaltung. Dieser Plan wird mithilfe von EDA-Software (Electronic Design Automation) erstellt.
Leiterplattendesign:
- Layout: Nach dem Schaltplan wird das Layout der Leiterplatte entworfen. Dies umfasst die Platzierung der Bauteile und das Routing der Leiterbahnen, die die elektrischen Verbindungen zwischen den Bauteilen herstellen.
Materialien
Basismaterial:
- Leiterplattenmaterial: Die meisten Leiterplatten bestehen aus einem substrat-Material, das typischerweise aus FR-4 (Glasfaserverstärktes Epoxidharz) besteht. Dieses Material sorgt für mechanische Festigkeit und elektrische Isolierung.
Kupferfolie:
- Leiterbahnen: Eine dünne Schicht aus Kupferfolie wird auf das Basismaterial aufgebracht. Diese Kupferfolie bildet die Leiterbahnen, die die elektrischen Verbindungen auf der Leiterplatte herstellen.
Herstellungsprozess
Film-Erstellung:
- Maskierung: Ein Film wird erstellt, der die Schaltkreise darstellt und auf die Kupferfolie aufgebracht wird. Dies dient als Vorlage für das spätere Ätzen.
Ätzen:
- Kupferentfernung: Überflüssiges Kupfer wird durch Ätzen entfernt, wobei nur die gewünschten Leiterbahnen und Pads auf der Leiterplatte verbleiben. Dieser Schritt wird durch chemische Prozesse durchgeführt.
Bohrung:
- Durchkontaktierungen: Löcher werden gebohrt, um die Leiterplatte für Durchkontaktierungen und Bauteilanschlüsse vorzubereiten. Diese Löcher sind wichtig für die Verbindung der verschiedenen Schichten einer Mehrschicht-Leiterplatte.
Löten:
- Verbindung: Die Bauteile werden auf der Leiterplatte befestigt und durch Löten an den Leiterbahnen verbunden. Hierbei wird entweder durch Wellenlöten oder durch Reflow-Löten gearbeitet, abhängig von der Art der Bauteile.
Veredlung:
- Oberflächenbeschichtung: Verschiedene Oberflächenbeschichtungen werden aufgetragen, um die Leiterplatte zu schützen und die Lötbarkeit zu verbessern. Dies kann Goldbeschichtung (ENIG), Zinnbeschichtung (HASL) oder andere Beschichtungen umfassen.
Qualitätskontrolle
Optische Inspektion:
- Visuelle Prüfung: Die Leiterplatte wird visuell auf Fehler, wie z. B. Lötfehler oder defekte Leiterbahnen, überprüft.
Elektrische Tests:
- E-Test: Leiterplatten werden auf elektrische Fehler, wie Kurzschlüsse oder offene Verbindungen, getestet.
Mechanische Prüfungen:
- Maßhaltigkeit: Überprüfung der Abmessungen und Toleranzen der Leiterplatte, um sicherzustellen, dass sie den Design-Spezifikationen entsprechen.
Verpackung und Versand
Schutz:
- Verpackung: Die fertigen Leiterplatten werden in Schutzhüllen verpackt, um sie während des Transports und der Lagerung vor physikalischen Schäden zu schützen.
Versand:
- Lieferung: Die Leiterplatten werden an den Kunden oder zur weiteren Montage und Integration versandt.
Aufbau einer Leiterplatte im Detail
Einseitige Leiterplatte:
- Ein Schichtaufbau: Besteht aus einer einzigen Kupferschicht auf einer Seite des Substrats. Einfach und kostengünstig, geeignet für weniger komplexe Schaltungen.
Zweischichtige Leiterplatte:
- Zwei Schichten: Kupferlagen auf beiden Seiten des Substrats, verbunden durch Durchkontaktierungen. Bietet mehr Flexibilität bei der Schaltungsanordnung.
Mehrschichtige Leiterplatte:
- Mehrere Schichten: Mehrere Kupferschichten sind durch isolierende Schichten getrennt und durch Durchkontaktierungen verbunden. Ermöglicht komplexe und kompakte Designs mit vielen Verbindungen.
Flex-Leiterplatte:
- Flexibles Material: Besteht aus flexiblem Material, das es ermöglicht, die Leiterplatte in verschiedene Formen zu biegen oder zu rollen. Ideal für Anwendungen, die Beweglichkeit oder Platzersparnis erfordern.
Zusammenfassung
Der Aufbau einer Leiterplatte umfasst zahlreiche Schritte, von der anfänglichen Planung und dem Design über die Auswahl und Verarbeitung der Materialien bis hin zur Herstellung, Veredelung und Qualitätssicherung. Jede Phase ist entscheidend für die Qualität und Funktionalität der fertigen Leiterplatte. Durch die sorgfältige Ausführung und Kontrolle jedes Schrittes wird sichergestellt, dass die Leiterplatte zuverlässig und effektiv in den vorgesehenen elektronischen Geräten funktioniert.
Vgl. auch → Lagenaufbau
- AUSFRÄSEN
- AUSSENLAGE
- AUTOROUTER
Ausfräsen ist ein Verfahren, das in der Leiterplattenfertigung verwendet wird, um spezifische Teile der Leiterplatte zu bearbeiten oder zu entfernen. Dieser Prozess ist besonders nützlich, um präzise Ausschnitte, Anpassungen und die Herstellung von spezifischen Formen auf der Leiterplatte zu realisieren. Hier sind die Details und Anwendungen des Ausfräsens in der Leiterplattenfertigung:
Was ist Ausfräsen?
Definition:
- Ausfräsen: Das Ausfräsen ist ein mechanisches Bearbeitungsverfahren, bei dem Material von der Leiterplatte entfernt wird, um bestimmte Formen, Ausschnitte oder Anpassungen zu erstellen. Dies wird durch den Einsatz einer Fräse oder eines CNC-Fräsers (Computer Numerical Control) erreicht, der präzise Schneidbewegungen ausführt.
Verfahren:
- Fräsen: Beim Fräsen wird ein rotierendes Schneidwerkzeug verwendet, um Material von der Leiterplatte abzutragen. Der Fräsvorgang kann verschiedene Tiefen und Formen erzeugen, je nach den Anforderungen des Designs.
Anwendungen des Ausfräsens
Ausschnitte und Öffnungen:
- Bauteile: Um Bauteile in spezifischen Positionen zu platzieren oder zu sichern, können Ausschnitte oder Öffnungen in der Leiterplatte erstellt werden.
- Montage: Platz für Befestigungselemente oder Anschlüsse kann durch Ausfräsen geschaffen werden.
Formgebung:
- Spezielle Formen: Leiterplatten können in spezielle Formen oder Konturen gefräst werden, um Anpassungen an Gehäusen oder zur Integration in bestimmte Geräte zu ermöglichen.
Verbindungspads:
- Anpassungen: Gelegentlich müssen Verbindungspads oder Bereiche für spezifische Verbindungen oder Kontaktflächen durch Fräsen modifiziert werden.
Reduzierung des Materialaufwands:
- Leichtbau: Durch das Entfernen von überschüssigem Material kann das Gewicht der Leiterplatte reduziert werden, was besonders in Anwendungen mit Gewichtsbeschränkungen wichtig ist.
Vorteile des Ausfräsens
Präzision:
- Hohe Genauigkeit: Das Fräsen ermöglicht sehr präzise und wiederholbare Bearbeitungen, was zu exakten Ausschnitten und Formen führt.
Flexibilität:
- Designänderungen: Es erlaubt Anpassungen und Änderungen an der Leiterplatte nach dem Herstellungsprozess, um spezielle Anforderungen zu erfüllen.
Vielseitigkeit:
- Verschiedene Materialien: Das Verfahren kann auf eine Vielzahl von Materialien angewendet werden, einschließlich FR-4, flexiblen Materialien und anderen Leiterplattensubstraten.
Herausforderungen des Ausfräsens
Kosten:
- Zusätzliche Kosten: Das Fräsen kann zusätzliche Kosten verursachen, insbesondere wenn es sich um komplexe oder präzise Anforderungen handelt. Die Maschinen und Werkzeuge für das Fräsen sind oft kostenintensiv.
Materialverlust:
- Überflüssiges Material: Während des Fräsvorgangs wird Material entfernt, was zu Abfall führen kann. Dies kann die Materialkosten erhöhen und ist in Bezug auf Nachhaltigkeit weniger effizient.
Bearbeitungszeit:
- Zeitaufwand: Der Fräsprozess kann zeitaufwendig sein, insbesondere bei komplexen oder detaillierten Designs.
Schritte im Ausfräsprozess
Designvorbereitung:
- CAD-Daten: Die Design- und Fräsdaten werden in einer CAD-Software (Computer-Aided Design) erstellt und an die Fräsmaschine übergeben. Diese Daten enthalten genaue Anweisungen für die Fräse.
Werkstückfixierung:
- Sicherung: Die Leiterplatte wird sicher auf der Fräsmaschine befestigt, um sicherzustellen, dass sie sich während des Fräsvorgangs nicht bewegt.
Fräsen:
- Bearbeitung: Die Fräse wird aktiviert und führt den Schneidvorgang gemäß den Designvorgaben durch. Die Fräse entfernt Material, um die gewünschten Formen und Ausschnitte zu erzeugen.
Nachbearbeitung:
- Feinabstimmung: Nach dem Fräsen können zusätzliche Nachbearbeitungsschritte erforderlich sein, um Kanten zu glätten oder weitere Anpassungen vorzunehmen.
Fazit
Das Ausfräsen ist ein präzises und vielseitiges Verfahren zur Bearbeitung von Leiterplatten, das es ermöglicht, spezifische Formen, Öffnungen und Anpassungen zu erstellen. Trotz seiner Vorteile, wie hohe Genauigkeit und Flexibilität, können Kosten, Materialverlust und Zeitaufwand Herausforderungen darstellen. Es wird in vielen verschiedenen Anwendungen eingesetzt, um sicherzustellen, dass Leiterplatten den spezifischen Anforderungen und Designs der elektronischen Geräte entsprechen.
Vgl. auch → Fräsen
Die Außenlage einer Leiterplatte bezieht sich auf die äußeren Schichten einer Leiterplatte, die direkt mit der Umgebung in Kontakt stehen oder die äußeren Schichten einer mehrschichtigen Leiterplatte, die für die Verbindung mit anderen Komponenten oder Gehäusen verantwortlich sind. Hier sind die wichtigsten Aspekte der Außenlagen einer Leiterplatte:
Definition und Bedeutung
Äußere Schichten:
- Außenlage: Die Außenlagen einer Leiterplatte sind die Schichten, die sich an den äußeren Rändern der Leiterplatte befinden. Bei einer einlagigen Leiterplatte ist dies die einzige Schicht, bei mehrlagigen Leiterplatten sind es die obersten und untersten Schichten der gesamten Struktur.
Funktion:
- Elektrische Verbindungen: Sie enthalten die Leiterbahnen, Pads und andere elektrische Verbindungen, die notwendig sind, um Bauteile mit der Leiterplatte zu verbinden.
- Mechanische Befestigung: Sie spielen eine wichtige Rolle bei der Befestigung und dem mechanischen Schutz der Leiterplatte in einem Gehäuse oder einer Montageanordnung.
Eigenschaften und Anforderungen
Materialien:
- Basismaterial: Die Außenlagen bestehen typischerweise aus demselben Basismaterial wie die inneren Schichten, wie z. B. FR-4 (Glasfaserverstärktes Epoxidharz) oder andere Leiterplattensubstrate.
- Kupferbeschichtung: Diese Schichten sind mit einer dünnen Kupferfolie beschichtet, die die elektrischen Verbindungen und Leiterbahnen bildet.
Oberflächenbeschichtung:
- Schutzbeschichtung: Die Außenlagen sind oft mit Schutzschichten versehen, wie Lötstopplack (Solder Mask), um die Kupferbahnen vor Oxidation und Beschädigung zu schützen und Kurzschlüsse zu verhindern.
- Lötfläche: In Bereichen, wo Bauteile gelötet werden, kann eine spezielle Beschichtung wie HASL (Hot Air Solder Leveling) oder ENIG (Electroless Nickel Immersion Gold) aufgetragen werden, um die Lötbarkeit zu verbessern.
Design:
- Leiterbahnen und Pads: Das Design der Außenlagen umfasst die Platzierung von Leiterbahnen, Pads für Bauteile und gegebenenfalls auch Wärmeleitflächen oder Abschirmungen.
- Bauform: Die Außenlage beeinflusst die mechanische Form der Leiterplatte, einschließlich Ausschnitten, Bohrungen und Konturen, die für die Befestigung oder Anpassung an das Gehäuse notwendig sind.
Herstellungsprozess
Belichtung und Ätzen:
- Belichtung: Die äußeren Schichten werden belichtet, um die Muster der Leiterbahnen und Pads auf der Kupferfolie zu erstellen.
- Ätzen: Überflüssiges Kupfer wird durch Ätzen entfernt, um die gewünschten Leiterbahnmuster zu hinterlassen.
Löten und Beschichten:
- Löten: Bauteile werden auf den Pads der Außenlagen platziert und durch Löten verbunden.
- Beschichtung: Die Leiterplatte wird mit Schutzschichten versehen, um sie vor Umwelteinflüssen zu schützen.
Nachbearbeitung:
- Fräsen und Bohren: Gegebenenfalls werden zusätzliche Bearbeitungen wie Fräsen oder Bohren durchgeführt, um die Leiterplatte für die endgültige Montage vorzubereiten.
Typische Anwendungen
Konnektivität:
- Externe Verbindungen: Die Außenlagen sind entscheidend für die Herstellung von Verbindungen zwischen der Leiterplatte und externen Komponenten, wie z. B. Steckeranschlüssen, Schaltern und anderen Bauteilen.
Mechanische Integration:
- Gehäuse: Sie sind häufig die Schichten, die direkt mit dem Gehäuse oder der Montageplatte in Kontakt stehen, und müssen daher robust und mechanisch stabil sein.
Schutz und Haltbarkeit:
- Widerstandsfähigkeit: Die Außenlagen schützen die empfindlichen inneren Schichten vor physischen und chemischen Einflüssen, die die Leiterplatte beschädigen könnten.
Fazit
Die Außenlagen einer Leiterplatte sind essenziell für die Funktionalität, Mechanik und Schutz der gesamten Leiterplatte. Sie enthalten die entscheidenden elektrischen Verbindungen, die für die Kommunikation und Interaktion der Leiterplatte mit anderen Komponenten notwendig sind. Die sorgfältige Gestaltung und Bearbeitung der Außenlagen sind entscheidend für die Zuverlässigkeit und Leistung der fertigen Leiterplatte.
Vgl. auch → Top → Bottom
Der Autorouter ist ein Werkzeug in der Leiterplattendesign-Software, das automatisch die Verbindungen zwischen den Bauteilen einer Leiterplatte routet, also die Leiterbahnen entwirft, die elektrische Verbindungen herstellen. Hier sind die wesentlichen Aspekte des Autorouters und seiner Funktion im Designprozess von Leiterplatten:
Was ist ein Autorouter?
Definition:
- Autorouter: Ein Autorouter ist eine Funktion oder Software innerhalb von Electronic Design Automation (EDA)-Tools, die automatisch die Leiterbahnen auf einer Leiterplatte basierend auf einem vorgegebenen Schaltplan anordnet und routet.
Funktion:
- Automatische Verlegung: Der Autorouter übernimmt die Aufgabe, die Verbindungen zwischen den Bauteilen ohne manuelle Eingriffe zu erstellen. Er berücksichtigt dabei Designregeln wie Abstand, Leitungslängen und elektrische Anforderungen.
Wie funktioniert der Autorouter?
Eingabedaten:
- Schaltplan: Der Autorouter benötigt einen vollständig erstellten Schaltplan, der die logischen Verbindungen zwischen den Bauteilen beschreibt.
- Bauteilplatzierung: Die Bauteile müssen bereits auf der Leiterplatte platziert sein oder die Platzierung wird durch den Autorouter ebenfalls automatisch optimiert.
Routing-Algorithmus:
- Algorithmen: Der Autorouter verwendet verschiedene Algorithmen, um die beste Routing-Strategie zu finden. Zu den häufig verwendeten Algorithmen gehören A-Algorithmus*, Dijkstra-Algorithmus oder spezielle Heuristiken für das Routing.
- Designregeln: Er beachtet die festgelegten Designregeln, wie Mindestabstände zwischen Leiterbahnen, Leiterbahnbreiten und andere physikalische oder elektrische Anforderungen.
Ergebnisse und Anpassungen:
- Automatische Verbindungen: Der Autorouter erstellt die Leiterbahnen und Verbindungen entsprechend den Designregeln.
- Nachbearbeitung: Oftmals sind manuelle Anpassungen erforderlich, um die Routing-Qualität zu verbessern oder um spezifische Anforderungen zu erfüllen. Der automatisch generierte Entwurf kann nachträglich optimiert werden, um die Leistung oder Layout-Effizienz zu verbessern.
Vorteile des Autorouters
Zeiteinsparung:
- Schnelligkeit: Der Autorouter kann viel schneller Leiterbahnen routen als eine manuelle Methode, was den gesamten Designprozess beschleunigt.
Fehlerreduktion:
- Konsistenz: Durch die automatische Anwendung von Designregeln wird die Wahrscheinlichkeit von Fehlern reduziert, die bei manuellen Routings auftreten könnten.
Optimierung:
- Effizienz: Der Autorouter kann oft optimierte Routing-Pfade finden, die weniger Leiterbahnen oder kürzere Verbindungen erfordern, was zu einem kompakteren Layout führt.
Nachteile und Herausforderungen
Designqualität:
- Komplexität: Bei sehr komplexen Designs oder speziellen Anforderungen kann der Autorouter Schwierigkeiten haben, optimale Ergebnisse zu liefern. Manuelle Eingriffe sind oft notwendig, um die besten Ergebnisse zu erzielen.
Flexibilität:
- Begrenzte Anpassungen: Der Autorouter ist auf vorgegebene Regeln und Algorithmen angewiesen, was in einigen Fällen die Flexibilität einschränkt, insbesondere bei nicht-standardisierten Anforderungen oder speziellen Layouts.
Platzierung und Routing:
- Anpassung: In einigen Fällen kann die Platzierung der Bauteile auf der Leiterplatte durch den Autorouter nicht optimal genutzt werden, was zu suboptimalen Ergebnissen führen kann.
Einsatzmöglichkeiten
Prototypen:
- Schnelle Entwicklung: Autorouter werden oft für die schnelle Erstellung von Prototypen verwendet, um die Designzeit zu verkürzen.
Komplexe Schaltungen:
- Effizienz: Bei komplexen Schaltungen, die viele Verbindungen und Bauteile enthalten, kann der Autorouter helfen, die Routing-Aufgaben effizient zu bewältigen.
Design-Optimierung:
- Optimale Nutzung: Er kann als erstes Werkzeug zur Erstellung eines Routing-Entwurfs verwendet werden, der dann weiter manuell optimiert wird.
Fazit
Der Autorouter ist ein leistungsstarkes Werkzeug im Leiterplattendesign, das die Erstellung von Leiterbahnen automatisiert und den Designprozess erheblich beschleunigt. Während er zahlreiche Vorteile bietet, wie Zeitersparnis und Fehlerreduktion, kann er in bestimmten Situationen zusätzliche manuelle Feinabstimmungen erfordern, um die besten Ergebnisse zu erzielen. Der Autorouter ist ein wichtiger Bestandteil moderner EDA-Software und wird sowohl in der schnellen Prototypenerstellung als auch in der Entwicklung komplexer elektronischer Schaltungen eingesetzt.
Vgl. auch → Rastnest → Entflechtung → Routing → Design Rules
- BASISKUPFER
- BASISMATERIAL
- BAUGRUPPE
- BAUTEIL
- BAUTEILSEITE
Basiskupfer und Erstkupfer sind Begriffe, die sich auf die Kupferbeschichtung und -schicht auf Leiterplatten beziehen. Beide Begriffe beziehen sich auf unterschiedliche Phasen der Kupferverarbeitung in der Herstellung von Leiterplatten.
Basiskupfer
Basiskupfer bezeichnet die erste, grundlegende Kupferschicht, die auf der Leiterplatte aufgebracht wird, um eine leitfähige Grundlage für die weiteren Schichten zu bieten. Es ist die Kupferschicht, die direkt auf das Substrat (z.B. auf das FR-4- oder andere Leiterplattenmaterialien) aufgebracht wird. Hier sind die wichtigsten Aspekte des Basiskupfers:
Funktion:
- Leitfähigkeit: Basiskupfer dient als Basis für die elektrische Leitfähigkeit der Leiterplatte. Es bildet die Grundlage, auf der die Leiterbahnen, Pads und andere leitfähige Strukturen aufgebaut werden.
Dicke:
- Kupferdicke: Die Dicke des Basiskupfers variiert je nach Anforderungen der Leiterplatte. Typische Dicken liegen im Bereich von 18 µm bis 35 µm (0,5 oz/ft² bis 1 oz/ft²). Für spezielle Anwendungen können auch dickere Schichten verwendet werden.
Herstellung:
- Beschichtung: Das Basiskupfer wird in der Regel durch ein elektrochemisches Beschichtungsverfahren aufgebracht. Dies geschieht oft während des Produktionsprozesses, in dem das Kupfer auf das isolierende Substrat galvanisch aufgebracht wird.
Erstkupfer
Erstkupfer bezeichnet die Kupferschicht, die nach der Bearbeitung und Ätzung des Basiskupfers aufgebracht wird. Es kann sich auf zusätzliche Kupferschichten beziehen, die für spezielle Zwecke wie verstärkte Leiterbahnen oder besondere Layoutanforderungen hinzugefügt werden. Hier sind die wichtigen Aspekte des Erstkupfers:
Funktion:
- Verstärkung: Erstkupfer wird oft verwendet, um bestimmte Bereiche der Leiterplatte, wie z.B. Leiterbahnen oder Pads, zu verstärken. Dies ist wichtig für die Verbesserung der Stromtragfähigkeit oder die Erhöhung der mechanischen Festigkeit von Leiterbahnen.
Dicke und Anwendung:
- Verstärkung: Die Dicke des Erstkupfers kann variieren und wird oft in Bereichen angewendet, in denen zusätzliche Leitfähigkeit oder Festigkeit benötigt wird. Typischerweise wird Erstkupfer in Anwendungen wie Hochstromleitungen oder Verstärkungen verwendet.
Herstellung:
- Galvanisierung: Erstkupfer wird meist durch elektrolytische Galvanisierung aufgebracht, bei der eine zusätzliche Schicht Kupfer auf die bereits bestehende Schicht aufgebracht wird. Dieser Schritt erfolgt nach der Ätzung und beim Hinzufügen von zusätzlichen Kupferstrukturen.
Vergleich und Zusammenfassung
Basiskupfer ist die Grundschicht der Kupferbeschichtung, die direkt auf das Substrat aufgebracht wird und die Basis für die Leiterbahnstruktur bildet. Es hat die Aufgabe, die grundlegende elektrische Leitfähigkeit zu gewährleisten.
Erstkupfer bezieht sich auf zusätzliche Kupferschichten, die nach der ersten Kupferbeschichtung aufgebracht werden. Diese Schichten werden oft verwendet, um bestimmte Bereiche der Leiterplatte zu verstärken und die Leistung oder mechanische Stabilität zu erhöhen.
Beide Kupferschichten spielen eine wichtige Rolle in der Leiterplattenherstellung, wobei das Basiskupfer die Grundlage bildet und das Erstkupfer zusätzliche Funktionalität und Verstärkung bietet.
Vgl. auch → Basismaterial
Basismaterial für Leiterplatten bezeichnet das Hauptsubstrat, auf dem die elektrische Leitbahnen, Lötpads und andere Strukturen aufgebracht werden. Es ist der grundlegende Träger, der die mechanische und elektrische Grundlage für die Leiterplatte bietet. Hier sind die wichtigsten Aspekte des Basismaterials für Leiterplatten:
Typen von Basismaterialien
1.1. FR-4
- Beschreibung: FR-4 ist der am häufigsten verwendete Typ von Basismaterial für Leiterplatten. Es handelt sich um ein glasfaserverstärktes Epoxidharz.
- Eigenschaften: Gute elektrische Isolierung, hohe Temperaturbeständigkeit, mechanische Stabilität und geringe Feuchtigkeitsaufnahme. FR-4 ist kostengünstig und vielseitig einsetzbar.
- Anwendung: Standardanwendungen in der Elektronik, von Konsumgütern bis zu Industrieelektronik.
1.2. CEM-1 und CEM-3
- Beschreibung: CEM-1 ist ein Papier-basierter Verbundwerkstoff, während CEM-3 ein glasfaserverstärkter Epoxidharzverbundwerkstoff ist, der kostengünstiger ist als FR-4.
- Eigenschaften: Geringere Kosten im Vergleich zu FR-4, jedoch etwas weniger robust und feuchtigkeitsbeständig. CEM-3 bietet ähnliche Eigenschaften wie FR-4, ist jedoch in der Regel weniger widerstandsfähig.
- Anwendung: CEM-1 wird häufig für einfache, einlagige Leiterplatten verwendet, während CEM-3 oft für mehrlagige Leiterplatten in kostensensitiven Anwendungen verwendet wird.
1.3. Polyimid
- Beschreibung: Polyimid ist ein Hochleistungsmaterial, das für seine hervorragenden thermischen und chemischen Eigenschaften bekannt ist.
- Eigenschaften: Sehr hohe Temperaturbeständigkeit, chemische Beständigkeit und mechanische Festigkeit. Polyimid hat eine ausgezeichnete dielektrische Eigenschaft.
- Anwendung: Anwendungen in extremen Umgebungen, wie in der Raumfahrt, Automobilindustrie und Hochfrequenztechnik.
1.4. PTFE (Polytetrafluorethylen)
- Beschreibung: PTFE ist ein Material mit herausragenden elektrischen Eigenschaften und geringer Dielektrizitätskonstante.
- Eigenschaften: Sehr niedriger Dielektrizitätswert, hohe Temperaturbeständigkeit und chemische Beständigkeit.
- Anwendung: Hohe Frequenz- und Mikrowellenanwendungen, wie in der Hochfrequenz- und Kommunikationsindustrie.
1.5. Aluminiumkern
- Beschreibung: Leiterplatten mit einem Aluminiumkern bestehen aus einer Aluminiumschicht, die eine thermische Ableitung ermöglicht.
- Eigenschaften: Gute Wärmeableitung, mechanische Festigkeit und niedriges Gewicht. Ideal für Anwendungen, bei denen hohe Wärme entwickelt wird.
- Anwendung: Hochleistungs-LED-Beleuchtung, Leistungsbauelemente und andere Anwendungen, bei denen Wärme effizient abgeführt werden muss.
Eigenschaften des Basismaterials
2.1. Dielektrizitätskonstante (Dk):
- Beschreibung: Die dielektrische Konstante eines Materials beeinflusst die elektrische Signalübertragung. Ein niedrigerer Dk-Wert bedeutet geringere Signalverluste und eine höhere Geschwindigkeit der Signalübertragung.
2.2. Wärmeleitfähigkeit:
- Beschreibung: Die Fähigkeit des Materials, Wärme abzuleiten, ist wichtig für Anwendungen mit hoher Leistungsdichte. Materialien mit hoher Wärmeleitfähigkeit sind für solche Anwendungen besser geeignet.
2.3. Mechanische Festigkeit:
- Beschreibung: Das Basismaterial muss mechanisch stabil sein, um die Leiterplatte während der Herstellung und im Betrieb zu unterstützen. Eine hohe mechanische Festigkeit verhindert Risse und Verformungen.
2.4. Feuchtigkeitsaufnahme:
- Beschreibung: Die Fähigkeit des Materials, Feuchtigkeit aufzunehmen, beeinflusst seine Leistung und Lebensdauer. Materialien mit niedriger Feuchtigkeitsaufnahme sind widerstandsfähiger gegen Umgebungsbedingungen.
2.5. Temperaturbeständigkeit:
- Beschreibung: Das Basismaterial muss den Temperaturen während des Betriebs und der Herstellung standhalten. Materialien mit hoher Temperaturbeständigkeit sind für Anwendungen mit extremen Temperaturen besser geeignet.
Auswahlkriterien
Bei der Auswahl des Basismaterials für Leiterplatten müssen folgende Faktoren berücksichtigt werden:
- Anwendung: Bestimmte Anwendungen erfordern spezielle Eigenschaften wie hohe Temperaturbeständigkeit oder geringe dielektrische Verluste.
- Kosten: Der Preis des Materials kann je nach Leistungsfähigkeit und Spezifikationen variieren.
- Umgebung: Die Umgebungsbedingungen, wie Temperatur und Feuchtigkeit, beeinflussen die Wahl des geeigneten Basismaterials.
Fazit
Das Basismaterial für Leiterplatten bildet die Grundlage für die gesamte elektrische und mechanische Struktur der Leiterplatte. Die Wahl des richtigen Basismaterials ist entscheidend für die Leistung, Zuverlässigkeit und Kosteneffizienz der Leiterplatte. Verschiedene Materialien bieten unterschiedliche Eigenschaften, die für spezifische Anwendungen und Anforderungen optimiert sind.
Vgl. auch → FR4 → Aluminium →Polimid →Teflon → Pertinax
In Bezug auf Leiterplatten bezeichnet der Begriff Baugruppe ein vollständig zusammengebautes und funktionsfähiges Modul oder System, das eine oder mehrere Leiterplatten (PCBs) sowie zusätzliche Komponenten und Baugruppen umfasst. Hier sind die wesentlichen Aspekte einer Baugruppe:
Was ist eine Baugruppe?
Baugruppe ist ein umfassender Begriff, der eine komplette Assemblierung von Leiterplatten und anderen elektronischen Bauteilen beschreibt. Die Baugruppe besteht nicht nur aus der Leiterplatte selbst, sondern auch aus allen auf der Leiterplatte montierten Komponenten, wie z.B. Widerständen, Kondensatoren, integrierten Schaltungen (ICs), Steckverbindern und anderen Bauteilen.
Komponenten einer Baugruppe
Leiterplatte (PCB):
- Basis: Die Leiterplatte ist die Grundlage der Baugruppe, auf der die elektrischen Verbindungen und Schaltungen realisiert werden. Sie enthält die Leiterbahnen, Lötpads und mechanischen Montagestrukturen.
Bestückte Bauteile:
- Elektronische Komponenten: Auf der Leiterplatte sind verschiedene Bauteile wie Widerstände, Kondensatoren, Transistoren, ICs und andere elektronische Komponenten montiert. Diese Bauteile werden durch Lötprozesse oder andere Verbindungstechniken auf der Leiterplatte befestigt.
Mechanische Komponenten:
- Gehäuse und Befestigungen: Mechanische Teile wie Gehäuse, Halterungen, Schrauben und Abdeckungen gehören ebenfalls zur Baugruppe. Diese Teile sorgen für die physische Stabilität und den Schutz der elektronischen Komponenten.
Verbindungselemente:
- Steckverbinder und Anschlüsse: Baugruppen enthalten oft Steckverbinder und Anschlüsse, die eine Verbindung zu anderen Baugruppen oder externen Geräten ermöglichen.
Herstellung und Montage einer Baugruppe
Design und Layout:
- PCB-Design: Der erste Schritt bei der Herstellung einer Baugruppe ist das Design der Leiterplatte, das die elektrische Schaltung und die Platzierung der Bauteile festlegt.
Bestückung:
- Bestückungsprozesse: Nach der Fertigung der Leiterplatte werden die Bauteile auf der Leiterplatte platziert und verlötet. Dies kann durch manuelle Bestückung, automatisierte Maschinen (Pick-and-Place) oder eine Kombination von beiden erfolgen.
Verkabelung und Integration:
- Verbindung von Baugruppen: In vielen Fällen werden mehrere Leiterplatten oder Baugruppen miteinander verbunden, um ein komplettes System zu bilden. Diese Verbindungen können über Kabel, Steckverbinder oder andere Verbindungselemente erfolgen.
Tests und Prüfung:
- Funktionsprüfung: Nach der Montage wird die Baugruppe getestet, um sicherzustellen, dass alle elektronischen Funktionen korrekt arbeiten und die Baugruppe den Spezifikationen entspricht.
Gehäuseteil:
- Verpackung: Schließlich werden die Baugruppen in ein Gehäuse eingebaut oder anderweitig verpackt, um sie vor Umwelteinflüssen zu schützen und die Handhabung zu erleichtern.
Anwendungsbeispiele
Consumer Electronics:
- Beispiel: In einem Smartphone ist die Hauptbaugruppe das Haupt-Board, das die zentrale Leiterplatte enthält, auf der alle wesentlichen Komponenten wie Prozessor, Speicher und Kommunikationsmodule montiert sind.
Industrielle Anwendungen:
- Beispiel: In einem Industrie-Controller können mehrere Baugruppen in einem Gehäuse integriert sein, jede mit einer spezifischen Funktion, wie z.B. Steuerung, Kommunikation oder Signalverarbeitung.
Medizinische Geräte:
- Beispiel: In einem medizinischen Diagnosegerät besteht die Baugruppe aus mehreren Leiterplatten und Komponenten, die die gesamte Funktionalität des Geräts gewährleisten.
Fazit
Eine Baugruppe ist eine vollständige und funktionsfähige Assemblierung von Leiterplatten und weiteren elektronischen sowie mechanischen Komponenten. Sie bildet das Herzstück vieler elektronischer Geräte und Systeme und umfasst sowohl die elektrische als auch die mechanische Integration aller Teile. Die Herstellung einer Baugruppe beinhaltet das Design, die Bestückung, das Testen und das Verpacken, um ein zuverlässiges und funktionsfähiges Endprodukt zu gewährleisten.
In Bezug auf Leiterplatten (PCBs) sind Bauteile elektronische Komponenten, die auf der Leiterplatte montiert und für die Erfüllung bestimmter Funktionen innerhalb des elektrischen Schaltkreises verantwortlich sind. Diese Bauteile bilden zusammen mit der Leiterplatte das komplette elektronische System. Hier sind die wesentlichen Aspekte von Bauteilen auf Leiterplatten:
Typen von Bauteilen
Passivbauteile
- Widerstände (Resistoren): Widerstände begrenzen den Stromfluss und setzen eine bestimmte Spannung in einer Schaltung um. Sie sind in verschiedenen Widerstandswerten erhältlich und können in verschiedenen Formaten wie SMD (Surface-Mount Device) oder bedrahtet vorliegen.
- Kondensatoren (Capacitors): Kondensatoren speichern elektrische Energie in einem elektrischen Feld. Sie werden zur Glättung von Spannungen, zur Frequenzfilterung und für viele andere Zwecke verwendet. Sie sind ebenfalls in SMD- oder bedrahteter Form erhältlich.
- Induktivitäten (Inductors): Induktivitäten speichern Energie in einem Magnetfeld, wenn Strom durch sie fließt. Sie werden häufig in Filtern und zur Energieübertragung verwendet.
Aktivbauteile
- Transistoren: Transistoren sind Halbleiterbauelemente, die als Schalter oder Verstärker fungieren. Sie sind entscheidend für die Signalverarbeitung und die Steuerung in Schaltungen.
- Integrierte Schaltkreise (ICs): ICs sind komplexe Schaltungen, die viele Transistoren und andere Bauelemente auf einem einzigen Chip vereinen. Sie können alles von einfachen Logikgattern bis hin zu Mikroprozessoren und Speicherbausteinen enthalten.
- Dioden: Dioden ermöglichen den Stromfluss nur in eine Richtung und werden für Gleichrichtung, Schutz und Spannungsregulierung verwendet.
Elektromechanische Bauteile
- Relais: Relais sind Schalter, die durch einen elektromagnetischen Mechanismus betätigt werden. Sie ermöglichen die Steuerung großer Ströme oder Spannungen durch kleine Steuersignale.
- Schalter und Taster: Diese Bauteile ermöglichen die manuelle Steuerung oder Auswahl von Funktionen in einem Gerät.
Verbindungselemente
- Steckverbinder: Steckverbinder stellen elektrische Verbindungen zwischen verschiedenen Baugruppen oder Komponenten her. Sie sind in verschiedenen Typen wie Pin-Headern, Buchsen und RJ45-Verbindern erhältlich.
- Klemmen und Anschlüsse: Diese Bauteile bieten eine Möglichkeit zur Verbindung von externen Kabeln oder Leitungen mit der Leiterplatte.
Sensoren und Aktuatoren
- Sensoren: Sensoren messen physikalische Größen wie Temperatur, Licht oder Druck und wandeln diese in elektrische Signale um.
- Aktuatoren: Aktuatoren sind Bauteile, die elektrische Signale in mechanische Bewegungen umsetzen, wie z.B. Motoren oder Servomechanismen.
Funktionen der Bauteile
- Signalverarbeitung: Bauteile wie Transistoren und ICs verarbeiten und verstärken elektrische Signale.
- Strom- und Spannungsregulierung: Widerstände, Kondensatoren und Dioden helfen, die Strom- und Spannungswerte in einer Schaltung zu regulieren und zu stabilisieren.
- Energieübertragung und -speicherung: Induktivitäten und Kondensatoren speichern und übertragen elektrische Energie.
- Schutz und Steuerung: Dioden und Relais schützen Schaltungen vor Überlastungen und ermöglichen die Steuerung von Hochstromkreisen.
Montagemethoden
- Durchsteckmontage (Through-Hole): Bei der Durchsteckmontage werden die Bauteile durch Löcher in der Leiterplatte gesteckt und auf der gegenüberliegenden Seite verlötet.
- Oberflächenmontage (SMD – Surface-Mount Device): Bei der Oberflächenmontage werden die Bauteile direkt auf die Oberfläche der Leiterplatte gelötet, ohne dass Löcher erforderlich sind.
Fazit
Bauteile sind die grundlegenden Komponenten, die auf Leiterplatten montiert werden, um elektrische Schaltungen zu realisieren und spezifische Funktionen innerhalb eines elektronischen Systems zu erfüllen. Sie umfassen eine Vielzahl von passiven und aktiven Elementen, elektromechanischen Komponenten sowie Verbindungselementen. Die Auswahl und Platzierung der Bauteile auf einer Leiterplatte sind entscheidend für die Funktionalität und Leistung des gesamten elektronischen Geräts.
Vgl. auch → SMD → THT
Merkmale der Bauteilseite
Montagefläche
- Bestückung: Die Bauteilseite ist der Bereich der Leiterplatte, auf dem die Bauteile platziert und befestigt werden. Bei der Bestückung werden Bauteile entweder durch Löcher (Durchsteckmontage) gesteckt oder direkt auf die Oberfläche (Oberflächenmontage) gelötet.
- Layout: Die Bauteilseite enthält die Lötpads und Platzierungsmarkierungen, die für das Einlöten der Bauteile erforderlich sind. Diese Pads sind oft mit den Leiterbahnen der Leiterplatte verbunden, die elektrische Verbindungen zwischen den Bauteilen herstellen.
Kennzeichnung und Layout
- Silkscreen-Schicht: Auf der Bauteilseite wird oft eine Silkscreen-Schicht aufgebracht, die Text, Symbole und Markierungen enthält, um die Position und Identifikation der Bauteile zu erleichtern. Diese Schicht hilft bei der visuellen Inspektion und Bestückung der Leiterplatte.
- Platzierung: Das Layout auf der Bauteilseite muss sorgfältig geplant werden, um sicherzustellen, dass die Bauteile korrekt platziert sind und keine Kurzschlüsse oder Verbindungsprobleme auftreten.
Elektrische Verbindungen
- Lötpads und Leiterbahnen: Die Bauteilseite enthält Lötpads, auf denen die Bauteile befestigt werden. Diese Pads sind mit Leiterbahnen verbunden, die die elektrischen Verbindungen zwischen den Bauteilen herstellen. Die Leiterbahnen verlaufen oft durch die Leiterplatte und können von der Bauteilseite auf die Rückseite (Lötseite) führen.
Schutz und Wartung
- Beschichtung: In einigen Fällen kann die Bauteilseite mit einer Schutzschicht, wie z.B. einer Lötstopplackierung, versehen sein, um die Bauteile vor Feuchtigkeit und mechanischen Schäden zu schützen.
- Zugang: Die Bauteilseite ist oft die Seite der Leiterplatte, die für Wartungs- und Reparaturarbeiten zugänglich ist, da die Bauteile hier leicht identifiziert und ersetzt werden können.
Vergleich zur Lötseite
- Lötseite: Die Lötseite ist die gegenüberliegende Seite der Leiterplatte, auf der die Lötstellen für die Durchsteckbauteile sichtbar sind. Bei der Durchsteckmontage werden die Bauteile durch Löcher in der Leiterplatte gesteckt und auf der Lötseite verlötet. Diese Seite enthält die Lötpunkte und kann ebenfalls Leiterbahnen enthalten, die die Bauteile elektrisch verbinden.
Anwendung und Bedeutung
- Design und Fertigung: Beim Design der Leiterplatte muss die Bauteilseite so gestaltet werden, dass sie den spezifischen Anforderungen des Schaltplans und der Bestückung entspricht. Die korrekte Platzierung der Bauteile auf der Bauteilseite ist entscheidend für die Funktionalität und Leistungsfähigkeit der Leiterplatte.
- Bestückung: Die Bauteilseite ist der Hauptfokus während der Bestückung und Löten von Bauteilen, da sie die sichtbare und bearbeitbare Oberfläche für diese Prozesse darstellt.
Fazit
Die Bauteilseite einer Leiterplatte ist der zentrale Bereich, auf dem die elektronischen Bauteile montiert und elektrisch verbunden werden. Sie enthält wichtige Elemente wie Lötpads, Silkscreen-Markierungen und Platzierungsdetails, die für die korrekte Funktion und Montage der Leiterplatte entscheidend sind. Die sorgfältige Gestaltung und Pflege der Bauteilseite sind unerlässlich, um die Zuverlässigkeit und Leistungsfähigkeit des gesamten elektronischen Systems zu gewährleisten.
- BELICHTEN
- BESTÜCKUNG
- BESTÜCKUNGSDRUCK
- BESTÜCKUNGSPLAN
- BESTÜCKUNGSSEITE
Belichten ist ein entscheidender Prozess in der Leiterplattenherstellung, der für die Erstellung der Schaltungslayouts auf der Leiterplatte verantwortlich ist. Dieser Schritt ist Teil des sogenannten Fotolithografie-Verfahrens, das verwendet wird, um die Leiterbahnen und andere elektrische Verbindungen auf der Leiterplatte präzise zu übertragen. Hier sind die wesentlichen Aspekte und Schritte des Belichtungsprozesses:
Vorbereitung
Leiterplatten-Substrat: Zunächst wird die Leiterplatte vorbereitet, indem sie mit einer lichtempfindlichen Schicht (Photolack oder Fotolack) beschichtet wird. Diese Schicht reagiert auf UV-Licht und ermöglicht es, das Design auf die Leiterplatte zu übertragen.
Film oder Belichtungsmaske: Ein Film oder eine Belichtungsmaske, der das Schaltplan-Design enthält, wird vorbereitet. Dieser Film ist in der Regel transparent, wobei die Bereiche, die nicht belichtet werden sollen, opak sind.
Belichtungsprozess
Positionierung: Die Leiterplatte mit der lichtempfindlichen Schicht und der Belichtungsmaske wird in einer Belichtungsmaschine positioniert. Die Belichtungsmaschine verwendet UV-Licht, um das Design auf die Leiterplatte zu übertragen.
Belichtung: Die UV-Lichtquelle der Belichtungsmaschine strahlt durch die Belichtungsmaske auf die lichtempfindliche Schicht der Leiterplatte. Die UV-Strahlen härten den Photolack in den Bereichen aus, die durch die Maske hindurch beleuchtet werden. Die Bereiche, die von der Maske abgedeckt sind, bleiben unverändert.
Entwicklung
- Entwicklung der Leiterplatte: Nach der Belichtung wird die Leiterplatte in eine Entwicklungslösung getaucht oder durch eine Entwicklungslinie geführt. Die Entwicklungslösung entfernt den nicht ausgehärteten Photolack, sodass das Design auf der Leiterplatte sichtbar wird. Die Belichtungsmaske hat die Leiterbahnen und andere Designelemente auf der Leiterplatte hinterlassen.
Ätzen
- Ätzprozess: Die nun belichtete und entwickelte Leiterplatte wird in ein Ätzbad getaucht, das die freiliegenden Kupferflächen entfernt. Das Ätzen entfernt das Kupfer, das nicht durch den Photolack geschützt ist, wodurch die gewünschten Leiterbahnen und Verbindungen auf der Leiterplatte übrig bleiben.
Reinigung
- Entfernen des Photolacks: Nach dem Ätzprozess wird die Leiterplatte gereinigt, um den verbleibenden Photolack zu entfernen und die Leiterplatte für die nächste Bearbeitungsschritte vorzubereiten.
Vorteile des Belichtungsprozesses
- Hohe Präzision: Der Belichtungsprozess ermöglicht die präzise Übertragung von komplexen Schaltungslayouts auf die Leiterplatte, wodurch eine hohe Fertigungsgenauigkeit erreicht wird.
- Wiederholgenauigkeit: Durch den Einsatz von Masken und Filmen kann der Belichtungsprozess konsistent und wiederholbar durchgeführt werden, was wichtig für die Massenproduktion von Leiterplatten ist.
Fazit
Belichten ist ein wesentlicher Schritt in der Leiterplattenherstellung, der es ermöglicht, das elektrische Design auf die Leiterplatte zu übertragen. Dieser Prozess umfasst die Beschichtung der Leiterplatte mit einem lichtempfindlichen Fotolack, die Belichtung des Designs durch UV-Licht, die Entwicklung des Belichtungsbildes und das anschließende Ätzen, um die gewünschten Leiterbahnen zu erzeugen. Die Qualität und Präzision des Belichtungsprozesses sind entscheidend für die Funktionalität und Zuverlässigkeit der fertigen Leiterplatte.
Vgl. auch → Resist → Direktbelichter
Vorbereitung
Leiterplatte (PCB): Die Leiterplatte wird nach dem Layout- und Ätzprozess vorbereitet. Sie enthält bereits die gedruckten Leiterbahnen und Lötpads, auf denen die Bauteile befestigt werden.
Bauteile: Die zu bestückenden Bauteile werden vorbereitet und geprüft. Diese Bauteile können sowohl SMD-Bauteile (Surface-Mount Devices) als auch bedrahtete Bauteile sein.
Bestückungsmethoden
– Durchsteckmontage (Through-Hole Mounting)
- Einführung der Bauteile: Bauteile mit Drahtanschlüssen werden durch die Bohrlöcher in der Leiterplatte gesteckt.
- Verklebung: Die Bauteile werden durch Löten auf der gegenüberliegenden Seite der Leiterplatte befestigt. Dieser Schritt kann durch Handlöten, Wellenlöten oder Reflow-Löten erfolgen.
- Nachbearbeitung: Die Leiterplatte wird gereinigt, um überschüssiges Flussmittel oder Lötperlen zu entfernen.
– Oberflächenmontage (Surface-Mount Technology – SMT)
- Auftragen des Lötpaste: Eine dünne Schicht Lötpaste wird auf die Lötpads auf der Leiterplatte aufgebracht. Die Lötpaste enthält Lötmittel, das während des Lötprozesses schmilzt und die Bauteile fixiert.
- Platzierung der Bauteile: Bauteile werden durch automatisierte Maschinen (Pick-and-Place-Maschinen) auf die Lötpads positioniert. Diese Maschinen platzieren die Bauteile präzise und effizient.
- Reflow-Löten: Die Leiterplatte wird durch einen Reflow-Ofen geführt, in dem die Lötpaste schmilzt und die Bauteile fest auf den Lötpads fixiert wird.
- Nachbearbeitung: Überschüssige Lötpaste wird entfernt und die Leiterplatte wird auf Defekte geprüft.
Inspektion und Prüfung
- Optische Inspektion: Die bestückte Leiterplatte wird visuell oder mithilfe von automatisierten Inspektionssystemen (AOI – Automated Optical Inspection) überprüft, um sicherzustellen, dass alle Bauteile korrekt platziert und gelötet sind.
- Elektrische Prüfung: Tests wie In-Circuit-Tests (ICT) oder Funktionstests werden durchgeführt, um sicherzustellen, dass die Leiterplatte alle elektrischen Spezifikationen erfüllt und keine Verbindungsfehler vorliegen.
Fehlerbehebung und Nachbearbeitung
- Reparatur: Bei der Inspektion entdeckte Fehler werden behoben, indem Bauteile nachgelötet, ersetzt oder neu positioniert werden.
- Reinigung: Die Leiterplatte wird nach Bedarf gereinigt, um Flussmittelreste oder andere Verunreinigungen zu entfernen.
Verpackung und Versand
- Verpackung: Nach erfolgreicher Prüfung wird die Leiterplatte für den Versand verpackt. Oft werden sie in antistatischen Verpackungen untergebracht, um sie vor elektrostatischen Entladungen zu schützen.
- Dokumentation: Bei Bedarf wird die Leiterplatte mit Dokumentationen wie Testberichten und Produktionsprotokollen versehen.
Vorteile der Bestückung
- Kosteneffizienz: Automatisierte Bestückungsprozesse wie SMT reduzieren die Produktionskosten und erhöhen die Fertigungsgenauigkeit.
- Platzersparnis: SMD-Bauteile ermöglichen eine kompaktere Gestaltung der Leiterplatte, da sie auf der Oberfläche montiert werden können.
- Hohe Präzision: Durch moderne Bestückungstechniken können komplexe und präzise Leiterplatten hergestellt werden, die für den Einsatz in hochentwickelten elektronischen Geräten geeignet sind.
Fazit
Die Bestückung einer Leiterplatte ist ein kritischer Schritt in der Herstellung von Elektronikprodukten, der sicherstellt, dass alle Bauteile korrekt auf der Leiterplatte montiert und elektrisch verbunden sind. Der Prozess umfasst die Vorbereitung, Montage, Inspektion, Prüfung und Nachbearbeitung der Leiterplatte, um sicherzustellen, dass das Endprodukt den erforderlichen Spezifikationen und Qualitätsstandards entspricht. Moderne Bestückungsmethoden, einschließlich automatisierter SMT-Prozesse, tragen zur Effizienz und Präzision der Leiterplattenfertigung bei.
Der Bestückungsdruck ist ein wichtiger Bestandteil des Fertigungsprozesses bei der Leiterplattenproduktion, insbesondere bei der Oberflächenmontage (Surface Mount Technology, SMT). Er bezeichnet den Druck, der auf die Leiterplatte aufgebracht wird, um die genaue Position und Ausrichtung der Bauteile während der Bestückung zu gewährleisten. Der Bestückungsdruck dient mehreren Zwecken und wird in verschiedenen Phasen des Herstellungsprozesses verwendet:
Definition und Zweck
- Bestückungsdruck: Auch als Positionierdruck oder Druckmarken bezeichnet, bezieht sich der Bestückungsdruck auf Markierungen oder Drucke auf der Leiterplatte, die während des Bestückungsprozesses helfen, die Bauteile korrekt zu platzieren.
Arten von Bestückungsdruck
- Druckmarken: Dies sind spezifische Markierungen auf der Leiterplatte, die den Bestückungsautomaten anzeigen, wo Bauteile positioniert werden sollen. Sie dienen als visuelle Referenz für die automatische Platzierung der Bauteile.
- Silkscreen-Druck: Diese Schicht auf der Leiterplatte enthält Text und Symbole, die die Position und Identität der Bauteile angeben. Der Silkscreen-Druck ist eine Art von Bestückungsdruck, der den Designern hilft, die Bestückung zu überprüfen und zu verifizieren.
Prozess und Anwendung
- Druckvorbereitung: Vor der Bestückung wird die Leiterplatte mit einem Bestückungsdruck versehen, der oft auf den Lötpads und um die Position der Bauteile herum aufgebracht wird. Dieser Druck kann durch verschiedene Verfahren wie Siebdruck oder Tampondruck erfolgen.
- Automatische Bestückung: Bei der automatisierten Bestückung mit Pick-and-Place-Maschinen werden die Druckmarken genutzt, um die genaue Position und Ausrichtung der Bauteile auf der Leiterplatte zu gewährleisten. Die Maschinen erkennen die Druckmarken und justieren die Bauteile entsprechend.
Vorteile des Bestückungsdrucks
- Erhöhte Genauigkeit: Der Bestückungsdruck hilft dabei, die Bauteile präzise zu positionieren und auszurichten, was die Fertigungsqualität verbessert und Fehlplatzierungen minimiert.
- Vermeidung von Fehlern: Durch klare Markierungen und Referenzen können Fehler bei der Bauteilplatzierung reduziert werden, was die Zuverlässigkeit des Endprodukts erhöht.
- Effizienz: Der Bestückungsdruck ermöglicht eine schnelle und effiziente automatisierte Bestückung, indem er den Maschinen hilft, sich auf die richtige Position zu kalibrieren.
Nach der Bestückung
- Inspektion: Nach der Bestückung wird die Leiterplatte auf den Bestückungsdruck überprüft, um sicherzustellen, dass alle Bauteile korrekt platziert sind. Fehlerhafte Bestückungen können durch die Bestückungsmarken identifiziert und korrigiert werden.
- Reinigung: Der Bestückungsdruck kann nach der Bestückung manchmal gereinigt oder entfernt werden, insbesondere wenn er aus Materialien besteht, die sich mit der Zeit abnutzen könnten.
Fazit
Der Bestückungsdruck ist ein wesentlicher Bestandteil der Leiterplattenproduktion, der sicherstellt, dass Bauteile korrekt und präzise auf der Leiterplatte platziert werden. Durch die Bereitstellung von klaren Referenzen für die automatische Bestückung hilft der Bestückungsdruck, die Genauigkeit und Effizienz des Fertigungsprozesses zu verbessern. Er trägt zur Qualitätssicherung bei, indem er Fehler bei der Bauteilplatzierung minimiert und eine korrekte Ausrichtung gewährleistet.
Definition und Zweck
- Bestückungsplan: Ein Bestückungsplan, auch Bestückungsdruck, Bestückungslayout oder Pick-and-Place-Plan genannt, ist ein Diagramm oder Dokument, das die Positionen, Orientierungen und Typen der Bauteile auf der Leiterplatte angibt. Er dient als Anleitung für die Bestückungsmaschinen und den Bestückungsprozess.
Inhalte eines Bestückungsplans
- Bauteilpositionen: Der Plan zeigt die exakten Positionen der Bauteile auf der Leiterplatte, einschließlich der Koordinaten der Lötpads oder Mounting-Pads.
- Bauteilbezeichnungen: Jeder Bauteilplatz wird in der Regel mit einem eindeutigen Bauteilcode oder einer Bezeichnung versehen, die mit der Stückliste (BOM – Bill of Materials) übereinstimmt.
- Orientierung: Der Bestückungsplan zeigt oft auch die richtige Orientierung der Bauteile, insbesondere bei Polungselementen wie Dioden oder Kondensatoren, bei denen die Ausrichtung wichtig ist.
- Spezifikationen: Neben den Positionsdaten können zusätzliche Informationen wie Bauteilgrößen, Typen und Werte angegeben werden, um sicherzustellen, dass die richtigen Bauteile verwendet werden.
Erstellung eines Bestückungsplans
- CAD-Software: Bestückungspläne werden normalerweise mit Hilfe von CAD-Software (Computer-Aided Design) erstellt. Die Software verwendet die Layout-Daten und die Stückliste, um den Bestückungsplan zu generieren.
- Integration: Der Bestückungsplan wird oft in das gesamte Leiterplatten-Design integriert und kann in verschiedenen Formaten exportiert werden, wie z.B. Gerber-Dateien oder spezielle Bestückungsdateiformate (z.B. Centroid-Dateien).
Verwendung
- Automatische Bestückung: Bei der automatisierten Bestückung, etwa mit Pick-and-Place-Maschinen, dient der Bestückungsplan als Steuerdatei, die den Maschinen mitteilt, wo und wie die Bauteile platziert werden sollen.
- Manuelle Bestückung: In Fällen, in denen die Bestückung manuell erfolgt, verwenden Techniker den Bestückungsplan, um sicherzustellen, dass jedes Bauteil korrekt positioniert und eingelötet wird.
- Qualitätssicherung: Der Bestückungsplan wird auch bei der visuellen Inspektion und der Endprüfung verwendet, um sicherzustellen, dass alle Bauteile korrekt angebracht sind und keine Fehler vorliegen.
Vorteile
- Klarheit und Präzision: Der Bestückungsplan sorgt für eine präzise Platzierung der Bauteile, minimiert Fehler und verbessert die Qualität der Leiterplatte.
- Effizienz: Durch die Bereitstellung einer klaren Anleitung für Bestückungsmaschinen und Techniker wird der Bestückungsprozess effizienter und schneller.
- Fehlervermeidung: Ein gut ausgearbeiteter Bestückungsplan hilft dabei, Fehler bei der Bauteilplatzierung zu vermeiden und stellt sicher, dass alle Bauteile den Design-Spezifikationen entsprechen.
Nachbearbeitung
- Überprüfung: Nach der Bestückung wird überprüft, ob alle Bauteile gemäß dem Bestückungsplan positioniert wurden. Dies kann durch visuelle Inspektion, automatisierte Tests oder andere Qualitätssicherungsmaßnahmen erfolgen.
- Dokumentation: Der Bestückungsplan wird zusammen mit anderen Produktionsdokumenten archiviert und kann bei späteren Wartungsarbeiten oder Überholungen verwendet werden.
Fazit
Der Bestückungsplan ist ein unverzichtbares Dokument in der Leiterplattenfertigung, das die genaue Position und Orientierung der Bauteile festlegt. Er gewährleistet, dass der Bestückungsprozess präzise und effizient abläuft, was zu einer hohen Qualität und Zuverlässigkeit der fertigen Leiterplatten führt. Durch die Integration des Bestückungsplans in den gesamten Fertigungsprozess können Fehler minimiert und die Produktionsgeschwindigkeit erhöht werden.
Vgl. auch → Bauteilseite
- BEVELING
- BGA
- BIEGEFESTIGKEIT
- BILL OF MATERIALS
- BLACK PAD
Definition und Zweck
- Beveling: Beveling bezeichnet das Abschrägen der Kanten einer Leiterplatte, um eine geneigte Fläche zu schaffen. Dies wird erreicht, indem man die Kanten der Leiterplatte so bearbeitet, dass sie nicht mehr senkrecht, sondern schräg zur Oberfläche der Platine verlaufen.
Gründe für Beveling
- Sicherheit: Abgeschrägte Kanten verringern die Gefahr von scharfen Kanten, die Verletzungen verursachen können, insbesondere bei der Handhabung und Installation von Leiterplatten in Gehäusen oder Geräten.
- Verbesserte Passgenauigkeit: Beveling kann helfen, die Leiterplatte leichter in Gehäuse oder Steckplätze einzuführen, da die abgeschrägten Kanten die Montage erleichtern und das Risiko von mechanischen Beschädigungen reduzieren.
- Ästhetik: Abgeschrägte Kanten können das Aussehen der Leiterplatte verbessern, indem sie eine sauberere und professionellere Erscheinung verleihen.
- Reduzierung von Stress: Bei Leiterplatten, die in Gehäusen montiert werden, kann das Abfasen der Kanten dazu beitragen, mechanischen Stress und Spannungen, die durch unregelmäßige Kanten entstehen könnten, zu reduzieren.
Beveling-Verfahren
- Mechanisches Abfasen: Hierbei werden spezielle Fräsmaschinen oder Schleifgeräte verwendet, um die Kanten der Leiterplatte in einem bestimmten Winkel abzufasen. Dies erfolgt oft als letzter Schritt im Fertigungsprozess.
- Laser-Abfasen: In einigen modernen Produktionsanlagen wird Laserbeveling verwendet, bei dem ein Laserstrahl zur Bearbeitung der Kanten eingesetzt wird. Dies ermöglicht eine präzisere Steuerung und kann feineres Abfasen ermöglichen.
- Handabfasen: In weniger automatisierten oder kleineren Produktionsumgebungen kann das Abfasen auch manuell durch Schleifen oder Feilen erfolgen.
Ausführung
- Winkel: Die Kanten können in verschiedenen Winkeln abgeschrägt werden, je nach den spezifischen Anforderungen des Designs oder der Anwendung. Übliche Winkel für Beveling liegen oft zwischen 30° und 45°.
- Kantenbearbeitung: Das Beveling sollte gleichmäßig und sauber ausgeführt werden, um sicherzustellen, dass keine scharfen Stellen oder Unregelmäßigkeiten an den Kanten verbleiben.
Vorteile des Beveling
- Sicherheitsverbesserung: Reduziert das Risiko von Verletzungen durch scharfe Kanten und macht den Umgang mit Leiterplatten sicherer.
- Erleichterte Montage: Verbessert die Passgenauigkeit beim Einbau der Leiterplatte in Gehäuse oder Steckplätze, indem es das Einführen erleichtert.
- Ästhetik: Verleiht der Leiterplatte ein saubereres und professionelleres Aussehen.
Nachbearbeitung
- Reinigung: Nach dem Beveling kann es notwendig sein, die Leiterplatte zu reinigen, um Rückstände von Schleif- oder Fräsprozessen zu entfernen.
- Überprüfung: Die bearbeiteten Kanten werden überprüft, um sicherzustellen, dass das Abfasen gleichmäßig und gemäß den Spezifikationen durchgeführt wurde.
Fazit
Beveling ist ein Verfahren zur Bearbeitung der Kanten von Leiterplatten, das sowohl funktionale als auch ästhetische Vorteile bietet. Durch das Abrunden oder Abschrägen der Kanten wird die Sicherheit erhöht, die Montage erleichtert und das Aussehen der Leiterplatte verbessert. Verschiedene Methoden wie mechanisches Fräsen, Laserabfasen und manuelles Schleifen können verwendet werden, um die Kanten entsprechend den Anforderungen des Designs und der Anwendung zu bearbeiten.
Vgl. auch → Abfasen → Anfasen
Definition und Aufbau
BGA-Gehäuse: Das BGA-Gehäuse besteht aus einem Kunststoff- oder Keramikblock, in dem die Halbleiterchips eingebettet sind. Die Anschlussdrähte sind als kleine Lötbälle auf der Unterseite des Gehäuses angeordnet. Diese Lötbälle sind in einem Rastermuster angeordnet, daher der Name „Ball Grid Array“.
Lötbälle: Die Lötbälle sind die elektrischen Verbindungen zwischen dem BGA-Gehäuse und der Leiterplatte. Sie sind auf der Unterseite des Bauteils angebracht und werden während des Lötprozesses auf die Leiterplatte befestigt.
Vorteile des BGA
Hohe Packungsdichte: BGA-Gehäuse ermöglichen eine höhere Anzahl von Pins auf einer gegebenen Fläche im Vergleich zu traditionellen Gehäusen wie dem Dual In-line Package (DIP) oder dem Surface Mount Package (SMD). Dies ermöglicht die Platzierung von mehr Funktionen auf einer kleineren Fläche.
Geringerer Widerstand: Die Lötbälle bieten einen geringeren Widerstand und eine bessere elektrische Verbindung im Vergleich zu herkömmlichen Pins, was zu einer verbesserten Leistung führt.
Bessere Wärmeabfuhr: BGA-Gehäuse bieten oft eine bessere Wärmeableitung, da die Lötbälle direkt mit der Leiterplatte verbunden sind, was hilft, die Wärme des Chips effizient abzuleiten.
Verbesserte Zuverlässigkeit: Die gleichmäßige Verteilung der Lötbälle reduziert mechanische Belastungen auf die Verbindungen und verringert das Risiko von Rissen oder Bruch, die bei anderen Gehäusetypen auftreten können.
Anwendung
Leiterplatten-Design: Bei der Gestaltung von Leiterplatten, die BGA-Bauteile verwenden, müssen spezielle Designregeln beachtet werden. Dazu gehören die richtige Platzierung der Lötpads, die Sicherstellung der richtigen Lötbälle und die Berücksichtigung der Wärmeableitung.
Bestückung: Die Bestückung von BGA-Bauteilen erfolgt in der Regel mit automatisierten Pick-and-Place-Maschinen, die die Bauteile präzise auf den Lötpads platzieren. Danach werden die Leiterplatten durch einen Reflow-Ofen geführt, um die Lötbälle zu schmelzen und die Bauteile zu befestigen.
Herausforderungen
Fehlererkennung: Fehlerhafte Lötverbindungen bei BGA-Bauteilen sind schwieriger zu erkennen als bei Bauteilen mit sichtbaren Pins. Daher sind spezielle Prüfmethoden wie Röntgeninspektion erforderlich, um sicherzustellen, dass alle Lötbälle korrekt verlötet sind.
Wärmeverteilung: Während BGA-Gehäuse eine gute Wärmeableitung bieten, kann es in hochleistungsfähigen Anwendungen dennoch erforderlich sein, zusätzliche Kühlmaßnahmen zu integrieren, um die Temperatur des Bauteils zu kontrollieren.
Tests und Inspektion
Automatisierte Tests: Um die Qualität der BGA-Verbindungen zu überprüfen, werden oft automatisierte Testmethoden verwendet, einschließlich elektrischer Tests und der Röntgeninspektion, um versteckte Lötverbindungen zu überprüfen.
Reparatur: Falls notwendig, kann die Reparatur von BGA-Bauteilen komplex sein, da das Entfernen und Ersetzen von BGA-Bauteilen spezielle Ausrüstung und Fachwissen erfordert.
Fazit
BGA (Ball Grid Array) ist ein fortschrittliches Gehäusedesign für elektronische Bauteile, das hohe Packungsdichte, verbesserte elektrische Leistung und Zuverlässigkeit bietet. Aufgrund seiner Vorteile wird es häufig in modernen Elektronikgeräten verwendet, insbesondere in Anwendungen, bei denen Platzersparnis und hohe Leistung erforderlich sind. Die korrekte Gestaltung, Bestückung und Inspektion von BGA-Bauteilen sind entscheidend für die Herstellung hochwertiger und funktionaler Leiterplatten.
Die Biegefestigkeit und Querdurchbruchsfestigkeit sind wichtige Materialeigenschaften, die bei der Herstellung und Nutzung von Leiterplatten berücksichtigt werden müssen. Hier eine Übersicht über beide Begriffe:
Biegefestigkeit
Definition:
- Biegefestigkeit ist die Fähigkeit eines Materials, der Belastung durch Biegen zu widerstehen, ohne zu brechen oder dauerhaft verformt zu werden. Sie beschreibt die maximale Belastung, die ein Material bei einer Biegebeanspruchung aushalten kann, bevor es versagt.
Relevanz für Leiterplatten:
- Mechanische Stabilität: Bei Leiterplatten ist die Biegefestigkeit wichtig, um sicherzustellen, dass die Platine mechanischen Belastungen, die während der Handhabung, Montage oder Nutzung auftreten können, standhält. Eine hohe Biegefestigkeit verhindert das Riss- oder Bruchrisiko der Leiterplatte.
- Verarbeitung: Während des Herstellungsprozesses können Leiterplatten gebogen werden, um sie in bestimmte Gehäuse oder Module einzubauen. Eine ausreichende Biegefestigkeit ist erforderlich, um Schäden an der Platine oder den darauf befindlichen Bauteilen zu vermeiden.
Messung:
- Die Biegefestigkeit wird häufig durch spezielle Tests gemessen, bei denen ein Materialstück einer kontrollierten Biegebelastung ausgesetzt wird, bis es bricht oder versagt. Die Ergebnisse werden in der Regel in Megapascal (MPa) angegeben.
Querdurchbruchsfestigkeit
Definition:
- Querdurchbruchsfestigkeit beschreibt die Fähigkeit eines Materials, einem elektrischen Durchbruch oder einer elektrischen Entladung entlang seiner Oberfläche zu widerstehen. Dies ist besonders wichtig für die elektrische Isolation von Leiterplatten und den Schutz vor Kurzschlüssen oder anderen elektrischen Fehlfunktionen.
Relevanz für Leiterplatten:
- Elektrische Isolation: Die Querdurchbruchsfestigkeit ist entscheidend, um sicherzustellen, dass die Leiterplatte eine angemessene elektrische Isolation zwischen verschiedenen Leiterbahnen oder zwischen den Leiterbahnen und der Umgebung aufrechterhält. Eine hohe Querdurchbruchsfestigkeit verhindert, dass elektrische Impulse durch die Leiterplatte dringen und Kurzschlüsse oder andere Störungen verursachen.
- Materialauswahl: Die Auswahl der richtigen Materialien für die Leiterplatte, wie die Isolationsschicht und das Laminat, beeinflusst die Querdurchbruchsfestigkeit. Materialien mit höherer Querdurchbruchsfestigkeit bieten besseren Schutz gegen elektrische Entladungen.
Messung:
- Die Querdurchbruchsfestigkeit wird in der Regel durch Tests durchgeführt, bei denen eine Spannung auf das Material angelegt wird, bis es einen elektrischen Durchbruch erleidet. Die Querdurchbruchsfestigkeit wird üblicherweise in Volt pro Millimeter (V/mm) angegeben.
Zusammenfassung
Biegefestigkeit: Bezieht sich auf die Fähigkeit eines Materials, der Belastung durch Biegen zu widerstehen, ohne zu brechen oder sich zu verformen. Für Leiterplatten ist dies wichtig, um mechanische Schäden während der Handhabung und Nutzung zu vermeiden.
Querdurchbruchsfestigkeit: Beschreibt die Fähigkeit eines Materials, elektrischen Durchbrüchen oder Entladungen entlang seiner Oberfläche zu widerstehen. Sie ist entscheidend für die elektrische Isolation und den Schutz gegen Kurzschlüsse auf Leiterplatten.
Beide Eigenschaften sind entscheidend für die Leistung und Zuverlässigkeit von Leiterplatten und müssen bei der Auswahl der Materialien und dem Design berücksichtigt werden.
Bill of Materials (BOM), oder Stückliste, ist ein umfassendes Dokument, das eine detaillierte Aufstellung aller Materialien, Bauteile und Komponenten enthält, die für die Herstellung eines Produkts erforderlich sind. In der Leiterplattenfertigung spielt die BOM eine zentrale Rolle, da sie als Grundlage für die Beschaffung, Montage und Qualitätskontrolle dient. Hier sind die wesentlichen Aspekte einer BOM im Kontext der Leiterplattenfertigung:
Definition und Zweck
- Bill of Materials (BOM): Eine Stückliste ist eine detaillierte Aufstellung, die alle benötigten Materialien und Komponenten für die Fertigung eines Produkts auflistet. Sie beschreibt die genaue Menge, Typ, Spezifikationen und andere relevante Informationen zu jedem Bauteil.
Inhalte einer BOM
- Bauteilbezeichnungen: Jede Komponente wird mit einer eindeutigen Bezeichnung oder Teilenummer versehen, die es ermöglicht, das Bauteil in der Fertigung und beim Einkauf eindeutig zu identifizieren.
- Mengen: Die Stückliste gibt an, wie viele Einheiten jedes Bauteils benötigt werden.
- Spezifikationen: Technische Details wie Größe, Form, Materialtyp und andere Eigenschaften jedes Bauteils werden aufgeführt.
- Lieferanten: Informationen zu den Lieferanten oder Herstellern der Bauteile, einschließlich Kontaktinformationen und eventuell Bestellnummern.
- Kostenschätzungen: Einige BOMs enthalten Schätzungen der Kosten für jedes Bauteil, um die Gesamtproduktionskosten zu berechnen.
Arten von BOM
- Einfache BOM: Listet nur die grundlegenden Informationen zu den Bauteilen auf, wie Bezeichnung, Menge und allgemeine Spezifikationen.
- Vollständige BOM: Enthält detaillierte Informationen zu jedem Bauteil, einschließlich spezifischer Lieferantendaten, Kosten und eventuell spezifischer Herstellungsanforderungen.
- Strukturierte BOM: Zeigt die hierarchische Beziehung zwischen verschiedenen Baugruppen und Komponenten eines Produkts auf, was besonders bei komplexen Produkten nützlich ist.
- Varianten BOM: Wird verwendet, wenn ein Produkt in mehreren Varianten oder Konfigurationen hergestellt wird, und listet die Unterschiede zwischen den Varianten auf.
Verwendung der BOM
- Beschaffung: Die BOM dient als Grundlage für die Beschaffung der benötigten Bauteile und Materialien. Sie hilft den Einkäufern, die richtigen Komponenten in der erforderlichen Menge zu bestellen.
- Fertigung: In der Fertigung wird die BOM verwendet, um sicherzustellen, dass alle benötigten Bauteile vorhanden sind und korrekt in die Leiterplatte integriert werden.
- Montage: Die BOM hilft bei der Planung und Durchführung der Montage, indem sie die genauen Bauteile und deren Platzierung auf der Leiterplatte angibt.
- Qualitätskontrolle: Die Stückliste wird verwendet, um die Qualität der fertigen Leiterplatte zu überprüfen, indem sichergestellt wird, dass alle Bauteile korrekt eingebaut sind und den Spezifikationen entsprechen.
- Dokumentation: Sie dient als wichtige Dokumentation für die Nachverfolgung von Änderungen, Wartung und zukünftige Reparaturen oder Upgrades.
Erstellung und Pflege der BOM
- CAD-Integration: In modernen Produktionsumgebungen wird die BOM oft direkt aus der CAD-Software (Computer-Aided Design) generiert, die die Leiterplatte entwirft. Die CAD-Software kann automatisch eine Stückliste erstellen, die dann für die Fertigung verwendet wird.
- Aktualisierungen: Die BOM sollte regelmäßig aktualisiert werden, um Änderungen in den Bauteilen, Spezifikationen oder Lieferanteninformationen widerzuspiegeln. Dies ist wichtig, um sicherzustellen, dass alle Komponenten korrekt und aktuell sind.
Vorteile der BOM
- Effizienz: Eine präzise Stückliste erhöht die Effizienz bei der Beschaffung und Fertigung, da alle benötigten Bauteile und Materialien klar spezifiziert sind.
- Fehlervermeidung: Sie hilft, Fehler zu vermeiden, indem sie sicherstellt, dass die richtigen Bauteile in der richtigen Menge verwendet werden.
- Kostenkontrolle: Durch die Angabe von Kosten und Lieferanteninformationen hilft die BOM, die Produktionskosten zu kontrollieren und zu optimieren.
Fazit
Die Bill of Materials (BOM) ist ein unerlässliches Dokument in der Leiterplattenfertigung und im gesamten Produktionsprozess. Sie bietet eine detaillierte Übersicht aller benötigten Bauteile und Materialien, was eine effiziente Beschaffung, Fertigung und Qualitätskontrolle ermöglicht. Eine präzise und gut gepflegte BOM trägt erheblich zur erfolgreichen Produktion und Qualität eines Produkts bei.
Vgl. auch → BOM
Definition und Erscheinungsbild
- Black Pad: Black Pad ist ein Defekt, bei dem die Oberfläche der Leiterplatte, die normalerweise eine glänzende goldene Schicht durch den chemischen Vergoldungsprozess haben sollte, stattdessen eine matte, schwarze oder dunkelbraune Farbe annimmt. Diese Verfärbung ist oft ein Zeichen für eine chemische Reaktion, die das Kupfer unterhalb der Goldschicht beeinträchtigt hat.
Ursachen
- Chemische Reaktionen: Der Black Pad-Defekt tritt typischerweise auf, wenn es zu einer unvollständigen oder unsachgemäßen Beschichtung des Kupfers mit dem chemischen Nickel oder Gold kommt. Dies kann durch eine unzureichende Kontrolle der Prozessbedingungen wie Temperatur, pH-Wert oder Konzentration der Chemikalien verursacht werden.
- Nickel-Oxidation: Ein häufiger Grund ist die Bildung von Nickel-Oxid oder -Hydroxid an der Kupferoberfläche. Dies kann durch eine unsachgemäße Lagerung oder Behandlung des Kupfers vor der Vergoldung oder durch einen fehlerhaften chemischen Prozess während der Nickelablagerung entstehen.
- Kontaminierte Chemikalien: Verunreinigungen in den Chemikalien, die für die Vergoldung verwendet werden, können ebenfalls zur Bildung von Black Pad führen.
Auswirkungen auf die Leiterplatte
- Schlechte Lötbarkeit: Black Pad kann zu erheblichen Problemen bei der Lötbarkeit führen, da die schwarze oder matte Oberfläche oft nicht gut mit Lötzinn haftet. Dies kann zu unzuverlässigen Verbindungen oder sogar zu Lötfehlern führen.
- Schwache Verbindungen: Die schwache Haftung zwischen der Goldschicht und dem Kupfer darunter kann zu mechanischen oder elektrischen Verbindungsproblemen führen, die die Leistung und Zuverlässigkeit der Leiterplatte beeinträchtigen können.
- Korrosion: In einigen Fällen kann die Black Pad-Beschichtung auch zu einer erhöhten Anfälligkeit für Korrosion führen, was langfristige Probleme verursachen kann.
Vorbeugung und Behebung
- Prozesskontrolle: Um Black Pad zu vermeiden, ist es wichtig, die chemischen Prozesse für Nickel- und Goldbeschichtungen sorgfältig zu überwachen. Dazu gehört die regelmäßige Überprüfung und Kalibrierung der Chemikalien, die Kontrolle der Temperatur und der pH-Werte sowie die Einhaltung der empfohlenen Verfahrensparameter.
- Chemikalienqualität: Verwendung von hochwertigen und gut überwachten Chemikalien kann helfen, die Bildung von Black Pad zu vermeiden. Es ist wichtig, dass alle verwendeten Chemikalien den Spezifikationen entsprechen und keine Verunreinigungen enthalten.
- Materialprüfung: Vor der Verwendung sollten Kupferoberflächen auf ihre Qualität und Reinheit überprüft werden. Beschädigte oder verunreinigte Kupferflächen sollten vor der Vergoldung behandelt oder ersetzt werden.
Reparatur
- Reinigung: Bei der Entdeckung von Black Pad können die betroffenen Leiterplatten manchmal durch spezielle Reinigungsverfahren behandelt werden, um die Oberfläche vorzubereiten und die Lötbarkeit zu verbessern.
- Erneute Beschichtung: In einigen Fällen kann es erforderlich sein, den Vergoldungsprozess zu wiederholen oder alternative Beschichtungsmethoden zu verwenden, um die Probleme zu beheben.
Fazit
Der Black Pad-Defekt ist ein ernstes Problem in der Leiterplattenfertigung, das zu Lötproblemen und schwachen elektrischen Verbindungen führen kann. Er tritt oft aufgrund von Mängeln im chemischen Vergoldungsprozess auf. Durch sorgfältige Prozesskontrolle, qualitativ hochwertige Materialien und regelmäßige Überprüfungen können die Risiken minimiert und die Qualität der Leiterplatten sichergestellt werden.
- BLASENBILDUNG
- BLEI
- BLEIFREI
- BLIND VIA
- BOHRABSTAND
Blasenbildung in der Leiterplattenfertigung ist ein Defekt, bei dem sich Blasen oder Hohlräume zwischen den verschiedenen Schichten der Leiterplatte oder auf der Oberfläche bilden. Dieser Defekt kann während des Herstellungsprozesses auftreten und die Funktionalität und Qualität der Leiterplatte beeinträchtigen. Hier sind die wesentlichen Aspekte der Blasenbildung:
Definition und Erscheinungsbild
- Blasenbildung: Blasenbildung bezeichnet das Auftreten von Luftblasen oder Hohlräumen, die sich in der Leiterplatte bilden. Diese Blasen können sich zwischen den Schichten der Leiterplatte oder auf der Oberfläche der Leiterplatte zeigen. Sie erscheinen oft als sichtbare Aufwölbungen oder Schattierungen auf der Leiterplatte.
Ursachen
- Unzureichende Vakuumierung: Während des Laminierprozesses, bei dem die Schichten der Leiterplatte zusammengefügt werden, kann unzureichende Vakuumierung dazu führen, dass Luft oder andere Gase in den Laminierprozess eingeschlossen werden, was Blasenbildung verursachen kann.
- Feuchte Material: Wenn das Basismaterial oder die Beschichtungen, wie z.B. die Epoxidharz-Schicht, Feuchtigkeit enthalten, kann diese beim Erhitzen zu Dampf werden, der Blasen bildet.
- Unzureichende Haftung: Wenn die Haftung zwischen den Schichten der Leiterplatte oder zwischen der Leiterplatte und den Beschichtungen nicht ausreichend ist, kann dies zu Blasenbildung führen. Dies kann durch unvollständige oder inkonsistente Beschichtungen verursacht werden.
- Temperatur- und Druckfehler: Fehler in den Temperatur- und Druckbedingungen während des Laminierprozesses können dazu führen, dass sich Blasen bilden. Zu hohe Temperaturen oder ungleichmäßiger Druck können die Materialschichten beeinträchtigen und Blasen verursachen.
Auswirkungen auf die Leiterplatte
- Elektrische Probleme: Blasen können die elektrische Integrität der Leiterplatte beeinträchtigen, indem sie den Kontakt zwischen den Leiterbahnen und den Schichten unterbrechen, was zu Kurzschlüssen oder Fehlfunktionen führen kann.
- Mechanische Schwächen: Die Blasen können Schwachstellen in der Leiterplatte schaffen, die die mechanische Stabilität der Platine verringern. Dies kann zu Rissen oder anderen strukturellen Problemen führen.
- Verzerrungen und Fehlstellen: Blasenbildung kann zu optischen Verzerrungen oder Fehlstellen auf der Oberfläche der Leiterplatte führen, was die Qualität und Ästhetik beeinträchtigt.
Vorbeugung und Kontrolle
- Feuchtigkeitsmanagement: Um Blasenbildung zu verhindern, sollte das Material vor der Verarbeitung ausreichend getrocknet werden. Der Feuchtigkeitsgehalt des Basismaterials sollte regelmäßig überprüft werden, um sicherzustellen, dass es trocken und für den Laminierprozess geeignet ist.
- Vakuumierung: Die Sicherstellung einer ordnungsgemäßen Vakuumierung während des Laminierprozesses ist entscheidend, um das Einschließen von Luft oder Gasen zu verhindern.
- Prozesskontrolle: Überwachung und Kontrolle der Temperatur und des Drucks während des Laminierprozesses helfen, die Bedingungen für die Blasenbildung zu vermeiden. Die Einhaltung der empfohlenen Prozessparameter ist wichtig, um eine gleichmäßige und fehlerfreie Laminierung zu gewährleisten.
- Qualitätskontrolle: Regelmäßige Inspektionen und Tests der Leiterplatten während und nach dem Herstellungsprozess helfen, Blasenbildung frühzeitig zu erkennen und zu beheben.
Behebung
- Reparatur: Bei der Entdeckung von Blasen können spezielle Reparaturverfahren angewendet werden, z.B. durch Entfernen der betroffenen Bereiche und Nachbessern der Beschichtung, um die Blasen zu beheben.
- Neuproduktion: In schweren Fällen kann es notwendig sein, die betroffenen Leiterplatten zu ersetzen oder den Herstellungsprozess zu wiederholen, um die Qualität der Endprodukte sicherzustellen.
Fazit
Blasenbildung in Leiterplatten ist ein ernstzunehmendes Problem, das durch unzureichende Vakuumierung, feuchte Materialien oder fehlerhafte Prozessbedingungen verursacht werden kann. Die richtige Kontrolle der Herstellungsbedingungen und regelmäßige Qualitätsprüfungen sind entscheidend, um Blasenbildung zu vermeiden und die Integrität und Zuverlässigkeit der Leiterplatten zu gewährleisten.
Vgl. auch → Delamination
Blei (chemisch „Pb“, Plumbum) oder „lead“ (Englisch) ist ein Metall, das häufig als Bestandteil von Lotlegierungen verwendet wird. Aufgrund der Einführung der RoHS/WEEE-Norm wurde Blei größtenteils als Legierungsbestandteil verboten, da es giftig ist. Insbesondere die Dämpfe beim Löten stellen eine erhebliche Gesundheitsgefahr dar.
Heutzutage wird verbleites Lot für Leiterplatten in der Regel nur noch auf ausdrücklichen Kundenwunsch geliefert. Seit 2015 ist der Einsatz von bleihaltigem Lot in den meisten Produkten verboten und nur noch in spezifischen Anwendungsfällen gesetzlich erlaubt. Dazu gehören bestimmte Komponenten in der Automobiltechnik, Medizintechnik und Photovoltaikanlagen sowie in der Luft- und Raumfahrt, dem militärischen Bereich sowie in Forschung und Entwicklung.
Auch Hobbyanwender dürfen bleihaltiges Lot verwenden, solange sie ihre Geräte nicht in den Handel bringen.
Vgl. auch → RoHS
Bleifreies Lot bezeichnet Lötmaterialien, die ohne Blei formuliert sind. Diese Lote sind speziell für Anwendungen entwickelt worden, bei denen der Einsatz von Blei aufgrund von Umwelt- und Gesundheitsvorschriften nicht zulässig ist. Der Einsatz von bleifreiem Lot ist besonders relevant im Kontext von RoHS (Restriction of Hazardous Substances), einer Richtlinie der Europäischen Union, die den Einsatz bestimmter gefährlicher Stoffe in elektrischen und elektronischen Geräten einschränkt.
Definition und Zusammensetzung
- Bleifreies Lot: Bleifreies Lot ist ein Lötmaterial, das kein Blei enthält. Es besteht typischerweise aus einer Kombination anderer Metalle wie Zinn, Silber und Kupfer. Die genauen Zusammensetzungen können variieren, je nach den spezifischen Anforderungen und Anwendungen.
Häufige Legierungen für bleifreies Lot sind:
- SAC305: Eine weit verbreitete bleifreie Lötlegierung, bestehend aus 96,5 % Zinn, 3 % Silber und 0,5 % Kupfer.
- SAC387: Eine weitere häufig verwendete Legierung, bestehend aus 96,5 % Zinn, 3,0 % Silber und 0,5 % Kupfer.
- SnCu: Eine einfache Legierung, die aus Zinn und Kupfer besteht, häufig verwendet in weniger anspruchsvollen Anwendungen.
Eigenschaften
- Höhere Schmelztemperatur: Bleifreie Lote haben in der Regel höhere Schmelztemperaturen als bleihaltige Lote. Dies erfordert angepasste Lötprozesse und Temperaturprofile.
- Korrosionsbeständigkeit: Bleifreie Lote bieten eine gute Korrosionsbeständigkeit und können langfristig zuverlässig sein, besonders in anspruchsvollen Umgebungen.
- Mechanische Eigenschaften: Die mechanischen Eigenschaften wie Zugfestigkeit und Scherfestigkeit können bei bleifreien Loten variieren, wobei viele Legierungen ähnliche oder verbesserte Eigenschaften im Vergleich zu bleihaltigem Lot aufweisen.
Vorteile von bleifreiem Lot
- Umweltfreundlichkeit: Der Hauptvorteil von bleifreiem Lot ist die Verringerung der Umweltbelastung und der Gesundheitsrisiken, die durch Blei entstehen. Blei ist ein toxisches Schwermetall, das beim Recycling und bei der Entsorgung von Elektronikprodukten problematisch sein kann.
- Regulatorische Anforderungen: Die Einhaltung von Vorschriften wie RoHS ist erforderlich, um Produkte in bestimmten Märkten, insbesondere in der EU, verkaufen zu können.
Herausforderungen und Anpassungen
- Verarbeitungstemperatur: Die höhere Schmelztemperatur von bleifreiem Lot kann Anpassungen in den Lötprozessen erfordern. Dies kann zusätzliche Energie- und Kostenaufwendungen bedeuten.
- Lötverbindungen: Bleifreie Lote können unterschiedliche Fließverhalten und Benetzbarkeit aufweisen, was zu Anpassungen der Lötprozesse führen kann, um eine gleichmäßige und zuverlässige Verbindung zu gewährleisten.
- Zinn-Whisker: Ein weiteres bekanntes Problem bei bleifreiem Lot ist die Bildung von Zinn-Whiskern, die feine, haarartige Wachstum von Zinn auf der Oberfläche der Lötstellen sind. Diese können zu Kurzschlüssen führen, wenn sie nicht kontrolliert werden.
Anwendung
- Elektronik: Bleifreie Lote werden weitgehend in der Elektronikindustrie verwendet, insbesondere in der Herstellung von Leiterplatten und der Baugruppenmontage.
- Automobilindustrie: Viele Automobilhersteller verwenden bleifreie Lote aufgrund der hohen Zuverlässigkeitsanforderungen und der Einhaltung von Umweltvorschriften.
Überprüfung und Qualitätskontrolle
- Testverfahren: Um sicherzustellen, dass bleifreie Lötverbindungen zuverlässig sind, werden spezifische Testverfahren wie Scherfestigkeitstests, Wärmezyklen und andere Zuverlässigkeitstests durchgeführt.
- Prozessoptimierung: Die Optimierung der Lötprozesse, einschließlich der Auswahl geeigneter Flussmittel und Lötbedingungen, ist wichtig, um die besten Ergebnisse mit bleifreiem Lot zu erzielen.
Fazit
Bleifreies Lot bietet eine umweltfreundliche Alternative zu traditionellen bleihaltigen Loten und ist eine Voraussetzung für die Einhaltung von Vorschriften wie RoHS. Es stellt jedoch spezielle Anforderungen an die Löttechnik und erfordert sorgfältige Prozesskontrollen, um eine zuverlässige Leistung und hohe Qualität der Lötverbindungen sicherzustellen. Die Anpassung an die Eigenschaften und Herausforderungen bleifreier Lote ist entscheidend für eine erfolgreiche Implementierung in der Leiterplattenfertigung und anderen Elektronikprodukten.
Blind Vias sind spezielle Arten von Durchkontaktierungen (Vias) in Leiterplatten (PCBs), die nur eine Schicht der Leiterplatte durchdringen. Im Gegensatz zu durchgehenden Vias, die von der obersten bis zur untersten Schicht einer Leiterplatte reichen, sind Blind Vias nur in eine Richtung geöffnet, entweder von der Oberseite zur inneren Schicht oder von einer inneren Schicht zur Unterseite der Leiterplatte.
Definition und Erscheinungsbild
- Blind Vias: Diese Vias sind in einer Leiterplatte so ausgeführt, dass sie von der Oberfläche bis zu einer bestimmten inneren Schicht reichen, ohne die gesamte Leiterplatte zu durchdringen. Sie sind auf der gegenüberliegenden Seite der Leiterplatte nicht sichtbar und enden innerhalb der Leiterplatte, ohne eine Öffnung auf der gegenüberliegenden Seite zu haben.
Vorteile
- Platzersparnis: Blind Vias ermöglichen eine höhere Packungsdichte und kompaktere Leiterplattendesigns, da sie keine Öffnungen auf beiden Seiten der Leiterplatte benötigen. Dies ist besonders nützlich bei hochdichtem Design oder in Multi-Layer-Leiterplatten.
- Reduzierte Signalstörungen: Da Blind Vias nur eine begrenzte Anzahl an Schichten durchdringen, können sie helfen, Signalstörungen zu minimieren und die elektrischen Eigenschaften der Leiterplatte zu verbessern.
- Verbesserte Designflexibilität: Sie ermöglichen komplexere und platzierte Layouts auf der Oberfläche und den inneren Schichten der Leiterplatte.
Herausforderungen
- Kosten: Die Herstellung von Blind Vias kann teurer sein als die von durchgehenden Vias, da sie zusätzliche Bearbeitungsschritte und spezialisierte Fertigungsprozesse erfordert.
- Bearbeitungsaufwand: Die Herstellung und Inspektion von Blind Vias erfordern präzise Bearbeitungs- und Testmethoden, um sicherzustellen, dass die Vias korrekt eingebracht und funktional sind.
- Designkomplexität: Die Integration von Blind Vias kann das Design der Leiterplatte komplexer machen, da genaue Planung und Platzierung erforderlich sind, um sicherzustellen, dass alle elektrischen Verbindungen korrekt hergestellt werden.
Fertigungsprozess
- Bohr- und Beschichtungsprozess: Die Blind Vias werden typischerweise durch Bohren der Leiterplatte, gefolgt von der chemischen Beschichtung der Bohrlöcher, erstellt. Diese Vias werden in den Schichten eingebracht, die sie benötigen, ohne die gegenüberliegende Schicht zu durchdringen.
- Laminierung: In der Regel werden Blind Vias in den Leiterplattenprozess integriert, der mehrere Schichten umfasst. Die Leiterplatte wird in mehreren Schritten laminiert, wobei jede Schicht des Laminats die Vias abdeckt und die Verbindungen auf der Zielschicht hergestellt werden.
Anwendung
- Komplexe Elektronik: Blind Vias werden häufig in komplexen und hochdichten elektronischen Anwendungen eingesetzt, wie in mobilen Geräten, Computern, medizinischen Geräten und in der Automobilindustrie, um den verfügbaren Platz optimal zu nutzen und die Leistungsfähigkeit der Leiterplatte zu verbessern.
- Hochfrequenzanwendungen: Sie sind besonders nützlich in Hochfrequenz- und Hochgeschwindigkeitsanwendungen, da sie die Signalintegrität verbessern können.
Qualitätskontrolle
- Inspektion: Die Qualität von Blind Vias muss sorgfältig geprüft werden, um sicherzustellen, dass keine Verstopfungen oder Fehler in den Vias vorliegen. Dies kann durch optische Inspektionen, Röntgenprüfungen oder andere zerstörungsfreie Testmethoden erfolgen.
- Testmethoden: Testmethoden, die auf die spezifischen Anforderungen von Blind Vias abgestimmt sind, sind entscheidend für die Sicherstellung der Funktionalität und Zuverlässigkeit der Leiterplatte.
Fazit
Blind Vias sind eine wichtige Technologie in der Leiterplattenfertigung, die es ermöglicht, höhere Packungsdichten und komplexere Designs zu realisieren. Obwohl sie höhere Kosten und eine komplexere Fertigung mit sich bringen, bieten sie erhebliche Vorteile in Bezug auf Designflexibilität, Platzersparnis und Signalstabilität. Ihre präzise Fertigung und Inspektion sind entscheidend für die Sicherstellung einer hohen Qualität und Zuverlässigkeit in modernen elektronischen Geräten.
Vgl. auch → Aspekt-Ratio
Definition und Bedeutung
- Bohrabstand: Der Bohrabstand ist der Abstand zwischen den Mittelpunkten benachbarter Bohrlöcher oder Vias auf der Leiterplatte. Er wird in der Regel in Millimetern (mm) oder Zoll (in) angegeben.
Einfluss auf das Design
- Komponentenplatzierung: Der Bohrabstand beeinflusst, wie dicht oder weit die Bohrlöcher und damit die Komponenten auf der Leiterplatte platziert werden können. Ein kleinerer Bohrabstand ermöglicht eine höhere Dichte der Komponenten und eine kompaktere Leiterplatte.
- Leiterbahnen: Der Abstand zwischen den Bohrlöchern kann die Platzierung und Verlegung der Leiterbahnen auf der Leiterplatte beeinflussen. Ein zu kleiner Abstand kann die Verlegung der Leiterbahnen erschweren und das Risiko von Kurzschlüssen oder Signalinterferenzen erhöhen.
- Hitzestau: Zu kleine Bohrabstände können zu Problemen mit der Wärmeableitung führen, da die Leiterplatte möglicherweise nicht genügend Raum für eine effektive Kühlung bietet.
Fertigungstechnische Überlegungen
- Bohrdurchmesser: Der Bohrabstand muss im Verhältnis zum Bohrdurchmesser optimiert werden. Zu kleine Abstände können die Stabilität der Leiterplatte beeinträchtigen und die Bearbeitbarkeit erschweren.
- Toleranzen: Die Präzision der Bohrabstände ist kritisch, insbesondere bei hochdichten Leiterplatten. Die Fertigungstoleranzen müssen eingehalten werden, um sicherzustellen, dass die Bohrlöcher genau positioniert sind und die Leiterplatte ordnungsgemäß funktioniert.
- Maschinenkapazität: Die Fertigungsmethoden und -maschinen, die für die Herstellung der Leiterplatte verwendet werden, haben ebenfalls Einfluss auf den minimal möglichen Bohrabstand. Moderne Maschinen können kleinere Abstände präzise bearbeiten, während ältere Maschinen größere Abstände benötigen.
Normen und Standards
- IPC-Standards: Die IPC-Normen, wie die IPC-2221 (Norm für die Designregeln von Leiterplatten), bieten Richtlinien für den minimalen Bohrabstand, um eine zuverlässige Funktion und Herstellbarkeit sicherzustellen. Diese Standards berücksichtigen verschiedene Aspekte wie elektrische Anforderungen, mechanische Stabilität und Herstellbarkeit.
- Herstellerspezifikationen: Leiterplattenhersteller geben oft spezifische Anforderungen und Empfehlungen für Bohrabstände in ihren Designrichtlinien an. Diese sollten beim Design der Leiterplatte berücksichtigt werden.
Anwendungen
- Hochdichte Leiterplatten: In Anwendungen, bei denen Platzmangel herrscht und eine hohe Dichte von Komponenten erforderlich ist, werden häufig kleine Bohrabstände verwendet. Beispiele hierfür sind Mobilgeräte, Computer und medizinische Geräte.
- Multilayer-PCBs: Bei Mehrlagigen Leiterplatten kann der Bohrabstand auch Einfluss auf die Anzahl der Schichten und die Art der Verbindungen zwischen den Schichten haben.
Qualitätskontrolle
- Inspektion und Test: Der Bohrabstand muss regelmäßig überprüft werden, um sicherzustellen, dass die Leiterplatte den Spezifikationen entspricht. Dies kann durch optische Inspektion, Röntgenprüfungen oder andere Messmethoden erfolgen.
- Prozesskontrolle: Während der Herstellung ist es wichtig, die Maschinen und Prozesse regelmäßig zu kalibrieren und zu überprüfen, um die Einhaltung der erforderlichen Bohrabstände zu gewährleisten.
Fazit
Der Bohrabstand ist ein wesentlicher Faktor im Leiterplattendesign und -herstellungsprozess. Er beeinflusst die Platzierung von Komponenten, die Verlegung der Leiterbahnen und die Fertigungsanforderungen der Leiterplatte. Eine sorgfältige Planung und Kontrolle des Bohrabstands sind entscheidend, um die Leistung, Zuverlässigkeit und Herstellbarkeit der Leiterplatte sicherzustellen.
- BOHREN
- BOHRPROGRAMM
- BOHRUNG
- BOM
- BOTTOM
Das Bohren ist erforderlich für die Herstellung von Fanglöchern, Durchkontaktierungen und Bauteilbohrungen auf Leiterplatten. Es ermöglicht die Verbindung der Schichten (Lagen) und das Einsetzen von Bauteilen zu einem späteren Zeitpunkt.
Bei ein- und doppelseitigen Leiterplatten erfolgt dieser Prozess unmittelbar nach dem Zuschnitt. Bei mehrschichtigen Leiterplatten hingegen erfolgt das Bohren erst nach der Laminierung. Zunächst müssen die Innenlagen strukturiert und verpresst werden, bevor sie gebohrt werden können.
Vgl. auch → Fanglöcher → Durchkontaktierung → Innenlage
Bohrprogramm bezieht sich auf die spezifischen Anweisungen und Daten, die zur Steuerung des Bohrvorgangs auf einer Leiterplatte verwendet werden. Es enthält alle notwendigen Informationen, um die Bohrlöcher an den vorgesehenen Positionen auf der Leiterplatte präzise zu erstellen. Dieses Programm ist ein wesentlicher Bestandteil des Fertigungsprozesses und stellt sicher, dass die Leiterplatte gemäß den Designvorgaben hergestellt wird.
Definition und Inhalt
Bohrprogramm: Ein Bohrprogramm ist eine Datei oder eine Sammlung von Anweisungen, die Details über die Positionen, Durchmesser und Tiefe der Bohrlöcher auf einer Leiterplatte enthalten. Diese Daten werden von Fertigungsmaschinen genutzt, um die Bohrlöcher exakt gemäß den Designanforderungen zu erstellen.
Inhalt des Bohrprogramms:
- Positionen der Bohrlöcher: Koordinaten der Mitte jedes Bohrlochs auf der Leiterplatte.
- Durchmesser der Bohrlöcher: Der Durchmesser der Bohrlöcher, der in der Regel abhängig von den Anforderungen der elektronischen Komponenten und Verbindungen gewählt wird.
- Tiefe der Bohrlöcher: Die Tiefe, bis zu der die Bohrlöcher in die Leiterplatte gebohrt werden, einschließlich der Berücksichtigung von Schichtdicken und spezifischen Anforderungen.
- Bohrreihenfolge: Die Reihenfolge, in der die Bohrlöcher gebohrt werden sollen, um die Effizienz zu maximieren und mögliche Fehler zu minimieren.
- Spezielle Bohranforderungen: Besondere Anweisungen für spezielle Bohrungen wie Blind Vias oder Durchgangsbohrungen.
Erzeugung des Bohrprogramms
Design-Software: Das Bohrprogramm wird typischerweise von Design-Software generiert, die auf dem Leiterplattendesign basiert. EDA (Electronic Design Automation)-Tools wie Altium Designer, KiCad oder Autodesk EAGLE können Bohrprogramme erstellen, die dann an die Fertigungsmaschinen weitergegeben werden.
Dateiformate: Bohrprogramme werden in speziellen Dateiformaten gespeichert, die von Fertigungsmaschinen gelesen werden können. Zu den gängigen Formaten gehören:
- Excellon-Format: Ein weit verbreitetes Format für Bohrprogramme, das von vielen Leiterplattenherstellern und -maschinen unterstützt wird.
- Gerber-Dateien: Diese enthalten oft auch Bohrinformationen, die in Kombination mit anderen Daten für die Fertigung verwendet werden.
Fertigungsprozess
Bohrmaschine: Das Bohrprogramm wird an eine CNC-Bohrmaschine oder ein anderes automatisiertes Bohrwerkzeug übermittelt. Die Maschine verwendet die Anweisungen aus dem Programm, um die Bohrlöcher präzise in die Leiterplatte zu bohren.
Verarbeitung: Während der Bearbeitung wird die Leiterplatte möglicherweise in mehreren Schritten bearbeitet, und das Bohrprogramm sorgt dafür, dass jede Phase des Bohrvorgangs korrekt durchgeführt wird, einschließlich der Verwendung verschiedener Bohrer für unterschiedliche Durchmesser und Schichten.
Vorteile
- Präzision: Ein gut definiertes Bohrprogramm sorgt für hohe Präzision und Konsistenz bei der Herstellung von Bohrlöchern auf Leiterplatten.
- Effizienz: Durch die genaue Planung und Programmierung der Bohrvorgänge kann die Effizienz der Produktion gesteigert und die Bearbeitungszeit minimiert werden.
- Fehlervermeidung: Ein klar definiertes Bohrprogramm hilft, Fehler zu vermeiden, die durch manuelle Eingriffe oder ungenaue Positionierungen auftreten könnten.
Qualitätskontrolle
- Inspektion: Die Qualität der Bohrlöcher muss regelmäßig überprüft werden, um sicherzustellen, dass sie den Spezifikationen entsprechen. Dies kann durch visuelle Inspektionen, Messungen und andere Prüfmethoden erfolgen.
- Kalibrierung: Die Maschinen und Werkzeuge müssen regelmäßig kalibriert werden, um die Genauigkeit der Bohrvorgänge zu gewährleisten.
Anwendung und Beispiele
- Leiterplattenfertigung: Bohrprogramme werden in der Fertigung von Leiterplatten verwendet, um die präzise Platzierung von Bohrlöchern für die Befestigung von Bauteilen und die Herstellung von elektrischen Verbindungen sicherzustellen.
- Prototypen und Serienproduktion: Sowohl in der Prototypenfertigung als auch in der Serienproduktion sind präzise Bohrprogramme entscheidend für die Qualität und Funktionalität der Leiterplatten.
Fazit
Ein Bohrprogramm ist ein zentraler Bestandteil des Leiterplattenfertigungsprozesses, der sicherstellt, dass Bohrlöcher präzise und gemäß den Designanforderungen erstellt werden. Durch den Einsatz moderner Design-Software und präziser Fertigungsmaschinen wird ein hohes Maß an Genauigkeit und Effizienz erreicht. Eine sorgfältige Erstellung, Überprüfung und Umsetzung des Bohrprogramms ist entscheidend für die Herstellung qualitativ hochwertiger Leiterplatten.
Vgl. auch → Excellon → Sieb & Meyer
Definition und Typen
Bohrung: Eine Bohrung ist eine präzise bearbeitete Öffnung in der Leiterplatte. Sie kann verschiedene Funktionen haben, darunter das Verbinden von Schichten oder das Befestigen von Bauteilen.
Typen von Bohrungen:
- Durchgangsbohrungen (Through-Hole Vias): Diese Bohrungen erstrecken sich durch die gesamte Dicke der Leiterplatte und ermöglichen Verbindungen zwischen allen Schichten der Leiterplatte.
- Blind Vias: Diese Bohrungen beginnen an einer Leiterplattenschicht und enden in einer oder mehreren inneren Schichten, ohne die gegenüberliegende Seite der Leiterplatte zu erreichen.
- Buried Vias: Diese Bohrungen sind vollständig innerhalb der inneren Schichten der Leiterplatte und sind von außen nicht sichtbar. Sie verbinden nur die inneren Schichten.
- Geschlossene Bohrungen (Pad Vias): Diese Bohrungen enden auf der Oberfläche der Leiterplatte und sind häufig zur Befestigung von Bauteilen wie Durchführungen oder Stiften verwendet.
Design und Planung
- Designüberlegungen:
- Positionierung: Die genaue Positionierung der Bohrungen ist entscheidend für die korrekte Funktion und die Fertigung der Leiterplatte. Bohrungen müssen sorgfältig auf den Schaltplan und das Layout abgestimmt werden.
- Durchmesser: Der Durchmesser der Bohrungen hängt von den Anforderungen der Bauteile und den elektrischen Verbindungen ab. Zu große Bohrungen können die Stabilität der Leiterplatte beeinträchtigen, während zu kleine Bohrungen Probleme bei der Bestückung verursachen können.
- Abstand: Der Abstand zwischen den Bohrungen muss so gestaltet werden, dass er den Fertigungstoleranzen entspricht und gleichzeitig genügend Platz für Leiterbahnen und andere Designmerkmale bietet.
Fertigungsprozess
Bohrtechnik:
- CNC-Bohren: Moderne Leiterplatten werden in der Regel mit CNC-gesteuerten Bohrmaschinen bearbeitet, die hohe Präzision und Wiederholgenauigkeit bieten.
- Laserbohren: Für sehr feine oder kleine Bohrungen wird häufig Laserbohren eingesetzt, das extrem präzise und schnell arbeiten kann.
Prozessschritte:
- Positionierung: Die Leiterplatte wird in der Maschine positioniert, und das Bohrprogramm wird geladen.
- Bohren: Die Bohrmaschine führt die Bohrungen gemäß dem Programm aus. Je nach Bohrungstyp und -größe werden unterschiedliche Bohrer verwendet.
- Reinigung: Nach dem Bohren werden die Bohrlöcher gereinigt, um Rückstände zu entfernen, die die Qualität und Funktion der Leiterplatte beeinträchtigen könnten.
Funktionen und Vorteile
- Elektrische Verbindungen: Bohrungen ermöglichen elektrische Verbindungen zwischen verschiedenen Schichten der Leiterplatte. Durchgangsbohrungen sind dabei besonders wichtig für die Herstellung von Mehrlagigen Leiterplatten.
- Mechanische Befestigung: Bohrungen bieten auch Mechanik zur Befestigung von Bauteilen auf der Leiterplatte. Dies ist besonders wichtig für die Stabilität und Festigkeit der Bauteilbefestigung.
- Wärmeableitung: Bestimmte Bohrungen können helfen, Wärme von Bauteilen abzuleiten und die Wärmeverteilung auf der Leiterplatte zu verbessern.
Qualitätskontrolle
- Inspektion: Die Bohrungen müssen auf ihre Positionierung, Größe und Sauberkeit überprüft werden. Dies kann durch visuelle Inspektion, Röntgenprüfung oder automatisierte Testsysteme erfolgen.
- Toleranzen: Die Fertigungstoleranzen für Bohrungen müssen eingehalten werden, um sicherzustellen, dass alle Bohrungen den Spezifikationen entsprechen und korrekt funktionieren.
Anwendung
- Prototypen und Serienproduktion: In der Prototypenfertigung und in der Serienproduktion sind präzise Bohrungen unerlässlich, um die Funktionalität und Qualität der Leiterplatte sicherzustellen.
- Hochdichte Leiterplatten: Bei hochdichten Leiterplatten-Designs werden häufig kleine Bohrungen verwendet, um den Platz optimal zu nutzen und komplexe Schaltungen zu realisieren.
Fazit
Bohrungen sind ein entscheidender Aspekt des Leiterplattendesigns und der Fertigung. Sie ermöglichen elektrische Verbindungen, die Befestigung von Bauteilen und tragen zur Funktionalität und Stabilität der Leiterplatte bei. Eine präzise Planung, Fertigung und Inspektion der Bohrungen ist unerlässlich, um die Qualität und Zuverlässigkeit der Leiterplatte sicherzustellen.
Vgl. auch → DK → NDK → PTH → NPTH → Vias → Mulitlayers
BOM steht für „Bill Of Materials“ und bezieht sich auf die Bauteilliste für die Bestückung von Leiterplatten.
Die Erstellung der BOM kann oft zeitaufwändig sein, da die Bauteile gesucht und bestellt werden müssen.
Vgl. auch → Bill of Materials
Bottom bezeichnet die „Unterseite“ von Leiterplatten, die früher oft als Lötseite bezeichnet wurde. Damals wurden jedoch ausschließlich THT-Bauteile auf dieser Seite der Leiterplatte gelötet.
Mit der Einführung von SMD-Bauteilen ist der Begriff „Lötseite“ nicht mehr eindeutig, und „Bottom“ ist daher eine klarere Bezeichnung.
Vgl. auch → THT → SMD
- BREAKOUT
- BURIED VIA
Breakout in der Leiterplattenentwicklung bezieht sich auf eine Technik, die verwendet wird, um mehrere Leitungen von einem Punkt auf einer Leiterplatte zu verteilen oder zu „verzweigen“. Dies geschieht oft, wenn ein einzelner Pin eines Bauteils oder ein Verbindungs-Pad auf einer Leiterplatte auf mehrere Leiterbahnen oder Pads auf der Leiterplatte geführt werden muss.
Definition und Zweck
- Breakout: Das „Breakout“ beschreibt den Prozess des Verteilens oder Weiterleitens von Verbindungen auf einer Leiterplatte. Es wird verwendet, um eine einzige Verbindung oder einen einzelnen Pin auf eine größere Anzahl von Verbindungen oder Pads zu verteilen.
Anwendung und Beispiele
- Verkabelung eines Bauteils: Bei integrierten Schaltkreisen (ICs) mit vielen Pins oder bei Bauteilen, die hohe Anschlussdichte haben, kann ein Breakout erforderlich sein, um alle Pins korrekt auf die Leiterplatte zu führen.
- Verbindungspunkte: Ein Breakout kann helfen, Verbindungen von einem einzelnen Punkt zu verschiedenen Punkten auf der Leiterplatte zu leiten, insbesondere wenn es sich um Verbindungen zu externen Bauteilen oder Anschlüssen handelt.
Designüberlegungen
- Layout: Im Layout-Prozess werden Breakouts sorgfältig geplant, um sicherzustellen, dass alle Verbindungen korrekt und effizient geführt werden. Es ist wichtig, dass die Verzweigungen keine Signalstörungen oder -verluste verursachen.
- Größe der Pads und Leiterbahnen: Die Größe und Form der Breakout-Pads und -Leiterbahnen sollten an die Anforderungen der elektrischen Verbindungen angepasst werden. Dies hilft, eine gute Signalübertragung und mechanische Stabilität zu gewährleisten.
Fertigungstechniken
- Design: Breakout-Designs werden in der EDA-Software (Electronic Design Automation) erstellt. Die Software ermöglicht das Zeichnen der Breakout-Verbindungen und die Prüfung auf mögliche Fehler oder Verbindungsprobleme.
- Herstellung: Während der Herstellung werden die Breakouts gemäß dem Designmuster auf der Leiterplatte umgesetzt. Die Bohrlöcher, Pads und Leiterbahnen werden gemäß den Entwurfsdateien bearbeitet.
Vorteile
- Effiziente Nutzung des Platzes: Durch den Einsatz von Breakouts kann der Platz auf der Leiterplatte effizienter genutzt werden, indem mehrere Verbindungen von einem einzigen Punkt aus geführt werden.
- Flexibilität: Breakouts bieten Flexibilität bei der Verbindung von Bauteilen und ermöglichen es, eine große Anzahl von Verbindungen auf einer kompakten Leiterplatte unterzubringen.
- Einfachheit der Verbindungen: Sie erleichtern die Verbindung von Bauteilen mit vielen Pins oder Anschlüssen auf einer Leiterplatte, ohne dass jede einzelne Leitung direkt zum Bauteil geführt werden muss.
Nachteile
- Signalqualität: Wenn Breakouts nicht korrekt gestaltet sind, können sie zu Signalstörungen oder -verlusten führen, insbesondere bei hochfrequenten Signalen.
- Platzierungskonflikte: Eine unsachgemäße Planung von Breakouts kann zu Platzierungskonflikten und einer unübersichtlichen Leiterplatte führen.
Beispiele für Breakout-Designs
- Breakout-Pads: Diese sind spezielle Pads, die für die Verteilung von Verbindungen auf der Leiterplatte verwendet werden. Sie können groß genug sein, um mehrere Leitungen oder Verbindungen aufzunehmen.
- Breakout-Boards: Dies sind spezielle Platinen, die dazu dienen, Verbindungen von Bauteilen mit vielen Pins auf eine überschaubare Anzahl von Pins oder Anschlussmöglichkeiten zu führen. Sie werden häufig verwendet, um die Verwendung komplexer Bauteile zu vereinfachen.
Fazit
Breakout ist ein wichtiger Aspekt des Leiterplatten-Designs, der es ermöglicht, komplexe Verbindungen effizient zu organisieren und auf der Leiterplatte zu verteilen. Eine sorgfältige Planung und Ausführung von Breakouts sind entscheidend für die Funktionalität und Leistung der Leiterplatte, insbesondere bei Designs mit vielen Verbindungen oder komplexen Anforderungen.
Buried Vias sind spezielle Arten von Bohrungen in Leiterplatten, die ausschließlich innerhalb der Schichten einer Leiterplatte liegen und von außen nicht sichtbar sind. Diese Vias spielen eine wichtige Rolle in der Leiterplattenfertigung, insbesondere bei komplexen und mehrlagigen Designs.
Definition
- Buried Vias: Diese Vias verbinden zwei oder mehr interne Schichten einer Leiterplatte, ohne die äußeren Schichten der Leiterplatte zu durchdringen. Sie sind vollständig in der Struktur der Leiterplatte eingebettet und daher von außen nicht sichtbar.
Eigenschaften
- Verborgene Platzierung: Da sie innerhalb der Leiterplatte liegen und nicht durch die äußeren Schichten hindurchgehen, sind Buried Vias nicht sichtbar, wenn die Leiterplatte montiert oder betrachtet wird.
- Schichtverbindung: Buried Vias ermöglichen es, elektrische Verbindungen zwischen verschiedenen internen Schichten der Leiterplatte herzustellen. Dies ist besonders nützlich in mehrlagigen Leiterplatten-Designs, bei denen komplexe Verbindungen erforderlich sind.
Design und Planung
- Platzierung: Die Positionierung der Buried Vias muss im Designstadium sorgfältig geplant werden, da sie die Verbindung zwischen spezifischen Schichten herstellen. Die Platzierung erfolgt oft in Übereinstimmung mit den elektrischen Anforderungen und dem Layout der Leiterplatte.
- Designregeln: Die Designer müssen sicherstellen, dass die Buried Vias den Herstellungsanforderungen entsprechen und dass ausreichend Platz für Leiterbahnen und andere Designmerkmale vorhanden ist.
Fertigungsprozess
Herstellung: Die Herstellung von Buried Vias erfolgt in mehreren Schritten:
- Laminate: Mehrlagige Leiterplatten werden aus verschiedenen Schichten von Laminaten aufgebaut. Buried Vias werden zwischen diesen Schichten positioniert.
- Bohren und Füllen: Bohrlöcher für Buried Vias werden in den inneren Schichten gebohrt und anschließend mit Kupfer oder einem anderen leitfähigen Material gefüllt.
- Verpressen: Die Leiterplatten werden verpresst, um die Schichten zusammenzufügen und die Buried Vias zu integrieren.
Prüfung: Da Buried Vias nicht sichtbar sind, sind spezielle Prüfmethoden erforderlich, um ihre Integrität und Funktionalität sicherzustellen. Dazu gehören Röntgeninspektion und andere zerstörungsfreie Prüfmethoden.
Vorteile
- Erweiterte Designmöglichkeiten: Buried Vias ermöglichen komplexere Leiterplattendesigns, da sie Verbindungen zwischen inneren Schichten herstellen, ohne den Platz auf den äußeren Schichten zu beanspruchen.
- Reduzierte Interferenzen: Durch die Verwendung von Buried Vias können Designer Signalinterferenzen auf den äußeren Schichten reduzieren, da die Verbindungen in den inneren Schichten verborgen sind.
- Platzersparnis: Sie helfen, den Platz auf den äußeren Schichten zu maximieren und ermöglichen eine höhere Dichte und Komplexität im Leiterplattendesign.
Nachteile
- Kosten: Die Herstellung von Buried Vias kann teurer sein, da sie zusätzliche Verarbeitungsschritte und Prüfmethoden erfordert.
- Fertigungskomplexität: Die Integration von Buried Vias erhöht die Komplexität des Fertigungsprozesses und kann die Herstellung von Leiterplatten anspruchsvoller machen.
Anwendungen
- Hochdichte und komplexe Leiterplatten: Buried Vias werden häufig in Hoc leistungsanwendungen und komplexen Leiterplatten-Designs verwendet, wie z.B. in der Telekommunikation, der Computertechnik und der Medizintechnik.
- Mehrlagige Leiterplatten: Sie sind besonders nützlich in mehrlagigen Leiterplatten, wo sie zur Verbindung mehrerer Schichten beitragen, ohne die äußeren Schichten zu beeinträchtigen.
Fazit
Buried Vias sind eine wichtige Technologie in der Leiterplattenfertigung, die es ermöglicht, komplexe elektrische Verbindungen innerhalb von Leiterplatten herzustellen, ohne die äußeren Schichten zu durchdringen. Sie bieten Vorteile in Bezug auf Designflexibilität und Platzierung, stellen jedoch auch höhere Anforderungen an die Fertigung und Prüfung.
Vgl. auch → Durchkontaktierung → Multilayers
- CAD
- CAF-RESISTENZ
- CAM
- CARBON
- CASTELLATED-HOLS
CAD für Leiterplatten bezieht sich auf den Einsatz von Computer-Aided Design (CAD)-Software, um die Gestaltung, Entwicklung und Dokumentation von Leiterplatten (PCBs) zu unterstützen. Diese Software ermöglicht es Ingenieuren und Designern, präzise und effiziente Leiterplattendesigns zu erstellen, die den technischen Anforderungen und Spezifikationen entsprechen. Hier sind die wesentlichen Aspekte und Funktionen von CAD-Software für Leiterplatten:
Was ist CAD für Leiterplatten?
Definition:
- CAD-Software: Computer-Aided Design-Software für Leiterplatten ist eine spezialisierte Software, die zur Erstellung von Leiterplattendesigns verwendet wird. Sie unterstützt sowohl die Schaltplanerstellung als auch das Layout der Leiterbahnen und Bauteile auf der Leiterplatte.
Funktionalität:
- Schaltplanerstellung: Die Software ermöglicht es, elektrische Schaltpläne zu erstellen, die die logischen Verbindungen zwischen Bauteilen darstellen.
- Layout-Design: Nach der Erstellung des Schaltplans wird das Layout für die Leiterplatte entworfen, wobei die Positionierung der Bauteile und die Verlegung der Leiterbahnen berücksichtigt werden.
Hauptfunktionen der CAD-Software für Leiterplatten
Schaltplaneditor:
- Erstellung von Schaltplänen: Zeichnen und Verwalten der Schaltpläne, die die elektrischen Verbindungen zwischen den Bauteilen darstellen.
- Symbolbibliotheken: Verwendung von Bibliotheken mit Symbolen für verschiedene elektronische Bauteile.
Leiterplattenlayout:
- Bauteilplatzierung: Anordnung der Bauteile auf der Leiterplatte gemäß den Designanforderungen und dem Schaltplan.
- Leiterbahnen-Routing: Automatisches oder manuelles Verlegen der Leiterbahnen, die die elektrischen Verbindungen herstellen.
Design- und Fertigungsregeln:
- Design Rule Check (DRC): Überprüfung der Leiterplatte auf Verstöße gegen Designregeln wie Abstände, Leiterbahnbreiten und elektrische Spezifikationen.
- Electrical Rule Check (ERC): Überprüfung der elektrischen Verbindungen auf mögliche Fehler oder Inkonsistenzen.
Simulation und Analyse:
- Signal- und Stromanalyse: Simulation der elektrischen Eigenschaften der Leiterplatte, um sicherzustellen, dass sie den Leistungsanforderungen entspricht.
- Thermische Analyse: Bewertung der Wärmeverteilung auf der Leiterplatte, um Überhitzung und mögliche Fehler zu vermeiden.
Gerber-Dateien und Fertigungsdokumentation:
- Erstellung von Gerber-Dateien: Generierung der standardisierten Dateien, die für die Herstellung der Leiterplatte benötigt werden.
- Fertigungsdokumentation: Erzeugung von Dokumenten wie Bestückungsplänen, Bohrlisten und Schaltplanansichten.
Vorteile der CAD-Software für Leiterplatten
Präzision und Effizienz:
- Genauigkeit: CAD-Software ermöglicht präzises Design und reduziert menschliche Fehler, die bei manuellen Zeichnungen auftreten könnten.
- Automatisierung: Automatisierte Funktionen wie Autorouter und Design Rule Checks beschleunigen den Designprozess und verbessern die Effizienz.
Design-Optimierung:
- Simulation: Durch die integrierten Simulationswerkzeuge können Designer die Leistung ihrer Designs vor der Herstellung überprüfen und optimieren.
- Fehlererkennung: Designfehler und Regelverstöße können frühzeitig erkannt und behoben werden.
Dokumentation und Kommunikation:
- Fertigungsunterlagen: Die Software erstellt umfassende Dokumente und Dateien, die für die Herstellung und Montage der Leiterplatte benötigt werden.
- Kollaboration: CAD-Tools ermöglichen eine einfache Zusammenarbeit zwischen verschiedenen Teammitgliedern und Abteilungen.
Herausforderungen und Überlegungen
Komplexität:
- Lernkurve: CAD-Software kann komplex sein und eine steile Lernkurve erfordern, insbesondere für Anfänger oder neue Benutzer.
- Komplexe Designs: Die Software muss in der Lage sein, mit komplexen Designs und mehrschichtigen Leiterplatten umzugehen.
Kosten:
- Lizenzgebühren: Professionelle CAD-Software für Leiterplatten kann teuer sein, insbesondere für hochentwickelte Funktionen und umfangreiche Bibliotheken.
Integration:
- Kompatibilität: Die Software muss mit anderen Tools und Systemen kompatibel sein, z. B. zur Integration von Simulationstools oder Fertigungssystemen.
Beliebte CAD-Software für Leiterplatten
- Altium Designer: Eine umfassende und weit verbreitete Lösung für PCB-Design, bekannt für ihre leistungsstarken Funktionen und Benutzerfreundlichkeit.
- Eagle: Ein beliebtes Tool für kleinere bis mittlere Designs, oft verwendet von Hobbyisten und Kleinunternehmen.
- KiCad: Eine Open-Source-Option, die für ihre Flexibilität und Kosteneffizienz geschätzt wird.
- OrCAD: Eine professionelle Lösung für komplexe Designs und Simulationen.
Fazit
CAD-Software für Leiterplatten ist ein unverzichtbares Werkzeug für moderne Elektronikdesigner, das präzise Design, effiziente Fertigungsdokumentation und umfassende Simulationen ermöglicht. Trotz der Herausforderungen bei der Nutzung und den Kosten bietet sie erhebliche Vorteile in Bezug auf Genauigkeit, Effizienz und Designoptimierung. Die Wahl der richtigen CAD-Software hängt von den spezifischen Anforderungen des Projekts und den verfügbaren Ressourcen ab.
Vgl. auch → CAM → EAGLE → TARGET 3001!
CAF-Resistenz bezieht sich auf die Fähigkeit von Leiterplattenmaterialien, Widerstand gegen Conductive Anodic Filament (CAF)-Korrosion zu leisten. CAF ist ein Phänomen, bei dem leitende Filamente durch die Leiterplatte wachsen und zu unerwünschten Kurzschlüssen führen können. Die CAF-Resistenz ist besonders wichtig für die Zuverlässigkeit und Langlebigkeit von Leiterplatten in anspruchsvollen Umgebungen.
Was ist CAF?
Definition:
- Conductive Anodic Filament (CAF): CAF bezeichnet das Wachstum von leitfähigen Filamenten durch das Leiterplattenmaterial, das normalerweise durch elektrochemische Prozesse entsteht. Diese Filamente können zwischen Leiterbahnen und innerhalb der Leiterplatte selbst entstehen und zu Kurzschlüssen oder Fehlfunktionen führen.
Ursachen:
- Feuchtigkeit: CAF-Wachstum wird häufig durch hohe Luftfeuchtigkeit und feuchte Bedingungen gefördert.
- Elektrische Spannung: Eine dauerhafte elektrische Spannung kann das Wachstum von CAFs begünstigen.
- Materialfehler: Unzureichend behandelte oder minderwertige Leiterplattenmaterialien können anfälliger für CAF-Wachstum sein.
CAF-Resistenz
Bedeutung:
- Zuverlässigkeit: Eine hohe CAF-Resistenz ist entscheidend für die langfristige Zuverlässigkeit von Leiterplatten, insbesondere in elektronischen Geräten, die in feuchten oder extremen Umgebungen betrieben werden.
- Fehlervermeidung: Durch die Vermeidung von CAF-Wachstum können Kurzschlüsse und Ausfälle minimiert werden.
Materialien:
- CAF-resistente Materialien: Bestimmte Leiterplattenmaterialien, wie hochentwickelte Epoxidharze und spezielle Glasfaserverbunde, bieten eine verbesserte Resistenz gegen CAF. Materialien, die speziell für hohe CAF-Resistenz entwickelt wurden, haben eine verbesserte chemische und mechanische Stabilität.
Design-Strategien:
- Schaltkreismuster: Das Design der Leiterplatten sollte so gestaltet werden, dass die Wahrscheinlichkeit von CAF-Wachstum minimiert wird. Dazu gehört die Optimierung der Leiterbahnen und die Vermeidung von zu engen Abständen zwischen den Leiterbahnen.
- Beschichtungen: Der Einsatz von Schutzbeschichtungen wie Lötstopplack (Solder Mask) kann dazu beitragen, das Risiko von CAF-Korrosion zu reduzieren.
Testverfahren:
- CAF-Test: Leiterplattenmaterialien werden häufig auf ihre CAF-Resistenz getestet, um sicherzustellen, dass sie den Anforderungen an langfristige Zuverlässigkeit und Leistungsfähigkeit entsprechen. Dies kann durch spezielle Prüfstandards und Testmethoden erfolgen, die auf die Simulierung von feuchten und elektrischen Bedingungen ausgelegt sind.
Relevante Normen und Standards
IPC-Standards:
- IPC-6012: Standard für Leiterplattenmaterialien, der Anforderungen an CAF-Resistenz enthalten kann.
- IPC-TM-650: Technisches Handbuch mit Prüfmethoden, einschließlich CAF-Testmethoden, um die Widerstandsfähigkeit gegen CAF zu bewerten.
ASTM-Standards:
- ASTM D257: Testmethoden für die elektrische Widerstandsfähigkeit von Leiterplattenmaterialien, die auch zur Beurteilung der CAF-Resistenz herangezogen werden können.
Fazit
CAF-Resistenz ist ein kritischer Faktor für die Zuverlässigkeit und Langlebigkeit von Leiterplatten, insbesondere in anspruchsvollen oder feuchten Umgebungen. Der Einsatz von CAF-resistenten Materialien und die Anwendung bewährter Design- und Testmethoden sind entscheidend, um das Risiko von CAF-Korrosion zu minimieren und die Leistungsfähigkeit der Leiterplatten zu gewährleisten.
Vgl. auch → FR4
CAM steht für Computer-Aided Manufacturing und bezieht sich auf den Einsatz von Computertechnologie zur Unterstützung und Automatisierung der Fertigung von Leiterplatten (PCBs). Während CAD (Computer-Aided Design) sich auf das Design und die Planung von Leiterplatten konzentriert, befasst sich CAM mit der Umsetzung dieser Designs in physische Leiterplatten durch automatisierte Fertigungsprozesse.
Was ist CAM für Leiterplatten?
Definition:
- CAM (Computer-Aided Manufacturing): CAM für Leiterplatten bezieht sich auf die Software und Prozesse, die dazu verwendet werden, die Entwürfe, die in der CAD-Phase erstellt wurden, in fertige Leiterplatten zu überführen. CAM-Software bereitet die Designdaten auf, um sie in den Fertigungsprozess zu integrieren, und steuert die Maschinen, die die Leiterplatten herstellen.
Ziel:
- Fertigungsvorbereitung: CAM-Software bereitet die Designdateien für die Herstellung vor, indem sie notwendige Informationen wie Bohrungen, Leiterbahnmuster und Layouts verarbeitet und an die Produktionsmaschinen überträgt.
Hauptfunktionen der CAM-Software für Leiterplatten
Datenaufbereitung:
- Gerber-Dateien: CAM-Software liest und verarbeitet Gerber-Dateien, die die Leiterbahnen, Pads und anderen Designmerkmale der Leiterplatte beschreiben.
- Bohrdaten: Sie integriert Bohrdaten, die die Positionen und Durchmesser der Bohrungen für Durchkontaktierungen und Montagelöcher angeben.
Verifizierung und Optimierung:
- Design Rule Check (DRC): Die Software überprüft, ob die Designregeln eingehalten werden, um sicherzustellen, dass die Leiterplatte fehlerfrei ist und den Herstellungsanforderungen entspricht.
- Optimierung: Sie optimiert die Fertigungsdaten, indem sie beispielsweise die Platzierung von Bauteilen und die Verteilung von Leiterbahnen anpasst, um die Effizienz des Fertigungsprozesses zu erhöhen.
Fertigungsdaten-Erzeugung:
- Stanz- und Fräsdaten: Erstellung der notwendigen Daten für das Stanzen und Fräsen der Leiterplatte.
- Lötstopplack- und Maskendaten: Generierung der Daten für das Aufbringen von Schutzschichten wie Lötstopplack und Schutzmasken.
Maschinensteuerung:
- Automatisierte Maschinen: Die CAM-Software steuert automatisierte Maschinen wie Bestückungsautomaten, Ätzmaschinen und Bohrmaschinen, die die Leiterplatte gemäß den bereitgestellten Daten fertigen.
Dokumentation:
- Fertigungsdokumente: Erstellung von Dokumenten wie Bestückungsplänen, Montageanweisungen und Qualitätsprüfdaten, die für den Produktionsprozess benötigt werden.
Vorteile der CAM-Software für Leiterplatten
Automatisierung:
- Effizienz: Automatisierte Verarbeitung der Designdaten erhöht die Effizienz und reduziert den manuellen Aufwand im Fertigungsprozess.
- Fehlerreduktion: Durch automatisierte Überprüfungen und Optimierungen werden Fehler minimiert, die bei manueller Bearbeitung auftreten könnten.
Präzision:
- Genauigkeit: CAM-Software sorgt für eine hohe Präzision bei der Übertragung von Designdaten in den Fertigungsprozess, was zu einer besseren Qualität und Konsistenz der Leiterplatten führt.
Flexibilität:
- Anpassungen: CAM-Software ermöglicht es, Designänderungen schnell umzusetzen und die Fertigungsdaten entsprechend anzupassen, um auf Designänderungen oder neue Anforderungen zu reagieren.
Herausforderungen und Überlegungen
Komplexität der Daten:
- Datenintegration: Die Integration von komplexen Designdaten in die CAM-Software kann herausfordernd sein und erfordert sorgfältige Datenaufbereitung und -verarbeitung.
Software-Kosten:
- Investition: Professionelle CAM-Software kann kostspielig sein, insbesondere für Unternehmen, die umfangreiche oder spezialisierte Funktionen benötigen.
Schulung:
- Benutzerkompetenz: Die Bedienung von CAM-Software kann eine umfassende Schulung und Einarbeitung erfordern, um ihre Funktionen effektiv nutzen zu können.
Beliebte CAM-Software für Leiterplatten
- Altium Designer: Bietet umfassende CAM-Funktionen für die Verarbeitung von Designdateien und die Steuerung des Fertigungsprozesses.
- Gerber-Viewer: Viele CAM-Tools können Gerber-Dateien verarbeiten, die von verschiedenen CAD-Softwareplattformen exportiert werden.
- Zuken CAM: Eine Lösung, die speziell für die Verarbeitung und Fertigung von Leiterplatten entwickelt wurde.
Fazit
CAM-Software spielt eine entscheidende Rolle bei der Umsetzung von Leiterplattendesigns in physische Produkte. Durch die Automatisierung und Optimierung des Fertigungsprozesses trägt sie zur Effizienz und Präzision bei und ermöglicht eine schnelle und fehlerfreie Herstellung von Leiterplatten. Die richtige Wahl und effektive Nutzung von CAM-Software sind entscheidend für die Qualität und Zuverlässigkeit der produzierten Leiterplatten.
Vgl. auch → CAD
Carbon-Verfahren bezieht sich auf eine spezielle Technik zur Herstellung von Leiterplatten, die sich auf die Verwendung von Kohlenstoff oder kohlenstoffhaltigen Materialien konzentriert. Diese Methode kann verschiedene Anwendungen und Vorteile haben, je nachdem, wie Kohlenstoff in den Herstellungsprozess integriert wird.
Was ist das Carbon-Verfahren?
Definition:
- Carbon-Verfahren: In der Leiterplattenfertigung beschreibt dieses Verfahren die Integration von Kohlenstoffmaterialien, um bestimmte Eigenschaften der Leiterplatte zu verbessern, insbesondere in Bezug auf die elektrische Leitfähigkeit, Wärmeableitung und mechanische Festigkeit.
Ziel:
- Leiterplatten-Optimierung: Das Hauptziel des Carbon-Verfahrens ist es, die Leistung und Zuverlässigkeit von Leiterplatten zu verbessern, indem Kohlenstoff als Bestandteil der Materialien verwendet wird.
Anwendungen des Carbon-Verfahrens
Carbon-Füllstoffe:
- Leiterplattenmaterialien: Kohlenstoff kann als Füllstoff in Harzen und Epoxidmaterialien verwendet werden, um die elektrische Leitfähigkeit und die thermischen Eigenschaften der Leiterplatte zu verbessern.
- Wärmeableitung: Kohlenstoffverbindungen wie Graphit können dazu beitragen, die Wärme besser abzuleiten und so die Betriebstemperaturen der Leiterplatte zu kontrollieren.
Carbon-Beschichtungen:
- Antistatische Beschichtungen: Kohlenstoff kann in Form von speziellen Beschichtungen auf der Leiterplatte aufgebracht werden, um antistatische Eigenschaften zu erzielen und die Empfindlichkeit gegenüber elektrostatischen Entladungen (ESD) zu reduzieren.
Leiterbahnen:
- Kohlenstoff-Leiterbahnen: In einigen fortschrittlichen Anwendungen können auch Leiterbahnen aus kohlenstoffhaltigen Materialien verwendet werden, um spezifische elektrische Eigenschaften zu erzielen.
Vorteile des Carbon-Verfahrens
Verbesserte Wärmeableitung:
- Thermische Stabilität: Kohlenstoffmaterialien verbessern die Wärmeableitung, was besonders wichtig ist, um die thermische Belastung von Leiterplatten zu verringern und die Lebensdauer der Komponenten zu verlängern.
Erhöhte Leitfähigkeit:
- Elektrische Eigenschaften: Kohlenstoff kann die elektrische Leitfähigkeit erhöhen, was in bestimmten Anwendungen von Vorteil sein kann, wo hohe Leitfähigkeit erforderlich ist.
Mechanische Festigkeit:
- Strukturelle Integrität: Kohlenstoffverbindungen können die mechanische Festigkeit und Stabilität der Leiterplatte erhöhen, was zu einer besseren Gesamtleistung beiträgt.
Herausforderungen und Überlegungen
Materialkosten:
- Kosten: Die Integration von Kohlenstoffmaterialien kann die Materialkosten erhöhen, insbesondere bei spezialisierten Anwendungen.
Verarbeitungstechnologie:
- Verarbeitung: Das Carbon-Verfahren erfordert spezifische Verarbeitungstechnologien und -techniken, die möglicherweise zusätzliche Ausrüstung und Fachkenntnisse erfordern.
Designanpassungen:
- Komplexität: Die Verwendung von Kohlenstoffmaterialien kann zusätzliche Designüberlegungen und Anpassungen in der Leiterplattenkonstruktion erfordern.
Beispiele und Anwendungen
Hochleistungs- und Hochfrequenz-Leiterplatten:
- Elektronische Geräte: In Anwendungen, bei denen hohe Frequenzen und Leistungsdichten erforderlich sind, können Carbon-basierte Materialien verwendet werden, um die Leistung der Leiterplatte zu optimieren.
Kraftfahrzeug- und Luftfahrtindustrie:
- Zuverlässigkeit: In kritischen Anwendungen wie der Automobil- und Luftfahrtindustrie, wo hohe mechanische und thermische Belastungen auftreten, kann das Carbon-Verfahren zur Verbesserung der Zuverlässigkeit beitragen.
Konsumelektronik:
- Antistatische Beschichtungen: In der Konsumelektronik werden Carbon-beschichtete Leiterplatten möglicherweise verwendet, um ESD-Schutz zu gewährleisten und die Lebensdauer der Produkte zu verlängern.
Fazit
Das Carbon-Verfahren in der Leiterplattenfertigung bietet eine Reihe von Vorteilen, insbesondere hinsichtlich der Wärmeableitung, elektrischen Leitfähigkeit und mechanischen Festigkeit. Es stellt eine spezialisierte Methode dar, um die Leistung und Zuverlässigkeit von Leiterplatten zu verbessern. Trotz der Herausforderungen, die mit höheren Kosten und spezifischen Verarbeitungstechnologien verbunden sind, kann die Verwendung von Kohlenstoffmaterialien in bestimmten Anwendungen erhebliche Vorteile bieten und zu verbesserten Leiterplattenlösungen führen.
Castellated Holes (oder Castellated Slots) sind eine spezielle Art von Leiterplattenbohrungen oder -ausfräsungen, die in der Elektronikfertigung verwendet werden, um eine mechanische und elektrische Verbindung zwischen einer Leiterplatte (PCB) und einer anderen Platine oder einem Gehäuse herzustellen. Diese Technik wird oft bei der Herstellung von Leiterplattenmodulen verwendet, insbesondere in der Mobilfunk- und Elektronikindustrie.
Was sind Castellated Holes?
Definition:
- Castellated Holes: Diese sind halbkreisförmige oder halbseitige Aussparungen an den Kanten einer Leiterplatte, die es ermöglichen, dass die Platine mit einer anderen Platine oder einem Gehäuse mechanisch und elektrisch verbunden wird. Sie sehen aus wie kleine „Türme“ oder „Zähne“, die in die Leiterplatte gefräst oder gebohrt werden.
Design:
- Form: Die Form der Castellated Holes ist typischerweise halbrund oder gebogen, was es ermöglicht, dass die Kontakte auf der gegenüberliegenden Platine oder im Gehäuse genau passen. Diese Form sorgt für eine gute Passgenauigkeit und Verbindung.
Vorteile von Castellated Holes
Einfache Montage:
- Verbindung: Castellated Holes ermöglichen eine einfache und präzise mechanische und elektrische Verbindung zwischen verschiedenen Leiterplatten oder zwischen einer Leiterplatte und einem Gehäuse.
- Automatisierung: Diese Art der Verbindung erleichtert die automatisierte Bestückung und Montage, da die Leiterplatten präzise positioniert und verbunden werden können.
Kompakte Bauweise:
- Platzersparnis: Die Verwendung von Castellated Holes erlaubt es, Leiterplattenmodule kompakter zu gestalten und dennoch eine sichere Verbindung herzustellen, was besonders in platzkritischen Anwendungen von Vorteil ist.
Zuverlässigkeit:
- Robuste Verbindung: Die mechanische und elektrische Verbindung durch Castellated Holes bietet eine robuste und zuverlässige Lösung, die Störungen und Verbindungsprobleme minimieren kann.
Anwendungen
Modularität:
- Modulbaukästen: Castellated Holes werden häufig in modularen Elektronikdesigns verwendet, wo verschiedene Module auf einer gemeinsamen Basisplatine oder in einem Gehäuse verbunden werden. Dies ermöglicht eine flexible und erweiterbare Konstruktion.
Prototyping:
- Schnelle Entwicklung: Beim Prototyping können Castellated Holes verwendet werden, um schnell und einfach verschiedene Platinen miteinander zu verbinden, ohne aufwändige Steckverbinder oder Lötverbindungen verwenden zu müssen.
Kompakte Geräte:
- Kleinste Bauformen: In kompakten elektronischen Geräten, wie Mobiltelefonen oder tragbaren Geräten, wird diese Technik oft verwendet, um Platz zu sparen und gleichzeitig eine zuverlässige Verbindung sicherzustellen.
Herstellungsprozess
Design und Layout:
- Platine: Das Design für Castellated Holes wird während der Layout-Phase der Leiterplatte in der CAD-Software erstellt. Die Position und Größe der Castellated Holes müssen präzise definiert werden, um eine korrekte Passform zu gewährleisten.
Fertigung:
- Fräsen und Bohren: Castellated Holes werden typischerweise durch eine Kombination aus Fräsen und Bohren in der Leiterplatte hergestellt. Die Fräsen oder Bohrer erzeugen die charakteristische halbkreisförmige Form, die für die Verbindung benötigt wird.
Verarbeitung:
- Veredelung: Nach dem Fräsen und Bohren werden die Castellated Holes oft durch zusätzliche Verarbeitungsschritte, wie Verzinnen oder Beschichten, vorbereitet, um eine optimale elektrische Leitfähigkeit zu gewährleisten.
Fazit
Castellated Holes sind eine wertvolle Technik in der Leiterplattenfertigung, insbesondere für Anwendungen, bei denen präzise und kompakte Verbindungen zwischen Platinen oder zwischen Platinen und Gehäusen erforderlich sind. Sie bieten eine einfache, zuverlässige und platzsparende Lösung für die Montage und Verbindung in einer Vielzahl von Elektronikprojekten. Die korrekte Gestaltung und Fertigung dieser Strukturen ist entscheidend für die Leistungsfähigkeit und Langlebigkeit der Endprodukte.
Vgl. auch → Halboffene Durchkontaktieung
- CE-KENNZEICHNUNG
- CE-KONFORMITÄTSERKLÄRUNG
- CHEMISCH GOLD
- CHEMISCH NICKEL/GOLD
- CHEMISCH SILBER
Die CE-Kennzeichnung für Leiterplatten (PCBs) ist ein Prozess, durch den sichergestellt wird, dass Leiterplatten den europäischen Richtlinien und Normen entsprechen. Die CE-Kennzeichnung ist für viele elektronische Produkte und deren Komponenten erforderlich, um sie auf dem europäischen Markt legal verkaufen zu können. Die Anforderungen für die CE-Kennzeichnung variieren je nach dem Endprodukt, in dem die Leiterplatte verwendet wird, und den spezifischen Richtlinien, die für das betreffende Produkt gelten.
Bedeutung der CE-Kennzeichnung für Leiterplatten
Marktzugang:
- Die CE-Kennzeichnung ist erforderlich, um sicherzustellen, dass Leiterplatten in elektronischen Geräten und anderen Produkten, die auf dem europäischen Markt verkauft werden, den europäischen Vorschriften entsprechen.
Sicherheits- und Qualitätsstandards:
- Die CE-Kennzeichnung zeigt an, dass die Leiterplatte den relevanten Sicherheits-, Gesundheits- und Umweltanforderungen entspricht, die für Produkte in der EU festgelegt sind.
Anforderungen für die CE-Kennzeichnung von Leiterplatten
Richtlinien und Normen:
- Richtlinien: Die spezifischen Richtlinien, die für die CE-Kennzeichnung von Leiterplatten relevant sind, hängen davon ab, wie die Leiterplatte im Endprodukt verwendet wird. Beispiele hierfür sind die Elektromagnetische Verträglichkeit (EMV)-Richtlinie, die Niederspannungsrichtlinie (LVD) und die RoHS-Richtlinie (Beschränkung der Verwendung bestimmter gefährlicher Stoffe).
- Normen: Leiterplatten müssen in Übereinstimmung mit harmonisierten Normen produziert werden, die für die jeweiligen Richtlinien festgelegt sind. Diese Normen behandeln beispielsweise die elektrische Sicherheit und die elektromagnetische Verträglichkeit.
Technische Dokumentation:
- Dokumentation: Hersteller von Leiterplatten müssen technische Unterlagen erstellen, die die Einhaltung der relevanten Richtlinien belegen. Dazu gehören beispielsweise Prüfberichte, Materialdatenblätter und Produktionsberichte.
Prüfung und Zertifizierung:
- Prüfung: In einigen Fällen kann es erforderlich sein, dass Leiterplatten von benannten Stellen (notified bodies) geprüft werden, insbesondere wenn sie in sicherheitskritischen oder komplexen Anwendungen eingesetzt werden.
- Zertifizierung: Für einige Produkte kann eine Zertifizierung durch benannte Stellen notwendig sein, bevor die CE-Kennzeichnung angebracht wird.
Konformitätserklärung:
- Erklärung: Der Hersteller muss eine EG-Konformitätserklärung ausstellen, die die Einhaltung der relevanten Richtlinien und Normen bestätigt. Diese Erklärung muss zusammen mit der technischen Dokumentation bereitgehalten werden.
Anwendungen der CE-Kennzeichnung für Leiterplatten
Elektronische Geräte:
- Geräte: Leiterplatten, die in elektronischen Geräten wie Computern, Mobiltelefonen, Haushaltsgeräten und anderen elektronischen Geräten verwendet werden, müssen den CE-Anforderungen entsprechen, um sicherzustellen, dass die Endgeräte die erforderlichen Standards erfüllen.
Medizinische Geräte:
- Medizinprodukte: Leiterplatten, die in medizinischen Geräten eingesetzt werden, müssen zusätzlichen Anforderungen entsprechen, um die Sicherheit und Zuverlässigkeit der medizinischen Anwendungen zu gewährleisten.
Industrie- und Automatisierungstechnik:
- Industrielle Anwendungen: Leiterplatten in Industrieanlagen und Automatisierungssystemen müssen die Anforderungen der CE-Richtlinien erfüllen, um eine sichere und zuverlässige Funktionalität zu garantieren.
Schritte zur Erlangung der CE-Kennzeichnung für Leiterplatten
Verständnis der Richtlinien:
- Analyse: Ermitteln Sie, welche EU-Richtlinien und Normen für die Leiterplatte gelten, je nach dem Endprodukt, in dem sie verwendet wird.
Erstellung der technischen Dokumentation:
- Dokumente: Bereiten Sie die erforderlichen technischen Unterlagen vor, die die Konformität der Leiterplatte mit den relevanten Richtlinien belegen.
Durchführung von Prüfungen:
- Prüfung: Falls erforderlich, führen Sie Prüfungen durch, um sicherzustellen, dass die Leiterplatte den geltenden Normen entspricht.
Ausstellung der Konformitätserklärung:
- Erklärung: Stellen Sie eine EG-Konformitätserklärung aus, die die Einhaltung der relevanten Vorschriften bestätigt.
Anbringung der CE-Kennzeichnung:
- Kennzeichnung: Bringen Sie das CE-Zeichen auf der Leiterplatte oder dem Endprodukt an, falls erforderlich, und stellen Sie sicher, dass alle Dokumente bereitgehalten werden.
Fazit
Die CE-Kennzeichnung für Leiterplatten ist ein wichtiger Prozess, der sicherstellt, dass die Leiterplatten den europäischen Normen und Richtlinien entsprechen. Dies schützt nicht nur die Endnutzer und gewährleistet die Qualität und Sicherheit der elektronischen Geräte, sondern ermöglicht auch den freien Handel innerhalb der EU. Um die CE-Kennzeichnung zu erhalten, müssen Hersteller sicherstellen, dass ihre Leiterplatten alle relevanten Richtlinien einhalten und die erforderliche Dokumentation bereitstellen.
Vgl. auch → CE-Konformitätserklärung
Die CE-Konformitätserklärung für Leiterplatten (PCBs) ist ein offizielles Dokument, das bestätigt, dass eine Leiterplatte den relevanten Richtlinien und Normen der Europäischen Union entspricht, die für ihre Verwendung in Endprodukten gelten. Dieses Dokument ist Teil des Prozesses zur Erlangung der CE-Kennzeichnung und stellt sicher, dass die Leiterplatte den erforderlichen Sicherheits- und Qualitätsanforderungen entspricht.
Zweck der CE-Konformitätserklärung
Rechtliche Anforderung:
- Die CE-Konformitätserklärung ist notwendig, um die Einhaltung der europäischen Vorschriften zu belegen, damit die Leiterplatte auf dem europäischen Markt verkauft und verwendet werden kann.
Sicherheits- und Qualitätsgarantie:
- Sie stellt sicher, dass die Leiterplatte die grundlegenden Sicherheits- und Leistungsanforderungen erfüllt und damit sicher für den Einsatz in elektronischen Geräten ist.
Inhalt der CE-Konformitätserklärung
Identifikation des Herstellers:
- Name und Adresse: Vollständige Angaben des Herstellers oder seines autorisierten Vertreters, der für die Konformitätserklärung verantwortlich ist.
Produktbeschreibung:
- Produktbezeichnung: Detaillierte Beschreibung der Leiterplatte, einschließlich Modellnummer, Typ und gegebenenfalls spezifische Varianten.
Anwendbare Richtlinien und Normen:
- Richtlinien: Auflistung der relevanten EU-Richtlinien, die für die Leiterplatte gelten, wie die Elektromagnetische Verträglichkeit (EMV)-Richtlinie, die Niederspannungsrichtlinie (LVD) und die RoHS-Richtlinie (Beschränkung der Verwendung bestimmter gefährlicher Stoffe).
- Normen: Verweis auf die harmonisierten Normen oder spezifischen Normen, die zur Einhaltung der Richtlinien verwendet wurden.
Technische Dokumentation:
- Dokumentation: Hinweis auf die technische Dokumentation, die die Konformität der Leiterplatte belegt, wie z.B. Prüfberichte, Berechnungen und technische Zeichnungen.
Konformitätserklärung:
- Bestätigung: Eine klare Erklärung, dass die Leiterplatte den genannten Richtlinien und Normen entspricht.
Datum und Unterschrift:
- Datum: Das Datum, an dem die Konformitätserklärung ausgestellt wurde.
- Unterschrift: Unterschrift eines autorisierten Vertreters des Herstellers oder des Verantwortlichen.
Schritte zur Erstellung der CE-Konformitätserklärung für Leiterplatten
Überprüfung der Richtlinien:
- Feststellung: Ermitteln, welche EU-Richtlinien und Normen für die spezifische Anwendung der Leiterplatte relevant sind.
Erstellung der technischen Dokumentation:
- Dokumentation: Sammeln und erstellen der technischen Unterlagen, die die Konformität der Leiterplatte belegen. Dazu gehören Prüfberichte, Materialdatenblätter und technische Zeichnungen.
Durchführung von Prüfungen:
- Prüfung: Sicherstellen, dass die Leiterplatte gemäß den relevanten Richtlinien und Normen getestet wurde, insbesondere wenn sie in sicherheitskritischen oder komplexen Anwendungen eingesetzt wird.
Erstellung der Konformitätserklärung:
- Dokument: Verfassen der Konformitätserklärung, in der alle relevanten Informationen über die Einhaltung der Richtlinien und Normen angegeben werden.
Unterschrift und Datierung:
- Formalitäten: Die Konformitätserklärung muss datiert und von einer autorisierten Person unterschrieben werden, die für die Richtigkeit der Erklärung verantwortlich ist.
Aufbewahrung und Bereitstellung
Dokumentation aufbewahren:
- Archivierung: Die Konformitätserklärung und die zugehörige technische Dokumentation müssen für einen bestimmten Zeitraum aufbewahrt werden, um im Falle von Prüfungen oder Nachfragen von Aufsichtsbehörden bereitgestellt werden zu können.
Bereitstellung:
- Zugänglichkeit: Die Konformitätserklärung sollte bei Bedarf für Behörden oder Kunden zugänglich sein, insbesondere bei der Einführung von Produkten auf dem Markt oder bei Audits.
Fazit
Die CE-Konformitätserklärung ist ein wesentliches Dokument, das sicherstellt, dass eine Leiterplatte den europäischen Normen und Richtlinien entspricht und damit für den europäischen Markt geeignet ist. Sie umfasst wichtige Informationen über die Einhaltung der relevanten Richtlinien, die technische Dokumentation und die Bestätigung der Konformität durch den Hersteller. Durch die korrekte Erstellung und Pflege dieses Dokuments gewährleisten Hersteller die Sicherheit und Compliance ihrer Produkte und erleichtern deren Marktzugang in der EU.
Chemisch Gold bezieht sich auf eine spezielle Beschichtung, die auf Leiterplatten aufgebracht wird, um die Oberfläche zu schützen und die elektrische Leitfähigkeit zu verbessern. Im Gegensatz zu galvanisch aufgebrachten Goldschichten wird chemisch Gold durch einen chemischen Prozess, bei dem Gold in Lösung und dann auf die Leiterplatte aufgebracht wird, ohne eine elektrische Stromquelle zu nutzen, aufgetragen.
Vorteile von chemisch Gold
Korrosionsschutz:
- Schutz: Chemisch Gold bietet einen hervorragenden Schutz vor Korrosion und Oxidation, was besonders wichtig ist, um eine langfristige Zuverlässigkeit und Stabilität der elektronischen Verbindungen sicherzustellen.
Hohe Leitfähigkeit:
- Elektrische Eigenschaften: Die Beschichtung bietet eine ausgezeichnete elektrische Leitfähigkeit, was zu einer besseren Performance der Leiterplattenverbindungen führt.
Langlebigkeit:
- Verschleißfest: Die goldene Schicht ist sehr widerstandsfähig gegenüber mechanischer Abnutzung und Abrieb, was die Haltbarkeit der Leiterplatten erhöht.
Gleichmäßige Schichtdicke:
- Präzision: Chemisch Gold ermöglicht eine sehr gleichmäßige und präzise Schichtdicke, was für hohe Anforderungen an die Verbindungskontakte wichtig ist.
Vermeidung von Lötproblemen:
- Lötbarkeit: Die goldene Beschichtung erleichtert das Löten und minimiert Probleme wie Lötbrücken und schlechte Lötstellen, da die Oberfläche gut lötbar ist.
Prozess der chemischen Goldbeschichtung
Vorbereitung der Leiterplatte:
- Reinigung: Die Leiterplatte wird gründlich gereinigt, um Verunreinigungen, Oxidationen oder andere Rückstände zu entfernen, die die Beschichtung beeinträchtigen könnten.
Beschichtung:
- Chemische Behandlung: Die Leiterplatte wird in eine chemische Lösung getaucht, die Goldionen enthält. Das Gold wird durch einen chemischen Reduktionsprozess auf die Kupferflächen der Leiterplatte aufgebracht.
Verarbeitung und Trocknung:
- Trocknung: Nach dem Auftragen des Goldes wird die Leiterplatte getrocknet, und die Goldbeschichtung wird durch zusätzliche Behandlungen stabilisiert.
Anwendungen von chemisch Gold
Hohe Frequenz- und Hochgeschwindigkeitsanwendungen:
- RF- und Hochgeschwindigkeits-PCBs: Chemisch Gold wird oft in hochfrequenten und Hochgeschwindigkeitsanwendungen verwendet, da es exzellente elektrische Eigenschaften bietet.
Verbindungskontakte:
- Steckverbinder: Die goldene Beschichtung wird häufig für Steckverbinder und andere Verbindungselemente verwendet, um eine zuverlässige und korrosionsbeständige Verbindung zu gewährleisten.
Medizinische und Militärische Anwendungen:
- Kritische Anwendungen: In Bereichen wie der Medizintechnik oder der Militärtechnik, wo höchste Anforderungen an die Zuverlässigkeit und Haltbarkeit gestellt werden, ist chemisch Gold eine bevorzugte Wahl.
Nachteile der chemischen Goldbeschichtung
Kosten:
- Preis: Chemisch Gold kann teurer sein als andere Oberflächenbeschichtungen, da der Prozess und das Material kostenintensiv sind.
Dünne Schichtdicke:
- Begrenzung: Obwohl chemisch Gold eine gleichmäßige Schichtdicke ermöglicht, ist die Schichtdicke im Vergleich zu galvanisch aufgetragenem Gold begrenzt, was in bestimmten Anwendungen ein Nachteil sein könnte.
Fazit
Die chemische Goldbeschichtung ist eine hochwertige Oberflächenbehandlung für Leiterplatten, die eine ausgezeichnete elektrische Leitfähigkeit, Korrosionsschutz und Langlebigkeit bietet. Durch den chemischen Auftragsprozess wird eine präzise und gleichmäßige Goldschicht aufgebracht, die für viele anspruchsvolle Anwendungen ideal ist. Trotz der höheren Kosten ist chemisch Gold aufgrund seiner Vorteile in der Elektronikfertigung und in spezialisierten Anwendungen weit verbreitet.
Vgl. auch → Oberfläche → HAL
Vgl. auch → Chemisch Gold
Chemisch Silber ist eine Oberflächenbeschichtung für Leiterplatten (PCBs), die durch einen chemischen Prozess aufgebracht wird. Diese Beschichtung bietet mehrere Vorteile, insbesondere in Bezug auf Leitfähigkeit und Kosten, und wird häufig in der Elektronikfertigung verwendet.
Was ist chemisch Silber?
Chemisch Silber bezeichnet eine Beschichtung, bei der Silber durch einen chemischen Prozess auf die Leiterplatte aufgebracht wird. Dieser Prozess, auch als chemische Silberabscheidung bekannt, nutzt eine Silberlösung, die in Kontakt mit der Leiterplatte gebracht wird, um eine dünne Schicht Silber auf den Kupferflächen zu bilden. Im Gegensatz zur galvanischen Silberabscheidung, bei der Strom verwendet wird, um Silber auf die Leiterplatte abzuscheiden, erfolgt die chemische Silberabscheidung ohne elektrische Energie.
Vorteile von chemisch Silber
Kosteneffizienz:
- Preis-Leistungs-Verhältnis: Chemisch Silber ist im Vergleich zu anderen Beschichtungen wie chemisch Gold kostengünstiger. Dies macht es zu einer wirtschaftlichen Wahl für viele Anwendungen.
Gute Leitfähigkeit:
- Elektrische Eigenschaften: Silber ist bekannt für seine exzellente elektrische Leitfähigkeit. Die chemisch aufgebrachte Silberschicht verbessert die elektrische Leistung der Leiterplatte.
Lötbarkeit:
- Verarbeitbarkeit: Die Silberbeschichtung bietet eine gute Lötbarkeit, was die Verarbeitung der Leiterplatte während der Bestückung und Löten erleichtert.
Korrosionsschutz:
- Schutz: Chemisch Silber bietet einen gewissen Schutz gegen Oxidation und Korrosion, obwohl es nicht so robust ist wie andere Oberflächenbeschichtungen wie chemisch Gold.
Gleichmäßige Beschichtung:
- Präzision: Der chemische Prozess ermöglicht eine gleichmäßige und präzise Aufbringung der Silberschicht.
Prozess der chemischen Silberbeschichtung
Vorbereitung der Leiterplatte:
- Reinigung: Die Leiterplatte wird gründlich gereinigt, um Schmutz, Oxide und andere Verunreinigungen zu entfernen, die die Beschichtung beeinträchtigen könnten.
Beschichtung:
- Chemische Abscheidung: Die Leiterplatte wird in eine Silberlösung getaucht. Silberionen in der Lösung reagieren chemisch und lagern sich auf den Kupferflächen der Leiterplatte ab, wodurch eine dünne Silberschicht entsteht.
Verarbeitung und Trocknung:
- Trocknung: Nach der Beschichtung wird die Leiterplatte getrocknet und die Silberbeschichtung wird stabilisiert.
Anwendungen von chemisch Silber
Kosteneffiziente Leiterplatten:
- Allgemeine Anwendungen: Chemisch Silber wird häufig in Anwendungen verwendet, bei denen Kosten und Leistung im Gleichgewicht stehen müssen, wie in Consumer-Elektronik und weniger kritischen Industriegeräten.
Verbindungskontakte:
- Steckverbinder: Die Beschichtung wird oft in Verbindungskontakten verwendet, da sie eine gute Lötbarkeit und elektrische Leitfähigkeit bietet.
Prototypen und Kleinserien:
- Entwicklungsprojekte: Aufgrund der kostengünstigen Herstellung ist chemisch Silber besonders geeignet für Prototypen und Kleinserienfertigung.
Nachteile der chemischen Silberbeschichtung
Oxidation:
- Korrosionsprobleme: Silber ist anfällig für Oxidation, was im Laufe der Zeit zu einer Verschlechterung der elektrischen Eigenschaften führen kann. Die Silberbeschichtung kann sich schwarz verfärben, wenn sie nicht richtig geschützt wird.
Haltbarkeit:
- Mechanische Abnutzung: Die Beschichtung kann mechanisch weniger widerstandsfähig sein als andere Oberflächen wie chemisch Gold, was zu Abnutzung oder Beschädigung bei intensiver Nutzung führen kann.
Lagerung:
- Empfindlichkeit: Leiterplatten mit chemisch Silber müssen möglicherweise unter speziellen Bedingungen gelagert werden, um eine Oxidation der Silberoberfläche zu verhindern.
Fazit
Die chemische Silberbeschichtung bietet eine kostengünstige und effektive Lösung für viele Anwendungen in der Leiterplattenfertigung. Sie kombiniert gute elektrische Leitfähigkeit und Lötbarkeit mit einem erschwinglichen Preis. Trotz ihrer Vorteile ist es wichtig, die Beschichtung gegen Oxidation zu schützen und ihre Anwendung entsprechend der Anforderungen der jeweiligen elektrischen und mechanischen Umgebung zu wählen.
Vgl. auch → Chemisch Zinn → Chemisch Gold → Drahtbonden
- CHEMISCH ZINN
- CLIPPING
- COURTYARD
- CTE
- CTI-WERT
- CU
Chemisch Zinn ist eine Oberflächenbeschichtung, die auf Leiterplatten (PCBs) aufgebracht wird, um die Leitfähigkeit zu verbessern und Korrosion zu verhindern. Diese Beschichtung wird durch einen chemischen Prozess aufgetragen, bei dem Zinn in Lösung auf die Leiterplatte aufgebracht wird. Im Folgenden sind die wichtigsten Aspekte und Eigenschaften von chemisch beschichtetem Zinn zusammengefasst:
Was ist chemisch Zinn?
Chemisch Zinn bezeichnet eine Beschichtung, bei der eine dünne Schicht Zinn durch einen chemischen Prozess auf die Leiterplatte aufgebracht wird. Dieser Prozess nutzt eine Zinnlösung, die auf die Leiterplatte aufgetragen wird, um eine gleichmäßige Zinnschicht auf den Kupferflächen zu erzeugen. Im Gegensatz zu galvanischen Verfahren, bei denen Strom verwendet wird, um Zinn abzuscheiden, erfolgt die chemische Zinnbeschichtung ohne elektrische Energie.
Vorteile von chemisch Zinn
Gute Lötbarkeit:
- Verarbeitung: Chemisch Zinn bietet eine ausgezeichnete Lötbarkeit, was bedeutet, dass Lötverbindungen auf der beschichteten Leiterplatte einfach und zuverlässig hergestellt werden können.
Kosteneffizienz:
- Preis-Leistungs-Verhältnis: Die Beschichtung ist kostengünstig im Vergleich zu anderen Oberflächenbehandlungen wie chemisch Gold, was sie zu einer wirtschaftlichen Wahl für viele Anwendungen macht.
Gleichmäßige Beschichtung:
- Präzision: Die chemische Zinnbeschichtung sorgt für eine gleichmäßige Schichtdicke, die eine konsistente Leistung und Zuverlässigkeit der Leiterplatte gewährleistet.
Reflow-Schutz:
- Prozesstauglichkeit: Zinn schützt die Kupferflächen während des Reflow-Lötprozesses vor Oxidation und stellt sicher, dass die Lötverbindungen von hoher Qualität sind.
Prozess der chemischen Zinnbeschichtung
Vorbereitung der Leiterplatte:
- Reinigung: Die Leiterplatte wird gründlich gereinigt, um Oxide, Verunreinigungen und andere Rückstände zu entfernen, die die Qualität der Beschichtung beeinträchtigen könnten.
Beschichtung:
- Chemische Abscheidung: Die Leiterplatte wird in eine Zinnlösung getaucht. Die Zinnionen in der Lösung lagern sich chemisch auf den Kupferflächen der Leiterplatte ab und bilden eine dünne Schicht Zinn.
Verarbeitung und Trocknung:
- Trocknung: Nach dem Auftragen der Zinnschicht wird die Leiterplatte getrocknet, und die Zinnbeschichtung wird stabilisiert.
Anwendungen von chemisch Zinn
Standard-Anwendungen:
- Elektronik: Chemisch Zinn wird häufig in Standard-Leiterplatten verwendet, die in der Konsumelektronik und anderen nicht extrem anspruchsvollen Anwendungen zum Einsatz kommen.
Prototypen und Kleinserien:
- Entwicklung: Aufgrund seiner Kosten- und Verarbeitungsvorteile wird chemisch Zinn oft für Prototypen und Kleinserienfertigungen verwendet.
Wellenlöten:
- Verarbeitung: Die Beschichtung eignet sich gut für Leiterplatten, die im Wellenlötprozess verwendet werden, da sie die Kupferoberflächen während des Lötens schützt.
Nachteile der chemischen Zinnbeschichtung
Oxidation:
- Korrosionsanfälligkeit: Zinn kann mit der Zeit oxidieren, was zu einer Verschlechterung der elektrischen Eigenschaften führen kann. Daher ist eine zusätzliche Schutzschicht oder eine spezielle Lagerung notwendig, um eine langfristige Leistung zu gewährleisten.
Mechanische Abnutzung:
- Verschleiß: Die Zinnschicht ist weniger widerstandsfähig gegenüber mechanischer Abnutzung im Vergleich zu anderen Beschichtungen wie chemisch Gold oder chemisch Silber.
Lagerung:
- Empfindlichkeit: Leiterplatten mit chemisch Zinn müssen unter kontrollierten Bedingungen gelagert werden, um eine vorzeitige Oxidation der Zinnoberfläche zu verhindern.
Fazit
Die chemische Zinnbeschichtung bietet eine kostengünstige und effektive Lösung für viele Anwendungen in der Leiterplattenfertigung. Sie stellt sicher, dass Leiterplatten gut lötbar sind und schützt die Kupferflächen während des Lötprozesses. Trotz ihrer Vorteile, wie der ausgezeichneten Lötbarkeit und Kosteneffizienz, ist es wichtig, die Beschichtung richtig zu lagern und gegebenenfalls zusätzlichen Schutz gegen Oxidation zu berücksichtigen, um die langfristige Leistung der Leiterplatten zu gewährleisten.
Vgl. auch → PCB OVERSEAS
Clipping in Bezug auf Leiterplatten und Elektronik bezieht sich auf den Prozess, bei dem Signale oder Daten in einer bestimmten Weise zugeschnitten oder beschränkt werden, um bestimmte Anforderungen oder Spezifikationen zu erfüllen. Der Begriff „Clipping“ kann verschiedene Bedeutungen je nach Kontext haben, insbesondere in der Signalverarbeitung und in der Leiterplattenfertigung. Hier sind die wichtigsten Aspekte des Clippings im Zusammenhang mit Elektronik und Leiterplatten:
Clipping in der Signalverarbeitung
Definition:
- Signalverarbeitung: Im Kontext der Signalverarbeitung bezieht sich Clipping auf die Methode, bei der ein Signal auf einen bestimmten Bereich beschränkt wird. Dies geschieht durch das Beschneiden von Signalspitzen, die über einem festgelegten Schwellenwert liegen.
Anwendung:
- Verhinderung von Verzerrungen: Clipping wird verwendet, um Verzerrungen in elektrischen Signalen zu vermeiden, die auftreten können, wenn das Signal die maximalen Werte eines Systems überschreitet. Dies kann in Audioverstärkern, Kommunikationssystemen und anderen elektronischen Geräten geschehen.
Arten des Clippings:
- Hartes Clipping: Bei hartem Clipping werden Signalspitzen abrupt auf den maximalen Wert begrenzt, was zu verzerrten Signalen führen kann.
- Weiches Clipping: Bei weichem Clipping werden Signalspitzen allmählich begrenzt, was eine geringere Verzerrung verursacht und eine sanftere Übergangszone bietet.
Auswirkungen:
- Verzerrung: Clipping kann zu Verzerrungen und Signalverfälschungen führen, insbesondere wenn die Clipping-Grenzen nicht richtig eingestellt sind.
Clipping in der Leiterplattenfertigung
Definition:
- Leiterplatten: Im Kontext der Leiterplattenfertigung bezieht sich Clipping oft auf den Prozess, bei dem überstehende oder nicht benötigte Teile von Leiterplatten entfernt werden. Dies kann das Entfernen von überschüssigem Material oder das Schneiden von Leiterplatten auf die gewünschte Größe umfassen.
Anwendung:
- Größenanpassung: Clipping wird verwendet, um Leiterplatten auf die richtige Größe zu bringen oder um spezifische Konturen und Formen zu erstellen, die für die Montage und Integration in ein Endgerät erforderlich sind.
- Verarbeitung: Dieser Prozess kann mechanisch oder chemisch erfolgen, wobei mechanische Fräsen oder Laserschneiden gängige Methoden sind.
Vorteile:
- Präzision: Durch Clipping kann die Leiterplatte genau auf die erforderlichen Spezifikationen zugeschnitten werden, was eine präzise Passform und Funktionalität im Endprodukt sicherstellt.
- Reduzierung von Abfall: Effizientes Clipping kann helfen, Abfall zu reduzieren und die Nutzung von Material zu optimieren.
Fazit
Clipping ist ein vielseitiger Begriff in der Elektronik und Leiterplattenfertigung. In der Signalverarbeitung beschreibt es das Beschneiden von Signalspitzen, um Verzerrungen zu verhindern, während es in der Leiterplattenfertigung das Schneiden oder Entfernen von überschüssigem Material bezeichnet, um die Leiterplatte auf die erforderlichen Spezifikationen zu bringen. In beiden Kontexten spielt Clipping eine wichtige Rolle bei der Optimierung von Leistung und Passgenauigkeit.
Der Begriff „Courtyard“ bezieht sich in der Leiterplattenfertigung auf eine bestimmte Designzone rund um ein Bauteil, die für die Platzierung und Montage von Komponenten und deren Verbindungen von Bedeutung ist. Hier sind die wesentlichen Aspekte des Courtyards im Kontext von Leiterplatten:
Was ist ein Courtyard?
Courtyard bezeichnet den Raum auf einer Leiterplatte, der um ein Bauteil herum definiert ist und für die Montage und Installation von Komponenten berücksichtigt werden muss. Es handelt sich um eine Art Schutzbereich oder Sicherheitszone, die sicherstellt, dass keine anderen Komponenten oder Verbindungen in diesen Bereich hineinragen, was zu Problemen bei der Bestückung oder Funktion führen könnte.
Funktionen und Bedeutung des Courtyards
Sicherstellung der Montierbarkeit:
- Platzierung: Der Courtyard-Bereich stellt sicher, dass um ein Bauteil herum genügend Platz vorhanden ist, um es ordnungsgemäß zu montieren und zu löten, ohne dass benachbarte Bauteile oder Verbindungen im Weg sind.
Vermeidung von Interferenzen:
- Abstand halten: Der Courtyard hilft, Interferenzen zwischen benachbarten Komponenten zu vermeiden, indem er sicherstellt, dass andere Bauteile oder Leiterbahnen nicht in diesen Bereich hineinragen und so die Funktionalität der Schaltung beeinträchtigen.
Designvorgaben:
- Herstellungsrichtlinien: Der Courtyard wird oft durch Designregeln und -richtlinien definiert, die sicherstellen, dass alle Bauteile den erforderlichen Abstand zu anderen Komponenten oder Leiterbahnen haben, um Montageprobleme und elektrische Störungen zu vermeiden.
Fehlervermeidung:
- Vermeidung von Kurzschlüssen: Durch die Definition eines Courtyard-Bereichs wird das Risiko von Kurzschlüssen oder anderen elektrischen Problemen verringert, die auftreten können, wenn Bauteile oder Verbindungen zu nah beieinander liegen.
Darstellung und Nutzung im PCB-Design
PCB-Design-Software:
- Integration: In vielen PCB-Design-Softwareprogrammen wie Eagle, Altium Designer oder KiCad wird der Courtyard-Bereich automatisch oder manuell definiert, um sicherzustellen, dass alle Bauteile korrekt platziert und die Designregeln eingehalten werden.
Visuelle Darstellung:
- Design-Dokumentation: Der Courtyard-Bereich wird oft als zusätzliche Schicht oder als visuelle Markierung im Schaltplan und Layout angezeigt, um Designern zu helfen, die Platzierung und Abstände korrekt zu überprüfen.
Verifikation:
- Design-Checks: Während des Design-Reviews und der Verifikation wird der Courtyard-Bereich überprüft, um sicherzustellen, dass keine Überschreitungen oder Verstößen gegen die Platzierungsrichtlinien vorliegen.
Fazit
Der Courtyard ist ein wichtiger Aspekt im PCB-Design, der den erforderlichen Platz um ein Bauteil definiert, um eine ordnungsgemäße Montage und Vermeidung von Interferenzen sicherzustellen. Durch die Einhaltung der Courtyard-Regeln können Designer sicherstellen, dass ihre Leiterplatten effizient und fehlerfrei gefertigt und montiert werden können.
Vgl. auch → DFM
CTE steht für Coefficient of Thermal Expansion (Temperaturausdehnungskoeffizient). Dieser Begriff ist besonders wichtig im Kontext von Leiterplatten (PCBs), da er die Fähigkeit eines Materials beschreibt, sich bei Temperaturänderungen auszudehnen oder zusammenzuziehen. Hier sind die wesentlichen Aspekte des CTE in Bezug auf Leiterplatten:
Was ist der CTE?
Der CTE (Coefficient of Thermal Expansion) ist eine Maßzahl, die angibt, wie stark sich ein Material bei Temperaturänderungen ausdehnt oder zusammenzieht. Der CTE wird typischerweise in Einheiten von Teilen pro Million (ppm) pro Grad Celsius (°C) angegeben.
Bedeutung des CTE für Leiterplatten
Materialauswahl:
- Kompatibilität: Der CTE ist entscheidend bei der Auswahl der Materialien für Leiterplatten. Materialien mit ähnlichem CTE-Wert wie die verwendeten Komponenten und Lötmaterialien sorgen dafür, dass sich die Leiterplatte und die Komponenten gleichmäßig ausdehnen und zusammenziehen, um mechanische Spannungen und Risse zu vermeiden.
Reliabilität und Lebensdauer:
- Stressvermeidung: Ein hoher Unterschied im CTE zwischen der Leiterplatte und den Komponenten kann zu mechanischen Spannungen führen, insbesondere bei Temperaturwechseln. Diese Spannungen können die Lebensdauer der Leiterplatte und der Bauteile beeinträchtigen und zu Lötstellenrissen oder anderen Defekten führen.
Design-Überlegungen:
- Thermisches Management: Beim Design von Leiterplatten müssen Designer den CTE-Wert berücksichtigen, um sicherzustellen, dass die Leiterplatte unter verschiedenen Betriebstemperaturen zuverlässig funktioniert. Dies schließt das Design von Lötstellen und die Platzierung von Komponenten ein.
Materialien:
- Leiterplattenmaterialien: Unterschiedliche Leiterplattenmaterialien haben unterschiedliche CTE-Werte. Beispielsweise haben FR-4, ein weit verbreitetes Leiterplattenmaterial, und andere Hochfrequenzmaterialien wie PTFE unterschiedliche CTE-Werte. Bei der Auswahl des Materials muss berücksichtigt werden, wie gut es die thermischen Ausdehnungen seiner Umgebung anpasst.
CTE in der Praxis
Messung:
- Testmethoden: Der CTE eines Materials wird durch spezielle Testmethoden gemessen, bei denen das Material über einen definierten Temperaturbereich hinweg erwärmt oder abgekühlt wird, und die Änderung der Abmessungen des Materials aufgezeichnet wird.
Simulationswerkzeuge:
- Design-Simulation: In modernen PCB-Design-Softwaretools können Designer Simulationen durchführen, um die Auswirkungen unterschiedlicher CTE-Werte auf das Design zu bewerten und mögliche Probleme vor der Fertigung zu identifizieren.
Design-Richtlinien:
- Richtlinien und Standards: Es gibt spezifische Richtlinien und Standards, die den Umgang mit CTE-Werten regeln, um sicherzustellen, dass Leiterplatten und Komponenten unter verschiedenen Betriebsbedingungen zuverlässig bleiben.
Fazit
Der CTE (Coefficient of Thermal Expansion) ist ein kritischer Faktor bei der Leiterplattenfertigung und -design. Er beschreibt, wie stark sich ein Material bei Temperaturänderungen ausdehnt oder zusammenzieht. Die Berücksichtigung des CTE hilft dabei, mechanische Spannungen zu vermeiden und die Zuverlässigkeit der Leiterplatte über verschiedene Temperaturbereiche hinweg sicherzustellen. Designer müssen sorgfältig wählen und testen, um sicherzustellen, dass alle Materialien und Komponenten gut zusammenarbeiten, um eine langlebige und funktionale Leiterplatte zu gewährleisten.
Vgl. auch → Mulitlayer
Der CTI-Wert (Comparative Tracking Index) ist eine wichtige Kenngröße in der Leiterplattenfertigung, insbesondere im Hinblick auf die elektrische Sicherheit und die Isolationsfähigkeit von Materialien. Er misst die Fähigkeit eines Materials, elektrische Durchschläge und Kriechströme zu widerstehen, die durch Verschmutzung oder Feuchtigkeit verursacht werden können. Hier sind die wesentlichen Aspekte des CTI-Werts im Kontext von Leiterplatten:
Was ist der CTI-Wert?
Der CTI-Wert (Comparative Tracking Index) ist eine Kennzahl, die angibt, wie widerstandsfähig ein Material gegenüber elektrischen Durchschlägen ist, die durch Kriechströme entlang seiner Oberfläche verursacht werden. Der Wert wird typischerweise in Volt (V) angegeben und beschreibt die Spannung, bei der das Material beginnt, elektrische Durchschläge unter definierten Testbedingungen zu entwickeln.
Bedeutung des CTI-Werts für Leiterplatten
Elektrische Sicherheit:
- Isolationsfähigkeit: Der CTI-Wert ist ein Indikator für die Fähigkeit eines Leiterplattenmaterials, elektrische Isolation aufrechtzuerhalten, selbst wenn es durch Feuchtigkeit oder Verschmutzung beeinträchtigt wird. Ein hoher CTI-Wert bedeutet, dass das Material besser in der Lage ist, elektrische Durchschläge zu verhindern und eine sichere Isolation zu bieten.
Vermeidung von Kriechströmen:
- Kriechstromfestigkeit: Der CTI-Wert hilft dabei, das Risiko von Kriechströmen zu minimieren, die durch Verunreinigungen oder feuchte Bedingungen auf der Leiterplatte entstehen können. Materialien mit höherem CTI-Wert sind widerstandsfähiger gegen diese Art von elektrischen Problemen.
Materialauswahl:
- Leiterplattenmaterialien: Bei der Auswahl von Leiterplattenmaterialien ist der CTI-Wert ein wichtiger Faktor. Materialien wie FR-4 haben spezifische CTI-Werte, die sicherstellen müssen, dass sie den Anforderungen an elektrische Isolierung und Sicherheit entsprechen. Höherwertige Materialien für besonders anspruchsvolle Anwendungen können einen höheren CTI-Wert aufweisen.
Testverfahren für den CTI-Wert
Testbedingungen:
- Verschmutzung und Feuchtigkeit: Der CTI-Wert wird durch spezielle Tests bestimmt, bei denen das Material unter kontrollierten Bedingungen mit feuchten und verschmutzten Umgebungen konfrontiert wird. Dabei wird die Spannung erhöht, bis ein elektrischer Durchschlag auftritt.
Testmethoden:
- Standardisierte Tests: Der CTI-Wert wird gemäß internationalen Standards wie IEC 60112 getestet. Diese Tests bewerten die elektrische Durchschlagsfestigkeit von Materialien, die verschiedenen elektrischen und umweltbedingten Belastungen ausgesetzt sind.
Anwendung des CTI-Werts in der Leiterplattenfertigung
Design-Richtlinien:
- Sicherheitsstandards: In der Leiterplattenfertigung und -design werden Materialien mit ausreichendem CTI-Wert ausgewählt, um sicherzustellen, dass die Leiterplatten die erforderlichen Sicherheitsstandards erfüllen und zuverlässig in verschiedenen Umgebungen arbeiten.
Zulassungen:
- Normen und Vorschriften: Der CTI-Wert ist ein Bestandteil von Zulassungs- und Zertifizierungsprozessen für Leiterplattenmaterialien und -produkte, insbesondere in sicherheitskritischen Anwendungen, wie in der Automobil- und Luftfahrtindustrie.
Fazit
Der CTI-Wert (Comparative Tracking Index) ist eine wichtige Kennzahl für die elektrische Sicherheit von Leiterplattenmaterialien. Er misst die Fähigkeit eines Materials, elektrische Durchschläge und Kriechströme zu widerstehen, die durch Verschmutzung oder Feuchtigkeit entstehen können. Ein hoher CTI-Wert ist entscheidend, um eine zuverlässige elektrische Isolation und Sicherheit in verschiedenen Betriebsumgebungen zu gewährleisten. Bei der Auswahl von Leiterplattenmaterialien ist es wichtig, den CTI-Wert zu berücksichtigen, um sicherzustellen, dass die Materialien den erforderlichen Sicherheits- und Leistungsanforderungen entsprechen.
Vgl. auch → Kriechstromfestigkeit
Cu steht für Kupfer
Vgl. auch → Kupfer
- DAMPFPHASEN-LÖTEN
- DELAMINATION
- DESIGN RULES
- DESIGN RULE CHECK
- DFA
Dampfphasen-Löten ist ein spezielles Verfahren zum Löten von Elektronikbauteilen auf Leiterplatten, das sich durch seine einzigartigen Eigenschaften und Vorteile auszeichnet. Es gehört zu den reflow-Lötverfahren, bei denen die Lötverbindungen durch Erhitzen einer Lötpaste hergestellt werden. Das Dampfphasen-Löten nutzt die physikalischen Eigenschaften von Dampf, um eine präzise und kontrollierte Wärmeübertragung zu ermöglichen.
Definition und Prinzip
- Dampfphasen-Löten: Auch bekannt als „Vapor Phase Soldering“ (VPS), ist ein Löten-Verfahren, bei dem die Leiterplatte und die Bauteile durch das Verdampfen eines speziellen Lötsmittels (typischerweise ein Fluorcarbon) auf die erforderliche Temperatur gebracht werden. Die Wärme wird durch den Dampf des Lötsmittels übertragen, der eine konstante und kontrollierte Temperatur aufrechterhält.
Prozessbeschreibung
- Vorbereitung: Die Leiterplatte wird zusammen mit der Lötpaste und den Bauteilen in eine Dampfphasen-Lötmaschine geladen. Die Lötpaste enthält Lötmaterial, das während des Lötprozesses geschmolzen wird.
- Erwärmen durch Dampf: Die Maschine erzeugt Dampf durch Erhitzen des Lötsmittels, das die Leiterplatte umgibt. Der Dampf hat eine feste Siedetemperatur, die für das spezifische Lötsystem ausgelegt ist.
- Löten: Der Dampf bringt die gesamte Leiterplatte auf die genaue Löttemperatur. Das Lötmaterial in der Paste schmilzt und bildet eine feste Verbindung zwischen den Bauteilen und der Leiterplatte.
- Kühlung: Nach dem Löten wird die Leiterplatte aus dem Dampf herausgenommen und abgekühlt. Die Lötstellen erstarren und die Verbindung wird stabil.
Vorteile
- Gleichmäßige Wärmeübertragung: Durch die konstante Temperatur des Dampfes wird eine gleichmäßige und präzise Wärmeübertragung auf alle Teile der Leiterplatte gewährleistet, was die Qualität der Lötverbindungen verbessert.
- Reduzierte thermische Belastung: Die genaue Steuerung der Löttemperatur minimiert die thermische Belastung der Bauteile und der Leiterplatte, was das Risiko von Schäden reduziert.
- Geringere Oxidation: Da der Lötprozess in einem geschlossenen Dampfraum stattfindet, ist das Risiko von Oxidation der Lötstellen während des Prozesses reduziert.
Nachteile
- Kosten: Dampfphasen-Lötmaschinen und das spezielle Lötsystem können kostspielig sein, was das Verfahren für kleine Produktionsvolumen weniger attraktiv macht.
- Wartung: Die Ausrüstung benötigt regelmäßige Wartung und Nachfüllungen des Lötsmittels, um optimal zu funktionieren.
- Begrenzte Anwendung: Die Technologie kann möglicherweise nicht für alle Leiterplatten-Designs oder Bauteile geeignet sein, insbesondere bei sehr komplexen oder hochdichten Leiterplatten.
Anwendungsbereiche
- Komplexe Bauteile: Ideal für die Verarbeitung von Leiterplatten mit vielen Bauteilen oder für sehr dichte Designs, bei denen eine präzise Temperaturkontrolle erforderlich ist.
- Kleinserien und Prototypen: Aufgrund der höheren Kosten kann das Verfahren in Kleinserienfertigung und Prototypenentwicklung nützlich sein, wo eine hohe Qualität der Lötverbindungen entscheidend ist.
- Hohe Qualität: Besonders geeignet für Anwendungen, bei denen die Qualität der Lötstellen von höchster Bedeutung ist, wie z.B. in der Medizintechnik oder Luft- und Raumfahrt.
Vergleich zu anderen Lötverfahren
- Reflow-Löten: Im Vergleich zum herkömmlichen Reflow-Löten bietet das Dampfphasen-Löten eine präzisere Temperaturkontrolle, ist jedoch kostenintensiver und komplexer in der Einrichtung.
- Wellenlöten: Im Gegensatz zum Wellenlöten, bei dem die gesamte Leiterplatte durch geschmolzenes Lot geführt wird, bietet das Dampfphasen-Löten eine kontrollierte Temperaturumgebung, die das Risiko von Wärme- und Schädigungen reduziert.
Fazit
Das Dampfphasen-Löten ist ein präzises und kontrolliertes Lötsystem, das sich durch seine gleichmäßige Wärmeübertragung und reduzierte thermische Belastung auszeichnet. Es bietet besonders hohe Qualität der Lötverbindungen und wird in anspruchsvollen Anwendungen und bei komplexen Leiterplatten-Designs eingesetzt. Trotz der höheren Kosten und Wartungsanforderungen bleibt es eine wertvolle Technologie in der Leiterplattenfertigung.
Definition und Ursachen
Delamination: Der Begriff beschreibt den Prozess, bei dem sich die Schichten einer mehrlagigen Leiterplatte voneinander lösen. Dies kann auf ein Versagen der Klebefolie oder des Laminats zwischen den Schichten hinweisen.
Ursachen:
- Thermische Belastung: Hohe Temperaturen, wie sie bei der Herstellung oder bei der Nutzung auftreten, können die Klebeverbindung zwischen den Schichten schwächen und zu Delamination führen.
- Feuchtigkeit: Eindringen von Feuchtigkeit oder Wasser kann die Klebeschicht aufweichen und zu einer Trennung der Schichten führen.
- Mechanische Belastung: Stöße, Vibrationen oder andere mechanische Einwirkungen können die Struktur der Leiterplatte beschädigen und zu Delamination führen.
- Unzureichende Verarbeitung: Fehler während des Laminierungsprozesses oder unvollständige Aushärtung der Klebstoffe können ebenfalls Delamination verursachen.
- Chemische Einflüsse: Chemische Reaktionen oder Verunreinigungen während der Produktion können die Klebeschicht schädigen.
Auswirkungen
- Elektrische Ausfälle: Delamination kann zu Unterbrechungen in den elektrischen Verbindungen führen und somit zu Ausfällen oder Fehlfunktionen der Leiterplatte.
- Mechanische Schwäche: Die Struktur der Leiterplatte wird geschwächt, was zu physischen Brüchen oder anderen Schäden führen kann.
- Wassereintritt: Delaminierte Bereiche können Wasser oder andere Verunreinigungen aufnehmen, die zusätzliche Schäden verursachen können.
Vermeidung und Prävention
- Qualitätskontrolle: Strenge Kontrollen während der Fertigung, insbesondere bei der Laminierung und Aushärtung der Leiterplatte, können das Risiko von Delamination minimieren.
- Temperatur- und Feuchtigkeitsmanagement: Sicherstellen, dass Leiterplatten in kontrollierten Umgebungen produziert und gelagert werden, um extreme Temperaturen und Feuchtigkeit zu vermeiden.
- Materialauswahl: Verwendung von hochwertigen Materialien und Klebstoffen, die den spezifischen Anforderungen der Leiterplatte entsprechen, kann helfen, Delamination zu verhindern.
- Design: Berücksichtigung von Designfaktoren, die das Risiko mechanischer Belastungen minimieren, kann ebenfalls zur Vermeidung von Delamination beitragen.
Erkennung
- Optische Inspektion: Sichtbare Anzeichen von Delamination können durch optische Inspektion entdeckt werden, insbesondere wenn die Leiterplatte mechanisch beschädigt oder abgenutzt ist.
- Röntgeninspektion: Röntgenuntersuchungen können eingesetzt werden, um interne Schichtprobleme zu erkennen, die auf Delamination hindeuten.
- Mechanische Tests: Tests wie der Scher- oder Biegetest können verwendet werden, um die strukturelle Integrität der Leiterplatte zu überprüfen und Delamination zu identifizieren.
Reparatur und Behebung
- Erneuerung: In den meisten Fällen muss eine delaminierte Leiterplatte ersetzt werden, da Reparaturen oft nicht die gleiche Leistung oder Zuverlässigkeit bieten.
- Reparaturtechniken: In einigen Fällen können spezielle Reparaturmethoden angewendet werden, um die beschädigten Bereiche zu stabilisieren, aber diese sind oft aufwändig und nicht immer effektiv.
Vergleich zu ähnlichen Problemen
- Delamination vs. Warping: Während Delamination das Ablösen von Schichten beschreibt, bezieht sich Warping auf Verformungen oder Verwindungen der gesamten Leiterplatte.
- Delamination vs. Voids: Voids sind Hohlräume oder Lufteinschlüsse in Lötverbindungen oder zwischen Schichten, die ebenfalls die Leiterplattenintegrität beeinträchtigen können.
Fazit
Delamination ist ein kritisches Problem in der Leiterplattenfertigung und -nutzung, das die elektrische und mechanische Integrität der Leiterplatte gefährden kann. Die Vermeidung und Kontrolle von Delamination erfordert sorgfältige Aufmerksamkeit während der Fertigung, strenge Qualitätskontrollen und geeignete Design- und Materialauswahl. Durch geeignete Maßnahmen können die Risiken minimiert und die Leistung der Leiterplatten optimiert werden.
Vgl. auch → Lagen
Design Rules (Designregeln) für Leiterplatten sind spezifische Richtlinien und Anforderungen, die während der Planung und Gestaltung von Leiterplatten berücksichtigt werden müssen, um sicherzustellen, dass die fertige Leiterplatte den funktionalen, elektrischen und mechanischen Anforderungen entspricht. Diese Regeln helfen dabei, die Zuverlässigkeit und Leistung der Leiterplatte zu gewährleisten und Produktionsprobleme zu vermeiden.
Definition und Bedeutung
- Design Rules: Dies sind eine Reihe von Richtlinien, die im Designprozess von Leiterplatten (PCB) angewendet werden. Sie umfassen geometrische Vorgaben, elektrische Anforderungen und Fertigungsstandards, die sicherstellen, dass die Leiterplatte sowohl funktional als auch produzierbar ist.
Arten von Design Rules
Geometrische Regeln:
- Leiterbahn-Breiten: Die Breite der Leiterbahnen muss so gewählt werden, dass sie den Strom tragen kann, ohne zu überhitzen oder eine zu hohe Widerstandsbelastung zu verursachen.
- Abstände: Mindestabstände zwischen Leiterbahnen, Pads und anderen Bauteilen sind erforderlich, um Kurzschlüsse und Signalstörungen zu vermeiden.
- Bohrgrößen: Bohrungen für Via-Pads, Befestigungsbohrungen und Bauteile müssen den Spezifikationen für die Größe und Position entsprechen.
Elektrische Regeln:
- Impedanzkontrolle: Bei Hochfrequenzanwendungen ist es wichtig, die Impedanz der Leiterbahnen zu kontrollieren, um Signalverluste und Reflexionen zu minimieren.
- Kreuzungen und Übertragungsleitungen: Vermeidung von unerwünschten Kreuzungen und Berücksichtigung der Übertragungsleitungen, um elektromagnetische Störungen (EMI) zu reduzieren.
- Stromtragfähigkeit: Sicherstellen, dass die Leiterbahnen ausreichend dimensioniert sind, um den maximalen Strom zu führen, den sie tragen müssen.
Mechanische Regeln:
- Randabstände: Mindestabstände von Leiterbahnen und Pads zum Rand der Leiterplatte, um mechanische Schäden während der Bearbeitung und Montage zu vermeiden.
- Bauteile-Platzierung: Positionierung der Bauteile auf der Leiterplatte muss den mechanischen Anforderungen und dem Platzbedarf entsprechen.
Fertigungsregeln:
- Minimale Bohrdurchmesser: Bestimmen des kleinsten Bohrdurchmessers, der für die Fertigung geeignet ist.
- Löcher und Via-Stapel: Gestaltung der Vias und ihrer Stapelungen, um die Herstellbarkeit zu gewährleisten und Fertigungsprobleme zu vermeiden.
Implementierung von Design Rules
- EDA-Software: Moderne Elektronik-Design-Automatisierungssoftware (EDA-Software) ermöglicht es Designern, Designregeln zu definieren und zu überprüfen. Diese Tools bieten automatische Prüfungen und Warnungen, wenn Designregeln verletzt werden.
- Design Rule Check (DRC): Ein Design Rule Check ist eine Funktion in EDA-Software, die das Design auf Regelverletzungen überprüft und Designer auf mögliche Probleme hinweist.
- Design Review: Regelmäßige Überprüfungen des Designs durch erfahrene Ingenieure können dazu beitragen, mögliche Regelverletzungen oder Probleme frühzeitig zu erkennen und zu beheben.
Vorteile der Anwendung von Design Rules
- Verbesserte Zuverlässigkeit: Durch die Einhaltung von Designregeln wird die Wahrscheinlichkeit von Fehlfunktionen und Ausfällen der Leiterplatte reduziert.
- Optimierte Leistung: Designregeln helfen dabei, die elektrische Leistung zu optimieren, indem sie sicherstellen, dass die Leiterplatte die gewünschten elektrischen Eigenschaften und Signalübertragungen erfüllt.
- Kosteneffizienz: Vermeidung von Fertigungsproblemen und Nacharbeiten durch frühzeitige Identifikation und Behebung von Designfehlern spart Zeit und Kosten.
Beispiele für Design Rule Verstöße
- Zu geringe Leiterbahn-Abstände: Wenn die Abstände zwischen den Leiterbahnen zu gering sind, kann es zu Kurzschlüssen oder Signalstörungen kommen.
- Unzureichende Leiterbahn-Breiten: Zu schmale Leiterbahnen können den benötigten Strom nicht sicher führen und überhitzen.
- Fehlerhafte Bohrungen: Bohrungen, die nicht den Spezifikationen entsprechen, können Probleme bei der Bestückung und Herstellung verursachen.
Fazit
Design Rules sind essenziell für die Gestaltung von Leiterplatten und spielen eine zentrale Rolle bei der Sicherstellung der Funktionalität, Zuverlässigkeit und Herstellbarkeit von Leiterplatten. Durch die sorgfältige Anwendung und Überprüfung dieser Regeln können Designer sicherstellen, dass ihre Leiterplatten den technischen Anforderungen entsprechen und problemlos produziert werden können.
Vgl. auch → DRC→ DFM
Design Rules Check (DRC) ist ein wesentlicher Bestandteil des Entwurfsprozesses von Leiterplatten (PCBs), der sicherstellt, dass das Design die festgelegten technischen Spezifikationen und Fertigungsanforderungen erfüllt. Dieser Überprüfungsprozess wird häufig in EDA-Software (Electronic Design Automation) durchgeführt, um sicherzustellen, dass das Layout der Leiterplatte keine Verstöße gegen die Designregeln aufweist und somit funktionsfähig und produzierbar ist.
Definition und Zweck
Design Rules Check (DRC): DRC ist ein automatisierter Prozess, der die Entwurfsdaten einer Leiterplatte auf Übereinstimmung mit einer vordefinierten Sammlung von Regeln und Spezifikationen überprüft. Diese Regeln umfassen typischerweise Abstandsanforderungen, Layoutbeschränkungen, Signalintegritätsanforderungen und andere wichtige Parameter.
Zweck: Der Hauptzweck des DRC ist es, Designfehler zu identifizieren und zu beheben, die die Funktionalität, Zuverlässigkeit oder Fertigbarkeit der Leiterplatte beeinträchtigen könnten. Durch den Einsatz von DRC können Entwickler sicherstellen, dass das Design den Herstellungsanforderungen entspricht und dass mögliche Probleme vor der eigentlichen Fertigung erkannt werden.
Wichtige Designregeln
DRC umfasst eine Vielzahl von Designregeln, die je nach Anwendung und Komplexität der Leiterplatte variieren können. Zu den häufigsten Regeln gehören:
Abstandregeln: Überprüfung, ob die Abstände zwischen Leiterbahnen, Pads, und anderen Elementen den festgelegten Mindestwerten entsprechen. Diese Regeln verhindern Kurzschlüsse und gewährleisten die elektrische Integrität.
Leiterbahnbreiten: Sicherstellung, dass die Breite der Leiterbahnen den Anforderungen für Strombelastbarkeit und Signalübertragung entspricht.
Bohr- und Padgrößen: Kontrolle, ob die Bohrungen und Pads die richtigen Größen für die Bauteile haben und für den Fertigungsprozess geeignet sind.
Schichtstapelung: Überprüfung der korrekten Anordnung und Verbindungen der verschiedenen Schichten in mehrlagigen Leiterplatten.
Signalintegrität: Sicherstellung, dass Signalwege und -routen für Hochfrequenzsignale oder andere empfindliche Signale optimiert sind.
Design für Fertigung (DFM): Überprüfung, ob das Design die Fertigungsanforderungen erfüllt und ob es mögliche Probleme bei der Herstellung gibt.
DRC-Methoden
Manuelle Überprüfung: In einigen Fällen kann eine manuelle Überprüfung durch den Designer erforderlich sein, insbesondere bei komplexen Designs oder spezifischen Anforderungen.
Automatisierte DRC-Tools: Die meisten modernen EDA-Softwarepakete bieten automatisierte DRC-Tools, die das Design in Echtzeit oder nach Abschluss des Entwurfs überprüfen. Diese Tools können umfangreiche Regelsets verwenden, um potenzielle Fehler zu identifizieren und zu kennzeichnen.
Ablauf des Design Rules Check
Festlegung der Designregeln: Vor der Überprüfung müssen die Designregeln definiert und in der EDA-Software konfiguriert werden. Diese Regeln basieren auf den Spezifikationen des Projekts und den Fertigungsanforderungen.
Durchführung des DRC: Die EDA-Software analysiert das Leiterplattendesign anhand der festgelegten Regeln. Während dieses Prozesses werden Fehler und Verstöße gegen die Regeln identifiziert und dokumentiert.
Fehlerbehebung: Die gefundenen Probleme müssen vom Designer behoben werden. Dies kann Anpassungen im Layout, Änderungen der Leiterbahnbreiten, Anpassungen der Abstände oder andere Korrekturen umfassen.
Wiederholte Überprüfung: Nach der Behebung der Fehler wird der DRC-Prozess wiederholt, um sicherzustellen, dass alle Probleme behoben wurden und keine neuen Fehler aufgetreten sind.
Finalisierung des Designs: Sobald alle Designregeln eingehalten werden und alle Fehler behoben sind, kann das Design für die Fertigung freigegeben werden.
Vorteile des Design Rules Check
Fehlervermeidung: DRC hilft dabei, potenzielle Designfehler frühzeitig zu identifizieren und zu beheben, bevor das Design in die Produktion geht.
Fertigungsfähigkeit: Durch die Einhaltung der Fertigungsregeln wird sichergestellt, dass das Design ohne Probleme produziert werden kann.
Kostenersparnis: Frühe Fehlererkennung reduziert die Notwendigkeit für teure Designänderungen und Nacharbeiten während oder nach der Fertigung.
Erhöhte Zuverlässigkeit: Das Einhalten der Designregeln trägt zur Verbesserung der Zuverlässigkeit und Leistung der fertigen Leiterplatte bei.
Fazit
Design Rules Check (DRC) ist ein unverzichtbarer Bestandteil des Leiterplattendesignprozesses, der sicherstellt, dass das Design den erforderlichen technischen Spezifikationen und Fertigungsanforderungen entspricht. Durch den Einsatz automatisierter DRC-Tools können Designer potenzielle Fehler frühzeitig erkennen, die Herstellbarkeit der Leiterplatte sicherstellen und die Gesamtqualität und Zuverlässigkeit der elektronischen Produkte verbessern.
Vgl. auch → Design Rules
DFA steht für Design for Assembly. Dies ist ein Ansatz in der Produktentwicklung, der darauf abzielt, Produkte so zu gestalten, dass sie einfach und kosteneffektiv zusammengebaut werden können. Im Kontext von Leiterplatten (PCBs) bezieht sich DFA auf die Gestaltung der Leiterplatte und ihrer Komponenten, um den Zusammenbau zu erleichtern, die Montagekosten zu reduzieren und die Gesamtzuverlässigkeit des Produkts zu verbessern.
Definition und Bedeutung
- Design for Assembly (DFA): DFA ist ein Designansatz, der darauf abzielt, die Montageeffizienz zu maximieren und die Produktionskosten durch Optimierung der Bau- und Montageprozesse zu minimieren. Dieser Ansatz hilft dabei, Probleme zu vermeiden, die während der Montage auftreten können, und sorgt für eine einfachere und fehlerfreie Fertigung.
Grundprinzipien von DFA
Reduzierung der Anzahl der Teile: Weniger Teile erleichtern die Montage und reduzieren die Wahrscheinlichkeit von Fehlern. Vereinfachte Designs, die weniger Komponenten erfordern, sind in der Regel kostengünstiger und schneller zu montieren.
Standardisierung von Bauteilen: Die Verwendung standardisierter Komponenten und Teile kann die Verfügbarkeit und Austauschbarkeit verbessern, die Schulungskosten für Montagepersonal senken und die Lagerhaltung vereinfachen.
Einfache Handhabung und Positionierung: Bauteile sollten so gestaltet und positioniert werden, dass sie leicht und ohne spezielle Werkzeuge oder Vorrichtungen montiert werden können. Dazu gehört auch, dass Bauteile in einer Weise platziert werden, die eine klare und einfache Ausrichtung ermöglicht.
Fehlervermeidung: Designmerkmale, die Fehler beim Zusammenbau verhindern, wie z.B. Verriegelungsmechanismen, Führungselemente oder asymmetrische Formen, helfen, Fehler während des Montageprozesses zu vermeiden.
Einfache Prüfung und Wartung: Der Zugang zu Bauteilen für Inspektion, Wartung oder Austausch sollte bei der Gestaltung berücksichtigt werden. Es sollte möglich sein, Prüfungen durchzuführen und Reparaturen vorzunehmen, ohne dass der gesamte Aufbau zerlegt werden muss.
Implementierung von DFA in der Leiterplattenherstellung
Layout-Optimierung: Das Design der Leiterplatte sollte so gestaltet werden, dass alle Bauteile leicht positioniert und gelötet werden können. Dies kann durch die Anordnung der Komponenten, die Minimierung der Anzahl von Verbindungen und die Vereinfachung der Leiterbahnführung erreicht werden.
Automatisierung: Berücksichtigung der Möglichkeiten zur Automatisierung des Montageprozesses. Designs, die für automatische Bestückungs- und Lötprozesse optimiert sind, können die Effizienz und Genauigkeit erhöhen.
Klares Markieren: Die Leiterplatte sollte klare Markierungen für die Positionierung und Orientierung der Bauteile enthalten, um den Montageprozess zu erleichtern.
Kompatibilität mit Standardverfahren: Sicherstellen, dass die Leiterplatte und ihre Komponenten mit den verfügbaren Fertigungs- und Montageverfahren kompatibel sind. Dies beinhaltet die Berücksichtigung von Toleranzen und Standardgrößen.
Vorteile von DFA
Kosteneinsparungen: Reduzierung der Montagekosten durch einfachere und schnellere Montageprozesse. Weniger Fehlerraten und Nacharbeiten führen zu niedrigeren Produktionskosten.
Verbesserte Qualität: Einfache und fehlervermeidende Designs tragen zur höheren Zuverlässigkeit und Qualität des Endprodukts bei.
Schnellere Markteinführung: Ein effizienter Montageprozess kann die Zeit bis zur Fertigstellung des Produkts verkürzen, was zu einer schnelleren Markteinführung führt.
Reduzierte Schulungskosten: Einfache und intuitive Designs erfordern weniger Schulung für das Montagepersonal, was zusätzliche Kosten spart.
Beispiele für DFA-Praktiken in der Leiterplattenfertigung
Durchkontaktierungen (Vias) optimieren: Vermeidung unnötiger und komplexer Via-Designs, die zusätzliche Arbeit und Fehlerquellen einführen können.
Komponentenausrichtung: Komponenten so anordnen, dass sie leicht automatisch bestückt werden können, z.B. durch Ausrichtung der Pins in der gleichen Richtung.
Reduzierung der Bauteilvariationen: Minimierung der verschiedenen Bauteiltypen und -größen, um den Montageprozess zu vereinfachen und Fehler zu vermeiden.
Fazit
Design for Assembly (DFA) ist ein wesentlicher Aspekt der Produktentwicklung, insbesondere in der Leiterplattenfertigung. Durch die Implementierung von DFA-Prinzipien kann die Montageeffizienz verbessert, die Kosten gesenkt und die Produktqualität erhöht werden. Eine durchdachte und optimierte Leiterplattengestaltung, die die Montagefreundlichkeit berücksichtigt, trägt zu einer erfolgreichen und kosteneffektiven Fertigung bei.
- DFM
- DICKKUPFER
- DIELEKTRIKUM
- DIELEKTRIZITÄTSKONSTANTE
- DIFFUSIONSSPERRE
DFM steht für Design for Manufacturing und ist ein Ansatz in der Produktentwicklung, der darauf abzielt, die Herstellbarkeit eines Produkts zu optimieren. Dieser Ansatz stellt sicher, dass ein Produkt nicht nur effizient und kostengünstig produziert werden kann, sondern auch dass es die Qualitätsstandards erfüllt und alle Produktionsanforderungen berücksichtigt.
Definition und Bedeutung
- Design for Manufacturing (DFM): DFM ist eine Methodik, die darauf abzielt, das Produktdesign so zu gestalten, dass es den Produktionsprozessen und -techniken optimal angepasst ist. Dies umfasst die Berücksichtigung der Fertigungskosten, der Produktionszeit und der Qualität, um die Herstellbarkeit zu verbessern und Produktionsprobleme zu vermeiden.
Grundprinzipien von DFM
Einfache Herstellung: Das Design sollte so einfach wie möglich gehalten werden, um die Herstellungskosten zu minimieren. Komplexe Designs, die viele verschiedene Komponenten oder Fertigungsschritte erfordern, können die Produktionskosten und -zeiten erhöhen.
Materialauswahl: Die Wahl von Materialien, die leicht verfügbar und kostengünstig sind, kann die Fertigungskosten senken und die Produktionsprozesse vereinfachen.
Standardisierung: Der Einsatz von standardisierten Komponenten und Prozessen kann die Fertigungskosten reduzieren und die Effizienz verbessern. Standardisierte Teile sind oft günstiger und schneller zu beschaffen und zu verarbeiten.
Fertigungstechniken: Berücksichtigung der Fertigungstechniken und -fähigkeiten des Herstellers. Das Design sollte den verfügbaren Technologien und Maschinen entsprechen, um die Produktionskosten und -zeiten zu optimieren.
Toleranzen und Passgenauigkeit: Festlegung realistischer Toleranzen, die die Herstellbarkeit nicht beeinträchtigen. Zu enge Toleranzen können die Fertigungskosten erhöhen und die Produktionszeiten verlängern.
Implementierung von DFM
Frühe Designphasen: DFM sollte bereits in der frühen Designphase berücksichtigt werden, um die größten Effizienzgewinne zu erzielen. Änderungen im späteren Verlauf der Produktentwicklung können teurer und schwieriger umzusetzen sein.
Zusammenarbeit mit Herstellern: Enge Zusammenarbeit mit den Fertigungsingenieuren und -technikern kann helfen, Designprobleme frühzeitig zu erkennen und Lösungen zu entwickeln, die die Produktionsanforderungen erfüllen.
Simulation und Prototypen: Einsatz von Simulationstools und Prototypen zur Überprüfung der Herstellbarkeit und zur Identifizierung von potenziellen Problemen im Design vor der eigentlichen Produktion.
Vorteile von DFM
Kosteneinsparungen: Durch die Optimierung des Designs für die Herstellung können die Produktionskosten gesenkt und die Effizienz erhöht werden.
Kürzere Produktionszeiten: Ein gut durchdachtes Design kann die Produktionszeiten verkürzen, indem es den Fertigungsprozess vereinfacht und automatisiert.
Höhere Qualität: Die Berücksichtigung der Herstellbarkeit führt oft zu höherer Produktqualität, da das Design auf die Produktionsfähigkeiten abgestimmt ist und Fehlerquellen minimiert werden.
Reduzierte Produktionsrisiken: Durch die frühzeitige Identifizierung und Behebung von Designproblemen können Risiken und Probleme während der Produktion minimiert werden.
Beispiele für DFM-Praktiken in der Leiterplattenfertigung
Minimierung von Bohrungen und Vias: Reduzierung der Anzahl von Bohrungen und Vias kann die Produktionskosten senken und die Herstellbarkeit verbessern, da jeder zusätzliche Bohrungsschritt zusätzliche Kosten und Produktionszeiten verursacht.
Optimierung der Leiterbahnführung: Effiziente Leiterbahnführung, um unnötige Wendungen und Überlappungen zu vermeiden, kann die Fertigungskosten senken und die Signalübertragung verbessern.
Verwendung von Standardgrößen: Einsatz von standardisierten Bauteilen und Layouts kann die Komplexität reduzieren und die Fertigungskosten senken.
Fazit
Design for Manufacturing (DFM) ist ein wesentlicher Aspekt der Produktentwicklung, der darauf abzielt, die Herstellbarkeit eines Produkts zu verbessern und die Produktionskosten zu senken. Durch die frühzeitige Integration von DFM-Prinzipien in den Designprozess können Unternehmen sicherstellen, dass ihre Produkte effizient, kostengünstig und mit hoher Qualität produziert werden können. Eine enge Zusammenarbeit mit Herstellern und die Nutzung von Simulationstools sind entscheidend für die erfolgreiche Implementierung von DFM.
Vgl. auch → DRC
Definition und Bedeutung
- Dickkupfer: Dieser Begriff beschreibt Leiterplatten, bei denen das Kupfer auf der Oberfläche oder in den inneren Schichten dicker als die Standardwerte ist. Dickkupferleiterplatten werden typischerweise bei speziellen Anwendungen eingesetzt, die erhöhte Anforderungen an die Strombelastbarkeit und Wärmeableitung stellen.
Anwendungsgebiete von Dickkupfer
Leistungselektronik: In Schaltungen, die hohe Ströme führen müssen, wie in Leistungsreglern, Motorsteuerungen oder Netzteilen, sind dickkupferne Leiterplatten erforderlich, um die Wärme effektiv abzuleiten und die elektrischen Widerstände zu minimieren.
Wärmemanagement: Dickkupfer kann helfen, die Wärme, die durch hohe Ströme oder intensive Lasten erzeugt wird, effizient abzuleiten. Dies ist besonders wichtig in Anwendungen, bei denen die Wärmeentwicklung ein kritischer Faktor ist.
Hochfrequenzanwendungen: Bei Hochfrequenzanwendungen kann dickkupferne Beschichtung dazu beitragen, die Signalübertragungsqualität zu verbessern, indem sie den Widerstand verringert und die Signalintegrität erhöht.
Herstellung von Dickkupferleiterplatten
Kupferauftrag: Die Herstellung von Dickkupferleiterplatten beginnt mit dem Auftrag einer dicken Kupferschicht auf die Leiterplatte. Dies kann durch verschiedene Verfahren erfolgen, wie z.B. galvanisches Aufbringen von Kupfer oder durch die Verwendung spezieller Laminierprozesse.
Ätzen: Nach dem Auftrag des Kupfers wird das überschüssige Material durch Ätzen entfernt, um die gewünschten Leiterbahnstrukturen zu erzeugen. Das Ätzverfahren muss sorgfältig angepasst werden, um die Dicke des Kupfers zu berücksichtigen.
Veredelung: Dickkupferleiterplatten können zusätzlich veredelt werden, um Korrosionsschutz und bessere Lötfähigkeit zu gewährleisten. Typische Veredelungsverfahren sind das chemische Vergolden oder Verzinnen.
Vorteile von Dickkupfer
Erhöhte Stromtragfähigkeit: Dickere Kupferschichten können höhere Ströme führen, ohne dass es zu übermäßiger Erwärmung oder signifikantem Widerstand kommt.
Besseres Wärmemanagement: Dickkupfer leitet Wärme effizienter ab, was die Lebensdauer der Leiterplatte und ihrer Komponenten verlängern kann.
Erhöhte Robustheit: Dickere Kupferschichten verbessern die mechanische Festigkeit und Stabilität der Leiterplatte, was zu einer höheren Widerstandsfähigkeit gegen mechanische Belastungen und Abrieb führt.
Herausforderungen und Überlegungen
Kosten: Dickkupferleiterplatten sind in der Regel teurer als Standardleiterplatten, da der zusätzliche Kupferauftrag und die speziellen Fertigungsprozesse höhere Kosten verursachen.
Fertigung: Die Bearbeitung von dicken Kupferschichten kann komplexer sein und erfordert spezielle Ausrüstung und Prozesse, um sicherzustellen, dass die Leiterplatten den gewünschten Spezifikationen entsprechen.
Design-Anforderungen: Bei der Gestaltung von Leiterplatten mit dickem Kupfer muss berücksichtigt werden, dass die thermischen und elektrischen Eigenschaften des Designs an die Dicke des Kupfers angepasst werden müssen.
Fazit
Dickkupfer ist eine wichtige Bauweise in der Leiterplattenfertigung, die für spezielle Anwendungen mit hohen Anforderungen an Strombelastung und Wärmemanagement erforderlich ist. Die Verwendung von dickem Kupfer bietet signifikante Vorteile in Bezug auf Stromtragfähigkeit und Wärmeableitung, bringt jedoch auch Herausforderungen bei Kosten und Fertigung mit sich. Durch sorgfältige Planung und den Einsatz geeigneter Fertigungstechniken kann die Leistung und Zuverlässigkeit von Leiterplatten in anspruchsvollen Anwendungen erheblich verbessert werden.
Dielektrikum ist ein Begriff aus der Elektronik und Materialwissenschaft, der ein Material beschreibt, das als Isolator zwischen leitenden Schichten in elektronischen Bauteilen, insbesondere in Leiterplatten, verwendet wird. Es hat die Fähigkeit, elektrische Felder zu isolieren und zu speichern, ohne selbst elektrischen Strom zu leiten.
Definition und Bedeutung
- Dielektrikum: Ein Dielektrikum ist ein nichtleitendes Material, das in der Lage ist, ein elektrisches Feld zu speichern. Es wird in verschiedenen elektronischen und elektrischen Anwendungen eingesetzt, um die Isolierung zwischen elektrischen Leitern zu gewährleisten und die Leistungsfähigkeit von Bauteilen wie Kondensatoren und Leiterplatten zu verbessern.
Eigenschaften eines Dielektrikums
Elektrische Isolation: Die Hauptfunktion eines Dielektrikums ist die elektrische Isolation. Es verhindert das unerwünschte Übertreten von elektrischem Strom zwischen leitenden Schichten oder Bauteilen.
Dielektrische Konstante: Die Fähigkeit eines Dielektrikums, elektrische Felder zu speichern, wird durch seine dielektrische Konstante (εr) beschrieben. Ein höherer Wert der dielektrischen Konstante bedeutet, dass das Material eine größere Kapazität hat, elektrische Energie zu speichern.
Verlustfaktor: Der Verlustfaktor gibt an, wie viel Energie in Form von Wärme verloren geht, wenn das Dielektrikum einem elektrischen Feld ausgesetzt wird. Ein niedriger Verlustfaktor ist wünschenswert, um Energieverluste zu minimieren.
Durchschlagfestigkeit: Die Durchschlagfestigkeit ist die maximale Spannung, die ein Dielektrikum aushalten kann, bevor es zusammenbricht und elektrisch leitend wird.
Verwendung von Dielektrika in Leiterplatten
Isolation: In Leiterplatten (PCBs) wird das Dielektrikum verwendet, um die verschiedenen Kupferschichten (Leiterbahnen) voneinander zu isolieren. Dies verhindert Kurzschlüsse und sorgt für eine zuverlässige elektrische Trennung zwischen den verschiedenen Schaltkreisen.
Kapazität: Dielektrische Materialien in PCBs beeinflussen die Kapazität und die elektrischen Eigenschaften der Schaltungen. Die Wahl des richtigen Dielektrikums kann die Leistung der Leiterplatte, insbesondere in Hochfrequenz- und Hochgeschwindigkeitsanwendungen, verbessern.
Mechanische Stabilität: Neben der elektrischen Isolation tragen Dielektrika auch zur mechanischen Stabilität der Leiterplatte bei, indem sie die verschiedenen Schichten zusammenhalten.
Typische Dielektrika in Leiterplatten
FR-4: Ein weit verbreitetes Epoxidharz-Glasfaser-Verbundmaterial, das in den meisten Standard-PCBs verwendet wird. FR-4 bietet gute elektrische Isolierung, mechanische Festigkeit und Wärmebeständigkeit.
CEM-1 und CEM-3: Materialien, die häufig in weniger anspruchsvollen Leiterplatten verwendet werden. Sie bestehen aus Epoxidharz und Papier (CEM-1) oder Epoxidharz und Glasfaser (CEM-3).
Polyimid: Ein Hochtemperatur-Dielektrikum, das in flexiblen Leiterplatten und Hochleistungsanwendungen verwendet wird. Es bietet hervorragende elektrische Eigenschaften und Wärmebeständigkeit.
PTFE (Teflon): Ein spezielles Dielektrikum, das in Hochfrequenzanwendungen verwendet wird. PTFE hat eine niedrige dielektrische Konstante und einen niedrigen Verlustfaktor, was es ideal für Hochfrequenzschaltungen macht.
Vorteile von Dielektrika
Verhindert Kurzschlüsse: Durch die elektrische Isolierung wird das Risiko von Kurzschlüssen zwischen den Leitungen auf der Leiterplatte minimiert.
Verbessert die Leistungsfähigkeit: Die Wahl eines geeigneten Dielektrikums kann die elektrische Leistung der Leiterplatte verbessern, insbesondere in Bezug auf Signalübertragung und Rauschunterdrückung.
Erhöht die Lebensdauer: Ein gutes Dielektrikum kann zur Langlebigkeit der Leiterplatte beitragen, indem es die Auswirkungen von elektrischer Überlastung und Wärme auf die elektrischen Verbindungen reduziert.
Herausforderungen
Materialkosten: Hochleistungs-Dielektrika wie PTFE oder spezielle Polyimide können teurer sein als Standardmaterialien wie FR-4.
Verarbeitung: Einige Dielektrika erfordern besondere Verarbeitungstechniken, die zusätzliche Ausrüstung und Fachwissen erfordern können.
Fazit
Dielektrikum ist ein entscheidendes Material in der Leiterplattenherstellung und anderen elektrischen Anwendungen. Es sorgt für die notwendige elektrische Isolation, beeinflusst die Kapazität und die Leistungsfähigkeit der Schaltungen und trägt zur mechanischen Stabilität bei. Die Wahl des richtigen Dielektrikums ist entscheidend für die Zuverlässigkeit und Effizienz elektronischer Geräte und Systeme.
Vgl. auch → FR4
Die Dielektrizitätskonstante in Bezug auf Leiterplatten ist ein entscheidender Parameter, der die elektrische Leistung und das Verhalten des Materials beschreibt, aus dem die Leiterplatte besteht. Sie wird auch als relative Permittivität bezeichnet und spielt eine wesentliche Rolle bei der Bestimmung der elektrischen Eigenschaften der Leiterplatte, insbesondere ihrer Kapazität und Signalübertragung.
Definition und Bedeutung
Dielektrizitätskonstante (εr): Die Dielektrizitätskonstante eines Materials ist das Verhältnis der elektrischen Feldstärke in einem Vakuum zur elektrischen Feldstärke in diesem Material. Sie gibt an, wie gut ein Material elektrische Felder im Vergleich zu einem Vakuum durchlässt.
Relative Permittivität: Der Begriff „relative Permittivität“ beschreibt die gleiche Eigenschaft wie die Dielektrizitätskonstante. Es handelt sich um eine dimensionslose Größe, die die Fähigkeit eines Materials beschreibt, elektrische Felder zu speichern und zu isolieren.
Einfluss auf die Leiterplattenleistung
Kapazität: Die Dielektrizitätskonstante beeinflusst die Kapazität von Kondensatoren auf der Leiterplatte. Materialien mit höherer Dielektrizitätskonstante erlauben es, mehr elektrische Energie in einer gegebenen Volumeneinheit zu speichern, was bei der Herstellung von Kondensatoren und anderen Bauteilen von Bedeutung ist.
Signalgeschwindigkeit: Die Geschwindigkeit, mit der elektrische Signale durch das Dielektrikum einer Leiterplatte reisen, wird durch die Dielektrizitätskonstante beeinflusst. Ein höherer Wert der Dielektrizitätskonstante führt zu einer langsameren Signalgeschwindigkeit.
Verlustfaktor: Die Dielektrizitätskonstante beeinflusst auch den Verlustfaktor eines Materials, der die Energieverluste beschreibt, die auftreten, wenn das Material einem elektrischen Feld ausgesetzt wird. Ein niedriger Verlustfaktor ist wünschenswert, um Energieverluste zu minimieren und die Effizienz der Leiterplatte zu verbessern.
Typische Materialien und ihre Dielektrizitätskonstanten
FR-4: Das am häufigsten verwendete Basismaterial für Leiterplatten hat eine Dielektrizitätskonstante im Bereich von etwa 4,0 bis 5,0. FR-4 ist ein Epoxidharz-Glasfaser-Verbundmaterial, das in vielen Standardanwendungen verwendet wird.
CEM-1 und CEM-3: Diese Materialien haben Dielektrizitätskonstanten, die normalerweise etwas höher sind als die von FR-4, etwa im Bereich von 4,5 bis 6,0. Sie werden oft in weniger anspruchsvollen Anwendungen verwendet.
PTFE (Teflon): Ein Hochfrequenzmaterial mit einer Dielektrizitätskonstante von etwa 2,1 bis 2,2. PTFE wird für Anwendungen verwendet, bei denen geringe Verluste und hohe Frequenzen erforderlich sind.
Polyimid: Ein weiteres Dielektrikum für anspruchsvolle Anwendungen, das eine Dielektrizitätskonstante im Bereich von 3,0 bis 4,0 hat. Es wird häufig in flexiblen und Hochtemperaturanwendungen eingesetzt.
Auswirkungen auf die Leiterplattenkonstruktion
Designüberlegungen: Die Wahl des richtigen Dielektrikums mit der passenden Dielektrizitätskonstante ist entscheidend für die Leistungsfähigkeit und Zuverlässigkeit von Leiterplatten. Dies betrifft insbesondere Hochfrequenz- und Hochgeschwindigkeitsanwendungen, bei denen die Signalübertragung und -integrität von höchster Bedeutung sind.
Temperaturabhängigkeit: Die Dielektrizitätskonstante kann temperaturabhängig sein, was bei der Konstruktion von Leiterplatten berücksichtigt werden muss. Materialien, die bei verschiedenen Temperaturen stabil bleiben, sind für Anwendungen in variablen Umgebungen wichtig.
Messung und Testen
Messmethoden: Die Dielektrizitätskonstante kann durch verschiedene Tests und Messmethoden bestimmt werden, einschließlich der Kapazitätsmessung von Proben und der Messung der Dielektrizitätskonstante in einem Labor.
Normen und Standards: In vielen Fällen werden die Werte der Dielektrizitätskonstante durch Normen und Standards spezifiziert, um sicherzustellen, dass Materialien die erforderlichen elektrischen Eigenschaften für ihre Anwendungen erfüllen.
Fazit
Die Dielektrizitätskonstante ist ein grundlegender Parameter in der Leiterplattenfertigung, der die elektrischen Eigenschaften und die Leistung von Leiterplattenmaterialien bestimmt. Die Wahl des richtigen Dielektrikums mit der passenden Dielektrizitätskonstante ist entscheidend für die Effizienz, Zuverlässigkeit und Leistungsfähigkeit elektronischer Schaltungen. Materialien mit geeigneten Dielektrizitätskonstanten helfen dabei, die Anforderungen an Kapazität, Signalübertragung und Verlustminimierung in verschiedenen Anwendungen zu erfüllen.
Vgl. auch → Signalintegrität → Impedanz
Definition und Bedeutung
- Diffusionssperre: Eine Diffusionssperre ist eine Schutzschicht auf oder in einer Leiterplatte, die das Eindringen von Substanzen blockiert, die die elektrischen und mechanischen Eigenschaften der Leiterplatte negativ beeinflussen könnten. Sie wird oft verwendet, um die Haltbarkeit und Zuverlässigkeit von Leiterplatten in anspruchsvollen Umgebungen zu verbessern.
Funktionen einer Diffusionssperre
Schutz vor Feuchtigkeit: Eine Diffusionssperre verhindert das Eindringen von Feuchtigkeit in die Leiterplatte, was Korrosion und andere Feuchtigkeitsschäden verhindern kann.
Schutz vor chemischen Einflüssen: Sie schützt die Leiterplatte vor schädlichen chemischen Substanzen, die in der Umgebung vorhanden sein können und die Schaltkreise oder das Basismaterial angreifen könnten.
Vermeidung von Migrationseffekten: Eine Diffusionssperre kann helfen, die Migration von Metallen oder anderen Elementen zu verhindern, die die elektrischen Eigenschaften der Leiterplatte beeinträchtigen könnten.
Materialien und Technologien
Oxidbeschichtungen: Oft werden Oxid- oder Nitride-Schichten als Diffusionssperren verwendet. Diese Schichten sind dünn und bilden eine Barriere gegen das Eindringen von Feuchtigkeit und anderen Substanzen.
Beschichtungen: Bestimmte Beschichtungen, wie z.B. Epoxid- oder Polyimid-basierten Schichten, werden auf die Leiterplatte aufgebracht, um als Diffusionssperren zu fungieren. Diese Beschichtungen bieten sowohl Schutz als auch zusätzliche mechanische Stabilität.
Verbundmaterialien: In einigen Fällen werden spezielle Verbundmaterialien in der Leiterplattenstruktur verwendet, die von Natur aus eine diffusionsresistente Eigenschaft besitzen.
Anwendung in der Leiterplattenfertigung
Schutzbeschichtungen: Während der Herstellung von Leiterplatten können Schutzbeschichtungen aufgebracht werden, um die Leiterplatte während der weiteren Verarbeitung und Nutzung zu schützen.
Verpackung und Lagerung: In der Verpackung und Lagerung von Leiterplatten können zusätzliche Schutzmaßnahmen getroffen werden, um zu verhindern, dass Feuchtigkeit oder andere schädliche Substanzen die Leiterplatten beeinträchtigen.
Vorteile der Diffusionssperre
Erhöhte Lebensdauer: Durch den Schutz vor Umwelteinflüssen wird die Lebensdauer der Leiterplatte verlängert, da Korrosion und andere Schäden vermieden werden.
Verbesserte Zuverlässigkeit: Die Leiterplatte bleibt in anspruchsvollen Umgebungen funktionsfähig und zuverlässig, was besonders wichtig für elektronische Geräte in der Automobilindustrie, Luft- und Raumfahrt oder medizinischen Anwendungen ist.
Schutz vor Fehlfunktionen: Die Sperre hilft, Fehlfunktionen aufgrund von Umwelteinflüssen zu verhindern, die sonst zu Kurzschlüssen oder Ausfällen führen könnten.
Herausforderungen und Überlegungen
Kostenzuwachs: Die Hinzufügung von Diffusionssperren kann die Produktionskosten erhöhen, da zusätzliche Materialien und Verarbeitungsschritte erforderlich sind.
Verarbeitungskomplexität: Das Aufbringen von Diffusionssperren muss sorgfältig ausgeführt werden, um sicherzustellen, dass keine Bereiche ausgelassen werden und die Leiterplatte vollständig geschützt ist.
Kompatibilität: Die Materialien für Diffusionssperren müssen mit den übrigen Komponenten der Leiterplatte kompatibel sein, um keine unerwünschten Wechselwirkungen oder Probleme zu verursachen.
Fazit
Diffusionssperren sind eine wichtige Komponente in der Herstellung und dem Einsatz von Leiterplatten, besonders in Umgebungen, die hohe Anforderungen an Schutz und Zuverlässigkeit stellen. Sie spielen eine entscheidende Rolle beim Schutz der Leiterplatten vor Umwelteinflüssen und tragen zur langfristigen Zuverlässigkeit und Funktionalität bei. Die Wahl des geeigneten Materials und der Technologie für Diffusionssperren ist entscheidend für die Leistungsfähigkeit und Haltbarkeit der Leiterplatten in verschiedenen Anwendungen.
- DIMENSION LAYER
- DIREKTBELICHTER
- DK
- DOPPELSEITIGE LEITERPLATTE
- DRAHTBONDEN
In der Leiterplattenfertigung bezieht sich der Begriff Dimension Layer auf eine spezielle Schicht, die für die Definition und Visualisierung der physischen Abmessungen und des Layouts der Leiterplatte verwendet wird. Diese Schicht enthält wichtige Informationen, die für die Fertigung und Montage der Leiterplatte erforderlich sind.
Definition und Funktion
- Dimension Layer: Eine Dimension Layer ist eine zusätzliche Schicht in der Leiterplattendatei, die spezifische Abmessungen und Layout-Details der Leiterplatte festlegt. Diese Schicht wird verwendet, um die exakten Maße der Leiterplatte sowie die Platzierung von Bohrungen, Schnittkanten und anderen relevanten Merkmalen zu definieren.
Verwendungszwecke
Fertigung: Der Dimension Layer bietet den Fertigungsbetrieben präzise Informationen über die Größe und Form der Leiterplatte. Dies ist wichtig, um sicherzustellen, dass die Leiterplatte korrekt geschnitten und bearbeitet wird.
Montage: Bei der Montage der Leiterplatte gibt der Dimension Layer Informationen über die Platzierung von Komponenten und die Dimensionierung von Ausschnitten und Bohrungen. Dies hilft, sicherzustellen, dass alle Teile korrekt positioniert und montiert werden.
Designüberprüfung: Der Dimension Layer wird auch verwendet, um das Design der Leiterplatte zu überprüfen und sicherzustellen, dass alle Abmessungen und Layouts den Anforderungen entsprechen. Dies kann Fehler bei der Fertigung oder Montage verhindern.
Bestandteile eines Dimension Layers
Abmessungen der Leiterplatte: Die Dimension Layer zeigt die Gesamtabmessungen der Leiterplatte, einschließlich Länge, Breite und Dicke.
Bohrungen und Ausschnitte: Diese Schicht zeigt die Position und Größe von Bohrungen, Ausschnitten und anderen Bearbeitungen auf der Leiterplatte.
Schnittkanten: Der Dimension Layer definiert die Schnittkanten der Leiterplatte und zeigt an, wie die Leiterplatte aus dem Grundmaterial ausgeschnitten werden soll.
Toleranzen: In einigen Fällen enthält die Dimension Layer auch Informationen über die Toleranzen, die bei der Fertigung berücksichtigt werden müssen, um sicherzustellen, dass die Leiterplatte den spezifizierten Abmessungen entspricht.
Integration in Design-Software
EDA-Tools: In der elektronischen Design-Automation (EDA)-Software wird der Dimension Layer oft als separate Schicht definiert, die zusammen mit anderen Design-Schichten wie dem Layout, der Schaltung und den Bohrungen verwaltet wird.
Visualisierung: Der Dimension Layer wird in Design-Software visualisiert, um sicherzustellen, dass alle Maße und Layouts korrekt dargestellt werden und den Spezifikationen entsprechen.
Tipps zur Nutzung
Präzision: Achten Sie darauf, dass alle Dimensionen auf der Dimension Layer genau und präzise sind, um Fertigungsfehler zu vermeiden.
Normen und Standards: Stellen Sie sicher, dass die Dimension Layer den branchenüblichen Normen und Standards entspricht, um Komplikationen bei der Fertigung und Montage zu verhindern.
Aktualisierung: Halten Sie die Dimension Layer aktuell, insbesondere wenn Änderungen am Design vorgenommen werden, um sicherzustellen, dass alle Maße korrekt sind.
Fazit
Der Dimension Layer ist ein wesentlicher Bestandteil des Leiterplattendesigns, der die präzisen Abmessungen und Layouts definiert, die für die Fertigung und Montage der Leiterplatte erforderlich sind. Er gewährleistet, dass alle physischen Aspekte der Leiterplatte korrekt umgesetzt werden, was zu einer fehlerfreien Produktion und einer effizienten Montage führt. Die korrekte Erstellung und Verwendung der Dimension Layer ist entscheidend für die Qualität und Genauigkeit der finalen Leiterplatte.
Ein Direktbelichter ist ein Gerät, das in der Leiterplattenfertigung verwendet wird, um direkt auf das Leiterplattenmaterial zu belichten. Dieser Prozess ist eine wesentliche Phase in der Herstellung von Leiterplatten, insbesondere beim Erstellen von Schaltkreisdesigns auf den Schichten der Leiterplatte.
Definition und Funktionsweise
Direktbelichter: Ein Direktbelichter ist eine Art Belichtungsgerät, das Licht direkt auf ein fotempfindliches Material auf der Leiterplatte projiziert. Dies geschieht ohne die Notwendigkeit von lichtempfindlichen Filmen oder Masken. Die Belichtung erfolgt direkt auf dem Leiterplattenmaterial, was die Prozessschritte vereinfacht und oft die Präzision und Effizienz erhöht.
Belichtungsprozess: Der Direktbelichter projiziert Licht durch eine digitale Vorlage oder ein Layout, das auf einem Computer erstellt wurde, direkt auf das photoreaktive Material der Leiterplatte. Die Belichtung bewirkt, dass bestimmte Bereiche des Materials chemisch verändert werden, wodurch die gewünschten Schaltungen und Muster auf der Leiterplatte abgebildet werden.
Vorteile des Direktbelichters
Höhere Präzision: Durch den direkten Belichtungsprozess werden sehr präzise Muster und feine Details auf der Leiterplatte erzeugt. Dies ist besonders wichtig für hochkomplexe und hochdichte Leiterplattenlayouts.
Reduzierte Fehleranfälligkeit: Der Verzicht auf Filme und Masken reduziert die Fehlerquellen, die bei traditionellen Belichtungsmethoden auftreten können, wie z.B. Unschärfen oder Verzug.
Effizienzsteigerung: Der Direktbelichter kann den Belichtungsprozess beschleunigen und die Produktionszeiten verkürzen, da keine Filme erstellt und bearbeitet werden müssen.
Flexibilität: Digitale Vorlagen ermöglichen schnelle Anpassungen und Änderungen des Layouts, was die Flexibilität bei der Leiterplattenproduktion erhöht.
Typen von Direktbelichtern
Laser-Direktbelichter: Verwendet Laserstrahlen, um das Licht präzise auf das photoreaktive Material zu projizieren. Diese Art von Direktbelichter ist besonders für sehr feine und detaillierte Muster geeignet.
LED-Direktbelichter: Nutzt LED-Technologie zur Belichtung des Materials. LEDs bieten eine lange Lebensdauer und konstante Lichtintensität, was zu stabilen und wiederholbaren Belichtungsprozessen führt.
Anwendungsgebiete
Prototypenbau: Direktbelichter werden häufig für die Herstellung von Prototypenleiterplatten verwendet, da sie eine schnelle und präzise Belichtung ermöglichen.
Kleinserienfertigung: Auch bei der Herstellung von Kleinserien können Direktbelichter von Vorteil sein, um die Effizienz zu steigern und die Kosten zu senken.
Hochpräzise Leiterplatten: In Bereichen wie der Hochfrequenztechnik, der Medizintechnik und der Raumfahrt werden Direktbelichter eingesetzt, um Leiterplatten mit sehr hohen Anforderungen an Präzision und Detailgenauigkeit herzustellen.
Integration in den Fertigungsprozess
Design-Software: Der Direktbelichter wird typischerweise in Kombination mit moderner Design-Software verwendet, die digitale Layouts erstellt, die dann direkt auf die Leiterplatte belichtet werden.
Kalibrierung und Wartung: Eine regelmäßige Kalibrierung und Wartung des Direktbelichters sind erforderlich, um sicherzustellen, dass die Belichtungsqualität konstant hoch bleibt.
Fazit
Der Direktbelichter ist eine fortschrittliche Technologie in der Leiterplattenfertigung, die die Belichtung von Leiterplattenmaterialien direkt und präzise ermöglicht. Er bietet zahlreiche Vorteile, darunter höhere Präzision, reduzierte Fehleranfälligkeit und Effizienzsteigerung. Die Verwendung von Direktbelichtern ist besonders vorteilhaft für die Herstellung komplexer und hochpräziser Leiterplatten und hat sich in der modernen Leiterplattenproduktion als unverzichtbares Werkzeug etabliert.
Vgl. auch → LDI
Steht für Durchkontaktierung
Vgl. auch → Durchkontaktierung
Eine doppelseitige Leiterplatte (auch als Double-Sided PCB bezeichnet) ist eine Art von Leiterplatte, die auf beiden Seiten mit Kupferbahnen ausgestattet ist. Diese Bauform ermöglicht eine höhere Dichte an Schaltkreisen und Verbindungen als einseitige Leiterplatten und wird häufig in einer Vielzahl von elektronischen Geräten eingesetzt.
Definition und Struktur
Doppelseitige Leiterplatte: Eine doppelseitige Leiterplatte hat auf beiden Seiten der Platine Leiterbahnen, die über eine Reihe von Durchkontaktierungen (Vias) miteinander verbunden sind. Diese Leiterbahnen sind in der Regel aus Kupfer und ermöglichen die Verbindung und Integration der elektronischen Bauteile auf der Leiterplatte.
Struktur: Eine doppelseitige Leiterplatte besteht aus einem Basismaterial, das typischerweise aus FR4 (ein Glasfaserverbundstoff) besteht, und ist auf beiden Seiten mit einer dünnen Schicht Kupfer versehen. Die Leiterbahnen sind entweder durch eine Ätztechnik oder durch ein anderes Verfahren, wie das Druckverfahren, aufgebracht.
Vorteile
Erhöhte Schaltungsdichte: Durch die Möglichkeit, sowohl die Vorder- als auch die Rückseite der Leiterplatte zu nutzen, können mehr Verbindungen und Schaltungen auf einer kompakteren Fläche untergebracht werden. Dies ist besonders nützlich bei komplexen oder leistungsstarken Schaltungen.
Kosteneffizienz: Im Vergleich zu mehrlagigen Leiterplatten sind doppelseitige Leiterplatten oft kostengünstiger in der Herstellung, da sie weniger Schichten und weniger komplexe Fertigungsprozesse erfordern.
Verbesserte Wärmeableitung: Die doppelseitige Konstruktion kann eine bessere Wärmeableitung bieten, da Wärme von beiden Seiten der Leiterplatte abgeführt werden kann.
Erweiterte Designflexibilität: Das Design von Schaltkreisen kann auf beiden Seiten der Leiterplatte optimiert werden, was die Flexibilität bei der Platzierung von Bauteilen und der Verbindung von Schaltungen erhöht.
Fertigungsprozess
Design: Der Designprozess umfasst das Erstellen des Schaltplans und das Layout der Leiterbahnen auf beiden Seiten der Leiterplatte. CAD-Software wird verwendet, um die Platine zu entwerfen und die Verbindungen zwischen den Schichten zu planen.
Herstellung: Die Leiterplatte wird in mehreren Schritten gefertigt:
- Laminierung: Das Basismaterial wird mit einer Kupferschicht versehen.
- Belichtung und Ätzen: Die Kupferschichten werden belichtet und die nicht benötigten Kupferbereiche werden durch Ätzen entfernt.
- Bohrung: Durchkontaktierungen (Vias) werden gebohrt, um die beiden Seiten der Platine elektrisch zu verbinden.
- Plattieren und Veredeln: Die Bohrlöcher werden mit Kupfer beschichtet und die Leiterplatte wird weiter veredelt, um Schutzschichten und Lötstoppmasken aufzubringen.
Anwendungen
Konsumelektronik: Doppelseitige Leiterplatten werden häufig in Konsumelektronik wie Computern, Fernsehern, und Haushaltsgeräten verwendet, um die Komplexität der Schaltungen zu erhöhen und Platz zu sparen.
Automobilindustrie: In der Automobilindustrie finden doppelseitige Leiterplatten Anwendung in verschiedenen Steuergeräten und Sicherheitssystemen.
Medizintechnik: In der Medizintechnik werden doppelseitige Leiterplatten für Diagnose- und Überwachungsgeräte verwendet, wo Zuverlässigkeit und Präzision entscheidend sind.
Designüberlegungen
Platzierung der Bauteile: Da beide Seiten der Leiterplatte genutzt werden, müssen die Bauteile sorgfältig platziert werden, um sicherzustellen, dass alle Verbindungen korrekt hergestellt werden und keine Interferenzen auftreten.
Durchkontaktierungen: Die Platzierung und Anzahl der Vias müssen sorgfältig geplant werden, um eine zuverlässige elektrische Verbindung zwischen den beiden Seiten der Leiterplatte zu gewährleisten.
Wärmemanagement: Bei hohem Stromverbrauch oder Wärmeentwicklung sollten geeignete Maßnahmen zur Wärmeableitung eingeplant werden, um Überhitzung zu vermeiden.
Fazit
Eine doppelseitige Leiterplatte ist eine vielseitige und kosteneffiziente Lösung für viele elektronische Anwendungen. Sie ermöglicht eine höhere Dichte an Schaltungen, bietet Flexibilität im Design und verbessert die Wärmeableitung. Durch den Einsatz beider Seiten der Leiterplatte können komplexe und leistungsstarke elektronische Geräte effizient realisiert werden.
Vgl. auch → Zweiseitige Leiterplatte
Drahtbonden ist ein Verfahren zur Verbindung von Halbleiterchips mit einer Leiterplatte oder einem anderen Trägermaterial durch feine Drähte. Diese Technik wird häufig in der Elektronikfertigung verwendet, um die elektrischen Verbindungen zwischen den Chips und der Leiterplatte herzustellen. Drahtbonden ist besonders wichtig in der Herstellung von integrierten Schaltungen und Bauelementen.
Definition und Zweck
Drahtbonden: Drahtbonden ist der Prozess, bei dem dünne Drähte (meist aus Gold oder Silber) verwendet werden, um Verbindungen zwischen den Bondpads eines Halbleiterchips und den Leiterbahnen einer Leiterplatte oder eines anderen Substrats herzustellen. Diese Drähte werden durch einen speziellen Bonding-Prozess fixiert, der die elektrischen Verbindungen dauerhaft und zuverlässig macht.
Zweck: Der Hauptzweck des Drahtbondens besteht darin, elektrische Signale zwischen dem Halbleiterchip und der Leiterplatte zu übertragen. Diese Verbindungen sind essentiell für die Funktionalität von elektronischen Geräten wie Prozessoren, Speicherbausteinen und anderen integrierten Schaltkreisen.
Drahtbondverfahren
Es gibt mehrere Verfahren für das Drahtbonden, die je nach Anwendung und Anforderungen ausgewählt werden:
Thermokompressionsbonden: Bei diesem Verfahren wird ein feiner Draht zwischen dem Bondpad und dem Substrat platziert. Durch Wärme und Druck wird der Draht an beiden Enden verschmolzen, wodurch eine elektrische Verbindung entsteht. Dies ist häufig bei Goldbonden üblich.
Ultraschallbonden: Hierbei wird ein feiner Draht durch Ultraschallwellen und Druck an das Bondpad gebunden. Die Vibrationen des Ultraschalls erzeugen lokale Hitze, die den Draht mit dem Substrat verbindet. Dieses Verfahren wird oft für Silber- oder Aluminiumdrähte verwendet.
Kaltbonden (Wedge Bonding): Beim Kaltbonden wird der Draht durch mechanischen Druck und ohne Wärme miteinander verbunden. Dieses Verfahren wird vor allem für spezielle Anwendungen und Materialien eingesetzt.
Vorteile des Drahtbondens
Kosteneffizienz: Drahtbonden ist im Vergleich zu anderen Verbindungstechniken oft kostengünstiger und ermöglicht eine schnelle und präzise Herstellung von Verbindungen.
Flexibilität: Es ist möglich, Drahtbonden in verschiedenen Konfigurationen und mit unterschiedlichen Materialien anzuwenden, was Flexibilität bei der Entwicklung und Herstellung von Elektronikbauteilen bietet.
Zuverlässigkeit: Die Technik bietet eine hohe Zuverlässigkeit der Verbindungen, die den elektrischen und mechanischen Anforderungen der Anwendung standhalten.
Drahtmaterialien
Gold: Gold ist aufgrund seiner ausgezeichneten elektrischen Leitfähigkeit und Korrosionsbeständigkeit häufig das bevorzugte Material für Drahtbonden. Es ist jedoch teurer als andere Materialien.
Silber: Silber bietet ebenfalls gute elektrische Eigenschaften und wird oft in Anwendungen verwendet, bei denen Kosten eine größere Rolle spielen.
Aluminium: Aluminium ist ein weiteres Material, das beim Drahtbonden verwendet wird. Es ist kostengünstig und bietet gute Verbindungseigenschaften, insbesondere in spezifischen Anwendungen.
Anwendungen
Halbleiterindustrie: Drahtbonden wird weitreichend in der Halbleiterindustrie verwendet, um Chips mit Leiterplatten oder Gehäusen zu verbinden. Dies ist eine kritische Technik bei der Herstellung von Mikroprozessoren, Speicherchips und anderen integrierten Schaltkreisen.
Elektronikfertigung: In der Elektronikfertigung wird Drahtbonden auch für die Herstellung von Bauelementen wie Sensoren, LEDs und Kommunikationsmodulen eingesetzt.
Designüberlegungen
Drahtdurchmesser und -länge: Die Größe und Länge der Drähte müssen sorgfältig ausgewählt werden, um eine zuverlässige elektrische Verbindung zu gewährleisten und Signalverluste oder Interferenzen zu minimieren.
Bondpads: Die Größe und Platzierung der Bondpads auf dem Chip und dem Substrat sind entscheidend für den Erfolg des Bondvorgangs. Sie müssen präzise ausgelegt sein, um eine effektive Verbindung zu ermöglichen.
Prozesskontrolle: Der Drahtbondprozess muss sorgfältig überwacht werden, um sicherzustellen, dass die Verbindungen von hoher Qualität sind und den gewünschten elektrischen und mechanischen Anforderungen entsprechen.
Fazit
Drahtbonden ist eine zentrale Technik in der Elektronikfertigung, die es ermöglicht, feine und zuverlässige elektrische Verbindungen zwischen Halbleiterchips und Leiterplatten herzustellen. Durch verschiedene Bondverfahren und Materialien kann der Prozess an spezifische Anforderungen und Anwendungen angepasst werden. Drahtbonden bietet eine kosteneffiziente, flexible und zuverlässige Lösung für die Verbindung von elektronischen Bauteilen und ist entscheidend für die Herstellung moderner Elektronikprodukte.
- DRILL
- DURCHKONTAKTIERUNG
- DURCHSTEIGER
Definition und Zweck
Drill (Bohrung): Ein Drill in der Leiterplattenherstellung bezeichnet das Bohren von Löchern in der Platine. Diese Löcher können unterschiedliche Durchmesser haben und sind für die Platzierung von Bauteilen oder für elektrische Verbindungen zwischen den Schichten der Leiterplatte vorgesehen.
Zweck: Die Bohrungen erfüllen mehrere Funktionen:
- Durchkontaktierungen (Vias): Sie verbinden verschiedene Schichten innerhalb einer mehrlagigen Leiterplatte.
- Bauteilbefestigung: Sie ermöglichen das Einsetzen von Durchsteckbauteilen und deren Befestigung.
- Luftlöcher: Sie dienen der Gewichtsreduzierung und der Verbesserung der Wärmeableitung.
Bohrverfahren
Es gibt verschiedene Verfahren, um Bohrungen in Leiterplatten herzustellen:
Mechanisches Bohren: Dies ist die traditionelle Methode, bei der Präzisionsbohrer verwendet werden, um Löcher in die Leiterplatte zu bohren. Diese Methode ist geeignet für die meisten Leiterplattenanwendungen und bietet hohe Genauigkeit.
Laserbohren: Bei dieser Methode wird ein Laser verwendet, um Löcher in die Leiterplatte zu schneiden. Laserbohren wird oft bei hochpräzisen Anwendungen und für sehr kleine Durchmesser verwendet. Es bietet eine hohe Flexibilität und kann auf Materialien angewendet werden, die schwer zu bearbeiten sind.
Mikrobohren: Dies ist ein spezialisierter Prozess, der für sehr kleine Durchmesser erforderlich ist. Mikrobohren wird verwendet, um feine und präzise Löcher zu erstellen, die für moderne Elektronikbauteile erforderlich sind.
Bohrlocharten
Durchkontaktierungen (Vias): Diese Löcher verbinden die verschiedenen Schichten einer mehrlagigen Leiterplatte. Sie können je nach Art der Leiterplatte in Blind-, Buried- oder Through-Hole-Vias unterteilt werden.
Positionslöcher: Diese Löcher sind für die Platzierung und Befestigung von Bauteilen auf der Leiterplatte vorgesehen. Sie dienen als mechanische Befestigungspunkte für Komponenten wie Durchsteckbauteile.
Luftlöcher (Teardrops): Diese Löcher sind dafür vorgesehen, das Gewicht der Leiterplatte zu reduzieren oder die Wärmeableitung zu verbessern, ohne die strukturelle Integrität der Platine zu beeinträchtigen.
Designüberlegungen
Bohrdurchmesser und -platzierung: Die Größe und Position der Bohrungen müssen präzise geplant werden, um sicherzustellen, dass sie den funktionalen Anforderungen entsprechen und keine Signalstörungen oder mechanische Probleme verursachen.
Toleranzen: Die Bohrungen müssen innerhalb enger Toleranzen gefertigt werden, um sicherzustellen, dass die Bauteile korrekt passen und alle elektrischen Verbindungen zuverlässig hergestellt werden.
Materialien: Verschiedene Materialien der Leiterplatte erfordern unterschiedliche Bohrmethoden und -techniken. Die Wahl des richtigen Materials und der richtigen Bohrtechnik ist entscheidend für die Qualität und Leistung der Leiterplatte.
Fertigungsprozess
Bohrvorbereitung: Vor dem Bohren werden die Leiterplatte und die Bohrdaten vorbereitet. Die Bohrdaten können aus dem Designlayout der Leiterplatte abgeleitet werden.
Bohrung: Die Bohrungen werden durch die gewählte Methode (mechanisch, Laser, Mikrobohren) in die Leiterplatte eingebracht.
Veredlung: Nach dem Bohren werden die Bohrlöcher oft mit einer leitfähigen Schicht (z.B. Kupfer) versehen, insbesondere bei Durchkontaktierungen, um die elektrischen Verbindungen zu gewährleisten.
Inspektion: Die Bohrlöcher werden auf ihre Genauigkeit und Qualität überprüft, um sicherzustellen, dass sie den Spezifikationen entsprechen.
Anwendungen
Leiterplattenherstellung: Bohrungen sind ein grundlegender Schritt in der Herstellung von Leiterplatten und werden in allen Arten von Leiterplatten eingesetzt, von einfachen einseitigen Platinen bis hin zu komplexen mehrlagigen Designs.
Elektronikmontage: Bohrungen sind entscheidend für die Montage und Befestigung von elektronischen Bauteilen und für die Integration von Schaltkreisen in elektronischen Geräten.
Fazit
Drill in der Leiterplattenfertigung ist ein wesentlicher Prozess, der die Erstellung von Bohrungen für verschiedene Zwecke ermöglicht. Die Wahl der Bohrtechnik, die Präzision bei der Durchführung und die sorgfältige Planung sind entscheidend, um eine hohe Qualität und Funktionalität der Leiterplatte sicherzustellen. Von der einfachen Positionierung von Bauteilen bis hin zur komplexen Durchkontaktierung in mehrlagigen Platinen – der Bohrprozess spielt eine zentrale Rolle in der Elektronikfertigung.
Vgl. auch → Bohrung → Durchkontaktierung → PCB
Durchkontaktierung (auch als Via bezeichnet) ist ein wesentliches Konzept in der Leiterplattenfertigung, das die Verbindung zwischen verschiedenen Schichten einer mehrlagigen Leiterplatte ermöglicht. Diese Technik ist entscheidend für die Funktionalität und Integrität elektronischer Schaltungen, da sie es erlaubt, elektrische Signale und Strom über verschiedene Schichten hinweg zu leiten.
Definition und Zweck
Durchkontaktierung (Via): Ein Via ist ein leitender Bohrloch in einer Leiterplatte, das Schaltungen und elektrische Verbindungen zwischen verschiedenen Schichten der Leiterplatte herstellt. Diese Bohrungen sind mit einem leitenden Material, üblicherweise Kupfer, beschichtet, um elektrische Verbindungen zu ermöglichen.
Zweck: Durchkontaktierungen sind notwendig, um komplexe Leiterplattendesigns zu realisieren, bei denen viele Schichten und eine Vielzahl von Verbindungen erforderlich sind. Sie ermöglichen die Integration von Verbindungen zwischen unterschiedlichen Schaltkreisen und Komponenten, die auf verschiedenen Schichten der Leiterplatte platziert sind.
Typen von Durchkontaktierungen
Blind Vias: Diese Vias verbinden nur eine äußere Schicht mit einer oder mehreren inneren Schichten. Sie sind von der Oberfläche der Leiterplatte aus nicht sichtbar, da sie nicht bis zur gegenüberliegenden Seite durchgehen.
Buried Vias: Diese Vias verbinden nur interne Schichten und sind von der Leiterplattensoberfläche nicht sichtbar. Sie sind zwischen den Schichten versteckt und dienen dazu, Schaltungen innerhalb der Leiterplatte zu verbinden.
Through-Hole Vias: Diese Vias durchdringen die gesamte Leiterplatte und verbinden alle Schichten von der Oberseite zur Unterseite der Leiterplatte. Sie sind die am häufigsten verwendeten Durchkontaktierungen und können sowohl für elektrische Verbindungen als auch für mechanische Befestigungen genutzt werden.
Fertigungsprozesse für Durchkontaktierungen
Bohren: Zunächst wird ein Loch in die Leiterplatte gebohrt, das die spätere Durchkontaktierung aufnimmt. Dies geschieht mithilfe von Präzisionsbohrmaschinen.
Beschichtung: Nach dem Bohren wird das Loch mit einer leitfähigen Schicht, in der Regel Kupfer, beschichtet. Dies erfolgt häufig durch Galvanisierung, bei der Kupfer in das Loch elektrophoretisch abgeschieden wird.
Löten: In einigen Fällen wird das Via zusätzlich mit Lot gefüllt, um die elektrische Verbindung zu verbessern und eine stabile Verbindung zu gewährleisten.
Verkappung: Bei der Herstellung von Blind- und Buried-Vias werden die Bohrungen nach der Beschichtung oft mit einer Schutzschicht verkappt, um sie vor Umwelteinflüssen zu schützen.
Designüberlegungen
Größe und Platzierung: Die Größe der Vias und deren Platzierung auf der Leiterplatte müssen sorgfältig geplant werden, um sicherzustellen, dass sie die elektrischen und mechanischen Anforderungen erfüllen, ohne das Layout der Leiterplatte zu beeinträchtigen.
Stapelung: In mehrlagigen Leiterplatten können Vias gestapelt werden, um Verbindungen zwischen verschiedenen Schichten herzustellen. Die Stapelung muss jedoch so gestaltet sein, dass sie keine Signalstörungen oder elektromagnetische Interferenzen verursacht.
Kapazität und Widerstand: Die Größe und das Design der Vias beeinflussen ihre elektrische Leistung, einschließlich der Kapazität und des Widerstands. Größere Vias bieten in der Regel einen geringeren Widerstand, können jedoch den Platzbedarf erhöhen.
Anwendungen
Komplexe Schaltungen: Durchkontaktierungen sind besonders wichtig in komplexen Leiterplatten, die viele Schichten erfordern, wie sie in Computern, Mobiltelefonen und anderen hochentwickelten elektronischen Geräten verwendet werden.
Signal- und Stromverbindungen: Sie ermöglichen sowohl die Übertragung von Signalen als auch die Verteilung von Strom durch die verschiedenen Schichten der Leiterplatte.
Fazit
Durchkontaktierungen sind ein unverzichtbares Element in der Leiterplattenfertigung, das die Verbindung und Integration von verschiedenen Schichten ermöglicht. Durch sorgfältige Planung und präzise Ausführung tragen Vias zur Funktionalität, Zuverlässigkeit und Komplexität moderner Leiterplatten bei. Sie sind entscheidend für die Entwicklung und Herstellung fortschrittlicher elektronischer Geräte und Schaltungen.
Vgl. auch → Via → PTH → NPTH
Durchsteiger ist ein Begriff aus der Leiterplattenfertigung, der sich auf spezielle Löcher oder Bohrungen in Leiterplatten bezieht, die die elektrische Verbindung zwischen verschiedenen Schichten oder zwischen der Leiterplatte und externen Bauteilen ermöglichen. In der Regel werden Durchsteiger (englisch „Through-Hole“) verwendet, um elektronische Komponenten sicher auf der Leiterplatte zu befestigen und elektrische Verbindungen zwischen den Schichten herzustellen.
Definition und Zweck
Durchsteiger (Through-Hole): Durchsteiger sind Bohrungen in einer Leiterplatte, die von einer Seite der Platine zur anderen durchgehen. Sie ermöglichen es, dass Bauteile durch die Platine hindurch gesteckt werden, und sind ein wesentlicher Bestandteil bei der Montage von Komponenten und der Schaltung von elektrischen Verbindungen.
Zweck: Die Hauptfunktionen von Durchsteigern sind:
- Befestigung von Bauteilen: Durchsteiger ermöglichen die mechanische Befestigung von Durchsteckbauteilen wie Widerständen, Kondensatoren und integrierten Schaltkreisen (ICs).
- Verbindung von Schichten: In mehrlagigen Leiterplatten verbinden Durchsteiger die verschiedenen Schichten der Platine elektrisch miteinander.
Arten von Durchsteigern
Standard Durchsteiger: Diese Durchsteiger haben einen definierten Durchmesser und werden verwendet, um die meisten Standardbauteile zu montieren und Verbindungen zu ermöglichen.
Verzinnte Durchsteiger: Um die Lötbarkeit und Korrosionsbeständigkeit zu verbessern, können Durchsteiger mit einer dünnen Schicht Zinn überzogen werden.
Veredelte Durchsteiger: Bei dieser Art von Durchsteigern wird die Bohrung zusätzlich mit einer Kupferschicht versehen, um die elektrische Leitfähigkeit zu verbessern und eine gute Lötverbindung zu gewährleisten.
Herstellungsprozess
Bohrung: Die Durchsteiger werden in der Leiterplatte durch mechanisches Bohren, Lasern oder Mikrobohren erstellt, abhängig von der Größe und dem Material der Leiterplatte.
Veredlung: Nach dem Bohren werden die Bohrungen oft mit einer leitfähigen Schicht versehen. Diese Schicht kann Kupfer sein, das auf die Wände der Bohrung aufgebracht wird, um eine elektrische Verbindung herzustellen.
Verzinnung: Die Oberfläche der Durchsteiger wird oft mit einer Lötstopplackschicht und/oder einer Verzinnung versehen, um das Lötverfahren zu erleichtern und die Bauteile zu schützen.
Designüberlegungen
Durchmesser und Position: Der Durchmesser und die Position der Durchsteiger müssen präzise geplant werden, um sicherzustellen, dass die Bauteile korrekt passen und die elektrischen Verbindungen ordnungsgemäß hergestellt werden.
Toleranzen: Die Toleranzen für Durchsteiger müssen eng eingehalten werden, um eine hohe Qualität der Verbindungen und eine zuverlässige Montage der Bauteile zu gewährleisten.
Mechanische Belastung: Durchsteiger müssen so ausgelegt werden, dass sie den mechanischen Belastungen standhalten, die durch das Einstecken und Löten der Bauteile entstehen.
Anwendungen
Elektronikmontage: Durchsteiger sind weit verbreitet in der Elektronikmontage, insbesondere bei der Herstellung von Leiterplatten für Konsumgüter, Computer, Kommunikationsgeräte und andere elektronische Geräte.
Reparatur und Wartung: In der Reparatur und Wartung von elektronischen Geräten werden Durchsteiger oft verwendet, da sie eine einfache Möglichkeit bieten, Komponenten auszutauschen oder zu reparieren.
Vorteile und Nachteile
Vorteile:
- Robuste Verbindung: Durchsteiger bieten eine mechanisch stabile und elektrische Verbindung, die besonders bei der Montage von Durchsteckbauteilen wichtig ist.
- Einfache Fertigung: Der Prozess des Durchsteckens und Lötens von Bauteilen ist relativ einfach und gut etabliert.
Nachteile:
- Platzbedarf: Durchsteiger nehmen zusätzlichen Platz auf der Leiterplatte ein und können die Anzahl der verfügbaren Schaltkreise verringern.
- Baugröße: Die Montage von Bauteilen durch Durchsteiger kann die Baugröße der Leiterplatte erhöhen, was bei kompakten Designs ein Nachteil sein kann.
Fazit
Durchsteiger sind ein unverzichtbarer Bestandteil der Leiterplattenfertigung, der es ermöglicht, elektronische Bauteile sicher zu befestigen und elektrische Verbindungen zwischen den Schichten der Leiterplatte herzustellen. Sie bieten eine zuverlässige und bewährte Methode für die Montage und Verbindung von Bauteilen, sind jedoch in bestimmten Anwendungen, insbesondere bei der Miniaturisierung und hohen Dichte von Leiterplatten, möglicherweise weniger vorteilhaft als andere Technologien.
Vgl. auch → Durchkontaktierung
- E-TEST
- EAGLE
- EINPRESSTECHNIK
- EINRICHTKOSTEN
- EINRICHTUNG
Der Adaptertest hingegen ist aufwändiger, da er einen speziell angepassten Nadeladapter benötigt, der exakt auf die jeweilige Leiterplatte abgestimmt ist. Dieser Test ermöglicht es, alle Verbindungen der Leiterplatte gleichzeitig zu prüfen, was die Testdauer im Vergleich zum Flying Probe erheblich verkürzt. Die getesteten Leiterplatten werden anhand einer Netzliste, die aus den Konstruktionsdaten abgeleitet wird, auf Kurzschlüsse und Unterbrechungen überprüft.
Es ist jedoch zu beachten, dass ein elektrischer Test allein keine hundertprozentige Sicherheit bietet. Daher ist eine ergänzende optische Kontrolle erforderlich. Leiterplatten, die während des Tests als fehlerhaft identifiziert werden, werden aussortiert oder im Nutzen besonders markiert.
Vgl. auch → Fingertester → Adaptertest → Netzliste → optische Kontrolle
Autodesk EAGLE ist eine weit verbreitete Software für das Design von Leiterplatten und wird oft aufgrund der verfügbaren kostenlosen Basisversion genutzt.
Die Dateiendung für Board-Dateien lautet .brd, während Schaltpläne (Schematics) unter der Endung .sch gespeichert werden.
Ab 2026 wird Autodesk den Support für EAGLE einstellen, da die Funktionen in Autodesk Fusion 360 integriert werden.
Vgl. auch → Schaltplan → Schematic
Einpresstechnik ist ein Verfahren zur lötfreien Verbindung von Bauteilen auf Leiterplatten. Diese Technik wird oft verwendet, um elektronische Komponenten sicher und zuverlässig zu fixieren, ohne dass Löten erforderlich ist. Hier sind die wesentlichen Aspekte der Einpresstechnik:
Grundprinzip:
- Mechanische Verbindung:
- Einpressstifte: Bei der Einpresstechnik werden spezielle Stifte oder Pins in die Durchkontaktierungen (Vias) der Leiterplatte gepresst. Diese Stifte haben typischerweise eine feste, meist zylindrische Form und sind so dimensioniert, dass sie in die gebohrten Löcher der Leiterplatte passen.
- Pressvorgang: Der Pressvorgang wird durch Maschinen durchgeführt, die die Stifte mit einer kontrollierten Kraft in die Leiterplatte einpressen. Dies sorgt für einen festen Kontakt zwischen den Stiften und den Leiterbahnen der Leiterplatte.
Arten der Einpresstechnik:
Massive Einpresstechnik:
- Stifte: Hier werden starre, massive Stifte verwendet, die in die Leiterplatte gepresst werden. Diese Stifte deformieren das Kupfer im Bereich der Bohrung und sorgen für einen festen mechanischen und elektrischen Kontakt.
- Vorteile: Bietet eine robuste Verbindung und hohe mechanische Stabilität.
- Anwendung: Häufig in Anwendungen, bei denen eine hohe Festigkeit erforderlich ist.
Flexible Einpresstechnik:
- Stifte: Hier kommen flexible oder elastische Stifte zum Einsatz, die sich im Bereich der Einpresszone zusammenpressen lassen.
- Vorteile: Bietet eine gewisse Flexibilität und kann bei unterschiedlichen Materialien und Bohrungsgrößen verwendet werden.
- Anwendung: Oft verwendet, wenn eine gewisse Anpassungsfähigkeit an unterschiedliche Leiterplattenmaterialien erforderlich ist.
Vorteile der Einpresstechnik:
Kein Löten erforderlich:
- Keine thermische Belastung: Da keine Lötprozesse notwendig sind, wird die Leiterplatte nicht thermisch belastet, was besonders vorteilhaft für temperaturempfindliche Bauteile ist.
- Keine Gefahr von Lötbrücken: Es besteht keine Gefahr von Lötbrücken, die zu Kurzschlüssen führen könnten.
Reparierbarkeit:
- Einfaches Entfernen: Bauteile, die mit Einpresstechnik befestigt sind, können mechanisch aus der Leiterplatte entfernt und ersetzt werden, was Wartungs- und Reparaturarbeiten erleichtert.
Hohe Zuverlässigkeit:
- Langlebigkeit: Die mechanische Verbindung kann eine hohe Zuverlässigkeit und Stabilität bieten, besonders in Umgebungen mit mechanischen Belastungen.
Nachteile der Einpresstechnik:
Toleranzen:
- Genauigkeit erforderlich: Es müssen enge Toleranzen bei den Bohrungsdurchmessern eingehalten werden, um eine ordnungsgemäße Passform der Stifte zu gewährleisten.
Platzierung von SMD-Bauteilen:
- Begrenzter Platz: Im Bereich der Einpresstelle können oft keine SMD-Bauteile platziert werden, was das Layout der Leiterplatte beeinflussen kann.
Materialauswahl:
- Legierungen: Einige Einpressstifte enthalten Legierungen, die unter den RoHS-Richtlinien als kritisch betrachtet werden können. Daher muss auf die Auswahl der Materialien geachtet werden.
Normen und Standards:
- DIN EN IEC 60352-5: Diese Norm behandelt lötfreie Einpressverbindungen und beschreibt die Anforderungen und Prüfmethoden für solche Verbindungen in Elektro- und Elektronikgeräten.
Anwendung:
- Elektronikfertigung: Die Einpresstechnik wird oft in der Elektronikfertigung verwendet, insbesondere bei der Montage von Verbindungselementen oder Steckverbindern auf Leiterplatten.
- Kleinserien und Prototypen: Häufig eingesetzt in Kleinserien oder Prototypen, wo Flexibilität und einfache Anpassungen wichtig sind.
Zusammengefasst ist die Einpresstechnik ein Verfahren zur Herstellung mechanischer und elektrischer Verbindungen auf Leiterplatten ohne Lötprozess. Sie bietet Vorteile in Bezug auf die Zuverlässigkeit und Reparierbarkeit, bringt jedoch auch Herausforderungen bezüglich Toleranzen und Platzierung mit sich.
Vgl. auch → Durchkontaktierung
Einrichtkosten, auch als Rüstkosten bekannt, entstehen bei der Vorbereitung von Maschinen für den Produktionsprozess. Dazu gehören beispielsweise die Herstellung notwendiger Werkzeuge wie E-Test-Adapter oder Stanzwerkzeuge, die Anfertigung von Filmen sowie die Erstellung von Programmen.
Je kleiner die bestellte Stückzahl an Leiterplatten ist, desto stärker fallen diese Einrichtkosten ins Gewicht. Bei Prototypen können sie einen erheblichen Anteil der Gesamtkosten ausmachen, während sie bei Großserien oft kaum ins Gewicht fallen. Einige Leiterplattenhersteller weisen die Einrichtkosten separat aus, während andere, insbesondere bei Prototypen, diese in den Stückpreis integrieren.
Durch das POOL-Prinzip im PCB-POOL® von Beta LAYOUT werden die Einrichtkosten auf alle Aufträge verteilt und entfallen somit.
Vgl. auch → Einrichtung → Rüstkosten
Die Einrichtung umfasst die Vorbereitungen, die vor dem eigentlichen Produktionsbeginn einer Leiterplatte erforderlich sind. Dabei müssen Maschinen so eingerichtet werden, dass entsprechende Kosten entstehen. Beispielsweise müssen Bohr- und Fräsdaten eingelesen und Programme für den E-Test geladen werden.
Auch das Auswählen der richtigen Materialien, das präzise Einstellen von Maschinenzeiten und -parametern sowie weitere Schritte im Produktionsprozess der Leiterplatte gehören dazu.
Diese Einrichtungskosten entsprechen weitgehend den sogenannten Rüstkosten.
Vgl. auch → Rüstkosten
- EINSEITIGE LEITERPLATTE
- ENDKUPFER
- ENDOBERFLÄCHE
- ENIG
- ENTFLECHTUNG
Eine einseitige Leiterplatte, auch als Single-Sided PCB bekannt, ist eine der grundlegendsten und am weitesten verbreiteten Arten von Leiterplatten. Sie besteht aus einer einzigen Schicht leitfähigem Material, typischerweise Kupfer, das auf einer einzigen Seite eines isolierenden Substrats aufgebracht ist.
Merkmale und Eigenschaften:
Aufbau:
- Leitfähige Schicht: Die elektrische Schicht (meist Kupfer) befindet sich auf nur einer Seite des Substrats.
- Substrat: Das Substrat ist meist ein nichtleitendes Material wie FR4 (Glasfaserverstärktes Epoxidharz) oder andere Kunststoffmaterialien.
Design:
- Einfache Verdrahtung: Aufgrund der einseitigen Struktur ist das Design relativ einfach. Alle Verbindungen und Komponenten müssen auf der einzigen Seite der Leiterplatte platziert werden.
- Begrenzte Komplexität: Einseitige Leiterplatten sind ideal für einfache Schaltungen oder Anwendungen mit geringer Komplexität. Sie sind weniger geeignet für komplexe oder hochdichte Schaltungen, die mehrere Schichten erfordern.
Herstellung:
- Kostengünstig: Die Herstellung von einseitigen Leiterplatten ist kostengünstiger als bei mehrschichtigen oder doppelseitigen Leiterplatten, da weniger Fertigungsschritte erforderlich sind.
- Einfachheit: Der Produktionsprozess ist weniger komplex, was zu schnelleren Produktionszeiten führt.
Anwendungen:
- Konsumelektronik: Einseitige Leiterplatten werden häufig in Konsumelektronik wie Radios, Fernsehern und Haushaltsgeräten verwendet.
- Prototypen: Sie sind auch häufig in frühen Prototypen und einfachen Experimenten im Elektronikbereich zu finden.
- Bildung: In Ausbildungs- und Schulungsanwendungen werden sie oft verwendet, um grundlegende Prinzipien der Leiterplattenentwicklung zu lehren.
Vor- und Nachteile:
Vorteile:
- Kostengünstig: Geringere Produktionskosten aufgrund der einfacheren Fertigung.
- Einfache Konstruktion: Einfach zu designen und zu fertigen, ideal für weniger komplexe Schaltungen.
- Schnelle Prototypenerstellung: Schnelle Herstellung und einfache Handhabung bei der Prototypenerstellung.
Nachteile:
- Begrenzte Dichte: Eingeschränkte Anzahl von Bauteilen und Verbindungen, die auf einer Seite untergebracht werden können.
- Erhöhte Größe: Um alle Komponenten und Verbindungen unterzubringen, kann die Leiterplatte größer sein, was in kompakteren Designs problematisch sein kann.
- Einseitige Verbindungen: Alle Verbindungen müssen einseitig geführt werden, was die Layout-Komplexität erhöhen kann, wenn viele Verbindungen erforderlich sind.
Zusammengefasst ist eine einseitige Leiterplatte eine kosteneffektive und einfach zu fertigende Lösung für grundlegende und weniger komplexe elektronische Anwendungen. Sie bietet eine gute Basis für einfache Designs und Prototypen, ist jedoch in der Vielseitigkeit und Komplexität durch ihre einseitige Struktur begrenzt.
Vgl. auch → Lage
Diese Dicke kann entweder durch eine Verringerung des ursprünglichen Basiskupfers, etwa durch Ätzprozesse, oder durch eine Verstärkung der Kupferschicht, beispielsweise durch galvanischen Kupferaufbau, erreicht werden. Die standardisierten nominalen Endkupferdicken sind in der IPC-4562 festgelegt.
Im PCB-POOL® bieten wir starre und Alukern-Leiterplatten mit einer Endkupferdicke von 35 µm online an. Bei PCB-OVERSEAS sind 35 µm und 70 µm verfügbar, während flexible Leiterplatten eine Endkupferdicke von 22 µm aufweisen.
Vgl. auch → Kupferdicke → Ätzen
Die Endoberfläche einer Leiterplatte bezieht sich auf die letzte Bearbeitungs- oder Veredelungsschicht, die auf die Leiterplatte aufgebracht wird, nachdem das grundlegende Design und die Struktur fertiggestellt sind. Diese Oberfläche hat einen erheblichen Einfluss auf die Leistung, Haltbarkeit und Funktionalität der Leiterplatte. Es gibt verschiedene Arten von Endoberflächen, die je nach Anwendung und Anforderungen ausgewählt werden. Hier sind die wichtigsten Typen:
Typen der Endoberflächen:
Lötstoppmaske (Solder Mask):
- Funktion: Diese Schicht schützt die Kupferflächen vor Oxidation und verhindert das unerwünschte Fließen von Lötmaterial während des Bestückungsprozesses.
- Material: Wird meist aus Epoxidharz oder einem ähnlichen Material aufgebracht und ist in der Regel grün, kann aber auch in anderen Farben verfügbar sein.
- Vorteil: Reduziert die Gefahr von Lötbrücken und schützt vor mechanischen Schäden.
Oberflächenveredelungen:
- HASL (Hot Air Solder Leveling): Ein häufig verwendetes Verfahren, bei dem die Leiterplatte in geschmolzenes Lot getaucht und dann mit heißer Luft abgezogen wird, um eine gleichmäßige Lotbeschichtung zu erzeugen.
- ENIG (Electroless Nickel Immersion Gold): Eine Kombination aus einer Nickel- und einer Goldschicht, die für ausgezeichnete Lötbarkeit und Korrosionsbeständigkeit sorgt. Ideal für Anwendungen mit feinen Lötpads.
- OSP (Organic Solderability Preservative): Ein organisches Mittel, das eine Schutzschicht auf dem Kupfer hinterlässt und die Lötbarkeit bewahrt, während es gleichzeitig umweltfreundlicher ist als einige andere Methoden.
- Immersion Silver/Gold: Eine dünne Silber- oder Goldschicht wird durch ein chemisches Bad auf die Kupferflächen aufgebracht. Bietet gute Lötbarkeit und Korrosionsschutz.
Silkscreen Layer:
- Funktion: Diese Schicht enthält Drucke wie Bauteilbezeichnungen, Logos und andere wichtige Informationen für die Bestückung und Wartung.
- Material: Typischerweise auf die Leiterplatte gedruckt, meist in weiß oder schwarz.
Finale Oberflächenbehandlung:
- Verwendung: Um die Leiterplatte für den Endgebrauch zu schützen, kann eine zusätzliche Behandlung wie eine Konformalbeschichtung (z.B. Epoxid- oder Silikonbeschichtung) aufgetragen werden, um vor Feuchtigkeit, Staub und chemischen Einflüssen zu schützen.
Bedeutung der Endoberfläche:
- Verbesserte Lötbarkeit: Die Endoberfläche beeinflusst direkt die Qualität der Lötverbindungen und kann die Lebensdauer und Zuverlässigkeit der Leiterplatte erhöhen.
- Korrosionsschutz: Schutzschichten verhindern Oxidation und andere Umwelteinflüsse, die die Leistungsfähigkeit der Leiterplatte beeinträchtigen könnten.
- Mechanische Haltbarkeit: Eine robuste Endoberfläche kann die Leiterplatte vor physikalischen Schäden und Abnutzung schützen.
Auswahlkriterien:
Die Auswahl der Endoberfläche hängt von mehreren Faktoren ab, einschließlich:
- Anwendungsanforderungen: Ob die Leiterplatte in einem Hochfrequenz-, Hochstrom- oder Umgebung mit aggressiven Chemikalien verwendet wird.
- Kosten: Verschiedene Veredelungsmethoden haben unterschiedliche Kosten, die sich auf die Gesamtproduktion auswirken können.
- Kompatibilität: Sicherstellen, dass die Endoberfläche mit den vorgesehenen Lötverfahren und Bauteilen kompatibel ist.
Zusammengefasst ist die Endoberfläche einer Leiterplatte eine entscheidende Komponente, die die Funktionalität, Haltbarkeit und Qualität der fertigen Leiterplatte beeinflusst. Die Wahl der richtigen Oberflächenveredelung ist daher entscheidend für die Leistung und Zuverlässigkeit des Endprodukts.
Vgl. auch → Oberfläche
ENIG steht für „Electroless Nickel Immersion Gold“ und bezeichnet eine Oberflächenveredelungstechnologie, die häufig in der Leiterplattenherstellung verwendet wird. Bei diesem Verfahren wird zunächst eine Schicht Nickel durch einen chemischen Prozess auf die Kupferleiterbahnen aufgetragen, gefolgt von einer dünnen Goldschicht, die durch Tauchverfahren aufgebracht wird.
Wesentliche Eigenschaften von ENIG:
- Korrosionsschutz: Das Gold schützt das darunterliegende Nickel vor Oxidation und Korrosion.
- Lötbarkeit: Die Goldschicht bietet eine ausgezeichnete Lötbarkeit, was sie ideal für Oberflächenmontagetechnologien (SMT) macht.
- Planare Oberfläche: ENIG erzeugt eine sehr gleichmäßige und plane Oberfläche, die besonders bei feinen Pitch-Bauteilen vorteilhaft ist.
- Haltbarkeit: Durch die Nickel-Gold-Kombination ist die Oberfläche mechanisch stabil und langlebig.
- Kompatibilität: ENIG ist kompatibel mit verschiedenen Technologien, darunter Chip-On-Board (COB) und Flip-Chip-Verfahren.
ENIG ist eine beliebte Wahl, wenn es um zuverlässige und langlebige Oberflächen auf Leiterplatten geht, insbesondere bei Anwendungen, die hohe Präzision und Lötbarkeit erfordern.
Vgl. auch → Chemisch Gold
Prozess der Entflechtung
Schaltplan-Analyse:
- Datenübertragung: Nach der Erstellung des Schaltplans werden die Informationen in die Entflechtungsphase überführt. Der Schaltplan enthält die logischen Verbindungen zwischen den Bauteilen, jedoch nicht die physikalische Platzierung oder die Routing-Details.
Platzierung der Bauteile:
- Manuelles oder automatisches Platzieren: Die Bauteile werden auf der Leiterplatte positioniert. Dies kann manuell durch den Designer oder automatisch durch Platzierungsalgorithmen erfolgen.
Routing der Leiterbahnen:
- Verbindungen herstellen: Die physikalischen Verbindungen zwischen den Bauteilen werden erstellt. Dies umfasst das Verlegen von Leiterbahnen (oder Spuren) auf der Leiterplatte, um die Verbindungen herzustellen, die im Schaltplan definiert sind.
- Vermeidung von „Rat’s Nest“: Die Entflechtung beinhaltet auch die Vermeidung von „Rat’s Nest“-Situationen, bei denen Leiterbahnen sich überkreuzen oder ungeordnet verlaufen. Dies erfordert eine sorgfältige Planung und oft die Optimierung der Routing-Strecken.
Vermeidung von Überkreuzungen:
- Korrektur und Optimierung: Überkreuzungen und Konflikte im Leiterbahnnetzwerk müssen durch Umstrukturierung oder Umlenkung der Leiterbahnen gelöst werden. Dies kann das Verlegen von neuen Leiterbahnen oder das Anpassen der Platzierung der Bauteile umfassen.
Design-Rule-Check (DRC):
- Regelprüfung: Die Entflechtung wird durch Design-Rule-Checks überprüft, um sicherzustellen, dass alle Entwurfsregeln eingehalten werden. Dies umfasst die Überprüfung der Leiterbahnabstände, Bohrlochgrößen und anderer Designvorgaben.
Tools und Software:
- EDA-Software: Der Prozess der Entflechtung wird häufig mit Hilfe von EDA-Software (Electronic Design Automation) durchgeführt, die sowohl manuelle als auch automatische Routing-Funktionen bietet. Beispiele für solche Software sind Altium Designer, KiCad, Eagle und OrCAD.
- Autorouter: Viele EDA-Tools bieten Autorouter-Funktionen, die automatisch die besten Verbindungen zwischen Bauteilen vorschlagen und umsetzen.
Bedeutung der Entflechtung:
- Optimierung der Leistung: Durch sorgfältige Entflechtung kann die Leistung der Leiterplatte optimiert werden, indem Störungen minimiert und die Signalqualität verbessert wird.
- Vermeidung von Fehlern: Eine präzise Entflechtung hilft, mögliche Fehler zu vermeiden, die zu Kurzschlüssen oder schlechten Verbindungen führen könnten.
- Reduzierung der Produktionskosten: Ein gut durchdachtes Layout kann die Produktionskosten senken, indem es die Effizienz der Fertigung und die Anzahl der erforderlichen Nacharbeiten verbessert.
Herausforderungen und Überlegungen:
- Komplexität: Bei komplexen Schaltungen kann die Entflechtung eine erhebliche Herausforderung darstellen, insbesondere bei der Planung der Leiterbahnen und der Minimierung von Signalstörungen.
- Verpackung und Platzierung: Die physikalische Platzierung der Bauteile auf der Leiterplatte ist entscheidend für die Effektivität des Entflechtungsprozesses und muss sorgfältig geplant werden.
Zusammengefasst ist die Entflechtung ein kritischer Schritt im Leiterplattendesign, bei dem das elektrische Design in ein physikalisches Layout übersetzt wird. Sie erfordert sorgfältige Planung und die Verwendung geeigneter Werkzeuge, um ein funktionales und effizientes Leiterplattenlayout zu erstellen.
Vgl. auch → Schaltplan → Routing
- ENTGRATEN
- EPOXIDHARZ
- ESD
- EUROPAKARTE
- EXCELLON
- EXTENDED GERBER
Das Entgraten bei Leiterplatten bezieht sich auf den Prozess des Entfernens von Graten, also kleinen unerwünschten Metall- oder Materialresten, die bei der mechanischen Bearbeitung der Leiterplatte entstehen können. Diese Grate entstehen typischerweise an den Rändern der Leiterplatte, insbesondere nach dem Fräsen, Bohren oder Stanzen.
Warum ist Entgraten wichtig?
- Vermeidung von Kurzschlüssen: Scharfe Kanten oder Metallreste können Kurzschlüsse verursachen, was die Funktion der Leiterplatte beeinträchtigen könnte.
- Verbesserte mechanische Stabilität: Das Entfernen von Graten erhöht die mechanische Stabilität und verhindert potenzielle Brüche oder Risse an den Rändern der Leiterplatte.
- Erleichterung der Weiterverarbeitung: Eine gratfreie Leiterplatte lässt sich leichter und sicherer weiterverarbeiten, etwa beim Einbau in Gehäuse oder bei der Montage von Bauteilen.
- Optische und ästhetische Verbesserung: Das Entgraten sorgt für eine saubere, professionelle Optik der fertigen Leiterplatte.
Das Entgraten erfolgt in der Regel durch mechanische Methoden wie Schleifen, Bürsten oder chemische Prozesse, um eine glatte und saubere Oberfläche der Leiterplatte zu gewährleisten.
Vgl. auch → Graten
Epoxidharz ist ein vielseitiger synthetischer Werkstoff, der aus einer Mischung von Epoxidharzen und Härtern besteht. Wenn diese beiden Komponenten miteinander vermischt werden, reagieren sie chemisch und härten aus, wodurch ein festes, widerstandsfähiges Material entsteht.
Eigenschaften von Epoxidharz:
- Hohe Festigkeit: Epoxidharz ist extrem widerstandsfähig und weist eine hohe mechanische Festigkeit auf, was es ideal für strukturelle Anwendungen macht.
- Chemische Beständigkeit: Es ist resistent gegenüber vielen Chemikalien, einschließlich Säuren, Basen und Lösungsmitteln.
- Elektrische Isolierung: Epoxidharz hat ausgezeichnete dielektrische Eigenschaften, weshalb es häufig in der Elektronik als Isolationsmaterial verwendet wird.
- Wasserdichtigkeit: Es ist wasserfest und bietet Schutz gegen Feuchtigkeit, was es ideal für Beschichtungen und Versiegelungen macht.
- Haftfähigkeit: Epoxidharz haftet sehr gut auf einer Vielzahl von Oberflächen, einschließlich Metallen, Kunststoffen, Glas und Holz.
In der Elektronik wird Epoxidharz häufig als Bindemittel für Glasfasern in FR4-Leiterplatten verwendet. Es dient als Isolator und bietet mechanische Stabilität.
Vgl. auch → FR4
ESD steht für „Electrostatic Discharge“ (auf Deutsch: „elektrostatische Entladung“). Es bezeichnet den plötzlichen Stromfluss, der auftritt, wenn sich zwei Objekte, die unterschiedliche elektrische Potentiale haben, berühren oder sehr nah kommen. Diese Entladung kann erhebliche Auswirkungen auf elektronische Bauteile und Geräte haben.
Ursachen und Mechanismus:
- Ladungsaufbau: ESD entsteht häufig durch die Ansammlung von statischer Elektrizität auf einem Objekt, die durch Reibung, Trennung oder Kontakt mit anderen Materialien verursacht wird.
- Entladung: Wenn die elektrische Spannung zwischen zwei Objekten groß genug wird, um die Luft zwischen ihnen zu überwinden, kommt es zu einem plötzlichen Funken oder Stromfluss – der sogenannten elektrostatischen Entladung.
Auswirkungen auf Elektronik:
- Schäden an Bauteilen: ESD kann elektronische Bauteile beschädigen, indem es zu einem sofortigen Stromfluss führt, der die empfindlichen Schaltkreise überlastet oder zerstört.
- Beeinträchtigung der Funktion: Auch wenn ESD nicht sofort sichtbare Schäden verursacht, kann es langfristig die Funktion und Lebensdauer von Bauteilen beeinträchtigen oder zu sporadischen Fehlfunktionen führen.
- Datenverlust: In digitalen Geräten kann ESD auch zu Datenverlust oder -korruption führen.
Schutzmaßnahmen:
- ESD-Schutzkleidung: Spezielle antistatische Kleidung wie ESD-Jacken und -Hosen, die den Kontakt von statischer Elektrizität mit empfindlichen Komponenten verhindern.
- ESD-Arbeitsplätze: ESD-sichere Arbeitsflächen, Bodenbeläge und Werkbänke, die statische Elektrizität ableiten.
- Erdung: Sicherstellen, dass alle Ausrüstungen und Materialien in ESD-Zonen geerdet sind, um eine sichere Ableitung von statischer Elektrizität zu gewährleisten.
- Antistatische Verpackungen: Verwendung von antistatischen Beuteln oder Schachteln für den Transport und die Lagerung von elektronischen Bauteilen.
Anwendungen:
- Fertigung: In der Leiterplattenherstellung und -bestückung werden ESD-Schutzmaßnahmen eingesetzt, um Schäden an empfindlichen Bauteilen zu vermeiden.
- Labor: In Elektroniklabors und bei der Reparatur von Geräten sind ESD-Schutzmaßnahmen entscheidend, um die Integrität der Test- und Reparaturarbeiten zu gewährleisten.
- Transport: Elektronische Bauteile werden in antistatischen Verpackungen versendet, um sie während des Transports zu schützen.
Zusammengefasst ist ESD ein kritisches Thema in der Elektronikfertigung und -wartung, das durch geeignete Schutzmaßnahmen effektiv gemanagt werden muss, um die Funktionalität und Lebensdauer von elektronischen Komponenten zu sichern.
In Bezug auf Leiterplatten bezieht sich der Begriff „Europakarte“ auf eine spezielle Art von Leiterplatte, die typischerweise in den europäischen Standards und Normen verankert ist. Hier sind einige Details dazu:
Definition und Merkmale:
- Standardgröße: Die Europakarte ist oft nach einem Standardmaß bemessen, das in Europa üblich ist, wie zum Beispiel 100 mm x 160 mm. Diese Standardgrößen erleichtern die Produktion und den Austausch von Leiterplatten in verschiedenen Anwendungen.
- Kompatibilität: Die Europakarte entspricht typischerweise den europäischen Normen für Leiterplatten, was sicherstellt, dass sie in europäischen Geräten und Systemen problemlos verwendet werden kann.
- Verwendung: Europakarten werden häufig in verschiedenen elektronischen Geräten und industriellen Anwendungen eingesetzt. Sie bieten eine zuverlässige und standardisierte Grundlage für die Integration von Elektronikkomponenten.
- Design: Die Gestaltung von Europakarten kann je nach Anwendung variieren, beinhaltet jedoch oft standardisierte Lochraster und Layouts, die eine einfache Integration in bestehende Systeme ermöglichen.
- Normen: Die Gestaltung und Spezifikationen von Europakarten können durch europäische Normen, wie sie beispielsweise von der International Electrotechnical Commission (IEC) oder der European Committee for Electrotechnical Standardization (CENELEC) festgelegt werden, geregelt sein.
Ergänzungen:
- Flexibilität und Anpassung: Obwohl es standardisierte Größen gibt, können Europakarten auf spezifische Anforderungen angepasst werden, um besondere Funktionen oder zusätzliche Komponenten aufzunehmen.
- Technologie: Neben den Standardgrößen kann die Technologie, die in Europakarten verwendet wird, moderne Fertigungsverfahren und Materialien umfassen, wie z.B. Hochfrequenzmaterialien oder mehrlagige Konstruktionen.
Zusammengefasst ist eine Europakarte eine standardisierte Leiterplatte, die in Europa üblich ist und in der Regel den regionalen Normen und Größenstandards entspricht. Sie wird häufig in einer Vielzahl von elektronischen und industriellen Anwendungen verwendet.
Excellon ist ein weit verbreitetes Dateiformat und ein Standard in der Leiterplattenfertigung, das für die Übermittlung von Bohr- und Fräsdaten verwendet wird. Hier sind einige wesentliche Aspekte des Excellon-Formats:
Definition und Verwendungszweck:
Bohr- und Fräsdaten: Excellon-Dateien enthalten Anweisungen für das Bohren und Fräsen von Leiterplatten. Diese Anweisungen beinhalten Positionen und Dimensionen der Löcher und Konturen, die auf der Leiterplatte bearbeitet werden sollen.
Standardisierung: Excellon ist ein Industriestandard, der von vielen Leiterplattenherstellern und -entwicklern verwendet wird, um eine einheitliche Kommunikation und Verarbeitung von Bohr- und Fräsdaten zu gewährleisten.
Dateiformate:
Excellon I (auch bekannt als Excellon Standard): Dieses Format ist die ursprüngliche Version und wird für einfache Bohr- und Fräsdaten verwendet.
Excellon II: Eine erweiterte Version des Formats, die zusätzliche Funktionen und Optionen für komplexere Anwendungen bietet.
Dateistruktur:
Befehle und Koordinaten: Excellon-Dateien bestehen aus einer Reihe von Befehlen und Koordinaten, die die genaue Position und Größe der Bohrlöcher und Fräskonturen auf der Leiterplatte festlegen.
Kommentarzeilen: Oft enthalten Excellon-Dateien auch Kommentarzeilen zur Dokumentation und für zusätzliche Anweisungen.
Integration:
CAD-Systeme: Excellon-Dateien werden in der Regel aus CAD-Systemen exportiert, die das Design der Leiterplatte erstellt haben. Diese Daten werden dann in der Fertigung verwendet, um die Leiterplatten präzise zu bearbeiten.
Vorteile:
Konsistenz: Excellon sorgt für Konsistenz und Genauigkeit bei der Übermittlung von Bohr- und Fräsdaten zwischen Designern und Herstellern.
Kompatibilität: Das Format wird von einer Vielzahl von Softwaretools und Fertigungsmaschinen unterstützt, was die Integration in verschiedene Produktionsprozesse erleichtert.
Zusammenfassend ist Excellon ein kritisches Format in der Leiterplattenfertigung, das die Übermittlung von präzisen Bohr- und Fräsdaten ermöglicht und somit eine genaue und effiziente Produktion von Leiterplatten sicherstellt.
Vgl. auch → Bohrprogramm
Extended Gerber ist eine erweiterte Version des traditionellen Gerber-Formats, das in der Leiterplattenherstellung verwendet wird. Das Gerber-Format selbst ist ein weit verbreiteter Standard für die Übertragung von Layout-Daten von Leiterplatten-Designs. Extended Gerber erweitert diese Funktionalität, um zusätzliche Informationen und Anforderungen der modernen Leiterplattenproduktion zu unterstützen.
Merkmale und Vorteile von Extended Gerber:
Erweiterte Datenkompatibilität:
- Vollständige Layer-Darstellung: Extended Gerber unterstützt die Darstellung aller Schichten einer Leiterplatte, einschließlich der speziellen Layer wie Lötstoppmasken, Bestückungsdrucke und Entlüftungslöcher.
- Zusätzliche Informationen: Es ermöglicht die Integration von zusätzlichen Informationen wie Bohr- und Fräskonturen, die für die Fertigung erforderlich sind. In der Regel im Fatenformat von Excellon oder Sieb & Meyer.
Präzisere Darstellung:
- Mehr Genauigkeit: Das Format bietet eine genauere und präzisere Darstellung der Design-Daten, was zu einer besseren Reproduzierbarkeit und Qualität der Leiterplatten führt.
- Erweiterte Befehle: Es enthält erweiterte Befehle und Funktionen, die eine detailliertere Kontrolle und Anpassung des Designs ermöglichen.
Kompatibilität mit modernen Fertigungsprozessen:
- Mehrlagige Leiterplatten: Extended Gerber kann komplexe mehrlagige Leiterplattenlayouts unterstützen, einschließlich der Definition von verschiedenen Materialien und deren Eigenschaften.
- 3D-Darstellung: Einige Implementierungen von Extended Gerber unterstützen auch 3D-Darstellungen der Leiterplatte, was bei der Fehlerüberprüfung und Designverifikation hilfreich ist.
Industrie-Standards:
- IPC-Standards: Extended Gerber entspricht oft den IPC-Standards wie IPC-2581, die für die elektronische Fertigungsindustrie definiert sind. Diese Standards verbessern die Interoperabilität zwischen Design- und Fertigungssystemen.
Anwendung in der Leiterplattenherstellung:
- Design-Übermittlung: Extended Gerber wird von Designern verwendet, um detaillierte und präzise Layout-Daten an Leiterplattenhersteller zu übermitteln.
- Fertigungsprozesse: Die erweiterten Funktionen des Formats unterstützen verschiedene Fertigungsprozesse, einschließlich der Bestückung, des Ätzens und der Endbearbeitung von Leiterplatten.
Ergänzungen:
- Kompatibilität mit EDA-Software: Viele moderne EDA-Softwaretools unterstützen Extended Gerber, was die Integration in den Designprozess erleichtert.
- Fehlervermeidung: Durch die detailliertere und präzisere Datenübertragung werden häufig Fehler in der Fertigung reduziert, da alle erforderlichen Informationen klar und umfassend übermittelt werden.
Zusammenfassend bietet Extended Gerber eine verbesserte und detaillierte Darstellung der Leiterplattendesign-Daten, die den Anforderungen moderner Fertigungsprozesse besser gerecht wird und eine höhere Präzision und Qualität in der Leiterplattenproduktion ermöglicht.
Vgl. auch → Excellon → Sieb & Meyer
- FÄDELTECHNIK
- FANGLÖCHER
- FASERN
- FEEDER
Fädeltechnik ist ein älteres Verfahren zur Herstellung von elektrischen Verbindungen auf Leiterplatten oder in elektronischen Baugruppen, das vor allem in der Prototypen- und Kleinserienfertigung eingesetzt wurde. Dabei werden Drähte manuell um Kontaktstifte oder Bauelementanschlüsse gewickelt, um Verbindungen zwischen verschiedenen Bauelementen herzustellen.
Funktionsweise der Fädeltechnik
- Kontaktstifte: Bei der Fädeltechnik werden Kontaktstifte auf einer nichtleitenden Trägerplatte (wie einer Leiterplatte ohne Leiterbahnen) befestigt, und die Bauelemente werden auf dieser Basis montiert.
- Drahtfädeln: Ein dünner isolierter Draht wird um die Kontaktstifte gewickelt, um elektrische Verbindungen zwischen den verschiedenen Bauelementen herzustellen. Die Isolation des Drahtes wird an den Verbindungsstellen durch das mechanische Wickeln entfernt, sodass ein sicherer elektrischer Kontakt entsteht.
- Manuell oder maschinell: Diese Technik kann entweder manuell oder maschinell durchgeführt werden. Bei der maschinellen Variante werden spezielle Fädelautomaten verwendet, die den Draht automatisch abrollen, an den richtigen Stellen platzieren und wickeln.
Vorteile der Fädeltechnik
- Flexibilität: Besonders bei Prototypen oder kleinen Serien ist die Fädeltechnik eine sehr flexible Methode, da sie leicht Änderungen im Design ermöglicht.
- Geringe Kosten bei kleinen Stückzahlen: Da keine speziellen Leiterplatten oder Masken hergestellt werden müssen, ist die Fädeltechnik für kleine Stückzahlen kostengünstiger als das Erstellen einer gedruckten Leiterplatte.
- Dichte Bestückung: Die Fädeltechnik erlaubt eine sehr dichte Bestückung, da die Drähte in mehreren Schichten gefädelt werden können.
Nachteile der Fädeltechnik
- Aufwendig: Da die Fädeltechnik größtenteils manuell oder durch spezialisierte Maschinen durchgeführt wird, ist sie zeitaufwendig und für Massenproduktion ungeeignet.
- Fehleranfälligkeit: Bei manueller Fädelarbeit können leicht Fehler auftreten, die zu fehlerhaften Verbindungen oder Kurzschlüssen führen.
- Mechanische Stabilität: Die Verbindungen können mechanisch weniger stabil sein als auf gedruckten Leiterplatten, da die Drähte nicht fest auf einer Oberfläche verlötet sind.
Anwendungen der Fädeltechnik
Die Fädeltechnik wurde in der Vergangenheit häufig für Prototypen, Labormuster und Kleinserien verwendet. Heutzutage ist sie weitgehend von automatisierten Verfahren wie der SMT-Bestückung (Surface Mount Technology) verdrängt worden, wird aber gelegentlich noch in speziellen Anwendungsfällen eingesetzt, wo schnelle und flexible Anpassungen erforderlich sind.
Fazit
Die Fädeltechnik war eine nützliche Methode für die Herstellung von Prototypen und Kleinserien in der Elektronik, hat jedoch in der modernen Massenproduktion aufgrund der Automatisierung und Effizienz von Leiterplatten- und SMT-Technologien weitgehend an Bedeutung verloren. Sie bietet jedoch weiterhin Vorteile in speziellen Situationen, in denen Flexibilität und schnelle Designänderungen im Vordergrund stehen.
Fanglöcher (auch als „Tooling Holes“, „Fangbohrungen“oder „Ausrichtungsbohrungen“ bekannt) sind nicht durchkontaktierte Bohrungen auf einer Leiterplatte, die zur Positionierung, Ausrichtung und Fixierung der Platine während des Herstellungsprozesses verwendet werden. Sie dienen dazu, die Leiterplatte während verschiedener Produktionsschritte wie Bohren, Bestücken, und Ätzen präzise zu halten und zu positionieren.
Funktion und Anwendung von Fanglöchern
Ausrichtung: Fanglöcher werden verwendet, um sicherzustellen, dass die Leiterplatte und die darauf basierenden Schablonen oder Werkzeuge exakt positioniert sind. Das ist besonders wichtig bei mehrlagigen Leiterplatten, bei denen die verschiedenen Schichten präzise aufeinander abgestimmt sein müssen.
Fixierung: Während der Bearbeitung, zum Beispiel beim Bohren oder beim Bestücken, helfen Fanglöcher dabei, die Platine an Ort und Stelle zu halten, um Verschiebungen und Ungenauigkeiten zu vermeiden.
Verwendung in Testprozessen: Sie können auch während des elektrischen Tests (E-Test) oder der optischen Inspektion als Bezugspunkte verwendet werden, um die Platine korrekt zu positionieren.
Gestaltung der Fanglöcher
- Platzierung: Fanglöcher werden in der Regel an den Rändern der Leiterplatte oder in speziellen Bereichen platziert, wo sie nicht die elektrischen Schaltungen oder Bauteile beeinträchtigen.
- Größe und Form: Die Größe und Form der Fanglöcher kann variieren, ist aber standardisiert, um mit den Werkzeugen und Maschinen kompatibel zu sein.
Vorteile von Fanglöchern
- Präzise Produktion: Durch die Verwendung von Fanglöchern wird sichergestellt, dass die verschiedenen Fertigungsschritte der Leiterplatte genau aufeinander abgestimmt sind.
- Reduzierung von Fehlern: Sie minimieren Fehler wie Versatz oder Fehlbohrungen, die zu Funktionsproblemen führen können.
Fazit
Fanglöcher sind essenziell, um eine präzise Fertigung und Bestückung von Leiterplatten sicherzustellen. Sie gewährleisten die exakte Positionierung und Stabilität der Platine während verschiedener Produktions- und Testprozesse.
Vgl. auch → Nicht durchkontaktierte Bohrungen → NDK
Siehe → Abfasern
Ein Feeder ist eine Vorrichtung, die in automatisierten Bestückungsmaschinen für Leiterplatten verwendet wird, um elektronische Bauteile präzise und kontinuierlich zuzuführen. Die Bauteile werden dabei oft von Rollen oder Trägerbändern (Tape) in die Maschine transportiert, wo sie anschließend auf die Leiterplatte gesetzt werden.
Funktion eines Feeders
Zuführung der Bauteile: Der Feeder sorgt dafür, dass die Bauteile in einer genauen Reihenfolge und Position in die Bestückungsmaschine gelangen, damit sie auf die Leiterplatte platziert werden können.
Automatisierte Prozesse: In hochautomatisierten Produktionsprozessen kann die Bestückungsmaschine durch Feeder eine große Menge von Bauteilen mit hoher Geschwindigkeit und Genauigkeit verarbeiten, ohne dass manuell eingegriffen werden muss.
Arten von Feedern
Tape Feeder: Diese Zuführung verwendet Trägerbänder, auf denen die Bauteile in regelmäßigen Abständen befestigt sind. Das Band wird kontinuierlich vorwärts bewegt, um Bauteile für die Bestückung bereitzustellen.
Stick Feeder: Hier werden die Bauteile in Röhrchen (Sticks) angeordnet und durch mechanische oder pneumatische Mittel zur Maschine transportiert.
Tray Feeder: In diesem Fall werden die Bauteile in Tabletts (Trays) bereitgestellt und nach Bedarf entnommen.
Bulk Feeder: Diese Zuführung kommt bei Bauteilen zum Einsatz, die lose und in größeren Mengen zugeführt werden, wobei ein Sortiermechanismus die korrekte Ausrichtung der Bauteile gewährleistet.
Vorteile eines Feeders
- Hohe Präzision: Feeder stellen sicher, dass Bauteile genau an die richtige Stelle geführt werden, was für die automatisierte Bestückung entscheidend ist.
- Effizienz: Sie ermöglichen eine schnelle und kontinuierliche Bestückung von Leiterplatten ohne manuelles Eingreifen.
- Flexibilität: Moderne Bestückungsmaschinen können mit mehreren Feedern ausgestattet werden, um eine Vielzahl unterschiedlicher Bauteile auf einer Platine zu platzieren.
Fazit
Ein Feeder ist ein essenzieller Bestandteil der automatisierten Bestückung von Leiterplatten. Er sorgt dafür, dass elektronische Bauteile präzise und effizient in die Maschine geführt werden, um die Bestückung von Leiterplatten in großen Mengen zu ermöglichen.
- FEINLEITER
- FIDUCIAL
- FINEPITCH
- FINGERTESTER
Eigenschaften und Anforderungen von Feinleitern
Leiterbahnbreite: Feinleiter haben extrem schmale Leiterbahnen, typischerweise unter 100 µm (Mikrometer). Diese schmalen Bahnen ermöglichen eine sehr hohe Schaltungsdichte.
Präzise Fertigung: Aufgrund der geringen Leiterbahnbreite und des kleinen Abstands zwischen den Leiterbahnen müssen sehr präzise Fertigungstechnologien wie Laser-Direktbelichtung oder fortschrittliche Ätzverfahren verwendet werden.
Isolationsabstände: Auch der Abstand zwischen den Leiterbahnen muss äußerst genau kontrolliert werden, um Kurzschlüsse und andere elektrische Probleme zu vermeiden.
Anwendungen von Feinleitern
Feinleiter kommen vor allem in Miniatur- und Hochleistungsanwendungen zum Einsatz, darunter:
Smartphones und Tablets: In diesen Geräten sind die Platzverhältnisse extrem begrenzt, daher werden Feinleiter verwendet, um die hohe Anzahl von Schaltkreisen unterzubringen.
Mikroprozessoren und Computerchips: Um die Komplexität und Leistungsfähigkeit von Prozessoren zu steigern, müssen auf kleinem Raum viele Schaltkreise integriert werden.
Medizinische Geräte: Miniaturisierte Elektronik in der Medizintechnik, etwa bei Implantaten, nutzt Feinleiter, um empfindliche Sensoren und Schaltungen unterzubringen.
Herausforderungen bei Feinleitern
Produktionskomplexität: Die Herstellung von Feinleitern erfordert spezielle Fertigungstechnologien, die sehr präzise arbeiten und hohe Anforderungen an Material und Prozesskontrolle stellen.
Zuverlässigkeit: Feinleiter müssen besonders robust gegen mechanische Belastungen, Hitze und andere Umwelteinflüsse sein, da ihre geringen Abmessungen sie empfindlicher gegenüber äußeren Einflüssen machen können.
Fazit
Feinleiter sind unerlässlich für moderne, hochintegrierte Elektronikgeräte, die eine hohe Schaltungsdichte auf kleinem Raum erfordern. Dank fortschrittlicher Fertigungstechnologien sind sie in der Lage, die Anforderungen moderner Anwendungen zu erfüllen, obwohl sie hohe Anforderungen an die Produktionsprozesse stellen.
Fiducials sind der englische Begriff für Passermarken oder Referenzmarken. Es handelt sich um präzise Markierungen oder Referenzpunkte auf einer Leiterplatte, die zur genauen Ausrichtung und Positionierung während des Bestückungsprozesses verwendet werden. Sie spielen eine zentrale Rolle bei der Automatisierung von Bestückungsvorgängen, insbesondere bei der Platzierung von Bauteilen durch Roboter oder Maschinen.
Funktion von Fiducials
Referenzpunkte für Maschinen: Fiducials dienen als optische Orientierungshilfen für Bestückungsmaschinen. Mithilfe von Kamerasystemen erkennen die Maschinen die Fiducials und können dadurch die exakte Position der Leiterplatte bestimmen.
Ausrichtung und Kalibrierung: Sie ermöglichen die präzise Kalibrierung der Maschinen, sodass Bauteile millimetergenau auf der Leiterplatte platziert werden können, selbst wenn die Platine während des Produktionsprozesses minimal verschoben wurde.
Reduktion von Fehlern: Fiducials helfen, Fehler wie Fehlplatzierungen oder Ausrichtungsfehler zu vermeiden, indem sie als Bezugspunkte dienen, die sicherstellen, dass die Leiterplatte und die Bauteile korrekt ausgerichtet sind.
Arten von Fiducials
Global Fiducials: Diese Markierungen befinden sich auf dem gesamten Layout der Leiterplatte und dienen zur Ausrichtung der gesamten Platine.
Local Fiducials: Diese werden in der Nähe von kritischen Bereichen oder Bauteilen aufgebracht, um die präzise Platzierung einzelner Komponenten sicherzustellen, insbesondere bei komplexen oder kleinen Bauteilen wie BGAs (Ball Grid Arrays).
Gestaltung von Fiducials
- Form: Fiducials sind in der Regel kreisförmig und werden als einfacher Punkt auf dem Kupferlayer der Leiterplatte angebracht.
- Größe: Ihre Größe variiert je nach Anforderungen, aber sie sind üblicherweise deutlich genug, um von optischen Systemen erkannt zu werden.
- Platzierung: Sie sollten in Bereichen platziert werden, die frei von anderen Layout-Elementen sind, um eine klare und ungestörte Erkennung durch die Maschinen zu gewährleisten.
Bedeutung für den Bestückungsprozess
Automatisierung: In automatisierten Fertigungslinien, bei denen hohe Geschwindigkeiten und Präzision erforderlich sind, sind Fiducials unverzichtbar. Sie sorgen dafür, dass die Maschinen immer korrekt ausgerichtet sind, auch wenn die Leiterplatte sich leicht verschiebt.
Präzision bei Miniaturbauteilen: Besonders bei der Platzierung kleiner und empfindlicher Bauteile auf komplexen Leiterplatten sorgen Fiducials für die nötige Genauigkeit.
Fazit
Fiducials sind essenzielle Markierungen für die präzise Ausrichtung und Bestückung von Leiterplatten in automatisierten Produktionsprozessen. Sie reduzieren die Wahrscheinlichkeit von Fehlplatzierungen und verbessern die Effizienz und Genauigkeit der Herstellung, insbesondere bei modernen, hochdichten Leiterplatten.
Vgl. auch → Passermarken → Referenzmarkern
Finepitch bezeichnet eine spezielle Art von elektronischen SMD-Bauteilen oder Anschlüssen, bei denen die Pins oder Anschlussstellen sehr dicht beieinander liegen. Dies erfordert eine besonders präzise Fertigung und Bestückung. Der Begriff wird häufig in der Leiterplattentechnologie verwendet, insbesondere bei der Entwicklung moderner, miniaturisierter Elektronik, wie Smartphones oder Prozessoren.
Eigenschaften von Finepitch
Geringer Pin-Abstand: Finepitch-Bauteile haben sehr kleine Abstände zwischen den Pins oder Anschlüssen, oft weniger als 0,5 mm. Dies ermöglicht es, mehr Anschlüsse auf kleiner Fläche unterzubringen, was für hochintegrierte Schaltkreise notwendig ist.
Höhere Komplexität: Die dichten Pin-Abstände machen die Fertigung und Bestückung von Finepitch-Bauteilen anspruchsvoller, da Präzision im Layout und bei der Platzierung der Bauteile entscheidend ist, um Kurzschlüsse oder offene Verbindungen zu vermeiden.
Anwendungen von Finepitch
Finepitch-Technologie wird in vielen modernen, kompakten Elektronikgeräten verwendet, darunter:
Mikroprozessoren und Chips: In der Halbleiterindustrie wird Finepitch häufig bei der Verbindung von integrierten Schaltungen (ICs) eingesetzt, um die Anzahl der Pins zu maximieren und gleichzeitig die Baugröße zu reduzieren.
Mobilgeräte und Wearables: In Geräten, bei denen Platz ein begrenzter Faktor ist, wie Smartphones, Tablets und tragbaren Geräten, ermöglicht Finepitch die Integration zahlreicher Funktionen auf kleinem Raum.
BGAs (Ball Grid Arrays) und QFPs (Quad Flat Packages): Diese Verpackungstypen für ICs nutzen Finepitch-Technologie, um die Anzahl der Verbindungen auf der Platine zu erhöhen, ohne die Größe der ICs zu vergrößern.
Herausforderungen von Finepitch
Herstellungskomplexität: Die Fertigung von Leiterplatten und Bauteilen mit Finepitch erfordert hochpräzise Maschinen, sowohl für das Routing der Leiterbahnen als auch für die Platzierung der Bauteile. Dies macht den Prozess aufwändiger und teurer.
Inspektion und Test: Die geringe Größe der Pins und der Abstände macht die visuelle Inspektion schwierig. Automatisierte Inspektionssysteme (wie AOI) und präzise Testmethoden sind notwendig, um sicherzustellen, dass keine Fehler wie Kurzschlüsse oder nicht korrekt verlötete Pins auftreten.
Finepitch im Bestückungsprozess
Feinfühlige Bestückung: Da die Pins so eng beieinanderliegen, müssen Bestückungsmaschinen und Lötverfahren, wie Reflow-Löten, extrem präzise arbeiten. Kleinste Fehljustierungen können zu Defekten führen.
Lötpaste: Die Wahl der richtigen Lötpaste und des Schablonendrucks ist besonders wichtig, um sicherzustellen, dass die feinen Pins korrekt verlötet werden.
Fazit
Finepitch-Technologie ist ein wesentlicher Bestandteil moderner Elektronik, da sie es ermöglicht, auf kleinstem Raum hochintegrierte Schaltkreise und Bauteile zu platzieren. Allerdings erfordert sie auch fortschrittliche Fertigungs- und Inspektionstechniken, um die hohen Anforderungen an Präzision und Zuverlässigkeit zu erfüllen.
Ein Fingertester (auch bekannt als Flying Probe Tester) ist ein Prüfgerät, das in der Elektronikfertigung zur Überprüfung von Leiterplatten (PCBs) auf elektrische Fehler wie Kurzschlüsse, Unterbrechungen oder falsche Verbindungen verwendet wird. Der Name „Fingertester“ stammt von den beweglichen Testspitzen (den „Fingern“), die flexibel auf der Leiterplatte platziert werden können, um die Leitungsbahnen und Bauteile zu überprüfen.
Funktionsweise des Fingertesters
Flexible Testspitzen: Anstatt eines festen Adapters (wie bei einem Adaptertest) werden beim Fingertester bewegliche, motorisierte Nadeln verwendet, die auf die zu prüfenden Punkte der Leiterplatte zusteuern. Diese Nadeln oder „Finger“ können unterschiedliche Bereiche der Platine erreichen.
Elektrische Tests: Der Fingertester misst Widerstand, Kapazität und andere elektrische Parameter, um sicherzustellen, dass die Verbindungen korrekt sind. Typische Tests umfassen die Überprüfung auf Kurzschlüsse, offene Verbindungen und Bauteilfehler.
Softwaregesteuert: Die Positionierung der Testspitzen erfolgt mittels Software, die ein Testprogramm basierend auf dem Schaltplan oder der Netzliste der Leiterplatte steuert.
Vorteile des Fingertesters
Keine spezielle Vorrichtung nötig: Im Gegensatz zum Adaptertest benötigt der Fingertester keine speziellen Adapter, die für jede Leiterplattenkonfiguration individuell angefertigt werden müssen. Das macht den Testprozess besonders bei kleinen Serien oder Prototypen schneller und kostengünstiger.
Schnell einsetzbar: Da der Fingertester keine umfangreiche Vorbereitung erfordert, kann er flexibel und kurzfristig für neue Designs verwendet werden, was ihn ideal für Prototypen und Kleinserien macht.
Präzision: Der Fingertester kann auch kleine, schwer zugängliche Bereiche der Leiterplatte überprüfen, da die Testspitzen sehr präzise positioniert werden können.
Nachteile des Fingertesters
Langsam im Vergleich zum Adaptertest: Da der Fingertester jede Verbindungsstelle der Leiterplatte nacheinander überprüft, kann der Testprozess bei komplexen und großen Leiterplatten vergleichsweise lange dauern.
Begrenzte Geschwindigkeit bei Großserien: Für größere Produktionsvolumina ist der Adaptertest (der alle Verbindungen gleichzeitig überprüft) oft schneller und effizienter.
Anwendungsbereiche
Prototypen und Kleinserien: Da der Fingertester schnell eingerichtet werden kann und keine speziellen Vorrichtungen benötigt, wird er häufig zur Prüfung von Prototypen und kleinen Stückzahlen verwendet.
Designüberprüfung: Vor der Massenproduktion kann der Fingertester verwendet werden, um sicherzustellen, dass das Leiterplattendesign fehlerfrei ist und alle Verbindungen korrekt funktionieren.
Fazit
Der Fingertester ist ein flexibles und kostengünstiges Prüfwerkzeug, das insbesondere bei Prototypen und Kleinserien eingesetzt wird. Aufgrund seiner Beweglichkeit und Präzision eignet er sich besonders gut für Designs, die sich häufig ändern oder für kleine Produktionen, bei denen sich die Anschaffung eines Adapters nicht lohnt. Für größere Serien ist jedoch der Adaptertest oft die bessere Wahl.
- FLEX (-PCBs)
- FLEXIBLE LEITERPLATTE
- FLYING PROBE
- FOOTPRINT
Vgl. auch → Flexible Leiterplatte
Flexible Leiterplatten (auch Flex-PCBs genannt) sind spezielle Leiterplatten, die auf flexiblen, dünnen Substraten basieren. Im Gegensatz zu starren Leiterplatten, die auf starren Materialien wie FR4 basieren, bestehen flexible Leiterplatten aus flexiblen Materialien wie Polyimid, die es ermöglichen, die Platine zu biegen oder zu falten, ohne ihre Funktion zu beeinträchtigen.
Aufbau einer flexiblen Leiterplatte
Substratmaterial: Das Substrat, also das Basismaterial, besteht in der Regel aus Polyimid oder anderen flexiblen, isolierenden Kunststoffen, die sich durch hohe Temperaturbeständigkeit und mechanische Flexibilität auszeichnen.
Leiterbahnen: Kupfer wird als Leitermaterial verwendet, das auf das flexible Substrat aufgetragen wird. Die Kupferschichten können geätzt oder auf andere Weise strukturiert werden, um die gewünschten Schaltkreise zu formen.
Schutzschichten: Die Kupferbahnen werden mit einer flexiblen Schutzschicht, oft einer Deckfolie oder einem Lötstopplack, abgedeckt, um sie vor mechanischen Einflüssen, Korrosion und elektrischen Störungen zu schützen.
Vorteile flexibler Leiterplatten
Platzersparnis: Flex-PCBs ermöglichen es, elektronische Systeme in kompakten, dreidimensionalen Formen zu bauen. Sie können in engen, gekrümmten Gehäusen oder an Stellen verwendet werden, an denen herkömmliche starre Leiterplatten nicht passen würden.
Gewichtsreduktion: Da weniger Material erforderlich ist, sind flexible Leiterplatten leichter als starre Leiterplatten, was besonders in der Luft- und Raumfahrt, im Automobilbereich und in tragbaren Geräten von Vorteil ist.
Hohe Zuverlässigkeit: Flexible Leiterplatten sind weniger anfällig für mechanische Belastungen wie Vibrationen und Erschütterungen, da sie sich biegen und anpassen können, ohne zu brechen.
Vielseitige Anwendungsmöglichkeiten: Sie können in einer Vielzahl von Anwendungen eingesetzt werden, darunter tragbare Elektronik, medizinische Geräte, Industrieanwendungen, Automobiltechnik und mehr.
Nachteile flexibler Leiterplatten
Höhere Herstellungskosten: Die Produktion flexibler Leiterplatten kann teurer sein als die Herstellung starrer PCBs, da spezielle Materialien und Prozesse erforderlich sind.
Empfindlicher gegenüber Beschädigungen: Trotz ihrer Flexibilität können diese Leiterplatten empfindlicher gegenüber rauen mechanischen Belastungen sein, insbesondere, wenn sie über längere Zeit wiederholt gebogen werden.
Komplexere Designprozesse: Die Entwicklung flexibler Leiterplatten erfordert oft spezielle Designsoftware und zusätzliche Planungsschritte, um sicherzustellen, dass die Flexibilität korrekt integriert wird, ohne die Funktion zu beeinträchtigen.
Anwendungsbereiche
Mobilgeräte und Wearables: Flexible Leiterplatten sind besonders in der Miniaturisierung von Elektronik wichtig, etwa bei Smartphones, Smartwatches und anderen tragbaren Geräten, wo Platz eine entscheidende Rolle spielt.
Medizinische Geräte: In der Medizintechnik kommen Flex-PCBs in Geräten wie Herzschrittmachern und Bildgebungsgeräten zum Einsatz, wo Zuverlässigkeit und Flexibilität entscheidend sind.
Automobil- und Luftfahrttechnik: Die Fähigkeit, Vibrationen und mechanische Belastungen besser standzuhalten, macht flexible Leiterplatten zu einer beliebten Wahl in der Automobil- und Luftfahrtindustrie.
Fazit
Flexible Leiterplatten bieten eine innovative Lösung für moderne Elektronikdesigns, bei denen Platz, Gewicht und mechanische Beanspruchung wichtige Faktoren sind. Ihre Vielseitigkeit ermöglicht es, sie in vielen hochspezialisierten und kompakten Anwendungen zu integrieren, obwohl sie etwas teurer und komplexer in der Herstellung sind.
Vgl. auch → Polyimid → Starrflex
Vgl. auch → Fingertester
Der Footprint einer Leiterplatte bezieht sich auf die physische Anordnung und Platzierung eines elektronischen Bauteils auf der Leiterplatte. Er stellt die geometrische Form dar, in der das Bauteil auf die Leiterplatte gelötet oder montiert wird. Der Footprint enthält spezifische Informationen über die Position der Lötpads, mechanische Haltepunkte und elektrische Anschlüsse, die erforderlich sind, damit das Bauteil ordnungsgemäß auf der Platine befestigt und elektrisch verbunden wird.
Bestandteile eines Footprints:
Lötpads: Die elektrischen Verbindungen, an denen die Pins oder Anschlüsse eines Bauteils gelötet werden.
Konturen des Bauteils: Die Außenmaße und Umrisse des Bauteils, die sicherstellen, dass es mechanisch auf der Platine passt.
Referenzmarkierungen: Markierungen, die dem Bestückungsprozess helfen, das Bauteil korrekt zu positionieren.
Position von Fiducials: Punkte auf der Platine, die zur genauen Ausrichtung und Positionierung von Bauteilen durch die Bestückungsmaschine verwendet werden.
Funktion und Bedeutung eines Footprints:
Exakte Positionierung: Der Footprint definiert die exakte Platzierung des Bauteils, sodass es mechanisch passt und elektrisch korrekt angeschlossen ist.
Elektrische Verbindung: Die Lötpads des Footprints stellen sicher, dass das Bauteil ordnungsgemäß mit den Leiterbahnen der Leiterplatte verbunden wird.
Design-Optimierung: Der Footprint hilft beim Design der Leiterplatte, indem er sicherstellt, dass alle Bauteile korrekt angeordnet sind und sich nicht gegenseitig stören. Er berücksichtigt zudem die Anforderungen an Löttechnik (SMD, THT) und Bauraum.
Arten von Footprints:
SMD (Surface-Mount Device) Footprints: Diese Footprints sind für oberflächenmontierte Bauteile konzipiert, bei denen die Lötpads sich auf derselben Seite der Leiterplatte befinden und die Bauteile direkt auf die Oberfläche gelötet werden.
THT (Through-Hole Technology) Footprints: Bei THT-Footprints haben die Bauteile Pins, die durch Bohrungen in der Leiterplatte geführt und auf der Rückseite verlötet werden.
Hybrid-Footprints: Diese kombinieren sowohl SMD- als auch THT-Elemente und werden für Bauteile verwendet, die beide Technologien nutzen.
Erstellung von Footprints:
EDA-Software: Footprints werden in elektronischen Design-Automations- (EDA-) Tools erstellt, wie z. B. Altium Designer, KiCad oder Eagle. Hier werden die geometrischen Abmessungen des Bauteils und die Position der Anschlüsse in den PCB-Layout integriert.
Normen und Standards: Footprints müssen oft nach festgelegten Normen erstellt werden, wie z. B. den IPC-Standards (z. B. IPC-7351), um sicherzustellen, dass sie mit den meisten Bauteilen und Leiterplatten kompatibel sind.
Fazit:
Der Footprint einer Leiterplatte ist ein entscheidender Teil des PCB-Designprozesses, da er die Schnittstelle zwischen dem elektronischen Bauteil und der Leiterplatte definiert. Eine präzise Gestaltung des Footprints gewährleistet nicht nur eine optimale elektrische Verbindung, sondern auch die mechanische Stabilität des Bauteils auf der Leiterplatte.
- FOTORESIST
- FR4
- FRÄSEN
- FREISTELLUNG
Siehe → Resist
FR4 ist ein weit verbreitetes Material in der Leiterplattenherstellung, das als Substrat für die meisten starren Leiterplatten (PCBs) dient. Der Begriff „FR4“ steht für „Flame Retardant 4“ und bezeichnet eine glasfaserverstärkte Epoxidharzplatte, die feuerbeständig ist. Dieses Material bietet eine ideale Kombination aus mechanischen, thermischen und elektrischen Eigenschaften, was es zur Standardwahl für Leiterplatten macht.
Eigenschaften von FR4:
Flammschutz: FR4 ist schwer entflammbar und erfüllt die Anforderungen an Feuerfestigkeit nach UL94-V0. Das bedeutet, dass das Material im Brandfall nicht weiterbrennt, sondern selbstlöschend ist.
Mechanische Stabilität: FR4 bietet hohe Festigkeit und Steifigkeit, was es ideal für starre Leiterplatten macht. Es hält sowohl mechanische Belastungen als auch Vibrationen gut aus.
Elektrische Isolierung: Das Epoxidharz sorgt für hervorragende Isolationseigenschaften, was die elektrische Integrität der Schaltung sicherstellt.
Geringe Feuchtigkeitsaufnahme: FR4 hat eine sehr niedrige Feuchtigkeitsaufnahme, was es für Umgebungen mit wechselnder Luftfeuchtigkeit geeignet macht.
Temperaturbeständigkeit: Es hat eine gute Wärmebeständigkeit und kann Temperaturen bis zu ca. 130–140 °C aushalten, was es für die meisten Elektronikprodukte geeignet macht.
Aufbau von FR4:
Glasfasergewebe: Der Kern von FR4 besteht aus gewebten Glasfasern, die für Festigkeit und Steifigkeit sorgen.
Epoxidharz: Die Glasfasern sind mit Epoxidharz getränkt, das das Material feuerhemmend und elektrisch isolierend macht.
Kupferfolie: In der Regel wird FR4 mit einer oder mehreren Lagen von Kupferfolie beschichtet, auf denen dann die Leiterbahnen der Platine geätzt werden. Als Material kann es so für 1- oder 2-Lagen Leiterplatten zum Einsatz kommen oder für Multilayer als PrePreg und Kern verwendet werden.
Anwendungsbereiche:
Consumer Electronics: Die meisten elektronischen Geräte, von Smartphones über Computer bis hin zu Haushaltsgeräten, verwenden Leiterplatten aus FR4.
Automotive: In der Automobilindustrie wird FR4 wegen seiner Stabilität und Haltbarkeit in vielen Elektroniksystemen eingesetzt.
Industrieelektronik: Maschinen und Geräte, die unter rauen Bedingungen arbeiten, profitieren von der Zuverlässigkeit und Beständigkeit von FR4-basierten Leiterplatten.
Luft- und Raumfahrt: Aufgrund seiner Flammschutzeigenschaften findet FR4 auch in der Luft- und Raumfahrt Anwendungen.
Nachteile von FR4:
Begrenzte Wärmeableitung: FR4 ist kein gutes Material für Anwendungen, bei denen eine hohe Wärmeableitung erforderlich ist, wie etwa bei Hochleistungs-LEDs oder Leistungsbauteilen.
Nicht für Hochfrequenzanwendungen: Bei sehr hohen Frequenzen kann FR4 zu Verlusten führen, weshalb für solche Anwendungen oft andere Materialien wie Rogers oder PTFE (Teflon) verwendet werden.
Fazit:
FR4 ist das Standardmaterial für starre Leiterplatten und bietet ein hervorragendes Gleichgewicht zwischen Kosten, Leistung und Verarbeitbarkeit. Es eignet sich für die meisten Anwendungen in der Elektronik, insbesondere bei Konsumgütern und industriellen Geräten, wo mechanische Stabilität und elektrische Isolierung entscheidend sind.
Vgl. auch → Multilayer → PrePreg
Fräsen ist ein wichtiger Prozess in der Herstellung von Leiterplatten (PCBs), bei dem Material von einer Leiterplatte entfernt wird, um spezifische Formen, Konturen, Stege, Ausschnitte oder Öffnungen zu erzeugen. Dieser Vorgang kann verwendet werden, um Leiterplatten nach den Designanforderungen zu bearbeiten, und wird häufig eingesetzt, um mechanische Teile wie Ausschnitte, Bohrungen oder Konturen für Bauteile zu schaffen.
Prozess des Fräsens:
Vorbereitung: Zunächst wird die Leiterplatte entsprechend dem Design in die Fräsmaschine eingespannt. Die CNC (Computer Numerical Control)-Technologie wird häufig verwendet, um präzise Fräsarbeiten durchzuführen.
Fräswerkzeug: Ein rotierendes Schneidwerkzeug (Fräser) wird eingesetzt, das je nach Bedarf verschiedene Durchmesser und Formen aufweisen kann. Die Wahl des Fräsers hängt von der Art des Materials und der gewünschten Bearbeitung ab.
Materialabtrag: Während des Fräsvorgangs wird das Material schichtweise abgetragen. Das Werkzeug bewegt sich in verschiedenen Achsen, um die spezifischen Formen und Konturen zu erstellen.
Abschluss: Nach dem Fräsen werden die Kanten oft entgratet, um scharfe Kanten zu entfernen und eine bessere Handhabung zu gewährleisten.
Anwendungsbereiche des Fräsens in der Leiterplattenherstellung:
Ausschnitte: Fräsen wird häufig verwendet, um Ausschnitte für Bauteile wie Steckverbinder oder Schalter zu erstellen.
Konturen: Die Form der Leiterplatte kann durch Fräsen an die spezifischen Anforderungen des Designs angepasst werden.
Bohren von Löchern: Obwohl Bohrungen oft durch spezielle Bohrmaschinen erstellt werden, können auch Fräswerkzeuge verwendet werden, um Löcher für Bauteile oder Befestigungen zu schaffen.
Spezielle Profile: Fräsen ermöglicht die Herstellung von speziellen Profilen oder Geometrien, die mit anderen Verfahren möglicherweise nicht realisierbar sind.
- Tiefenfräsung: Diese – auch unter Z-Fräsung bekannt – ermöglicht ein unterschiedliches Höhenniveau am Rand oder innerhalb der Leiterplatte.
Vorteile des Fräsens:
Hohe Präzision: CNC-Fräsen ermöglicht eine sehr präzise Bearbeitung, was zu exakten Formen und Maßen führt.
Flexibilität: Es können komplexe Designs und Formen realisiert werden, die mit anderen Methoden schwer zu erreichen sind.
Materialvielfalt: Fräsen kann auf verschiedenen Materialien angewendet werden, darunter FR4, Aluminium und spezielle Hochleistungskunststoffe.
Nachteile des Fräsens:
Kosten: Der Fräsprozess kann teurer sein als andere Bearbeitungsverfahren, insbesondere bei großen Stückzahlen.
Bearbeitungszeit: Fräsen kann zeitaufwändiger sein, besonders wenn komplexe Geometrien bearbeitet werden müssen.
Materialverlust: Durch den Abtrag des Materials kann es zu einem Verlust – zu einem geringeren Yield – kommen, was bei teureren Materialien signifikant sein kann.
Fazit:
Fräsen ist ein vielseitiger und präziser Prozess in der Leiterplattenherstellung, der es ermöglicht, spezifische Formen und Konturen zu schaffen. Es wird in vielen Anwendungen eingesetzt, um die Funktionalität und Anpassungsfähigkeit von Leiterplatten zu erhöhen. Die Wahl des Fräsverfahrens hängt von den spezifischen Anforderungen des Designs sowie von den verwendeten Materialien ab.
Vgl. auch → Steg → Yield → Tiefenfräsung
Freistellung bezieht sich in der Leiterplattenherstellung auf den Prozess, bei dem bestimmte Bereiche der Leiterplatte von einer leitfähigen Schicht befreit werden (Stopplack, Lötstopplack), um elektrische Isolation zu gewährleisten oder spezifische Designanforderungen zu erfüllen. Dieser Vorgang kann sowohl beim Erstellen der Leiterbahnen als auch bei der Vorbereitung von Lötflächen oder anderen wichtigen Bereichen der Platine erfolgen.
Anwendungen der Freistellung:
Isolierung von Leiterbahnen: Bereiche, in denen keine elektrische Verbindung bestehen soll, werden freigestellt, um Kurzschlüsse zu vermeiden und die Funktionalität der Schaltung zu sichern.
Vorbereitung von Lötflächen: Freistellungen können verwendet werden, um die Zonen zu markieren, an denen Bauteile gelötet werden sollen, wobei unerwünschte Kontaktstellen ausgeschlossen werden.
Anpassung an Geometrien: Bei speziellen Bauteilen oder Geometrien kann eine Freistellung erforderlich sein, um sicherzustellen, dass die Bauteile korrekt auf der Leiterplatte sitzen oder montiert werden können.
Prozess der Freistellung:
Design-Software: In der Regel erfolgt die Freistellung während des Designprozesses in einer elektronischen Design-Automations- (EDA) Software. Hier können Designer die Bereiche auswählen, die freigestellt werden sollen.
Gerber-Daten: Die Freistellungen werden in den Gerber-Daten, die zur Fertigung der Leiterplatte verwendet werden, spezifiziert.
Ätzen oder Fräsen: Nach der Erstellung der Leiterplatte können Freistellungen durch Ätzen oder Fräsen realisiert werden, wobei die unerwünschten Kupferbereiche abgetragen werden.
Vorteile der Freistellung:
Verbesserte Funktionalität: Durch die Isolierung bestimmter Bereiche können Designer sicherstellen, dass die elektrischen Eigenschaften der Platine den Anforderungen entsprechen.
Vermeidung von Kurzschlüssen: Freistellungen reduzieren das Risiko von elektrischen Fehlverbindungen, die zu Kurzschlüssen führen könnten.
Erleichterte Montage: Freigestellte Bereiche ermöglichen es, Bauteile einfacher zu montieren und zu löten, insbesondere bei komplexen Designs.
Nachteile der Freistellung:
Design-Komplexität: Die Notwendigkeit von Freistellungen kann das Design komplizierter machen und mehr Zeit in Anspruch nehmen.
Materialverlust: Je nach Methode kann es zu Materialverlusten kommen, was sowohl die Kosten als auch die Gesamtqualität der Leiterplatte beeinflussen kann.
Fazit:
Freistellungen sind ein wichtiger Bestandteil des Leiterplattendesigns und der Herstellung, da sie dazu beitragen, elektrische Isolation zu gewährleisten und die Funktionalität der Schaltung zu optimieren. Sie erfordern sorgfältige Planung und Ausführung, um sicherzustellen, dass die Leiterplatte effizient und zuverlässig arbeitet.
Vgl. auch → Stopplack → Lötstopplack
- GALV. NI/AU (HARTGOLD)
- GALVANIK
- GERBER
- GND
Galvanisch Nickel-Gold (auch als Hartgold bekannt) ist eine gängige Oberflächenbehandlung für Leiterplatten, die eine dünne Schicht aus Nickel und Gold auf die Kupferoberfläche aufbringt. Diese Behandlung bietet mehrere Vorteile, insbesondere in Bezug auf Korrosionsschutz, Leitfähigkeit und Lötbarkeit.
Prozess der galvanischen Nickel-Gold-Beschichtung:
Vorbereitung der Leiterplatte: Zunächst wird die Leiterplatte gereinigt und auf die galvanische Behandlung vorbereitet. Dies umfasst das Entfernen von Oxiden und Verunreinigungen von der Kupferoberfläche.
Nickel-Beschichtung: Die Leiterplatte wird in eine galvanische Lösung eingetaucht, die Nickelionen enthält. Durch elektrochemische Prozesse lagern sich die Nickelionen auf der Kupferoberfläche ab und bilden eine dünne Schicht.
Gold-Beschichtung: Im Anschluss wird die Goldschicht auf das Nickel aufgebracht. Diese Schicht ist normalerweise sehr dünn und dient hauptsächlich als Schutzschicht. Sie verbessert die Lötbarkeit und bietet eine gute elektrische Leitfähigkeit.
Vorteile der galvanischen Nickel-Gold-Beschichtung:
Korrosionsschutz: Die Nickel- und Goldschichten schützen die darunter liegende Kupferoberfläche vor Oxidation und Korrosion, was die Lebensdauer der Leiterplatte erhöht.
Verbesserte Lötbarkeit: Die Goldschicht sorgt für eine hervorragende Lötbarkeit, da sie bei der Wärmebehandlung stabil bleibt und eine gute Verbindung mit Lötmaterialien bildet.
Gute elektrische Eigenschaften: Die Kombination aus Nickel und Gold bietet eine hohe Leitfähigkeit, die für viele elektronische Anwendungen entscheidend ist.
Ästhetik: Die goldene Oberfläche verleiht der Leiterplatte ein hochwertiges Aussehen und kann für spezielle Anwendungen von Bedeutung sein.
Nachteile der galvanischen Nickel-Gold-Beschichtung:
Kosten: Gold ist ein teures Material, und die Verwendung von galvanischem Nickel-Gold kann die Produktionskosten erhöhen.
Dünne Schichten: Die Goldschicht ist in der Regel sehr dünn (in der Regel zwischen 0,1 und 5 µm), was bedeutet, dass sie nicht für Anwendungen geeignet ist, die eine dickere Schutzschicht erfordern.
Dynamik der Beschichtung: Der Prozess kann komplex sein und erfordert sorgfältige Kontrolle, um sicherzustellen, dass die Schichten gleichmäßig und ohne Defekte aufgetragen werden.
Anwendungsbereiche:
Hochwertige Elektronik: In Anwendungen, bei denen Zuverlässigkeit und Leistung entscheidend sind, wie in der Luft- und Raumfahrt, Automobilindustrie und medizinischen Geräten.
Verbindungselemente: Bei Steckverbindern und anderen Bauteilen, die häufig installiert und entfernt werden, ist eine gute Lötbarkeit und Korrosionsbeständigkeit erforderlich.
Leiterplatten für Hochfrequenzanwendungen: Aufgrund ihrer hervorragenden elektrischen Eigenschaften werden galvanisch beschichtete Leiterplatten oft in Hochfrequenzschaltungen verwendet.
Fazit:
Galvanisch Nickel-Gold (Hartgold) ist eine effektive Methode zur Verbesserung der Oberflächeneigenschaften von Leiterplatten. Diese Beschichtung bietet einen ausgezeichneten Schutz gegen Korrosion, verbessert die Lötbarkeit und gewährleistet eine hohe elektrische Leitfähigkeit. Obwohl die Kosten höher sein können, ist der Nutzen in vielen kritischen Anwendungen unbestreitbar.
Prozess der Galvanik:
Elektrolytlösung: Der Prozess erfolgt in einer Lösung, die Metallionen enthält (z. B. Nickel, Gold oder Kupfer). Diese Lösung dient als Elektrolyt.
Stromquelle: Ein elektrischer Strom wird durch die Lösung geleitet, wobei die Leiterplatte als Kathode fungiert. Die Metallionen aus der Lösung lagern sich an der Kathode ab und bilden eine dünne Metallschicht.
Kontrolle: Der Prozess erfordert eine präzise Kontrolle von Faktoren wie Temperatur, pH-Wert und Stromstärke, um eine gleichmäßige und fehlerfreie Beschichtung zu gewährleisten.
Anwendungen der Galvanik in der Leiterplattenherstellung:
Oberflächenbehandlung: Galvanik wird verwendet, um Schutzschichten aus verschiedenen Metallen aufzubringen, die Korrosion verhindern und die Lötbarkeit verbessern (z. B. galvanisches Nickel-Gold).
Erhöhung der Leitfähigkeit: Durch die Beschichtung mit Materialien wie Kupfer kann die elektrische Leitfähigkeit der Leiterplatte erhöht werden.
Strukturverstärkung: In bestimmten Anwendungen kann die Galvanik verwendet werden, um die strukturelle Integrität und Festigkeit von Bauteilen zu verbessern.
Vorteile der Galvanik:
Präzision: Die Galvanotechnik ermöglicht eine präzise Steuerung der Dicke und Qualität der Beschichtung.
Vielfalt der Materialien: Verschiedene Metalle können durch Galvanik aufgebracht werden, was eine Anpassung an spezifische Anforderungen ermöglicht.
Wirtschaftlichkeit: Im Vergleich zu anderen Beschichtungsverfahren kann die Galvanik kosteneffizient sein, insbesondere bei großen Stückzahlen.
Nachteile der Galvanik:
Umwelteinflüsse: Der Prozess kann umweltbelastend sein, wenn Abfälle nicht ordnungsgemäß behandelt werden. Die Verwendung von chemischen Stoffen erfordert strenge Vorschriften zur Abfallentsorgung.
Beschränkungen bei der Haftung: Die Haftung der aufgebrachten Schichten kann je nach Substrat und Beschichtungsmaterial variieren, was zu potenziellen Problemen führen kann.
Fazit:
Galvanik oder Galvanotechnik ist ein entscheidendes Verfahren in der Leiterplattenherstellung, das es ermöglicht, metallische Schichten präzise aufzubringen und die Eigenschaften von Leiterplatten zu verbessern. Mit ihren vielfältigen Anwendungen und Vorteilen ist sie ein wesentlicher Bestandteil moderner Elektronikfertigung.
Gerber ist ein weit verbreitetes Dateiformat, das in der Elektronikindustrie verwendet wird, insbesondere in der Leiterplattenherstellung. Es dient zur Übertragung von Informationen über die geometrischen Layouts von Leiterplatten und enthält spezifische Daten für die Fertigung.
Hauptmerkmale des Gerber-Formats:
Datenstruktur: Gerber-Dateien bestehen aus Befehlen und Koordinaten, die die verschiedenen Schichten der Leiterplatte beschreiben, einschließlich Kupferbahnen, Lötpads, Bohrlöcher und andere wichtige Merkmale.
Schichten: Das Gerber-Format ermöglicht die Erstellung mehrerer Schichten einer Leiterplatte, z. B. die Top- und Bottom-Schicht, die Lötmasken und die Siebdruckschicht (Silkscreen). Jede Schicht wird in einer separaten Gerber-Datei gespeichert.
Standardisierung: Das Gerber-Format ist standardisiert (vor allem durch die RS-274X-Spezifikation), was die Interoperabilität zwischen verschiedenen Software-Tools und Maschinen in der Leiterplattenfertigung ermöglicht.
Zubehördaten: Neben den Layoutdaten können auch Informationen über Bohrungen (in separaten Excellon-Dateien) und Materialparameter über separate Dateien bereitgestellt werden.
Anwendungen des Gerber-Formats:
Fertigung: Die Hauptanwendung von Gerber-Dateien liegt in der Herstellung von Leiterplatten. Sie werden an PCB-Hersteller übermittelt, um die benötigten Produktionsdaten zu liefern.
Design-Software: Elektronische Design-Automation (EDA)-Software verwendet das Gerber-Format, um das Design von Leiterplatten zu visualisieren und die Fertigungsdaten zu generieren.
Überprüfung: Gerber-Dateien werden auch zur Überprüfung und Validierung von PCB-Designs vor der Fertigung genutzt, um sicherzustellen, dass sie den Designanforderungen entsprechen.
Vorteile des Gerber-Formats:
Kompatibilität: Das Gerber-Format ist mit den meisten PCB-Design-Tools kompatibel, was den Austausch von Dateien zwischen verschiedenen Softwareanwendungen erleichtert.
Präzision: Die genauen geometrischen Informationen ermöglichen eine präzise Fertigung von Leiterplatten, was die Qualität und Leistung verbessert.
Flexibilität: Gerber-Dateien können einfach aktualisiert und angepasst werden, was Änderungen im Designprozess unterstützt.
Nachteile des Gerber-Formats:
Komplexität: Die Erzeugung und Handhabung von Gerber-Dateien kann für Neulinge in der Leiterplattenherstellung komplex sein.
Fehlende 3D-Informationen: Gerber-Dateien bieten keine 3D-Daten der Leiterplatte, was die Visualisierung und das Verständnis von komplexen Designs erschwert.
Fazit:
Das Gerber-Format ist ein unverzichtbarer Bestandteil der Leiterplattenherstellung, das eine präzise Kommunikation zwischen Designern und Herstellern ermöglicht. Durch seine Standardisierung und Flexibilität spielt es eine entscheidende Rolle in der modernen Elektronikfertigung und trägt zur Qualität und Effizienz der Produktionsprozesse bei.
GND steht für „Ground“ – im Deutschen spricht man von „Masse“ – und bezeichnet in der Elektronik den Bezugspunkt für elektrische Spannungen. Es handelt sich um die gemeinsame Rückleitung für elektrische Signale und bietet einen stabilen Referenzpunkt für die gesamte Schaltung. Hier sind einige wichtige Aspekte:
Funktionen von GND:
Referenzpunkt: GND dient als Bezugspunkt für alle Spannungen in einem Schaltkreis. Alle Spannungsmessungen werden relativ zu diesem Punkt vorgenommen.
Stromrückführung: GND bietet den Pfad für den Rückfluss von elektrischem Strom. Wenn ein elektrisches Gerät oder eine Schaltung funktioniert, fließt der Strom vom positiven Pol zur Last und zurück über den GND-Pfad.
Sicherheitsfunktion: In vielen elektrischen Systemen dient GND auch als Sicherheitsmaßnahme. Durch die Verbindung mit einem geerdeten Punkt wird das Risiko von Stromschlägen reduziert.
Anwendungen von GND:
Schaltungen: In der PCB-Design- und Fertigungsbranche wird GND häufig auf Leiterplatten verwendet, um die elektrische Stabilität zu gewährleisten und Rauschen zu minimieren.
Signalübertragung: In digitalen und analogen Schaltungen ist GND entscheidend für die Signalqualität und verhindert Störungen.
Erdung: Bei größeren elektrischen Installationen wird GND oft mit einer Erdung verbunden, um zusätzliche Sicherheitsvorkehrungen zu treffen.
GND in der Leiterplattenherstellung:
Leiterbahnen: GND-Leiterbahnen sind oft breiter und mit speziellen Designregeln versehen, um die elektrische Integrität zu gewährleisten und den Widerstand zu minimieren.
Via-Verbindungen: Um verschiedene Schichten einer Leiterplatte zu verbinden, werden Vias verwendet, die GND-Punkte auf den verschiedenen Schichten miteinander verbinden.
Bauteilanordnung: Die Anordnung von Bauteilen auf der Leiterplatte berücksichtigt oft den Zugang zu GND-Punkten, um eine effiziente Verbindung zu gewährleisten.
Fazit:
GND ist ein grundlegendes Konzept in der Elektronik und spielt eine entscheidende Rolle in der Funktionalität und Sicherheit von Schaltungen. Ein gut gestalteter GND-Pfad trägt zur Stabilität und Leistung von elektronischen Geräten bei und ist daher von zentraler Bedeutung in der Leiterplattenentwicklung und -herstellung.
Vgl. auch → Ground → Masse
- GOLD
- GRAT
- GROUND
Verwendung von Gold in der Leiterplattentechnik:
Oberflächenbeschichtung:
- Galvanisch Nickel-Gold: Diese Technik wird häufig eingesetzt, um eine dünne Goldschicht auf einer Nickelbasis aufzubringen. Diese Kombination schützt die darunter liegende Kupferoberfläche vor Korrosion und bietet hervorragende Lötbarkeit.
- Chemisch Gold: Hierbei wird Gold ohne elektrische Spannung aufgebracht, meist in sehr dünnen Schichten. Diese Methode wird häufig für Anwendungen verwendet, bei denen die Lötbarkeit und Korrosionsbeständigkeit entscheidend sind.
Verbindungstechnik:
- Stiftverbindungen: Gold wird oft für Kontakte und Verbindungen in Steckverbindern verwendet, da es eine hervorragende elektrische Leitfähigkeit bietet und eine Oxidation verhindert.
- Drahtbonden: In der Halbleiterindustrie wird Gold häufig zum Drahtbonden verwendet, um Verbindungen zwischen Chip und Gehäuse herzustellen.
Vorteile von Gold:
- Korrosionsbeständigkeit: Gold oxidiert nicht, was es ideal für Umgebungen macht, in denen Korrosion ein Risiko darstellt.
- Hervorragende Lötbarkeit: Die Lötfähigkeit von Gold ist sehr gut, was eine zuverlässige Verbindung zwischen den Bauteilen ermöglicht.
- Hohe elektrische Leitfähigkeit: Gold ist ein ausgezeichneter elektrischer Leiter, was die Leistung von elektrischen Verbindungen verbessert.
Nachteile von Gold:
- Kosten: Gold ist ein teures Material, was die Produktionskosten erhöhen kann. Daher wird es oft nur in Anwendungen verwendet, wo es unbedingt notwendig ist.
- Dünne Schichten: Die Dicke der Goldschicht ist normalerweise sehr gering, was bedeutet, dass sie in Anwendungen mit hoher mechanischer Beanspruchung möglicherweise nicht ausreichend Schutz bietet.
Anwendungsbereiche:
- Hochfrequenzanwendungen: Aufgrund seiner guten elektrischen Eigenschaften wird Gold häufig in Hochfrequenzschaltungen eingesetzt.
- Medizinische Geräte: In medizinischen Anwendungen, wo Zuverlässigkeit und Hygiene wichtig sind, wird Gold aufgrund seiner korrosionsbeständigen Eigenschaften geschätzt.
- Luft- und Raumfahrt: In der Luft- und Raumfahrttechnik werden Goldbeschichtungen verwendet, um die Funktionalität von kritischen elektronischen Komponenten zu gewährleisten.
Fazit:
Gold ist ein wichtiger Werkstoff in der Leiterplattentechnik, der sowohl für die Oberflächenbeschichtung als auch für die Verbindungstechnik unverzichtbar ist. Seine Eigenschaften tragen zur Verbesserung der Leistung und Zuverlässigkeit elektronischer Komponenten bei, auch wenn die Kosten eine Überlegung bei der Materialauswahl darstellen.
Vgl. auch → Chemisch Gold
Grate sind scharfe Kanten oder Überstände, die an den Rändern von Bauteilen, insbesondere nach dem Schneiden oder Fräsen von Materialien wie Leiterplatten, entstehen können. Diese unerwünschten Erhebungen können verschiedene Probleme verursachen und sollten daher nach der Herstellung behandelt werden.
Ursachen für Grate:
Bearbeitungsverfahren: Grate entstehen häufig während der mechanischen Bearbeitung, wie Fräsen, Schneiden oder Bohren. Die verwendeten Werkzeuge und deren Zustand beeinflussen die Gratebildung.
Materialeigenschaften: Einige Materialien neigen mehr zur Gratbildung als andere, abhängig von ihrer Härte und Zähigkeit.
Prozessparameter: Faktoren wie Schnittgeschwindigkeit, Vorschubrate und Werkzeuggeometrie können ebenfalls zur Bildung von Graten beitragen.
Probleme durch Grate:
- Sicherheit: Grate können scharfe Kanten aufweisen, die zu Verletzungen führen können, wenn Personen mit den Bauteilen in Kontakt kommen.
- Funktionsfähigkeit: In der Elektronik können Grate dazu führen, dass Bauteile nicht richtig montiert werden oder dass Verbindungen beeinträchtigt werden.
- Ästhetik: Grate beeinträchtigen das Aussehen der Bauteile, was in vielen Anwendungen unerwünscht ist.
Behandlung von Graten:
- Entgraten: Der Prozess des Entgratens entfernt die Grate von den Bauteilen. Dies kann mechanisch (z. B. Schleifen, Bürsten) oder chemisch (z. B. Ätzen) erfolgen.
- Werkzeugoptimierung: Die Verwendung von geeigneten Werkzeugen und die Anpassung der Bearbeitungsparameter können die Gratbildung minimieren.
- Qualitätskontrolle: Regelmäßige Inspektionen und Tests können helfen, die Bildung von Graten frühzeitig zu erkennen und zu behandeln.
Fazit:
Grate sind ein häufiges Problem in der Fertigung, insbesondere in der Leiterplattenherstellung. Ihre Behandlung ist entscheidend, um die Sicherheit, Funktionalität und Ästhetik der Bauteile zu gewährleisten. Durch geeignete Bearbeitungsverfahren und Nachbearbeitungstechniken kann die Gratbildung minimiert und die Qualität der Produkte verbessert werden.
Siehe → GND
- HAL
- HALBOFFENE DURCHKONTAKTIERUNG
- HALOGENFREI
- HALTESTEGE
Hot Air Leveling (HAL) ist ein Verfahren zur Oberflächenbehandlung von Leiterplatten, das in der Elektronikindustrie weit verbreitet ist. Es dient der Erstellung einer glatten, lötbaren Oberfläche, die insbesondere für die Bestückung und das Löten von Bauteilen wichtig ist. Hier sind die wichtigsten Aspekte von HAL:
Verfahren:
Vorbereitung: Die Leiterplatte wird zunächst gereinigt und von unerwünschten Rückständen befreit, um eine gleichmäßige Beschichtung zu gewährleisten.
Tauchprozess: Die Leiterplatte wird in ein Bad aus geschmolzenem Zinn oder Zinn-Legierung eingetaucht. Dabei bildet sich eine dünne Schicht der Legierung auf der Kupferoberfläche.
Heißluftbehandlung: Nach dem Eintauchen wird die Leiterplatte durch heiße Luft geführt, die das überschüssige Zinn abbläst und eine gleichmäßige und glatte Oberfläche hinterlässt.
Vorteile von HAL:
- Gute Lötbarkeit: HAL bietet eine ausgezeichnete Lötbarkeit, was die Verbindung von Bauteilen verbessert.
- Korrosionsschutz: Die Zinnbeschichtung schützt das Kupfer vor Oxidation und anderen Umwelteinflüssen.
- Einfache Verarbeitung: Das Verfahren ist relativ einfach und kann in den Produktionsprozess integriert werden.
Nachteile von HAL:
- Betriebsbedingungen: Die Qualität des HAL-Prozesses hängt stark von den Temperatur- und Zeitparametern ab. Unsachgemäße Bedingungen können zu ungleichmäßigen Beschichtungen führen.
- Legierungsbildung: In einigen Fällen kann die Legierung auf der Kupferoberfläche eine unzureichende Haftung aufweisen, was die Lötfähigkeit beeinträchtigen kann.
Anwendungen:
- Leiterplattenfertigung: HAL wird häufig für die Oberflächenbeschichtung von Leiterplatten eingesetzt, insbesondere in der Massenproduktion.
- Elektronische Geräte: Es ist besonders wichtig in Anwendungen, in denen eine hohe Zuverlässigkeit der Lötverbindungen erforderlich ist, wie in der Automobil- und Luftfahrtindustrie.
Fazit:
Hot Air Leveling ist ein effektives Verfahren zur Verbesserung der Oberflächenqualität von Leiterplatten und zur Sicherstellung der Lötbarkeit. Durch die Schaffung einer gleichmäßigen Zinnoberfläche bietet HAL zahlreiche Vorteile in der Elektronikfertigung, trotz einiger Herausforderungen, die bei der Prozesskontrolle beachtet werden müssen.
Halboffene Durchkontaktierung ist eine spezielle Technik in der Leiterplattentechnologie, die die Verbindung zwischen verschiedenen Schichten einer Leiterplatte ermöglicht, ohne dass die Bohrung vollständig durch alle Schichten reicht. Hier sind die wichtigsten Aspekte dieser Technik:
Definition:
- Eine halboffene Durchkontaktierung ist eine Bohrung, die nur teilweise durch eine Leiterplatte führt. Sie verbindet eine Schicht mit einer oder mehreren darunterliegenden Schichten, lässt jedoch die oberste Schicht unberührt.
Anwendungen:
- Signalverbindungen: Halboffene Durchkontaktierungen werden häufig verwendet, um Signale zwischen unterschiedlichen Schichten einer Leiterplatte zu übertragen, insbesondere in komplexen Designs.
- Einsparung von Platz: Sie sind nützlich in Anwendungen, in denen der Platz begrenzt ist und vollständige Durchkontaktierungen zu viel Raum beanspruchen würden.
Vorteile:
- Kostenreduktion: Durch den reduzierten Bohrungsaufwand können die Herstellkosten gesenkt werden.
- Vereinfachte Fertigung: Die Herstellung ist oft einfacher, da weniger Bohrungen erforderlich sind, was die Fertigungsgeschwindigkeit erhöht.
- Reduzierte Rückkehrwellen: Halboffene Durchkontaktierungen können helfen, Rückkehrwellen in Hochfrequenzanwendungen zu minimieren, da sie nicht vollständig durch die Leiterplatte führen.
Nachteile:
- Eingeschränkte Verbindungsoptionen: Da die Verbindung nicht vollständig durch die Leiterplatte führt, kann die Flexibilität bei der Planung von Schaltungen eingeschränkt sein.
- Verbindungsqualität: Die Verbindung zwischen den Schichten muss sorgfältig geplant werden, um sicherzustellen, dass sie eine ausreichende elektrische Integrität bietet.
Fazit:
Halboffene Durchkontaktierungen sind eine nützliche Technik in der Leiterplattenfertigung, die sowohl Kosten als auch Platz sparen kann. Sie bieten eine effektive Möglichkeit, Verbindungen zwischen Schichten herzustellen, während sie gleichzeitig einige der Herausforderungen der traditionellen Durchkontaktierungen umgehen.
Halogenfrei bezieht sich auf Materialien und Produkte, die keine halogenen Elemente enthalten, wie Fluor, Chlor, Brom und Jod. In der Elektronik- und Leiterplattenindustrie hat die Verwendung halogenfreier Materialien, – gerade im Basismaterial – an Bedeutung gewonnen, insbesondere aufgrund von Umwelt- und Gesundheitsbedenken.
Bedeutung in der Leiterplattenherstellung:
Umweltfreundlichkeit:
- Halogenfreie Materialien sind umweltfreundlicher, da sie bei der Verbrennung keine schädlichen halogenen Gase freisetzen, die zur Bildung von Dioxinen und anderen toxischen Verbindungen führen können.
Gesundheitsschutz:
- Die Verwendung halogenfreier Materialien reduziert die Risiken für die Gesundheit von Personen, die mit diesen Materialien während der Herstellung, Verarbeitung oder Entsorgung in Kontakt kommen.
REACH- und RoHS-Konformität:
- Halogenfreie Produkte erfüllen häufig die Anforderungen von REACH (Registration, Evaluation, Authorisation and Restriction of Chemicals) und RoHS (Restriction of Hazardous Substances), die den Einsatz gefährlicher Stoffe in elektronischen Produkten regulieren.
Materialien:
- Halogenfreie Epoxidharze: Diese werden häufig in der Leiterplattenproduktion verwendet, um die elektrischen Eigenschaften und die mechanische Stabilität zu gewährleisten, ohne halogene Chemikalien zu enthalten.
Vorteile:
- Bessere Umwelteigenschaften: Halogenfreie Materialien tragen zu einer nachhaltigeren Produktion und Entsorgung bei.
- Erhöhte Sicherheit: Reduzierte gesundheitliche Risiken während der Produktion und Nutzung.
Nachteile:
- Kosten: Halogenfreie Materialien können in der Herstellung teurer sein als herkömmliche Materialien.
- Leistungsunterschiede: In einigen Fällen können die physikalischen Eigenschaften von halogenfreien Materialien variieren, was die Designflexibilität einschränken kann.
Fazit:
Die Verwendung halogenfreier Materialien in der Leiterplattenfertigung ist ein wichtiger Schritt in Richtung nachhaltigerer und sicherer Elektronikprodukte. Sie bieten zahlreiche Vorteile, sowohl für die Umwelt als auch für die Gesundheit, und sind zunehmend in den Anforderungen der Branche verankert.
Vgl. auch → Basismaterial
Siehe → Steg
- HDI
- HF
- HOCHFREQUENZ LEITERPLATTE
- HOCH TG
- HÜLSE
HDI (High-Density Interconnect) bezeichnet eine Technologie in der Leiterplattenherstellung, die darauf abzielt, eine hohe Dichte an elektrischen Verbindungen und Komponenten auf einer relativ kleinen Fläche zu ermöglichen. Diese Technologie wird häufig in modernen elektronischen Geräten eingesetzt, die kompakte und leistungsstarke Leiterplatten benötigen.
Wesentliche Merkmale von HDI:
Feine Strukturen:
- HDI-Leiterplatten verfügen über sehr feine Leiterbahnen und enge Abstände zwischen den Komponenten. Dies ermöglicht die Integration einer größeren Anzahl von Bauteilen auf einer kleineren Fläche.
Durchkontaktierungen:
- HDI-Platten nutzen verschiedene Arten von Durchkontaktierungen, einschließlich Blind Vias und Buried Vias, die die Verbindung zwischen verschiedenen Schichten der Leiterplatte ermöglichen, ohne die gesamte Dicke der Platte zu durchdringen.
Multi-Layer-Designs:
- HDI-Technologie ermöglicht den Einsatz von mehrlagigen Leiterplatten, die komplexe Schaltungen und Funktionen unterstützen.
Vorteile von HDI:
- Platzersparnis: Durch die hohe Dichte können mehr Komponenten in einem kompakten Design untergebracht werden, was besonders in tragbaren und mobilen Geräten von Vorteil ist.
- Verbesserte Leistung: HDI-Platten ermöglichen kürzere Signalwege und eine bessere Signalqualität, was die Gesamtleistung der Schaltung verbessert.
- Flexibilität im Design: Entwickler haben mehr Spielraum für innovative Designs und können anspruchsvollere Schaltungen integrieren.
Anwendungen:
- Mobilgeräte: HDI-Technologie wird häufig in Smartphones, Tablets und anderen tragbaren Geräten eingesetzt.
- Computersysteme: Sie findet Anwendung in Motherboards und anderen Computerkomponenten, die hohe Leistung und geringe Größe erfordern.
- Automobil- und Luftfahrtindustrie: HDI wird auch in sicherheitskritischen Anwendungen eingesetzt, wo Zuverlässigkeit und Platzoptimierung entscheidend sind.
Nachteile von HDI:
- Kosten: Die Herstellung von HDI-Leiterplatten kann teurer sein als die von herkömmlichen Leiterplatten aufgrund der komplexeren Herstellungsprozesse.
- Verarbeitungsanforderungen: HDI-Platten erfordern spezialisierte Fertigungs- und Bearbeitungsverfahren, was die Produktionszeit verlängern kann.
Fazit:
HDI ist eine fortschrittliche Technologie in der Leiterplattenherstellung, die es ermöglicht, hochdichte und leistungsstarke elektronische Schaltungen zu entwickeln. Sie spielt eine entscheidende Rolle in der Miniaturisierung und Leistungssteigerung von modernen Elektronikgeräten.
Vgl. auch → Microvias → Blind Vias → Burried Vias
Siehe → GND
Hochfrequenz (HF)-Leiterplatten sind speziell für Anwendungen ausgelegt, die hochfrequente Signale verarbeiten, typischerweise im Frequenzbereich von 1 GHz bis über 100 GHz. Diese Leiterplatten sind in vielen modernen Technologien unverzichtbar, darunter Mobilfunk, Radartechnologie, Satellitenkommunikation und Hochgeschwindigkeitsdatenübertragung.
Wesentliche Merkmale von HF-Leiterplatten:
Materialien:
- HF-Leiterplatten werden aus speziellen Dielektrika gefertigt, die eine niedrige Dielektrizitätskonstante und einen niedrigen Verlustfaktor aufweisen. Gängige Materialien sind PTFE (Teflon), Rogers-Materialien oder andere spezielle laminierte Werkstoffe, die für Hochfrequenzanwendungen optimiert sind.
Designüberlegungen:
- Das Design von HF-Leiterplatten erfordert präzise Planung, um Signalverluste, Reflexionen und Störungen zu minimieren. Die Layout-Techniken beinhalten oft spezielle Impedanzanpassungen und die Verwendung von Stripline- oder Microstrip-Anordnungen.
Durchkontaktierungen:
- HF-Leiterplatten verwenden häufig Blind Vias oder Buried Vias, um die Signalwege zu optimieren und die Signalqualität zu gewährleisten.
Vorteile von HF-Leiterplatten:
- Geringe Verlustleistungen: Materialien mit niedrigem Verlust sorgen dafür, dass Signale über große Entfernungen mit minimaler Dämpfung übertragen werden können.
- Hohe Frequenzstabilität: HF-Leiterplatten sind so konzipiert, dass sie bei hohen Frequenzen eine stabile Leistung bieten, was entscheidend für die Zuverlässigkeit von Kommunikationssystemen ist.
- Flexibilität bei der Gestaltung: Die Verwendung spezialisierter Materialien ermöglicht innovative Designs, die auf die spezifischen Anforderungen von Hochfrequenzanwendungen abgestimmt sind.
Anwendungen:
- Telekommunikation: HF-Leiterplatten sind in Mobilfunk-Basisstationen, Satellitenschüsseln und anderen Kommunikationssystemen zu finden.
- Radar- und Satellitentechnologie: Sie werden in Radarsystemen, GPS-Technologie und Satellitenkommunikation verwendet, wo hohe Frequenzen und Signalintegrität entscheidend sind.
- Medizinische Geräte: In modernen medizinischen Geräten, die hochfrequente Signalverarbeitung erfordern, finden HF-Leiterplatten ebenfalls Anwendung.
Nachteile:
- Kosten: Hochfrequenzmaterialien und -herstellungsverfahren können teurer sein als die von Standard-Leiterplatten.
- Komplexität: Das Design und die Fertigung von HF-Leiterplatten erfordern spezialisierte Kenntnisse und Ausrüstung, was die Entwicklungszeit verlängern kann.
- Störanfällig: HF-Leiterplatten erfordern eine sorgfältige Auswahl an Designregeln, Materialauswahl und Herstellungsverfahren, um die Signalintegrität und Impedanzanpassung, zur Vermeidung von Störungen, zu gewährleisten.
Fazit:
Hochfrequenz-Leiterplatten sind entscheidend für die Leistung moderner Kommunikationstechnologien. Ihre speziellen Eigenschaften und Designanforderungen ermöglichen die effiziente Verarbeitung hochfrequenter Signale, was sie zu einem wichtigen Bestandteil in vielen hochentwickelten Anwendungen macht.
Vgl. auch → Signalintegrität → Impedanzanpassung
Der standard FR4 hat eine Tg von 130. Ab einen Tg-Wert von 170 kann man von einem High Tg (Hoch-Tg) sprechen. Für spezielle Anwendungen gibt es Materialien mit einem Tg von bis zu 280. Der Hogh Tg bezieht sich auf Materialien mit einer hohen Glasübergangstemperatur (Tg), die in der Leiterplattenherstellung verwendet werden. Die Tg ist die Temperatur, bei der ein Material von einem harten, spröden Zustand in einen flexiblen, gummiartigen Zustand übergeht. Hoch-Tg-Materialien sind entscheidend für Anwendungen, die hohe thermische Stabilität erfordern. Bei extrem hohen Betriebstemperaturen sollten vorzugsweise Materialien aus Polyimid, Teflon oder Keramik zur Anwendung kommen.
Wesentliche Merkmale von High Tg:
Erhöhte Temperaturbeständigkeit:
- Materialien mit hohem Tg können höheren Temperaturen standhalten, ohne ihre mechanischen und elektrischen Eigenschaften zu verlieren. Dies ist besonders wichtig in Anwendungen, in denen die Leiterplatte hohen thermischen Belastungen ausgesetzt ist.
Verbesserte Dimensionale Stabilität:
- Hoch-TG-Materialien bieten eine bessere dimensionale Stabilität bei wechselnden Temperaturen und Feuchtigkeitsbedingungen, was die Zuverlässigkeit der Leiterplatte erhöht.
Geringere Wasseraufnahme:
- Diese Materialien haben oft eine niedrigere Wasseraufnahme, was bedeutet, dass sie weniger anfällig für Feuchtigkeitsschäden sind, die zu elektrischen Problemen führen können.
Vorteile von High Tg-Materialien:
- Höhere Zuverlässigkeit: Ideal für Anwendungen in der Automobilindustrie, Luftfahrt und anderen Branchen, in denen Zuverlässigkeit unter extremen Bedingungen erforderlich ist.
- Erweiterte Lebensdauer: Hoch-TG-Leiterplatten können eine längere Lebensdauer haben, da sie weniger anfällig für thermische Erschöpfung sind.
- Bessere Leistung bei Hochfrequenz: Viele Hoch-TG-Materialien haben auch gute elektrische Eigenschaften, die sie für Hochfrequenzanwendungen geeignet machen.
Anwendungen:
- Automobilindustrie: In modernen Fahrzeugen werden Hoch-TG-Leiterplatten in sicherheitskritischen Systemen und zur Steuerung von Hochleistungsanwendungen eingesetzt.
- Luftfahrt und Raumfahrt: Diese Branchen erfordern Materialien, die extremen Bedingungen standhalten können, weshalb Hoch-TG-Materialien häufig verwendet werden.
- Telekommunikation: In Hochfrequenzanwendungen, wie Mobilfunk-Basisstationen, sind Hoch-TG-Leiterplatten vorteilhaft.
Nachteile:
- Kosten: Hoch-TG-Materialien sind in der Regel teurer als Standardmaterialien, was die Gesamtkosten der Leiterplatte erhöht.
- Komplexere Verarbeitung: Die Verarbeitung von Hoch-TG-Materialien kann anspruchsvoller sein und erfordert spezielle Herstellungsverfahren.
Fazit:
Hoch-TG-Materialien sind entscheidend für die Leistung und Zuverlässigkeit moderner Leiterplatten, insbesondere in Anwendungen, die hohe Temperaturen und anspruchsvolle Betriebsbedingungen erfordern. Sie bieten eine hervorragende thermische Stabilität und mechanische Integrität, was sie zu einer bevorzugten Wahl für viele hochentwickelte Technologien macht.
Vgl. auch → TG → Polyimid → Teflon
In Bezug auf Leiterplatten bezieht sich die Hülse häufig auf eine zylindrische Komponente, die in Verbindung mit der Leiterplattenherstellung und -montage verwendet wird. Diese Hülsen können unterschiedliche Funktionen haben, die entscheidend für die Funktionalität und Integrität der Leiterplatte sind.
Einsatzbereiche der Hülse in Leiterplatten:
Durchkontaktierungen:
- Hülsen werden oft verwendet, um Durchkontaktierungen zu stabilisieren oder zu isolieren. Sie können helfen, das Eindringen von Lötmaterial in bestimmte Bereiche zu verhindern und sicherzustellen, dass die elektrischen Verbindungen zuverlässig bleiben.
Bauteilbefestigung:
- In einigen Anwendungen dienen Hülsen dazu, Bauteile sicher an der Leiterplatte zu befestigen. Sie bieten mechanischen Halt und verhindern, dass sich die Bauteile während des Lötens oder des Betriebs bewegen.
Isolation:
- Hülsen aus isolierenden Materialien bieten zusätzlichen Schutz vor Kurzschlüssen und verhindern, dass elektrische Verbindungen unbeabsichtigt miteinander in Kontakt kommen.
Kabel- und Drahtanschlüsse:
- Hülsen können auch als Verbindungselemente für Kabel oder Drähte eingesetzt werden, um eine sichere und isolierte Verbindung zur Leiterplatte herzustellen.
Materialien:
- Hülsen für Leiterplatten werden in der Regel aus Materialien wie Kunststoff oder Metall gefertigt. Die Materialwahl hängt von den spezifischen Anforderungen der Anwendung ab, z. B. Temperaturbeständigkeit, Flexibilität und elektrische Eigenschaften.
Anwendungen:
- Hülsen finden sich in einer Vielzahl von elektronischen Geräten, darunter Computer, Mobiltelefone, industrielle Steuerungen und Haushaltsgeräte. Sie sind entscheidend für die Funktion und Sicherheit von Leiterplatten.
Fazit:
Hülsen spielen eine wichtige Rolle in der Leiterplattenherstellung, indem sie mechanische Unterstützung, Isolation und sichere Verbindungen gewährleisten. Ihre Anwendung ist entscheidend für die Zuverlässigkeit und Leistung elektronischer Systeme.
- IMMERSION GOLD
- IMPEDANZ
- IMPEDANZKONTROLLE
- IMS
- INNENLAGE
Immersion Gold ist die englische Abkürzung für die Leiterplattenoberfläche Electroless Nickel (ENIG)
Vgl. auch → Chemisch Nickel/Gold
Impedanz ist ein Begriff aus der Elektronik, der den Widerstand eines elektrischen Schaltkreises gegen den Wechselstrom beschreibt. In Bezug auf Leiterplatten (PCBs) spielt die Impedanz eine entscheidende Rolle, insbesondere bei Hochfrequenzanwendungen oder schnellen Signalübertragungen, wie sie in modernen Kommunikationssystemen und Computern auftreten.
Impedanz in der Leiterplatte:
Definition:
- Die Impedanz ist eine Kombination aus Widerstand (Resistanz) und Reaktanz (Kapazität und Induktivität) und wird in Ohm (Ω) gemessen. Sie beschreibt den Widerstand, den eine Leiterbahn oder ein Signalpfad einem Wechselstromsignal entgegensetzt.
Kontrollierte Impedanz:
- In vielen Hochgeschwindigkeits-Schaltungen muss die Impedanz präzise gesteuert werden, um Signalverluste oder Verzerrungen zu minimieren. Dies wird als kontrollierte Impedanz bezeichnet. Bei der Herstellung von Leiterplatten ist es wichtig, dass die Impedanz der Signalpfade exakt auf die Anforderungen der Schaltung abgestimmt ist.
Faktoren, die die Impedanz beeinflussen:
- Breite und Dicke der Leiterbahnen: Eine breitere oder dickere Leiterbahn hat eine geringere Impedanz.
- Abstand zwischen den Schichten: Die Distanz zwischen Leiterbahnen und der Bezugsebene (z. B. Masse oder Stromversorgung) beeinflusst die Impedanz.
- Material des Dielektrikums: Das Dielektrikum (Isolationsmaterial zwischen den Leiterbahnen) und seine Dielektrizitätskonstante haben einen großen Einfluss auf die Impedanz.
- Frequenz des Signals: Bei höheren Frequenzen kann die Impedanz variieren, da Induktivität und Kapazität eine stärkere Rolle spielen.
Wichtigkeit der Impedanzkontrolle:
- Eine nicht kontrollierte Impedanz kann zu Signalreflexionen, Übersprechen oder Signalverzögerungen führen, was die Funktionalität der gesamten Schaltung beeinträchtigt. Dies ist besonders wichtig in Hochfrequenz- oder Hochgeschwindigkeitsschaltungen wie in Computern, Telekommunikationsgeräten und medizinischen Geräten.
Anwendungen:
- Hochfrequenz-Leiterplatten: Für Schaltungen, die Signale mit hohen Frequenzen verarbeiten, wie WLAN-Router oder Mobiltelefone.
- Datenkommunikation: In High-Speed-Datenübertragungssystemen, wie USB, HDMI, Ethernet, bei denen die Signalqualität durch genaue Impedanzkontrolle sichergestellt wird.
Fazit:
Die Impedanz in der Leiterplattenherstellung ist ein kritischer Parameter, der die Signalqualität in Hochgeschwindigkeits- und Hochfrequenzanwendungen beeinflusst. Eine sorgfältige Impedanzkontrolle ist entscheidend, um die Leistungsfähigkeit moderner elektronischer Systeme zu gewährleisten.
Impedanzkontrolle bezieht sich auf die präzise Steuerung der Impedanz von Signalpfaden auf einer Leiterplatte (PCB), um Signalverluste, Verzerrungen und Reflexionen zu minimieren, insbesondere in Hochfrequenz- und Hochgeschwindigkeitsanwendungen. In der heutigen Elektronik, bei der hohe Datenraten und Frequenzen im Spiel sind, ist die Impedanzkontrolle entscheidend, um sicherzustellen, dass Signale effizient und fehlerfrei übertragen werden.
Warum ist Impedanzkontrolle wichtig?
Signalintegrität:
- Ohne korrekte Impedanzkontrolle kann es zu Signalreflexionen und -verzerrungen kommen, die zu Datenfehlern oder Verlusten führen können.
- Dies ist besonders wichtig bei schnellen digitalen Signalen und Hochfrequenz-Signalen, wie in Hochgeschwindigkeits-Datenleitungen (USB, HDMI, Ethernet) oder in der drahtlosen Kommunikation (WLAN, Mobilfunk).
Vermeidung von Signalreflexionen:
- Wenn die Impedanz der Leiterbahnen nicht mit der Impedanz der Quelle und der Last (z. B. eines Chips oder eines Steckers) übereinstimmt, kommt es zu Reflexionen, die das Signal stören und die Leistung des Systems beeinträchtigen.
Gleichbleibende Signalgeschwindigkeit:
- Eine stabile und kontrollierte Impedanz sorgt dafür, dass das Signal mit konstanter Geschwindigkeit durch die Leiterbahn fließt, was bei Hochgeschwindigkeits-Signalübertragungen von großer Bedeutung ist.
Faktoren, die die Impedanz beeinflussen:
Leiterbahnbreite und -dicke:
- Eine breitere oder dickere Leiterbahn hat eine geringere Impedanz, während eine schmalere oder dünnere Leiterbahn die Impedanz erhöht.
Dielektrikum:
- Das Isoliermaterial (Dielektrikum) zwischen den Leiterbahnen und Masse- oder Stromversorgungsebenen beeinflusst die Impedanz. Die Dielektrizitätskonstante (DK) des Materials spielt dabei eine entscheidende Rolle.
Abstand zu den Bezugsebenen:
- Der vertikale Abstand zwischen den Leiterbahnen und den darunterliegenden Bezugsebenen (Masse oder Stromversorgung) beeinflusst die Impedanz. Je größer der Abstand, desto höher die Impedanz.
Signalgeschwindigkeit und Frequenz:
- Bei höheren Frequenzen kann die Impedanz variieren, da kapazitive und induktive Effekte stärker ins Gewicht fallen.
Umgebungsfaktoren:
- Temperatur und Feuchtigkeit können ebenfalls Einfluss auf die Impedanz nehmen, indem sie die Eigenschaften des Dielektrikums oder der Leiterbahnen verändern.
Typen von kontrollierter Impedanz:
Single-Ended Impedanz:
- Wird für einzelne Leiterbahnen verwendet, die sich auf einer Bezugsebene (wie Masse) befinden.
Differenzielle Impedanz:
- Betrifft zwei Leiterbahnen, die ein differenzielles Signal übertragen, wie bei HDMI, USB oder Ethernet. Diese Leiterbahnen müssen eng beieinanderliegen und die Impedanz wird durch ihren Abstand zueinander und zur Bezugsebene bestimmt.
Herstellung von Leiterplatten mit Impedanzkontrolle:
Die Herstellung von PCBs mit kontrollierter Impedanz erfordert genaue Simulationen und Berechnungen während des Designs. Die Fertigung muss exakt nach diesen Spezifikationen erfolgen, um sicherzustellen, dass die gewünschten Impedanzwerte erreicht werden.
- Simulationssoftware: Wird verwendet, um die optimalen Dimensionen der Leiterbahnen, Abstände und Materialien zu berechnen.
- Messung und Überprüfung: Nach der Fertigung wird die Impedanz in der Regel durch spezielle Messgeräte überprüft, um sicherzustellen, dass sie innerhalb der zulässigen Toleranzen liegt.
Anwendungen der Impedanzkontrolle:
- Telekommunikation: Ethernet-Leiterbahnen oder Mobilfunkkomponenten erfordern eine genaue Impedanzkontrolle.
- Hochgeschwindigkeits-Datenübertragung: HDMI, USB, PCIe und andere schnelle Datenverbindungen.
- RFID- und HF-Schaltungen: Antennenschaltungen für drahtlose Kommunikation erfordern eine präzise Impedanzanpassung.
Fazit:
Die Impedanzkontrolle ist ein kritischer Prozess in der Herstellung von Leiterplatten, der sicherstellt, dass Hochfrequenz- und Hochgeschwindigkeitssignale ohne Signalverlust oder Verzerrung übertragen werden. Sie erfordert genaue Planung, Simulation und präzise Fertigung, um die Signalqualität zu gewährleisten und die Leistungsanforderungen moderner Elektronik zu erfüllen
IMS steht für Insulated Metal Substrate (isoliertes Metallsubstrat) und bezeichnet eine spezielle Art von Leiterplatten, die für Anwendungen mit hoher Wärmeableitung entwickelt wurden. Diese Leiterplatten bestehen aus einem Metallkern (meist Aluminium oder Kupfer), der durch eine isolierende Schicht von den darauf befindlichen Leiterbahnen getrennt ist. IMS-Leiterplatten werden häufig in leistungsstarken elektronischen Geräten eingesetzt, bei denen die Ableitung von Wärme entscheidend ist, beispielsweise in LED-Beleuchtungen, Leistungsumrichtern und Automobilanwendungen.
Aufbau von IMS-Leiterplatten:
Metallkern:
- Der Kern besteht in der Regel aus Aluminium oder Kupfer, da diese Metalle eine sehr gute thermische Leitfähigkeit haben und die Wärme effizient von den hitzeerzeugenden Bauteilen ableiten.
Dielektrische Schicht:
- Über dem Metallkern befindet sich eine isolierende Schicht, die elektrisch isolierend, aber thermisch leitfähig ist. Diese Schicht trennt den Metallkern von den Leiterbahnen und leitet gleichzeitig die Wärme von den Bauteilen zum Metallkern weiter.
Kupferschicht (Leiterbahnen):
- Auf der isolierenden Schicht werden die Leiterbahnen aufgebracht, in denen die elektrischen Signale fließen. Diese Schicht kann je nach Design und Anforderungen unterschiedlich dick sein.
Vorteile von IMS-Leiterplatten:
Hervorragende Wärmeableitung:
- Dank des Metallkerns leiten IMS-Platinen die Wärme effizient ab und verhindern Überhitzung. Dies ist besonders wichtig für Bauteile, die hohe Wärmemengen erzeugen, wie LEDs oder Leistungstransistoren.
Erhöhte Zuverlässigkeit:
- Durch die effektive Wärmeableitung bleibt die Temperatur der Bauteile niedriger, was ihre Lebensdauer verlängert und die Zuverlässigkeit der gesamten Schaltung verbessert.
Kompakte Bauweise:
- Da IMS-Leiterplatten die Wärme so gut ableiten, können Bauteile dichter zusammengebaut werden, was zu kompakteren Designs führt.
Typische Anwendungen:
- LED-Beleuchtungssysteme: Die hohe Wärmeentwicklung von LEDs macht IMS-Leiterplatten zu einer idealen Wahl, um die Lebensdauer und Effizienz der Beleuchtung zu verbessern.
- Leistungsumrichter: In Geräten, die elektrische Energie wandeln (z. B. in Wechselrichtern), helfen IMS-Platinen, die dabei entstehende Wärme effizient abzuführen.
- Automobilindustrie: IMS-Leiterplatten werden in Scheinwerfern, Motorsteuerungen und anderen hitzeerzeugenden Systemen von Fahrzeugen eingesetzt.
Fazit:
IMS-Leiterplatten sind eine ausgezeichnete Lösung für Anwendungen, bei denen Wärme effizient abgeführt werden muss. Ihre Struktur mit einem Metallkern bietet sowohl thermische Leitfähigkeit als auch elektrische Isolierung, wodurch sie für leistungsstarke, kompakte und zuverlässige elektronische Systeme unverzichtbar sind.
Vgl. auch → Alukern Platinen
Siehe → Steg
Die Innenlage einer Leiterplatte (Printed Circuit Board, PCB) bezieht sich auf die Schichten, die sich zwischen den äußeren, sichtbaren Schichten einer mehrlagigen Leiterplatte befinden. In einer mehrlagigen Leiterplatte besteht die Schaltung nicht nur aus einer Ober- und Unterseite, sondern auch aus mehreren inneren Schichten, die als Innenlagen bezeichnet werden. Diese Schichten enthalten zusätzliche Leiterbahnen, Stromversorgungs- und Masseflächen und tragen dazu bei, komplexe Schaltungen auf kleinem Raum zu realisieren.
Aufbau der Innenlagen in einer Leiterplatte:
Leiterbahnen:
- Die Innenlagen enthalten Leiterbahnen, die elektrische Verbindungen zwischen verschiedenen Komponenten der Leiterplatte herstellen. Sie sind ähnlich aufgebaut wie die Leiterbahnen auf den äußeren Schichten, jedoch in den mittleren Schichten der PCB verborgen.
Masse- und Versorgungsebenen (Power Planes):
- In vielen Fällen werden Innenlagen für Masse- oder Versorgungsspannungsebenen genutzt. Diese Ebenen bieten eine stabile Referenzspannung oder stellen den Strom für die Bauteile auf der Leiterplatte zur Verfügung. Die Nutzung von Innenlagen für Masse- und Versorgungsebenen kann die elektromagnetische Verträglichkeit (EMV) verbessern, da sie elektromagnetische Störungen reduzieren.
Isolationsmaterial:
- Die einzelnen Innenlagen sind durch Isolationsmaterialien wie Prepreg (Harz-getränkte Glasfasermatten) oder Laminat voneinander getrennt. Diese Materialien sorgen dafür, dass die verschiedenen leitenden Schichten elektrisch voneinander isoliert bleiben.
Via-Verbindungen:
- Um die Innenlagen mit den äußeren Lagen zu verbinden, werden Vias (Durchkontaktierungen) verwendet. Diese sind metallisierte Löcher, die elektrische Verbindungen zwischen den Schichten herstellen.
Vorteile von Innenlagen:
- Platzersparnis: Mehrlagige Leiterplatten mit Innenlagen ermöglichen es, komplexe Schaltungen auf kleinerem Raum zu realisieren, da sich mehr Verbindungen auf mehreren Ebenen verteilen lassen.
- Verbesserte Leistung: Die Verwendung von separaten Strom- und Masseebenen auf den Innenlagen verbessert die Signalqualität und die elektromagnetische Verträglichkeit (EMV), was insbesondere bei Hochfrequenzschaltungen oder empfindlichen Schaltungen wichtig ist.
- Höhere Komplexität: Durch die Verwendung von Innenlagen können Schaltungen mit mehr Komponenten und komplexeren Signalwegen realisiert werden, was in modernen Elektronikanwendungen, wie Smartphones oder Computern, unverzichtbar ist.
Fazit:
Die Innenlagen sind ein integraler Bestandteil von mehrlagigen Leiterplatten und tragen wesentlich dazu bei, die Miniaturisierung, Leistungsfähigkeit und Komplexität moderner Elektronik zu ermöglichen. Sie bieten zusätzliche Verbindungen und Funktionen, die auf den äußeren Schichten nicht ohne weiteres untergebracht werden können.
Vgl. auch → Top → Bottom
- INNENLIEGENDE DURCHKONTAKTIERUNG
- IPC
- ISOLATIONSWIDERSTAND
- ISO 14001
- ISO 9001
Eine innenliegende Durchkontaktierung (englisch: Buried Via) ist eine spezielle Art von Via (Durchkontaktierung) in einer mehrlagigen Leiterplatte (PCB), die nur die inneren Lagen miteinander verbindet und nicht an die äußeren Lagen durchdringt. Diese Vias sind in den mittleren Schichten der Leiterplatte „vergraben“ und von außen unsichtbar.
Merkmale der innenliegenden Durchkontaktierung:
Verbindung zwischen Innenlagen:
- Buried Vias werden ausschließlich verwendet, um Verbindungen zwischen den inneren Schichten der Leiterplatte herzustellen. Sie enden an den Innenlagen und durchdringen weder die Ober- noch die Unterseite der PCB.
Isolierung durch Außenlagen:
- Da die Durchkontaktierung nicht bis zu den äußeren Lagen reicht, wird sie nach dem Laminierungsprozess der Leiterplatte von den Außenlagen isoliert.
Versteckte Struktur:
- Nach dem Zusammenbau der Schichten ist die innenliegende Durchkontaktierung nicht mehr sichtbar, was eine glatte äußere Oberfläche der Leiterplatte gewährleistet.
Vorteile der innenliegenden Durchkontaktierung:
Platzersparnis: Sie ermöglicht eine effizientere Nutzung des verfügbaren Platzes auf der Leiterplatte, da sie den Signalweg innerhalb der inneren Schichten isoliert, ohne die äußeren Schichten zu beeinflussen. Dies ist besonders nützlich bei hochdichten Leiterplatten (HDI), bei denen viele Verbindungen auf engem Raum erforderlich sind.
Reduktion der Komplexität der äußeren Schichten: Da Buried Vias nicht die äußeren Schichten durchdringen, bleibt mehr Platz auf den äußeren Lagen für andere Bauelemente oder Leiterbahnen.
Verbesserte Signalqualität: Durch die isolierte Struktur können Signale besser abgeschirmt und Interferenzen minimiert werden, was die Signalintegrität verbessert.
Nachteile der innenliegenden Durchkontaktierung:
Kostenintensiv: Die Herstellung von innenliegenden Durchkontaktierungen erfordert mehrere Laminierungs- und Bearbeitungsschritte, was die Produktionskosten und -komplexität erhöht.
Mehrere Fertigungsprozesse erforderlich: Da die Durchkontaktierungen nur in den inneren Schichten hergestellt werden, müssen diese Schichten separat gebohrt, galvanisiert und laminiert werden, bevor die äußeren Schichten hinzugefügt werden.
Anwendungsbereiche:
Innenliegende Durchkontaktierungen werden häufig in komplexen, mehrlagigen Leiterplatten verwendet, die in Hochleistungsanwendungen wie Telekommunikation, Luft- und Raumfahrt sowie bei Geräten mit hohen Anforderungen an Signalgeschwindigkeit und -integrität zum Einsatz kommen. Sie sind besonders vorteilhaft, wenn Platz und Signalqualität von entscheidender Bedeutung sind.
Fazit:
Innenliegende Durchkontaktierungen (Buried Vias) sind eine hochspezialisierte Methode zur Verbindung von Innenlagen in mehrlagigen Leiterplatten, die es ermöglicht, Platz zu sparen und die Leistungsfähigkeit der Leiterplatte zu erhöhen, jedoch mit höheren Produktionskosten verbunden ist.
Vgl. auch → Burried Via
IPC ist eine internationale Organisation, die Standards für die Herstellung von Leiterplatten (PCBs) und elektronische Baugruppen entwickelt und pflegt. Der vollständige Name lautet Institute for Printed Circuits, aber heutzutage wird die Abkürzung IPC allein verwendet. Die Organisation ist weltweit anerkannt und setzt Normen, die von Herstellern, Designern und Zulieferern der Elektronikindustrie eingehalten werden.
Aufgaben und Ziele von IPC:
Entwicklung von Standards: IPC erstellt Normen und Richtlinien, die die Qualität und Zuverlässigkeit von Leiterplatten und elektronischen Baugruppen sicherstellen. Diese Standards decken alle Aspekte der Leiterplattenproduktion und -montage ab, von Designanforderungen bis zur Endkontrolle.
Schulung und Zertifizierung: IPC bietet Schulungen und Zertifizierungen für Fachleute in der Elektronikindustrie an, um sicherzustellen, dass die in den Standards festgelegten Prozesse korrekt implementiert werden.
Förderung der Qualität: Die Normen helfen, einheitliche Qualitätsanforderungen zu gewährleisten und die Kommunikationslücken zwischen Herstellern und Kunden zu schließen. So wird sichergestellt, dass Produkte den erforderlichen Spezifikationen entsprechen.
Forschung und Entwicklung: IPC fördert die Forschung und Innovation in der Elektronikfertigung, um den technologischen Fortschritt zu unterstützen und die Best Practices in der Branche kontinuierlich zu verbessern.
Bekannte IPC-Standards:
- IPC-A-610 – Akzeptanzkriterien für elektronische Baugruppen (Visuelle Inspektion und Qualitätssicherung)
- IPC-2221 – Allgemeine Designanforderungen für Leiterplatten
- IPC-6012 – Qualifikations- und Leistungsanforderungen für starre Leiterplatten
- IPC-7711/7721 – Richtlinien für die Reparatur und Modifikation von Leiterplatten
- IPC-4562 – Kupferfolien-Dickenstandards für Leiterplatten
Bedeutung der IPC-Standards:
Die IPC-Standards sind in der Elektronikindustrie von großer Bedeutung, da sie die Grundlagen für die Gestaltung, Herstellung und Qualitätskontrolle von Leiterplatten und Baugruppen bilden. Sie helfen, globale Anforderungen und Qualitätsrichtlinien zu vereinheitlichen und ermöglichen es Unternehmen, weltweit konsistente Produkte zu liefern.
Fazit:
IPC ist eine wichtige Organisation für die Standardisierung in der Leiterplatten- und Elektronikfertigung. Die von IPC entwickelten Normen sind weltweit anerkannt und tragen maßgeblich zur Sicherung der Qualität und Zuverlässigkeit von elektronischen Produkten bei.
Der Isolationswiderstand (englisch: Insulation Resistance) bezeichnet den Widerstand eines Materials oder einer Komponente gegen den Stromfluss zwischen zwei leitfähigen Teilen, die durch einen Isolator (z. B. Luft, Kunststoff, Glasfaser) getrennt sind. Bei Leiterplatten (PCBs) beschreibt der Isolationswiderstand den Widerstand zwischen zwei leitfähigen Bereichen, beispielsweise zwischen benachbarten Leiterbahnen, Pads oder durchkontaktierten Vias, die durch das dielektrische Material der Platine voneinander isoliert sind.
Eigenschaften und Bedeutung:
Einheit: Der Isolationswiderstand wird in Ohm (Ω) gemessen, oft in hohen Bereichen, wie Megaohm (MΩ) oder Gigaohm (GΩ), da gute Isolatoren sehr hohe Widerstandswerte aufweisen.
Bedeutung für die Funktionalität: Ein hoher Isolationswiderstand ist entscheidend, um sicherzustellen, dass es keinen unerwünschten Stromfluss zwischen getrennten Schaltungen oder Bauteilen gibt. Dies ist besonders wichtig in Hochfrequenz- und Hochspannungsanwendungen, da ein zu niedriger Isolationswiderstand zu Kurzschlüssen, Fehlfunktionen und Degradation führen kann.
Faktoren, die den Isolationswiderstand beeinflussen:
- Material des Dielektrikums: Materialien wie FR4 (glasfaserverstärktes Epoxidharz) oder PTFE (Teflon) bieten in der Regel hohe Isolationswiderstände.
- Feuchtigkeit: Die Feuchtigkeit im Material kann den Isolationswiderstand erheblich reduzieren, da Wasser als leitendes Medium fungieren kann.
- Verschmutzungen: Verschmutzungen, wie Staub, chemische Rückstände oder Feuchtigkeit, können den Isolationswiderstand ebenfalls verringern.
- Temperatur: Höhere Temperaturen führen in der Regel zu einer Verringerung des Isolationswiderstands, da die thermische Aktivierung den Stromfluss durch das Material erleichtert.
Messung des Isolationswiderstands:
Der Isolationswiderstand wird oft mit einem speziellen Prüfgerät gemessen, dem sogenannten Isolationswiderstandsmessgerät oder Megger, das hohe Spannungen anlegt und den resultierenden Stromfluss misst, um den Widerstand zu berechnen. Diese Messungen sind wichtig, um die Qualität und Sicherheit der Leiterplatte zu überprüfen, insbesondere in sicherheitskritischen Anwendungen wie Medizintechnik oder Luft- und Raumfahrt.
Anwendungsbereiche:
Hochspannungsanwendungen: In diesen Bereichen ist ein hoher Isolationswiderstand entscheidend, um eine sichere Trennung von stromführenden und nicht-stromführenden Bereichen zu gewährleisten.
Medizinische Geräte: In der Medizintechnik müssen Leiterplatten einen hohen Isolationswiderstand aufweisen, um elektrische Störungen oder potenziell gefährliche Leckströme zu vermeiden.
Zusammenfassung:
Der Isolationswiderstand beschreibt die Fähigkeit eines isolierenden Materials, den Stromfluss zwischen zwei leitenden Komponenten zu blockieren. Ein hoher Isolationswiderstand ist für die Zuverlässigkeit und Sicherheit elektronischer Geräte essenziell, insbesondere in Hochspannungs- und sicherheitskritischen Anwendungen.
ISO 14001 ist eine international anerkannte Norm für Umweltmanagementsysteme (UMS). Sie bietet einen Rahmen für Unternehmen, um ihre Umweltverantwortung systematisch zu steuern und kontinuierlich zu verbessern. Die Norm legt Anforderungen an ein Umweltmanagementsystem fest, das es Unternehmen ermöglicht, ihre Umweltleistung zu überwachen und negative Umweltauswirkungen zu minimieren.
Wichtige Aspekte der ISO 14001:
Umweltmanagementsystem (UMS):
- Unternehmen richten ein systematisches Managementsystem ein, um ihre Umweltziele zu verfolgen. Dies umfasst das Identifizieren und Bewerten von Umweltauswirkungen sowie das Implementieren von Maßnahmen zur Verbesserung der Umweltleistung.
Risikobasierter Ansatz:
- Die ISO 14001 ermutigt Unternehmen, Umweltaspekte und -risiken zu identifizieren, die sie beeinflussen können. Ziel ist es, potenzielle Risiken zu minimieren und Chancen zu nutzen, um die Umweltleistung zu verbessern.
Kontinuierliche Verbesserung:
- Der Ansatz der Norm basiert auf dem Plan-Do-Check-Act (PDCA)-Zyklus, der sicherstellt, dass Unternehmen kontinuierlich ihre Prozesse überprüfen, bewerten und verbessern.
Rechtliche Anforderungen:
- Unternehmen müssen sicherstellen, dass sie alle relevanten Umweltgesetze und Vorschriften einhalten. Die Norm hilft, ein System zu entwickeln, um diese Anforderungen systematisch zu überwachen und zu erfüllen.
Interne und externe Kommunikation:
- Ein wichtiges Element der ISO 14001 ist die transparente Kommunikation von Umweltzielen und -leistungen, sowohl intern (z. B. an Mitarbeiter) als auch extern (z. B. an Behörden, Kunden und die Öffentlichkeit).
Umweltaudits:
- Regelmäßige Audits und Überprüfungen der Umweltmaßnahmen und -prozesse stellen sicher, dass die Ziele der Norm eingehalten werden und das Unternehmen auf dem richtigen Weg ist, seine Umweltleistung kontinuierlich zu verbessern.
Vorteile von ISO 14001:
- Verbesserte Umweltleistung: Durch die Identifizierung und Reduzierung von Umweltauswirkungen können Unternehmen ihre Umweltleistung verbessern und nachhaltiger agieren.
- Rechtssicherheit: Unternehmen, die ISO 14001 implementieren, sind besser in der Lage, Umweltvorschriften einzuhalten und somit rechtliche Risiken zu minimieren.
- Kostenreduktion: Eine effizientere Ressourcennutzung und Abfallvermeidung kann zu erheblichen Kosteneinsparungen führen.
- Reputation und Marktchancen: Die Zertifizierung nach ISO 14001 signalisiert Kunden, Partnern und der Öffentlichkeit ein hohes Maß an Umweltbewusstsein und Verantwortung, was zu einem Wettbewerbsvorteil führen kann.
- Beteiligung der Mitarbeiter: Durch die Integration von Umweltmanagementprozessen in das tägliche Geschäftsumfeld können Mitarbeiter besser eingebunden und motiviert werden, sich aktiv an Umweltzielen zu beteiligen.
Zertifizierung nach ISO 14001:
Unternehmen können sich von unabhängigen Zertifizierungsstellen nach ISO 14001 zertifizieren lassen. Diese Zertifizierung bestätigt, dass das Unternehmen ein funktionierendes Umweltmanagementsystem eingeführt hat, das den Anforderungen der Norm entspricht.
Fazit:
Die ISO 14001 bietet einen klaren Rahmen für das Management und die Verbesserung der Umweltleistung eines Unternehmens. Die Norm hilft Organisationen, Umweltverantwortung zu übernehmen, regulatorische Anforderungen zu erfüllen und gleichzeitig wirtschaftliche Vorteile durch Effizienzgewinne und Kosteneinsparungen zu erzielen.
ISO 9001 ist eine international anerkannte Norm für Qualitätsmanagementsysteme (QMS). Sie bietet Unternehmen und Organisationen einen strukturierten Rahmen, um die Qualität ihrer Produkte und Dienstleistungen kontinuierlich zu verbessern und sicherzustellen, dass sie die Anforderungen von Kunden, rechtlichen Vorgaben und anderen Interessengruppen erfüllen.
Wichtige Aspekte der ISO 9001:
Kundenorientierung:
- Die Norm legt großen Wert auf die Bedürfnisse der Kunden und fordert, dass Unternehmen kontinuierlich darauf hinarbeiten, die Kundenzufriedenheit zu steigern. Die Ausrichtung auf den Kunden steht im Zentrum aller Qualitätsmanagementaktivitäten.
Führung und Engagement der obersten Leitung:
- ISO 9001 fordert, dass die Führungsebene das QMS aktiv unterstützt und lenkt. Die Geschäftsleitung muss die Qualitätsziele festlegen und sicherstellen, dass diese in der gesamten Organisation kommuniziert und umgesetzt werden.
Prozessorientierter Ansatz:
- Unternehmen sollen ihre Aktivitäten in Form von miteinander verknüpften Prozessen organisieren, die zur Erreichung der Qualitätsziele beitragen. Durch das Verständnis und die Steuerung dieser Prozesse können Unternehmen effizienter und effektiver arbeiten.
Risikobasiertes Denken:
- Die Norm fordert von Unternehmen, Risiken und Chancen im Zusammenhang mit ihren Prozessen zu erkennen und zu steuern. Dieser präventive Ansatz trägt dazu bei, Probleme zu vermeiden und kontinuierliche Verbesserungen zu fördern.
Kontinuierliche Verbesserung (KVP):
- ISO 9001 fördert die ständige Weiterentwicklung des Qualitätsmanagementsystems, um auf Veränderungen und Herausforderungen zu reagieren und langfristig konkurrenzfähig zu bleiben.
Faktenbasierte Entscheidungsfindung:
- Entscheidungen sollen auf der Grundlage von verlässlichen Daten und Informationen getroffen werden, um sicherzustellen, dass die Maßnahmen zur Verbesserung fundiert sind.
Beteiligung der Mitarbeiter:
- Alle Mitarbeiter eines Unternehmens sollen in das QMS eingebunden werden. Ihre Schulung und ihre aktive Beteiligung am Verbesserungsprozess sind entscheidend, um die Qualitätsziele zu erreichen.
Vorteile der ISO 9001:
- Verbesserte Produkt- und Dienstleistungsqualität: Durch die Einführung eines QMS können Unternehmen sicherstellen, dass ihre Produkte und Dienstleistungen den festgelegten Anforderungen entsprechen und eine hohe Qualität haben.
- Erhöhte Kundenzufriedenheit: Da ISO 9001 einen starken Fokus auf die Erfüllung der Kundenanforderungen legt, trägt die Implementierung der Norm dazu bei, die Kundenzufriedenheit zu steigern.
- Effizienzsteigerung: Durch die Standardisierung und Optimierung von Prozessen werden Ressourcen effizienter genutzt, was zu Kostensenkungen und einer höheren Produktivität führen kann.
- Wettbewerbsvorteil: Eine Zertifizierung nach ISO 9001 kann das Vertrauen von Kunden und Geschäftspartnern stärken und Unternehmen im Wettbewerb einen Vorteil verschaffen.
- Risikomanagement: ISO 9001 hilft Unternehmen, potenzielle Risiken frühzeitig zu erkennen und proaktiv zu steuern, was zu einer stabileren und robusteren Organisation führt.
Zertifizierung nach ISO 9001:
Unternehmen, die ein Qualitätsmanagementsystem gemäß den Anforderungen von ISO 9001 implementieren, können sich von unabhängigen Zertifizierungsstellen zertifizieren lassen. Die Zertifizierung bestätigt, dass das Unternehmen die Normanforderungen erfüllt und kontinuierlich daran arbeitet, seine Qualität zu verbessern.
Fazit:
ISO 9001 bietet Unternehmen einen klaren und strukturierten Ansatz zur Sicherstellung und Verbesserung ihrer Qualität. Die Norm hilft dabei, Prozesse zu optimieren, Risiken zu managen, die Kundenzufriedenheit zu steigern und die Wettbewerbsfähigkeit zu stärken. Sie wird weltweit in verschiedensten Branchen angewendet und ist ein bedeutendes Qualitätsmanagementwerkzeug für Unternehmen aller Größen.
- KANTENMETALISERUNG
- KAPTON
- KEEPOUT
- KERBRITZEN
Anwendungen der Kantenmetallisierung:
Mechanische Stabilität und Schutz:
- Die metallisierten Kanten verleihen der Leiterplatte zusätzliche Stabilität und schützen die Leiterbahnen vor äußeren Einflüssen oder Beschädigungen.
Leitfähigkeit zwischen verschiedenen Ebenen:
- In mehrlagigen Leiterplatten ermöglicht die Kantenmetallisierung eine Verbindung zwischen den Schichten an den Rändern der Platine, was für spezielle Designanforderungen hilfreich sein kann.
Verbesserte Abschirmung:
- Die Kantenmetallisierung hilft dabei, elektromagnetische Interferenzen (EMI) zu reduzieren und eine bessere Abschirmung zu gewährleisten, was in Hochfrequenz- und Hochleistungsanwendungen wichtig ist.
Verbindungsmöglichkeiten:
- Bei Steckverbindungen oder bei besonderen Gehäuseanforderungen werden metallisierte Kanten genutzt, um elektrische Kontaktpunkte an den Rändern der Leiterplatte bereitzustellen.
Herstellungsprozess:
Die Kantenmetallisierung erfolgt in mehreren Schritten:
Fräsen und Vorbereiten der Kanten:
- Die Kanten der Leiterplatte werden präzise gefräst und bearbeitet, um eine saubere Oberfläche für die Metallisierung vorzubereiten.
Auftragen einer Metallbeschichtung:
- Ähnlich wie bei der Durchkontaktierung von Bohrlöchern wird die Metallbeschichtung auf die Kanten aufgetragen, typischerweise durch Galvanisierung oder chemische Verfahren.
Veredelung der Oberfläche:
- Die Metallisierung wird anschließend weiter behandelt, um eine optimale Leitfähigkeit und Haltbarkeit zu gewährleisten. Dies kann auch durch zusätzliche Veredelungsprozesse wie Gold- oder Silberbeschichtungen geschehen.
Vorteile:
- Bessere elektrische Verbindungen entlang der Kanten.
- Erhöhte mechanische Stabilität und Schutz der Platine.
- Verbesserte Abschirmung gegen elektromagnetische Störungen.
Die Kantenmetallisierung ist eine spezialisierte Technik, die in fortgeschrittenen Leiterplatten-Designs angewendet wird, insbesondere in hochleistungsfähigen oder kritischen Anwendungen wie in der Luftfahrt, der Telekommunikation oder der Automobilindustrie.
Vgl. auch → halboffene Durchkontaktierung
Eigenschaften von Kapton:
Hohe Temperaturbeständigkeit:
- Kapton kann extremen Temperaturen standhalten, oft bis zu 260 °C (500 °F), was es ideal für Anwendungen macht, bei denen hohe Temperaturen auftreten können.
Chemische Beständigkeit:
- Das Material ist resistent gegen viele chemische Substanzen, einschließlich Lösungsmittel, Öle und Kraftstoffe, was es zu einer zuverlässigen Wahl für anspruchsvolle Umgebungen macht.
Elektrische Isolierung:
- Kapton hat hervorragende isolierende Eigenschaften, die es in elektrischen Anwendungen nützlich machen, insbesondere in Hochspannungsanwendungen.
Geringes Gewicht:
- Kapton ist ein leichtes Material, was es ideal für Anwendungen in der Luft- und Raumfahrt sowie in tragbaren Geräten macht.
Flexibilität:
- Kapton kann in verschiedenen Dicken und Formen hergestellt werden, einschließlich flexibler Folien, die sich gut für die Verwendung in flexiblen Leiterplatten eignen.
Anwendungen von Kapton:
Flexible Leiterplatten:
- Kapton wird häufig als Substratmaterial für flexible Leiterplatten verwendet, da es die notwendigen elektrischen und thermischen Eigenschaften bietet.
Isolierung:
- Es wird in der elektrischen Isolierung von Kabeln und Komponenten eingesetzt, insbesondere in Hochtemperatur- oder Hochspannungsanwendungen.
Schutzschichten:
- Kapton-Folien dienen als Schutzschichten für elektronische Komponenten, um sie vor mechanischen und chemischen Einflüssen zu schützen.
Luft- und Raumfahrt:
- In der Luft- und Raumfahrtindustrie wird Kapton wegen seiner hohen Temperaturbeständigkeit und Zuverlässigkeit in extremen Umgebungen eingesetzt, z. B. in Satelliten und Raumsonden.
Drucksensoren und Thermoelemente:
- Kapton wird in speziellen Sensoren und thermischen Anwendungen verwendet, da es eine gute Wärmeleitfähigkeit und Stabilität aufweist.
Fazit:
Kapton ist ein vielseitiges und leistungsstarkes Material, das aufgrund seiner hervorragenden Eigenschaften in einer Vielzahl von technischen Anwendungen, insbesondere in der Elektronik und der Luft- und Raumfahrt, eingesetzt wird. Die Kombination aus Temperaturbeständigkeit, chemischer Resistenz und elektrischer Isolierung macht es zu einer idealen Wahl für anspruchsvolle Anwendungen.
Keepout ist ein Begriff, der in der Leiterplatten-Design- und Fertigungsindustrie verwendet wird. Er bezieht sich auf bestimmte Bereiche auf einer Leiterplatte, in denen keine Komponenten, Leiterbahnen oder andere Designelemente platziert werden dürfen. Diese Bereiche sind häufig aus mehreren Gründen erforderlich:
Gründe für Keepout-Zonen:
Mechanische Einschränkungen:
- Bestimmte Bereiche der Leiterplatte können physikalische Einschränkungen aufweisen, wie z. B. Bohrungen, Ausschnitte oder mechanische Halterungen, in denen keine zusätzlichen Elemente platziert werden dürfen.
Elektromagnetische Verträglichkeit (EMV):
- Um Interferenzen zwischen verschiedenen Signalen zu minimieren, werden Keepout-Zonen eingerichtet, die die Platzierung von Komponenten in der Nähe sensibler Bereiche verhindern.
Wärmeableitung:
- In Zonen, in denen hohe Wärmeentwicklung zu erwarten ist, kann es notwendig sein, bestimmte Bereiche freizuhalten, um die Wärmeverteilung zu optimieren und Überhitzung zu vermeiden.
Zugänglichkeit für Lötstellen oder Wartung:
- Bestimmte Bereiche müssen möglicherweise frei bleiben, um einen einfachen Zugang für Lötarbeiten, Reparaturen oder Wartung zu gewährleisten.
Vermeidung von Kurzschlüssen:
- Keepout-Zonen können auch dazu dienen, das Risiko von Kurzschlüssen zwischen benachbarten Leiterbahnen oder Bauteilen zu reduzieren.
Implementierung von Keepout-Zonen:
CAD-Software: In modernen Leiterplattendesign-Software werden Keepout-Zonen typischerweise als spezielle Layer definiert, die während des Designprozesses berücksichtigt werden. Diese Zonen werden im Design-Layout deutlich gekennzeichnet, um sicherzustellen, dass Designer und Ingenieure sie beachten.
Design-Richtlinien: Viele Unternehmen und Hersteller haben spezifische Richtlinien für die Größe und Platzierung von Keepout-Zonen, die in den Designregeln ihrer Leiterplatten-Layoutsoftware festgelegt sind.
Fazit:
Keepout-Zonen sind ein wichtiger Bestandteil des Leiterplattendesigns, um die Funktionalität, Zuverlässigkeit und Sicherheit der finalen Produkte zu gewährleisten. Sie helfen, potenzielle Probleme zu vermeiden, die durch unbedachte Platzierungen von Komponenten und Leiterbahnen verursacht werden könnten.
Kerbritzen ist ein Verfahren, das in der Leiterplattenfertigung verwendet wird, um die Oberfläche von Leiterplatten zu veredeln und gleichzeitig deren elektrische Eigenschaften zu verbessern. Es handelt sich dabei um einen speziellen Prozess, der typischerweise bei der Herstellung von Leiterplatten mit hochpräzisen Anforderungen eingesetzt wird.
Eigenschaften und Vorteile von Kerbritzen:
Verbesserte Haftung:
- Kerbritzen sorgt für eine bessere Haftung zwischen der Leiterplatte und den darauf platzierten Bauteilen, was die Zuverlässigkeit der Verbindungen erhöht.
Erhöhte Korrosionsbeständigkeit:
- Durch die spezielle Behandlung werden die Leiterplatten widerstandsfähiger gegen korrosive Umgebungen, was ihre Lebensdauer verlängert.
Optimierte elektrische Eigenschaften:
- Kerbritzen kann die elektrischen Eigenschaften der Leiterplatte verbessern, insbesondere in Bezug auf die Leitfähigkeit und Isolation.
Feine Strukturen:
- Der Prozess ermöglicht die Schaffung von feinen Strukturen auf der Leiterplatte, die für hochdichte Anwendungen erforderlich sind.
Gleichmäßige Beschichtung:
- Kerbritzen gewährleistet eine gleichmäßige und kontrollierte Beschichtung der Leiterplatte, was zu einer konsistenten Qualität führt.
Anwendungen:
- Hochfrequenzanwendungen: Leiterplatten, die in der Hochfrequenztechnik verwendet werden, profitieren oft von den verbesserten elektrischen Eigenschaften durch Kerbritzen.
- Medizintechnik: In der Medizintechnik werden hohe Anforderungen an die Zuverlässigkeit und Haltbarkeit von Leiterplatten gestellt, weshalb Kerbritzen hier häufig angewendet wird.
- Luft- und Raumfahrt: In der Luft- und Raumfahrtindustrie werden Leiterplatten mit Kerbritzen veredelt, um den extremen Bedingungen standzuhalten, die während des Einsatzes auftreten können.
Fazit:
Kerbritzen ist ein wichtiger Schritt in der Leiterplattenfertigung, um die Qualität und Langlebigkeit von Leiterplatten zu erhöhen. Durch die Verbesserung der Haftung, Korrosionsbeständigkeit und elektrischen Eigenschaften trägt es dazu bei, die Gesamtleistung und Zuverlässigkeit von elektronischen Bauteilen zu optimieren.
Vgl. auch → Ritzen
Siehe → Steg
- KITTING
- KRIECHSTROMFESTIGKEIT
- KUPFER
Kitting ist ein Begriff, der in der Fertigungs- und Montageindustrie, insbesondere in der Elektronik- und Leiterplattenfertigung, verwendet wird. Er bezieht sich auf den Prozess der Zusammenstellung und Verpackung von Komponenten und Materialien, die für die Produktion oder Montage eines bestimmten Produkts erforderlich sind.
Eigenschaften und Vorteile von Kitting:
Effizienzsteigerung:
- Kitting optimiert den Fertigungsprozess, indem alle benötigten Teile und Materialien für eine bestimmte Baugruppe oder ein Produkt in einem Kit gesammelt werden. Dies reduziert die Zeit, die für die Suche nach einzelnen Komponenten aufgewendet wird.
Fehlerreduzierung:
- Durch das Zusammenstellen aller erforderlichen Teile in einem Kit wird das Risiko verringert, dass beim Zusammenbau Teile fehlen oder falsche Komponenten verwendet werden.
Kostenreduktion:
- Kitting kann die Lagerhaltungskosten senken, da weniger Platz für die Lagerung einzelner Komponenten benötigt wird. Außerdem kann es zu besseren Einkaufskonditionen kommen, wenn größere Mengen von Komponenten im Vorfeld beschafft werden.
Optimierung des Arbeitsablaufs:
- Kitting ermöglicht einen reibungsloseren Produktionsablauf, da die Arbeiter alle benötigten Teile auf einmal erhalten und nicht unterbrochen werden müssen, um fehlende Teile zu suchen.
Flexibilität:
- Kitting kann an spezifische Produktionsbedürfnisse angepasst werden. Unternehmen können Kits für unterschiedliche Produkte oder Varianten erstellen, was die Anpassung an wechselnde Marktanforderungen erleichtert.
Anwendungen:
Elektronikfertigung: In der Elektronikindustrie werden Kits häufig für die Bestückung von Leiterplatten verwendet, bei denen alle erforderlichen Bauteile in einem Paket zusammengestellt werden, um den Montageprozess zu vereinfachen.
Automobilindustrie: In der Automobilproduktion werden Kitting-Methoden verwendet, um sicherzustellen, dass alle Teile für die Montage eines Fahrzeugs effizient bereitgestellt werden.
Medizintechnik: Kitting wird auch in der Medizintechnik eingesetzt, wo es entscheidend ist, dass alle erforderlichen Komponenten für medizinische Geräte schnell und effizient zusammengeführt werden.
Fazit:
Kitting ist ein effektives Verfahren zur Optimierung von Fertigungs- und Montageprozessen. Durch die Zusammenstellung aller erforderlichen Komponenten in einem Kit wird die Effizienz gesteigert, Fehler werden reduziert und die Kosten können gesenkt werden. Diese Methode ist besonders vorteilhaft in Branchen mit hohen Anforderungen an Präzision und Geschwindigkeit, wie der Elektronik- und Leiterplattenfertigung.
Kriechstromfestigkeit ist ein wichtiger Begriff in der Elektrotechnik und Materialwissenschaft, der die Fähigkeit eines Materials beschreibt, elektrische Isolation bei hoher Feuchtigkeit oder unter bestimmten Umgebungsbedingungen aufrechtzuerhalten. Sie bezieht sich insbesondere auf die Fähigkeit eines Materials, den unerwünschten Fluss von elektrischem Strom (Kriechstrom) über die Oberfläche oder durch die Isolierung zu verhindern.
Wichtige Aspekte der Kriechstromfestigkeit:
Definition:
- Kriechstrom ist der elektrische Strom, der entlang der Oberfläche eines Isolators fließt. Dieser Fluss kann durch Verunreinigungen, Feuchtigkeit oder andere Umwelteinflüsse gefördert werden.
Messung:
- Die Kriechstromfestigkeit wird durch die Messung der Kriechstromstrecke (Kriechstromweg) und der Oberflächenbeschaffenheit des Materials bestimmt. Dabei spielen Faktoren wie Temperatur, Feuchtigkeit und die Art des Materials eine Rolle.
Bedeutung in der Praxis:
- In der Elektronik und Elektrotechnik ist die Kriechstromfestigkeit entscheidend, um Kurzschlüsse und andere elektrische Probleme zu vermeiden. Materialien mit hoher Kriechstromfestigkeit sind besonders wichtig in Anwendungen, die extremen Bedingungen ausgesetzt sind, wie in der Luft- und Raumfahrt, Automobilindustrie und Medizintechnik.
Materialien:
- Typische Materialien, die gute Kriechstromfestigkeit aufweisen, sind spezielle Kunststoffe, Keramiken und Glas. In Leiterplatten können Beschichtungen oder Materialien mit hoher Kriechstromfestigkeit verwendet werden, um die Zuverlässigkeit zu erhöhen.
Normen und Standards:
- Die Kriechstromfestigkeit von Materialien wird oft durch Normen wie die IEC 60112 (International Electrotechnical Commission) geregelt, die spezifische Tests und Kriterien zur Bestimmung der Kriechstromfestigkeit festlegt.
Fazit:
Die Kriechstromfestigkeit ist ein entscheidender Faktor für die Sicherheit und Zuverlässigkeit elektrischer Bauteile und Systeme. In der Leiterplattenfertigung und der allgemeinen Elektronik ist es wichtig, Materialien auszuwählen, die eine hohe Kriechstromfestigkeit aufweisen, um die langfristige Leistung und Sicherheit von Geräten zu gewährleisten.
Vgl. auch → CTI-Wert → FR4
Kupfer ist ein chemisches Element mit dem Symbol Cu und der Ordnungszahl 29. Es gehört zur Gruppe der Übergangsmetalle und ist eines der ältesten und am häufigsten verwendeten Metalle in der Geschichte der Menschheit. Hier sind einige wichtige Aspekte und Eigenschaften von Kupfer, insbesondere in Bezug auf die Elektronik und Leiterplatten:
Eigenschaften von Kupfer:
Leitfähigkeit:
- Kupfer hat eine hervorragende elektrische Leitfähigkeit, die nur von Silber übertroffen wird. Dies macht es zum bevorzugten Material für elektrische Leitungen und Leiterplatten, da es den Strom effizient leitet.
Wärmeleitfähigkeit:
- Neben seiner elektrischen Leitfähigkeit hat Kupfer auch eine hohe Wärmeleitfähigkeit, was es ideal für Anwendungen macht, bei denen Wärme abgeleitet werden muss, wie z. B. in Kühlkörpern.
Korrosionsbeständigkeit:
- Kupfer hat eine gewisse natürliche Korrosionsbeständigkeit, die jedoch durch Umwelteinflüsse, insbesondere Feuchtigkeit und aggressive Chemikalien, beeinträchtigt werden kann. In vielen Anwendungen wird daher eine Oberflächenbeschichtung wie Gold oder Zinn aufgebracht, um die Korrosionsbeständigkeit zu erhöhen.
Duktilität und Formbarkeit:
- Kupfer ist ein sehr duktiles Material, das leicht in Drähte gezogen oder in verschiedene Formen gebracht werden kann, ohne zu brechen.
Antimikrobielle Eigenschaften:
- Kupfer hat natürliche antimikrobielle Eigenschaften, die das Wachstum von Bakterien und anderen Mikroben hemmen. Dies macht es nützlich in medizinischen Anwendungen.
Verwendung von Kupfer in der Elektronik:
Leiterplatten:
- In der Leiterplattenfertigung wird Kupfer verwendet, um die elektrischen Verbindungen zwischen den verschiedenen Bauteilen zu schaffen. Kupfer wird auf die Leiterplatte aufgebracht, meist in Form von dünnen Schichten, die dann geätzt werden, um die gewünschten Leiterbahnen zu erstellen.
Verbindungselemente:
- Kupfer wird auch häufig in Verbindungselementen wie Lötstellen, Steckverbindern und anderen elektrischen Komponenten verwendet.
Kabel und Drähte:
- Kupferdrähte sind in der Elektronik und Elektrotechnik weit verbreitet, da sie eine hohe Leitfähigkeit und Flexibilität bieten.
Fazit:
Kupfer ist ein essentielles Material in der Elektronik und der Leiterplattenherstellung aufgrund seiner hervorragenden elektrischen und thermischen Eigenschaften. Seine Vielseitigkeit und Wirksamkeit machen es zu einem der wichtigsten Metalle in der modernen Technik.
Vgl. auch → Kupferdicke → Kupferverteilung → Verwölbungen/Verwirrungen
- KUPFERAUFBAU
- KUPFERDICKE
- KUPFERHAFTUNG
- KUPFERVERTEILUNG
Kupferaufbau bezieht sich auf die Anwendung von Kupfer auf Leiterplatten oder anderen elektronischen Bauteilen, um elektrische Verbindungen und Schaltungen zu schaffen. Dieser Prozess umfasst verschiedene Techniken zur Herstellung und Verstärkung von Kupferschichten, die für die Funktionalität der elektrischen Komponenten entscheidend sind. Hier sind die wichtigsten Aspekte des Kupferaufbaus:
Herstellung von Kupferstrukturen
Laminierung: Bei der Herstellung von Leiterplatten wird zunächst eine Basisfolie mit einer Kupferschicht laminiert. Diese Kupferschicht dient als Grundlage für die spätere Gestaltung der elektrischen Verbindungen.
Ätzen: Nach der Laminierung wird ein Ätzprozess durchgeführt, bei dem unerwünschte Kupferbereiche entfernt werden, um die gewünschten Leiterbahnen und Pads zu formen. Dies erfolgt häufig mithilfe von Fotolithografie, bei der lichtempfindliche Chemikalien (Photoresist) verwendet werden.
Verstärkung des Kupferaufbaus
Galvanischer Kupferaufbau: Um die Dicke der Kupferschicht zu erhöhen, wird ein galvanisches Verfahren eingesetzt. Dabei wird eine dünne Kupferschicht durch elektrochemische Ablagerung auf der Leiterplatte verstärkt. Dies verbessert die elektrischen Eigenschaften und die Haltbarkeit der Leiterbahnen.
Dickkupfertechnologie: Bei Anwendungen, die eine hohe Stromtragfähigkeit erfordern, wird Dickkupfertechnik eingesetzt, bei der Kupferdicken von mehr als 105 µm aufgebracht werden. Dies ist besonders wichtig für Hochstromanwendungen und Leistungsbauelemente.
Oberflächenbehandlung
- Verzinnung oder Veredelung: Nach dem Kupferaufbau kann eine Oberflächenbehandlung erfolgen, um Korrosionsbeständigkeit und Lötbarkeit zu verbessern. Häufig verwendete Methoden sind das Verzinnen oder die chemische Vergoldung.
Anwendungen
Leiterplatten: Kupferaufbau ist besonders wichtig für die Herstellung von gedruckten Leiterplatten (PCBs), die in nahezu allen elektronischen Geräten verwendet werden.
Hochfrequenzanwendungen: In der Hochfrequenztechnik werden speziell gestaltete Kupferstrukturen verwendet, um Signalverluste zu minimieren.
Wärmemanagement: Kupfer wird auch in Kühlkörpern und Wärmeleitplatten eingesetzt, um die Wärme von empfindlichen Bauteilen abzuleiten.
Fazit
Der Kupferaufbau ist ein wesentlicher Schritt in der Leiterplattenfertigung und spielt eine entscheidende Rolle für die elektrische Leistung und Zuverlässigkeit elektronischer Geräte. Die Wahl der richtigen Technik und der Kupferdicke ist entscheidend, um die spezifischen Anforderungen der Anwendung zu erfüllen.
Vgl. auch → Galvanik → Basiskupfer → Endkupfer
Definition und Maße
Die Kupferdicke wird üblicherweise in Mikrometern (µm) angegeben. Standarddicken liegen oft zwischen 18 µm und 105 µm, wobei spezielle Anwendungen auch dickere Schichten erfordern können.
Bedeutung der Kupferdicke
- Elektrische Leistung: Eine größere Kupferdicke kann den elektrischen Widerstand verringern, was besonders in Hochstromanwendungen von Vorteil ist.
- Wärmeableitung: Dickere Kupferschichten verbessern die Wärmeableitung, was in Anwendungen mit hoher Leistungsdichte wichtig ist.
- Mechanische Stabilität: Eine höhere Dicke kann die mechanische Festigkeit der Leiterbahnen erhöhen und die Widerstandsfähigkeit gegen Verformungen oder Beschädigungen verbessern.
Anwendungsbereiche
- Standardanwendungen: Für die meisten herkömmlichen Leiterplatten wird eine Kupferdicke von 35 µm (1 oz) verwendet.
- Hochstromanwendungen: In Anwendungen wie Leistungselektronik oder Hochfrequenztechnik kann die Kupferdicke auf 105 µm (3 oz) oder mehr erhöht werden.
- Dickkupfertechnologie: Für besonders anspruchsvolle Anwendungen, die hohe Stromtragfähigkeiten erfordern, wird diese Technologie eingesetzt.
Herstellung
Die Kupferdicke wird während des Herstellungsprozesses durch verschiedene Verfahren erreicht, darunter Laminierung, Ätzen und galvanische Beschichtung.
Fazit
Die Wahl der richtigen Kupferdicke ist entscheidend für die Funktionalität und Zuverlässigkeit von Leiterplatten. Sie beeinflusst nicht nur die elektrischen Eigenschaften, sondern auch die mechanische Stabilität und die Wärmeableitung der Platine.
Vgl. auch → Strombelastung → Impedanz → Basiskupfer Endkupfer
Kupferhaftung bezieht sich auf die Fähigkeit der Kupferschichten, sicher und dauerhaft an dem Substrat oder der Dielektrikumsschicht einer Leiterplatte zu haften. Diese Haftung ist entscheidend für die Funktionalität und Langlebigkeit der elektrischen Verbindungen und Schaltungen auf der Leiterplatte. Hier sind einige wichtige Aspekte zur Kupferhaftung:
Definition und Bedeutung
Kupferhaftung beschreibt die Adhäsion zwischen der Kupferschicht und dem darunter liegenden Material. Eine starke Haftung ist wichtig, um:
- Elektrische Zuverlässigkeit: Gewährleisten, dass die elektrischen Verbindungen stabil bleiben und keine Unterbrechungen auftreten.
- Mechanische Stabilität: Die Leiterbahnen gegen mechanische Beanspruchungen wie Vibrationen oder Temperaturwechsel resistent zu machen.
- Vermeidung von Delamination: Delamination ist die Ablösung von Schichten, die durch unzureichende Haftung verursacht werden kann und die Leistungsfähigkeit der Leiterplatte beeinträchtigt.
Faktoren, die die Kupferhaftung beeinflussen
- Oberflächenvorbereitung: Die gründliche Reinigung und Behandlung der Oberfläche vor dem Aufbringen der Kupferschicht sind entscheidend, um eine gute Haftung zu gewährleisten.
- Laminierungsverfahren: Die Art und Weise, wie das Kupfer laminiert oder aufgebracht wird, beeinflusst die Haftung. Hochdruck- und Hochtemperatur-Laminierungsverfahren können die Haftung verbessern.
- Chemische Behandlung: Vorbehandlungsprozesse wie das Ätzen oder die Anwendung von Haftvermittlern können die Haftung zwischen dem Kupfer und dem Substrat erhöhen.
Prüfung der Kupferhaftung
Die Haftung kann durch verschiedene Tests bewertet werden, darunter:
- Schältests: Diese Tests messen die Kraft, die erforderlich ist, um die Kupferschicht von der Leiterplatte zu trennen.
- Adhäsionstests: Diese Tests bewerten, wie gut die Kupferschicht unter verschiedenen Bedingungen haftet.
Anwendungen
Die Kupferhaftung ist für alle Arten von Leiterplatten wichtig, insbesondere für:
- Hochfrequenzanwendungen: Wo die Stabilität der elektrischen Verbindungen kritisch ist.
- Leistungsanwendungen: In denen hohe Ströme fließen und die mechanische Stabilität entscheidend ist.
Fazit
Die Kupferhaftung ist ein entscheidender Aspekt in der Leiterplattenfertigung, der die Zuverlässigkeit und Leistungsfähigkeit elektronischer Bauteile beeinflusst. Eine gute Haftung zwischen der Kupferschicht und dem Substrat ist unerlässlich, um die Qualität und Langlebigkeit der Leiterplatten zu gewährleisten.
Vgl. auch → Flexible Leiterplatte → Polyimid → FR4
Kupferverteilung bezieht sich auf die gleichmäßige Verteilung der Kupferschichten auf Leiterplatten oder anderen elektronischen Bauteilen. Eine optimale Kupferverteilung ist entscheidend für die Funktionalität, Leistung und Zuverlässigkeit der elektrischen Verbindungen und Schaltungen. Hier sind einige wichtige Aspekte zur Kupferverteilung:
Bedeutung der Kupferverteilung
Die gleichmäßige Verteilung von Kupfer ist wichtig, um:
- Elektrische Eigenschaften: Eine gleichmäßige Kupferverteilung gewährleistet, dass die elektrischen Widerstände über die gesamte Leiterplatte konsistent sind, was die Gesamtleistung verbessert.
- Wärmeableitung: Eine gleichmäßige Dicke der Kupferschichten verbessert die Wärmeableitung und minimiert Hotspots, die zu Überhitzung führen könnten.
- Mechanische Stabilität: Eine konsistente Kupferverteilung erhöht die Festigkeit der Leiterbahnen und reduziert das Risiko von Rissen oder anderen mechanischen Defekten.
Faktoren, die die Kupferverteilung beeinflussen
- Laminierungsprozess: Die Art und Weise, wie das Kupfer aufgebracht wird, hat einen direkten Einfluss auf die Verteilung. Hoher Druck und Temperatur während der Laminierung können die gleichmäßige Verteilung fördern.
- Ätzprozess: Während des Ätzens müssen unerwünschte Kupferbereiche entfernt werden, und die Qualität dieses Prozesses beeinflusst die endgültige Verteilung der Kupferstrukturen.
- Galvanische Ablagerung: Bei galvanischen Verfahren ist die Kontrolle der Elektrolytlösung und der Stromdichte entscheidend für eine gleichmäßige Kupferverteilung.
Überwachung und Kontrolle
Die Überwachung der Kupferverteilung erfolgt durch:
- Optische Inspektion: Visuelle oder automatisierte Inspektionsmethoden zur Überprüfung der gleichmäßigen Verteilung von Kupfer auf der Leiterplatte.
- Testverfahren: Elektrische Tests, um sicherzustellen, dass die Widerstandswerte innerhalb akzeptabler Toleranzen liegen.
Anwendungen
Die Kupferverteilung ist für verschiedene Anwendungen von Bedeutung, darunter:
- Hochfrequenz- und Mikrowellenanwendungen: Wo eine konsistente Signalübertragung entscheidend ist.
- Leistungsanwendungen: In der Leistungselektronik, wo hohe Ströme fließen, ist eine gleichmäßige Verteilung von Kupfer besonders wichtig.
Fazit
Die Kupferverteilung ist ein kritischer Aspekt in der Leiterplattenfertigung, der die elektrische Leistung, Wärmeableitung und mechanische Stabilität beeinflusst. Eine sorgfältige Kontrolle und Überwachung der Kupferverteilung ist unerlässlich, um die Qualität und Zuverlässigkeit elektronischer Geräte sicherzustellen.
Vgl. auch → Verwölbung/Verwindung
- LACK
- LAGE
- LAGENAUFBAU
- LAGERBARKEIT
- LAMINIEREN
Lack in der Leiterplattentechnik bezieht sich auf schützende Beschichtungen, die auf Leiterplatten (PCBs) aufgebracht werden, um diese vor Umwelteinflüssen, mechanischen Belastungen und Korrosion zu schützen. Diese Lackschichten sind entscheidend für die Langlebigkeit und Zuverlässigkeit der elektronischen Bauteile. Es gibt verschiedene Arten von Lacken, die für unterschiedliche Zwecke verwendet werden.
Arten von Lacken
Lötstopplack: Ein spezieller Lack, der auf Leiterplatten aufgebracht wird, um die Lötflächen während des Lötvorgangs zu schützen und das Überlaufen von Lötzinn zu verhindern. Er sorgt dafür, dass nur die dafür vorgesehenen Bereiche der Leiterplatte gelötet werden.
Schutzlack: Eine dünne, transparente Schicht, die auf die gesamte Leiterplatte aufgetragen wird, um diese vor Feuchtigkeit, Chemikalien, Staub und mechanischer Abnutzung zu schützen. Solche Lacke werden häufig bei elektronischen Geräten verwendet, die extremen Umwelteinflüssen ausgesetzt sind.
Abziehlack: Eine temporäre Schutzschicht, die während der Herstellung auf bestimmte Bereiche der Leiterplatte aufgebracht wird, um diese vor Beschädigungen oder Verunreinigungen zu schützen. Nach dem Herstellungsprozess wird der Lack wieder entfernt.
Bedeutung von Lacken
Schutz: Lacke bieten Schutz vor Umwelteinflüssen wie Feuchtigkeit, Chemikalien, Staub und mechanischen Belastungen. Dies verlängert die Lebensdauer der Leiterplatte und sorgt für zuverlässige Funktion.
Elektrische Isolierung: Einige Lacke bieten auch elektrische Isolation und verhindern Kurzschlüsse zwischen den Leiterbahnen.
Optische und mechanische Stabilität: Lacke können die mechanische Festigkeit und die optische Klarheit der Leiterplatte verbessern und so helfen, die Qualität und Haltbarkeit der Platine zu sichern.
Anwendungen
Automobilindustrie: In Fahrzeugen, wo Leiterplatten oft extremen Bedingungen ausgesetzt sind, schützt Lack vor Feuchtigkeit, Hitze und Vibrationen.
Medizintechnik: In medizinischen Geräten wird Lack verwendet, um Elektronik vor Flüssigkeiten und mechanischen Einflüssen zu schützen.
Industrielle Elektronik: Bei Anwendungen, die rauen Umgebungen standhalten müssen, ist der Einsatz von Schutzlacken unerlässlich.
Fazit
Lack ist ein unverzichtbarer Bestandteil der Leiterplattenfertigung, um die Zuverlässigkeit, Lebensdauer und Funktionalität von elektronischen Geräten zu gewährleisten. Die Wahl des richtigen Lacks hängt stark von den spezifischen Anforderungen der Anwendung ab.
Vgl. auch → Lötstopplack
In der Leiterplattentechnik beschreibt der Begriff „Lage“ eine Schicht oder Ebene innerhalb einer Leiterplatte (PCB). Eine Leiterplatte kann aus mehreren Lagen bestehen, insbesondere bei Multilayer-PCBs. Jede Lage hat ihre spezifische Funktion und trägt zur elektrischen Verschaltung oder mechanischen Stabilität der gesamten Leiterplatte bei.
Arten von Lagen
Außenlagen: Diese Lagen befinden sich auf der obersten und untersten Ebene der Leiterplatte und enthalten die sichtbaren Kupferleitungen, auf denen Bauteile platziert und gelötet werden.
Innenlagen: Bei Multilayer-PCBs sind Innenlagen zwischen den Außenlagen angeordnet und enthalten zusätzliche Kupferschichten für komplexe Schaltungsverbindungen. Sie dienen der internen Verschaltung von Signalen und Strom.
Signallage: Diese Lagen enthalten die Leiterbahnen, die zur Übertragung von Signalen zwischen den Bauteilen dienen. Sie sind oft in den Außen- oder Innenlagen integriert.
Masse- und Versorgungslagen: Diese Lagen sind für die Verteilung von Masse (GND) und Betriebsspannung zuständig und helfen, das elektrische Rauschen zu minimieren und die Signalintegrität zu verbessern.
Bedeutung der Lage
Die Anzahl und Anordnung der Lagen in einer Leiterplatte beeinflussen die Leistungsfähigkeit und Komplexität eines elektronischen Geräts. Je mehr Lagen, desto mehr Signalleitungen und Versorgungsebenen können integriert werden, was zu einer besseren Funktionalität, insbesondere bei komplexen und hochdichten Schaltungen, führt.
Vgl. auch → Lagenaufbau → Bottom→ Top
Der Lagenaufbau beschreibt die Struktur und Abfolge der verschiedenen Schichten einer Leiterplatte (PCB), insbesondere bei Multilayer-PCBs. Der Aufbau der einzelnen Lagen ist entscheidend für die Funktion, elektrische Eigenschaften und mechanische Stabilität der Leiterplatte. Die Lagen einer Leiterplatte bestehen aus leitfähigen und isolierenden Materialien, die präzise miteinander verbunden werden, um elektrische Signale effizient zu leiten und die thermische sowie mechanische Belastbarkeit zu gewährleisten.
Hauptbestandteile des Lagenaufbaus
Kupferlagen: Diese leitenden Schichten enthalten die Leiterbahnen, die für die Signalübertragung und Stromversorgung zuständig sind. Sie können als Außen- oder Innenlagen fungieren.
Isolationsschichten (Dielektrikum): Diese Schichten bestehen typischerweise aus Materialien wie FR4 oder anderen Harzen, die als Trennschicht zwischen den Kupferlagen dienen. Sie isolieren die Leiterbahnen voneinander, um Kurzschlüsse zu verhindern.
Prepreg: Ein vorimprägniertes, harzbeschichtetes Glasfasermaterial, das als Bindemittel zwischen den verschiedenen Lagen dient. Es wird unter Hitze und Druck laminiert, um die einzelnen Schichten zu verbinden.
Masse- und Versorgungslagen: Spezielle Lagen, die ausschließlich der Verteilung von Masse (GND) und Versorgungsspannung dienen. Diese Lagen helfen, elektromagnetische Störungen zu minimieren und sorgen für eine stabile Stromversorgung der Bauteile.
Außenlagen: Die oberste und unterste Kupferschicht, auf der die Bauteile platziert und gelötet werden. Diese Schichten enthalten Pads, über die Verbindungen zu den Bauteilen hergestellt werden.
Typischer Lagenaufbau einer Multilayer-Leiterplatte
- Oberste Außenlage: Kupferschicht mit Bauteilen und Leiterbahnen.
- Prepreg: Isolationsmaterial zwischen den Lagen.
- Innenlagen: Kupfer für Signalverbindungen oder Masse-/Versorgungslagen.
- Kernmaterial: Harzverstärktes Glasfasergewebe (z. B. FR4), das als Träger dient.
- Weitere Prepreg-Schichten und Innenlagen: Je nach Komplexität und Anzahl der Lagen wiederholt sich der Aufbau.
- Unterste Außenlage: Letzte Kupferschicht mit Verbindungen und Pads.
Bedeutung des Lagenaufbaus
Ein durchdachter Lagenaufbau sorgt für optimale Signalintegrität, thermische Ableitung und mechanische Festigkeit. Er ist besonders wichtig in Anwendungen, bei denen Hochfrequenzsignale, hohe Stromstärken oder kompakte Bauformen erforderlich sind. Ein fehlerhafter Lagenaufbau kann hingegen zu elektrischen Störungen, Kurzschlüssen oder unzureichender Wärmeableitung führen.
Vgl. auch → Lage → Prepreg
Die Lagerbarkeit von Leiterplatten und deren Materialien bezieht sich auf die Dauer und Bedingungen, unter denen Leiterplatten und ihre Bestandteile ohne Qualitätsverlust gelagert werden können. Sie beeinflusst die Funktionalität, Zuverlässigkeit und Lötbarkeit der Leiterplatten und ist insbesondere bei sensiblen Oberflächen oder empfindlichen Bauteilen von Bedeutung.
Wichtige Faktoren für die Lagerbarkeit:
Umgebungsbedingungen: Die Lagerbedingungen wie Temperatur, Luftfeuchtigkeit und Sauberkeit spielen eine entscheidende Rolle. Hohe Luftfeuchtigkeit und Temperaturschwankungen können zu Korrosion der Kupferflächen und Oxidation führen, was die Lötbarkeit beeinträchtigt.
Oberflächenbeschaffenheit: Verschiedene Oberflächenbehandlungen (z. B. HAL, chemisches Gold, chemisches Silber) haben unterschiedliche Lagerbarkeiten. Während chemisch verzinnte Oberflächen empfindlicher auf Umweltfaktoren reagieren, bieten chemische Goldoberflächen eine höhere Beständigkeit gegen Oxidation.
Verpackung: Die richtige Verpackung, oft vakuumverpackt oder in feuchtigkeitsresistenten Beuteln, kann die Lagerdauer verlängern. Antistatische und feuchtigkeitsresistente Materialien werden häufig verwendet, um die Leiterplatten vor schädlichen Einflüssen zu schützen.
Lagerdauer: Abhängig von der Art der Leiterplatte und den Lagerbedingungen kann die Lagerfähigkeit zwischen einigen Monaten bis zu mehreren Jahren variieren. In der Regel beträgt die empfohlene Lagerzeit für Leiterplatten etwa ein Jahr, bevor die Oberflächenoxidation oder Feuchtigkeitsaufnahme ihre Qualität beeinträchtigen könnte.
Maßnahmen zur Verbesserung der Lagerbarkeit:
Trockene Lagerung: Die Lagerung in trockenen, klimatisierten Räumen mit kontrollierter Luftfeuchtigkeit und Temperatur kann die Lebensdauer der Leiterplatten verlängern.
Verpackungsschutz: Verwendung von versiegelten Verpackungen, die das Eindringen von Feuchtigkeit und Staub verhindern.
Regelmäßige Überprüfung: Lagerbestände sollten regelmäßig auf Anzeichen von Korrosion, Oxidation oder anderen Schäden überprüft werden, um rechtzeitig Maßnahmen ergreifen zu können.
Fazit
Die Lagerbarkeit von Leiterplatten ist von den Lagerbedingungen, der verwendeten Oberflächenbehandlung und der Verpackung abhängig. Eine korrekte Lagerung kann dazu beitragen, die Qualität und Funktionalität der Leiterplatten über einen längeren Zeitraum zu erhalten und Produktionsprobleme zu vermeiden.
Das Laminieren von Leiterplatten ist ein entscheidender Prozessschritt in der Herstellung von mehrlagigen Leiterplatten (Multilayer-PCBs). Beim Laminieren werden mehrere Schichten von leitfähigem Material (meist Kupfer) und isolierenden Trägerschichten (Dielektrikum) unter Hitze und Druck miteinander verbunden, um eine stabile und funktionale Leiterplatte zu schaffen.
Wichtige Aspekte des Laminierens:
Materialien: Das Laminieren erfolgt zwischen Schichten von Kupferfolie und einem dielektrischen Material wie FR4 (Flammhemmendes Epoxidharz), Polyimid oder anderen Verbundwerkstoffen. Diese Materialien bilden die Schichten einer Multilayer-Leiterplatte, wobei das Kupfer für die Leitbahnen und das Dielektrikum als Isolator dient.
Lagenaufbau: Der Lagenaufbau beschreibt die Struktur einer Leiterplatte, bei der mehrere Schichten von leitfähigen und isolierenden Materialien gestapelt und durch Laminieren zusammengehalten werden. Eine typische Multilayer-Leiterplatte kann aus 4, 6, 8 oder mehr Lagen bestehen.
Prozess des Laminierens:
- Vorbereitung: Die einzelnen Schichten der Leiterplatte werden zunächst vorbereitet. Die Kupferfolien werden durch Ätzen oder andere Techniken in die gewünschte Leiterstruktur gebracht.
- Stapelung: Die Schichten (Kupfer und Dielektrikum) werden in der gewünschten Reihenfolge gestapelt.
- Hitze und Druck: Der Stapel wird in einer Presse hohen Temperaturen und Drücken ausgesetzt. Dabei verschmilzt das Dielektrikum mit den Kupferschichten, wodurch eine feste und homogene Struktur entsteht.
- Abkühlung: Nach dem Laminieren kühlt die Struktur ab und härtet aus, wodurch die Schichten dauerhaft verbunden bleiben.
Arten des Laminierens:
- Standard-Laminierung: Bei herkömmlichen Leiterplatten wird in der Regel FR4 als Trägermaterial verwendet.
- Sequential Lamination: Dieser Prozess wird angewendet, wenn komplexe Multilayer-PCBs mit innenliegenden Durchkontaktierungen (Buried Vias) hergestellt werden. Mehrere Laminiervorgänge sind nötig, um zusätzliche Schichten zu integrieren.
- Prepreg-Laminierung: Prepreg (pre-impregnated) ist ein vorimprägniertes Material aus Glasfaser und Harz, das zwischen die Lagen gelegt wird, um die Schichten zu binden.
Vorteile des Laminierens:
Erhöhte Stabilität: Durch das Laminieren erhalten die Leiterplatten eine hohe mechanische Stabilität, was sie widerstandsfähig gegen mechanische Belastungen macht.
Multilayer-Strukturen: Der Laminierprozess ermöglicht die Herstellung von komplexen, mehrschichtigen Leiterplatten, die für moderne Hochleistungsanwendungen benötigt werden.
Miniaturisierung: Durch das Laminieren mehrerer Lagen können kompakte und leistungsstarke elektronische Geräte entwickelt werden, da viele elektrische Verbindungen auf kleinstem Raum untergebracht werden können.
Fazit
Das Laminieren ist ein unverzichtbarer Schritt in der Produktion moderner Leiterplatten, insbesondere für Multilayer-PCBs. Es gewährleistet die stabile Verbindung der Schichten und beeinflusst direkt die mechanische Festigkeit, Zuverlässigkeit und Funktionalität der fertigen Leiterplatte.
Vgl. auch → Multilayer → Prepreg
- LANGLÖCHER
- LASERDIREKTBELICHTER
- LAYER
- LAYOUT
- LAYOUTSOFTWARE
Langlöcher sind längliche, ovale Bohrungen, die in Leiterplatten eingebracht werden, um spezielle Anforderungen zu erfüllen, die runde Bohrungen nicht abdecken können. Sie dienen vor allem dazu, mechanische Bauteile oder Komponenten mit ungewöhnlichen Anschlussformen aufzunehmen und zu fixieren.
Wichtige Aspekte von Langlöchern:
Mechanische Befestigung: Langlöcher werden oft verwendet, um Bauteile mit größeren oder nicht runden Pins oder Anschlüssen zu befestigen. Sie ermöglichen eine präzise Ausrichtung und Flexibilität bei der Montage von Komponenten.
Anpassungsfähigkeit: Durch die längliche Form bieten Langlöcher mehr Flexibilität als herkömmliche runde Bohrungen, insbesondere wenn eine genaue Positionierung notwendig ist oder Toleranzen bei der Montage berücksichtigt werden müssen.
Fertigungstechniken:
- Fräsen: Langlöcher werden in der Regel gefräst, da herkömmliche Bohrverfahren nicht für die Herstellung von nicht-runden Öffnungen geeignet sind.
- Bohrungs-Spezifikationen: Je nach Anforderung und Design der Leiterplatte können die Abmessungen und Toleranzen der Langlöcher stark variieren.
Metallisierung: In vielen Fällen werden Langlöcher, wie auch runde Bohrungen, metallisiert, um eine elektrische Verbindung zwischen verschiedenen Schichten der Leiterplatte zu ermöglichen.
Anwendungsgebiete:
- Langlöcher kommen häufig bei der Bestückung von Komponenten zum Einsatz, die breitere oder flache Anschlusspins haben, wie bei bestimmten Steckverbindern, Leistungselektronikbauteilen oder Transformatoren.
- Sie können auch in der mechanischen Konstruktion der Leiterplatte verwendet werden, um beispielsweise Schrauben oder andere Befestigungselemente aufzunehmen.
Vorteile von Langlöchern:
Erhöhte Flexibilität: Sie erlauben eine größere Bewegungsfreiheit und Anpassungsfähigkeit bei der Montage von Bauteilen.
Stabilität und Passgenauigkeit: Langlöcher bieten eine sichere Befestigungsmöglichkeit für Komponenten mit spezifischen mechanischen Anforderungen und tragen zur strukturellen Integrität der Baugruppe bei.
Fazit
Langlöcher sind ein wichtiger Bestandteil bei der Gestaltung und Herstellung von Leiterplatten, wenn es um spezielle mechanische und elektrische Anforderungen geht. Sie bieten eine vielseitige und flexible Lösung für die Befestigung und Ausrichtung von Komponenten auf der Platine.
Ein Laserdirektbelichter (LDI, Laser Direct Imaging) ist ein hochpräzises Gerät, das in der Leiterplattenherstellung zur Belichtung von Fotolacken direkt auf die Leiterplatte eingesetzt wird, ohne dass herkömmliche Fotomasken erforderlich sind. Es handelt sich um eine moderne und effiziente Technologie, die besonders in der Herstellung von komplexen und hochdichten Leiterplatten verwendet wird.
Wichtige Aspekte des Laserdirektbelichters:
Direkte Belichtung: Im Gegensatz zur traditionellen Methode, bei der eine Fotomaske verwendet wird, wird beim LDI-Verfahren der Fotolack direkt mit einem präzisen Laserstrahl belichtet. Dies erhöht die Genauigkeit und Flexibilität des Produktionsprozesses.
Hohe Auflösung: Die Laserbelichtung ermöglicht es, extrem feine Strukturen und enge Leiterbahnen mit hoher Präzision auf die Leiterplatte zu bringen. Dies ist besonders vorteilhaft bei der Produktion von HDI-Leiterplatten (High Density Interconnect) und anderen hochdichten Schaltungen.
Flexibilität bei Designänderungen: Da keine physische Maske benötigt wird, können Designänderungen schnell und kosteneffizient implementiert werden. Die Änderung erfolgt einfach durch Anpassung der digitalen Daten, die den Laser steuern.
Materialkompatibilität: Der LDI-Prozess ist mit verschiedenen Fotolacken und Basismaterialien kompatibel, was eine größere Vielseitigkeit in der Produktion ermöglicht.
Vorteile des Laserdirektbelichters:
Präzision: Die Möglichkeit, sehr feine Strukturen zu belichten, ermöglicht die Herstellung von hochkomplexen und miniaturisierten Schaltungen.
Schnelligkeit: Da keine Masken vorbereitet werden müssen, kann der Produktionsprozess erheblich beschleunigt werden. Dies ist besonders nützlich bei Prototypen oder kleinen Serien.
Kostenersparnis: Für kleinere Produktionsläufe oder häufige Designänderungen spart der Verzicht auf Fotomasken Zeit und Kosten.
Umweltfreundlicher: Da keine Masken und Chemikalien für die Maskenproduktion verwendet werden, trägt der LDI-Prozess zur Reduzierung von Abfallprodukten und Umweltschadstoffen bei.
Anwendungen:
HDI-Leiterplatten: Der LDI ist ideal für Leiterplatten mit hoher Dichte und komplexen Schaltkreisen, die eine sehr feine Struktur und enge Toleranzen erfordern.
Flexible Leiterplatten: Der LDI-Prozess kann auch für flexible Leiterplatten verwendet werden, da er präzise und schonend arbeitet.
Prototypenfertigung: Für Prototypen oder spezielle Kleinserien eignet sich der LDI besonders gut, da Designänderungen einfach und schnell umgesetzt werden können.
Fazit
Der Laserdirektbelichter ist ein leistungsstarkes Werkzeug in der modernen Leiterplattenherstellung, das durch seine Präzision, Flexibilität und Effizienz überzeugt. Vor allem bei hochdichten und komplexen Schaltungen ermöglicht der LDI-Technologie Fortschritte in der Fertigung, die mit traditionellen Methoden schwer zu erreichen wären.
Engl. Bezeichnung für Lage. Vgl. auch → Lage
Das Layout einer Leiterplatte (PCB, Printed Circuit Board) beschreibt die Anordnung aller elektronischen Bauteile, Leiterbahnen und Verbindungen auf der Platine. Es ist der entscheidende Schritt bei der Entwicklung von elektronischen Schaltungen, der die Funktionalität, Effizienz und Herstellbarkeit einer Platine bestimmt. Das Layout beeinflusst direkt die elektrische Leistung, die mechanische Stabilität und die Kosten der Leiterplatte.
Wichtige Aspekte des Layouts:
Komponentenanordnung: Die Positionierung der Bauteile auf der Platine ist entscheidend für den Signalfluss und die Wärmeverteilung. Komponenten, die miteinander interagieren, sollten nahe beieinander platziert werden, um die Länge der Leiterbahnen zu minimieren und Signalverluste zu reduzieren.
Leiterbahnen: Diese Verbindungen transportieren elektrische Signale zwischen den Komponenten. Die Breite der Leiterbahnen und der Abstand zwischen ihnen müssen sorgfältig geplant werden, um Kurzschlüsse, Übersprechen und Signalverzögerungen zu vermeiden.
Lagenaufbau: Moderne Leiterplatten bestehen oft aus mehreren Schichten (Multilayer), um eine kompakte und effiziente Signalführung zu ermöglichen. Das Layout umfasst die Planung der Verbindungen zwischen den Schichten durch Durchkontaktierungen (Vias).
Signalintegrität: Besonders bei Hochfrequenz- und Hochgeschwindigkeitsanwendungen muss das Layout die Signalintegrität sicherstellen. Dies umfasst die Minimierung von Signalreflexionen, Übersprechen und elektromagnetischen Interferenzen (EMI).
Wärmemanagement: Komponenten, die viel Wärme erzeugen, müssen so platziert werden, dass die Wärme effektiv abgeleitet werden kann. Hier können spezielle Kupferflächen oder Kühlkörper eingeplant werden.
Schritte beim Layout-Design:
Schaltplan erstellen: Zu Beginn wird ein Schaltplan der Schaltung erstellt, der die logischen Verbindungen zwischen den Komponenten zeigt.
Platzierung der Bauteile: Basierend auf dem Schaltplan werden die Komponenten auf der Leiterplatte positioniert. Dabei wird auf eine sinnvolle Anordnung geachtet, um den Signalfluss und die thermische Effizienz zu optimieren.
Routen der Leiterbahnen: Die elektrischen Verbindungen zwischen den Komponenten werden durch Leiterbahnen realisiert. Hierbei sind die Breite der Leiterbahnen und der Abstand zwischen ihnen von großer Bedeutung, insbesondere für Hochstromanwendungen und Signalverbindungen.
Einhaltung von Designregeln: Während des Layouts müssen Designregeln wie Mindestabstände, Mindestbreiten von Leiterbahnen und andere technische Spezifikationen eingehalten werden.
Simulation und Optimierung: Vor der Fertigung kann das Layout mithilfe von Software simuliert werden, um Probleme wie Signalverluste oder Übersprechen zu erkennen und zu beheben.
Werkzeuge:
- CAD-Software: Layout-Designs werden üblicherweise mit CAD-Programmen wie Altium Designer, Eagle oder KiCad erstellt. Diese Programme bieten Werkzeuge zur Bauteilplatzierung, Leiterbahnführung und Überprüfung des Designs.
Bedeutung des Layouts:
Zuverlässigkeit: Ein gutes Layout sorgt dafür, dass die Schaltung zuverlässig und fehlerfrei arbeitet.
Kosten: Ein optimiertes Layout kann die Herstellungskosten senken, indem der Platz effizient genutzt wird und unnötige Schichten vermieden werden.
Produktion: Ein durchdachtes Layout erleichtert die Herstellung der Leiterplatte, da es die Einhaltung von Design- und Fertigungsrichtlinien sicherstellt.
Fazit
Das Layout einer Leiterplatte ist ein entscheidender Schritt bei der Elektronikentwicklung. Es erfordert technische Expertise, um sicherzustellen, dass alle elektrischen, mechanischen und thermischen Anforderungen erfüllt werden. Ein gut durchdachtes Layout führt zu einer zuverlässigen, kosteneffizienten und leistungsfähigen Leiterplatte.
Vgl. auch → PCB
Layoutsoftware für Leiterplatten (PCBs) wird verwendet, um das Design, die Platzierung von Bauteilen und die Leitung von elektrischen Verbindungen zu planen und zu simulieren. Diese Programme sind essenziell für die Entwicklung und Herstellung von elektronischen Schaltungen und bieten eine Vielzahl von Funktionen, um ein optimiertes und funktionsfähiges Design zu erstellen. Hier sind einige gängige Layoutsoftware-Lösungen sowie deren Hauptmerkmale:
Bekannte Layoutsoftware-Lösungen:
Altium Designer
- Beschreibung: Eine der führenden Softwarelösungen für das PCB-Design, die umfangreiche Funktionen für Schaltplanerstellung, Simulation, 3D-Ansichten und Layout-Optimierung bietet.
- Funktionen:
- Schaltplanerstellung und PCB-Layout
- 3D-Vorschau der Platine
- Designregelprüfung (DRC) und Fertigungsdatenexport
- Hohe Integration mit Bauteilbibliotheken und Lieferanten
- Vorteile: Umfassende Funktionen, benutzerfreundliche Oberfläche, weit verbreitet in der Industrie.
- Einsatzbereiche: Hochentwickelte Elektronik-Designs, Prototypen und Serienproduktion.
KiCad
- Beschreibung: Eine Open-Source-Software, die für Schaltplanerstellung und Leiterplattenlayout verwendet wird. Sie ist kostenlos und sehr beliebt bei Hobbyisten sowie kleinen Unternehmen.
- Funktionen:
- Mehrlagen-Designs (Multilayer-PCBs)
- 3D-Ansicht und Schaltplansimulation
- Erweiterbare Bauteilbibliotheken
- Vorteile: Kostenlos, flexibel, Open-Source, stark wachsender Support in der Community.
- Einsatzbereiche: Kleine und mittelgroße Projekte, ideal für den Einstieg.
EAGLE (Autodesk)
- Beschreibung: Eine weit verbreitete Software, die besonders bei Hobbyisten und kleineren Unternehmen beliebt ist. Sie bietet eine umfassende Bibliothek und flexible Funktionen.
- Funktionen:
- Integrierte Schaltplanerstellung und PCB-Layout
- Einfache Netlist-Verwaltung
- Automatische und manuelle Leiterbahnführung
- Große Bauteilbibliotheken
- Vorteile: Einfache Benutzeroberfläche, gute Integration mit Autodesk-Produkten.
- Einsatzbereiche: Kleine bis mittelgroße Projekte, Prototyping.
OrCAD
- Beschreibung: Eine professionelle Softwarelösung, die von Cadence entwickelt wurde und sich besonders für komplexe Designs eignet.
- Funktionen:
- Leistungsstarke Schaltplanerstellung und Layout-Werkzeuge
- Signal- und Power-Integrity-Analyse
- Erweiterte 3D-Visualisierung
- Designregelprüfung und Produktionsdatenexport
- Vorteile: Hohe Leistung für große und komplexe Designs, präzise Analysen und Simulationen.
- Einsatzbereiche: Große und komplexe Designs, speziell für die High-End-Industrie.
DipTrace
- Beschreibung: Eine benutzerfreundliche Software, die sowohl für Anfänger als auch für Profis geeignet ist. Sie bietet Schaltplan- und PCB-Design-Funktionen.
- Funktionen:
- Schaltplanerstellung und PCB-Layout
- 3D-Vorschau und Bauteilplatzierung
- Bibliotheksmanagement mit 3D-Modellen
- Benutzerfreundliche Oberfläche
- Vorteile: Intuitive Benutzeroberfläche, gute Funktionalität für kleine bis mittelgroße Projekte.
- Einsatzbereiche: Kleine bis mittlere Projekte, gut geeignet für Prototypen.
DesignSpark PCB
- Beschreibung: Ein kostenloses PCB-Design-Tool von RS Components, das eine benutzerfreundliche Oberfläche bietet und ideal für kleine bis mittelgroße Projekte ist.
- Funktionen:
- Schaltplanerstellung und Leiterplatten-Layout
- Umfangreiche Bauteilbibliotheken
- Direkter Export von Bestelllisten und Fertigungsdaten
- Vorteile: Kostenlos, einfache Integration mit Komponenten von RS Components.
- Einsatzbereiche: Kleine Projekte, Prototyping.
Wichtige Funktionen von Layoutsoftware:
- Schaltplanerstellung: Die Möglichkeit, elektrische Schaltungen in einem logischen Diagramm zu entwerfen und zu simulieren.
- PCB-Layout: Planung der physischen Anordnung der Komponenten auf der Leiterplatte, einschließlich der Leitung von Leiterbahnen.
- DRC (Design Rule Check): Automatische Überprüfung, ob das Design den technischen Vorgaben und Fertigungsregeln entspricht.
- 3D-Visualisierung: Die Software kann eine 3D-Vorschau der Platine erstellen, um mögliche Platzierungsprobleme oder Kollisionen zu erkennen.
- Bauteilbibliotheken: Integrierte Bibliotheken mit Bauteilen, die die Auswahl und Platzierung von Komponenten erleichtern.
- Gerber-Export: Die Möglichkeit, Produktionsdaten in Form von Gerber-Dateien zu exportieren, die von Leiterplattenherstellern verwendet werden.
Fazit
Layoutsoftware ist unverzichtbar für die Entwicklung und Herstellung von Leiterplatten. Je nach Projektanforderungen und Budget kann zwischen einfachen, kostenfreien Tools und hochentwickelten, kommerziellen Softwarelösungen gewählt werden. Eine gute Software sollte neben einem präzisen Layout auch die Signalintegrität, elektrische Leistung und mechanische Eigenschaften der Platine sicherstellen.
Vgl. auch → Entflechtung → Autorouter→ Schaltplan → Design Roules → Design Roule Check (DCR)
- LDI
- LEITERBAHN
- LEITERBAHNBREITE
- LEITERPLATTE
- LEITERPLATTENENTFLECHTUNG
Laser Direct Imaging (LDI) ist ein fortschrittliches Verfahren zur Herstellung von Leiterplatten (PCBs), das es ermöglicht, hochpräzise und detaillierte Designs direkt auf die Kupferoberfläche zu übertragen. Diese Technologie ersetzt traditionelle Belichtungsmethoden und bietet zahlreiche Vorteile in der Leiterplattenfertigung. Hier sind die wichtigsten Aspekte von LDI:
Verfahren
- Laserbelichtung: Beim LDI wird ein Laserstrahl verwendet, um direkt auf die lichtempfindliche Schicht der Leiterplatte zu belichten. Der Laser kann sehr präzise gesteuert werden, was die Übertragung komplexer Muster und feiner Strukturen ermöglicht.
- Photopolymerschicht: Eine lichtempfindliche Schicht wird auf die Kupferoberfläche aufgetragen. Der Laser belichtet diese Schicht und härtet sie an den gewünschten Stellen, während die nicht belichteten Bereiche entfernt werden können.
Vorteile
- Hohe Präzision: LDI ermöglicht die Erstellung von sehr feinen Leiterbahnen und Pads, die für moderne, kompakte Elektronikdesigns erforderlich sind.
- Reduzierte Fertigungszeiten: Durch den Wegfall der traditionellen Fotopositiv- und -negativverfahren wird die Produktionszeit erheblich verkürzt.
- Weniger Materialverschwendung: Da keine Filme oder Masken benötigt werden, reduziert LDI den Materialabfall und die Kosten.
- Flexibilität: Das Verfahren ermöglicht schnelle Änderungen und Anpassungen im Designprozess, was insbesondere bei Prototypen von Vorteil ist.
Anwendungen
- Hochpräzise Leiterplatten: Ideal für Anwendungen, die extrem feine Strukturen erfordern, wie beispielsweise in der Hochfrequenztechnik, der Medizintechnik und in der Luft- und Raumfahrt.
- Prototyping: LDI wird häufig für die Herstellung von Prototypen verwendet, da es schnelle Iterationen und Anpassungen ermöglicht.
- Multilayer-Boards: Bei komplexen, mehrlagigen Leiterplatten kann LDI helfen, die erforderlichen Präzision und Konsistenz zu gewährleisten.
Fazit
Laser Direct Imaging ist eine innovative Technologie in der Leiterplattenherstellung, die die Fertigungseffizienz verbessert und die Designmöglichkeiten erweitert. Durch die Möglichkeit, komplexe und präzise Designs direkt auf die Leiterplatte zu übertragen, spielt LDI eine entscheidende Rolle in der modernen Elektronikproduktion.
Leiterbahnen sind entscheidende Komponenten in der Elektronik und in der Leiterplattentechnologie. Sie dienen als elektrische Verbindungen zwischen den verschiedenen Bauteilen einer Leiterplatte (PCB) und ermöglichen die Übertragung von elektrischen Signalen und Energie. Hier sind die wichtigsten Aspekte von Leiterbahnen:
Definition und Struktur
- Leiterbahn: Eine Leiterbahn ist ein dünner Kupferstreifen, der auf der Oberfläche einer Leiterplatte aufgebracht wird. Sie verbindet elektrische Bauteile wie Widerstände, Kondensatoren und integrierte Schaltungen miteinander.
- Material: Leiterbahnen bestehen normalerweise aus Kupfer, da es ein hervorragender elektrischer Leiter ist. Die Kupferschicht wird auf das Basismaterial (häufig FR4) laminiert und anschließend durch Ätzen in die gewünschte Form gebracht.
Eigenschaften
- Breite und Dicke: Die Breite und Dicke der Leiterbahn beeinflussen die elektrischen Eigenschaften, wie den Widerstand und die Stromtragfähigkeit. Breitere Leiterbahnen können mehr Strom führen, während dickere Bahnen den Widerstand verringern.
- Impedanz: Die geometrische Anordnung der Leiterbahnen beeinflusst auch die Impedanz, was besonders in Hochfrequenzanwendungen von Bedeutung ist.
Herstellung
- Ätzen: Nach der Laminierung wird die Kupferschicht belichtet und geätzt, um die gewünschten Leiterbahnstrukturen zu erzeugen. Dies erfolgt oft durch Fotolithografie.
- Verstärkung: In einigen Fällen kann eine galvanische Beschichtung oder Dickkupfertechnologie verwendet werden, um die Dicke der Leiterbahn zu erhöhen und die Leistung zu verbessern.
Anwendungen
- Verbindungen in der Elektronik: Leiterbahnen sind in nahezu allen elektronischen Geräten zu finden, von einfachen Schaltungen bis hin zu komplexen Multilayer-Boards.
- Hochfrequenztechnik: In Hochfrequenzanwendungen werden spezielle Leiterbahngeometrien eingesetzt, um Signalverluste zu minimieren.
Fazit
Leiterbahnen sind ein zentraler Bestandteil der Leiterplattenkonstruktion und spielen eine entscheidende Rolle für die Funktionalität und Leistung elektronischer Geräte. Ihre Gestaltung und Herstellung sind von großer Bedeutung für die Zuverlässigkeit und Effizienz der gesamten Schaltung.
Vgl. auch → Lage
Die Leiterbahnbreite bezieht sich auf die Breite der Kupferstreifen, die auf einer Leiterplatte (PCB) verwendet werden, um elektrische Verbindungen zwischen den verschiedenen Bauteilen herzustellen. Die Wahl der Leiterbahnbreite ist entscheidend für die elektrische Leistung, die mechanische Stabilität und die Gesamtzuverlässigkeit der Leiterplatte. Hier sind einige wichtige Aspekte zur Leiterbahnbreite:
Definition und Maße
- Maße: Die Leiterbahnbreite wird in Millimetern (mm) oder in Mil (1 Mil = 0,001 Zoll) angegeben. Typische Breiten können von 0,1 mm (4 Mil) bis zu mehreren Millimetern reichen, abhängig von den spezifischen Anforderungen der Schaltung.
Bedeutung der Leiterbahnbreite
Stromtragfähigkeit: Eine breitere Leiterbahn kann mehr Strom führen, was für Hochstromanwendungen wichtig ist. Die maximale Stromtragfähigkeit hängt von der Breite der Leiterbahn, der Dicke des Kupfers und der Umgebungstemperatur ab.
Widerstand: Eine breitere Leiterbahn hat einen geringeren elektrischen Widerstand, was zu einer besseren Signalübertragung und weniger Wärmeentwicklung führt.
Signalqualität: Bei Hochfrequenzanwendungen kann die Breite der Leiterbahn die Impedanz beeinflussen, was die Signalintegrität beeinträchtigen kann. Daher ist eine präzise Gestaltung der Leiterbahnbreite wichtig.
Anwendungen und Designüberlegungen
Standardanwendungen: Für die meisten herkömmlichen Leiterplatten beträgt die Leiterbahnbreite typischerweise zwischen 0,3 mm und 1 mm.
Hochstromanwendungen: In Anwendungen wie Leistungselektronik oder Motorsteuerungen können breitere Leiterbahnen (über 1 mm) erforderlich sein, um die höhere Strombelastung zu bewältigen.
Design Rules: Bei der Gestaltung von Leiterplatten müssen die Designregeln (Design Rules) der verwendeten PCB-Fertigungstechnologie berücksichtigt werden. Diese Regeln legen Mindest- und Höchstbreiten für Leiterbahnen fest.
Fazit
Die Wahl der richtigen Leiterbahnbreite ist entscheidend für die Leistung und Zuverlässigkeit von Leiterplatten. Sie beeinflusst nicht nur die elektrische Leistung, sondern auch die mechanische Stabilität und die Signalübertragung in elektronischen Schaltungen. Eine sorgfältige Planung und Gestaltung ist erforderlich, um die spezifischen Anforderungen der Anwendung zu erfüllen.
Vgl. auch → Strombelastbarkeit
Eine Leiterplatte (PCB, Printed Circuit Board) ist ein zentrales Element in der Elektronik, das zur mechanischen Unterstützung und elektrischen Verbindung von elektronischen Bauteilen dient. Sie ist ein fundamentales Bauelement in nahezu allen elektronischen Geräten, von einfachen Haushaltsgeräten bis hin zu komplexen Computern. Hier sind einige wichtige Aspekte zu Leiterplatten:
Aufbau und Materialien
Schichtaufbau: Leiterplatten bestehen aus mehreren Schichten, die in der Regel aus einem isolierenden Material (z. B. FR4, ein glasfaserverstärktes Epoxidharz) und Kupferleiterbahnen bestehen. Die Anzahl der Schichten kann von einseitigen (einlagigen) bis zu mehrlagigen Leiterplatten variieren.
Kupferoberfläche: Kupfer wird verwendet, um die elektrischen Verbindungen zwischen den Bauteilen herzustellen. Diese Kupferschichten werden durch Prozesse wie Laminierung, Ätzen und galvanische Beschichtung aufgebracht.
Herstellung
Design: Der Herstellungsprozess beginnt mit dem Entwurf der Leiterplatte, der typischerweise mit spezieller Software erfolgt. Dies umfasst die Erstellung von Schaltplänen und Layouts, die die Anordnung der Bauteile und Leiterbahnen festlegen.
Fertigung: Nach dem Design wird die Leiterplatte gefertigt, was Prozesse wie Laminierung, Bohren, Ätzen und Oberflächenbehandlungen umfasst. Jeder Schritt ist entscheidend für die Qualität und Leistung der fertigen Leiterplatte.
Funktionen
Verbindungen: Leiterplatten ermöglichen die elektrische Verbindung zwischen verschiedenen Komponenten, wie Widerständen, Kondensatoren, Mikrochips und anderen Bauteilen.
Mechanische Unterstützung: Sie bieten eine stabile Grundlage, auf der elektronische Komponenten montiert werden, was die Montage und den Betrieb von Geräten erleichtert.
Anwendungen
Elektronische Geräte: Leiterplatten werden in einer Vielzahl von Anwendungen eingesetzt, einschließlich Computer, Smartphones, medizinischen Geräten, Automobilen, Haushaltsgeräten und vielen anderen elektronischen Systemen.
Spezialisierte Leiterplatten: Es gibt verschiedene Arten von Leiterplatten, wie Hochfrequenz- oder flexible Leiterplatten, die für spezielle Anwendungen entwickelt wurden, um besondere Anforderungen zu erfüllen.
Fazit
Die Leiterplatte ist ein unverzichtbarer Bestandteil moderner Elektronik. Sie spielt eine entscheidende Rolle bei der Funktionalität, Zuverlässigkeit und Leistungsfähigkeit elektronischer Geräte. Die sorgfältige Planung, das Design und die Herstellung von Leiterplatten sind entscheidend für den Erfolg elektronischer Produkte.
Vgl. auch → PCB
Die Leiterplattenentflechtung (auch als „Entflechtung“ oder „De-Coupling“ bekannt) ist ein wichtiger Prozess in der Leiterplattentechnologie, der sich auf die Optimierung von Leiterbahnen und Schaltungen auf einer Leiterplatte konzentriert. Ziel ist es, die elektrische Leistung zu verbessern und Störungen zu minimieren. Hier sind einige wesentliche Aspekte der Leiterplattenentflechtung:
Definition und Bedeutung
Entflechtung bezieht sich auf die Minimierung von unerwünschten Wechselwirkungen zwischen verschiedenen elektrischen Signalen auf der Leiterplatte. Dies ist besonders wichtig in hochfrequenten oder komplexen Schaltungen, wo sich Signale gegenseitig stören können.
Durch geeignete Entflechtung kann die Signalintegrität verbessert werden, was zu einer besseren Leistung und Zuverlässigkeit der elektronischen Geräte führt.
Techniken der Entflechtung
Trennung von Leiterbahnen: Bei der Entflechtung werden kritische Signalleitungen von Hochfrequenz- oder Stromleitungen getrennt. Dies verhindert, dass hohe Ströme oder Rauschsignale die empfindlichen Signalpfade beeinträchtigen.
Verwendung von Ground-Planes: Ein Ground-Plane kann als Schirm fungieren, um die Auswirkungen von elektromagnetischen Interferenzen zu minimieren. Durch die Schaffung eines stabilen Bezugspotentials wird die Entflechtung verbessert.
Bypassing-Kondensatoren: Das Platzieren von Bypassing-Kondensatoren in der Nähe von integrierten Schaltungen hilft, hochfrequente Störungen zu reduzieren und Spannungsschwankungen zu glätten.
Vorteile der Leiterplattenentflechtung
Verbesserte Signalqualität: Durch die Minimierung von Störungen wird die Qualität der Signale verbessert, was für die Funktion von Hochgeschwindigkeitsanwendungen entscheidend ist.
Erhöhte Zuverlässigkeit: Entflechtung trägt dazu bei, Fehler und Störungen in der Schaltung zu reduzieren, was die Zuverlässigkeit des gesamten Systems erhöht.
Energieeffizienz: Eine effektive Entflechtung kann den Stromverbrauch reduzieren und die Effizienz von Schaltungen erhöhen, insbesondere in batteriebetriebenen Geräten.
Fazit
Die Leiterplattenentflechtung ist ein wesentlicher Aspekt des Designs und der Herstellung von Leiterplatten. Durch die Implementierung geeigneter Techniken zur Entflechtung können Entwickler die Leistung, Zuverlässigkeit und Effizienz elektronischer Systeme erheblich verbessern. Ein sorgfältiges Design und die Beachtung von Entflechtungsstrategien sind entscheidend, um die Herausforderungen moderner Elektronik zu meistern.
Vgl. auch → Schaltplan
- LICHTBOGENFESTIGKEIT
- LÖTAUGE
- LÖTEN
- LÖTSTOPPLACK
- LÖTPASTE
Die Lichtbogenfestigkeit ist ein wichtiger Parameter in der Elektrotechnik und insbesondere in der Leiterplattentechnologie, der die Fähigkeit von Materialien beschreibt, elektrischen Lichtbogen- oder Überschlagphänomenen standzuhalten. Lichtbögen entstehen, wenn ein elektrischer Strom durch die Luft oder ein anderes Medium fließt, und können erhebliche Schäden an elektronischen Komponenten und Leiterplatten verursachen. Hier sind einige wesentliche Aspekte der Lichtbogenfestigkeit:
Definition und Bedeutung
Lichtbogenfestigkeit bezieht sich auf die Fähigkeit eines Materials, elektrischen Lichtbogen zu widerstehen, ohne zu versagen oder zu schmelzen. Diese Eigenschaft ist entscheidend für die Sicherheit und Langlebigkeit elektronischer Bauteile und Systeme.
Materialien mit hoher Lichtbogenfestigkeit können in Umgebungen eingesetzt werden, in denen hohe Spannungen und Ströme auftreten, ohne dass es zu gefährlichen Lichtbogenbildung kommt.
Materialien und Anwendungen
Isoliermaterialien: In der Leiterplattentechnologie kommen häufig spezielle Kunststoffe und Verbundwerkstoffe zum Einsatz, die eine hohe Lichtbogenfestigkeit aufweisen. Diese Materialien sind entscheidend für die Herstellung von Leiterplatten, die in Hochspannungsanwendungen eingesetzt werden.
Leiterplatten: Leiterplatten, die für Anwendungen in der Leistungselektronik oder im Hochspannungsbereich konzipiert sind, müssen eine hohe Lichtbogenfestigkeit aufweisen, um die Integrität der elektrischen Verbindungen zu gewährleisten.
Testmethoden
Lichtbogentest: Die Lichtbogenfestigkeit wird häufig durch spezielle Tests bewertet, bei denen Materialien einem kontrollierten elektrischen Lichtbogen ausgesetzt werden. Die Dauer und Intensität des Lichtbogens werden gemessen, um die Widerstandsfähigkeit des Materials zu bestimmen.
Dielektrische Tests: Neben Lichtbogentests können auch andere dielektrische Tests durchgeführt werden, um die elektrischen Eigenschaften und die Lichtbogenfestigkeit von Materialien zu bewerten.
Vorteile einer hohen Lichtbogenfestigkeit
Erhöhte Sicherheit: Materialien mit hoher Lichtbogenfestigkeit reduzieren das Risiko von elektrischen Schlägen und Bränden, die durch Lichtbögen verursacht werden können.
Längere Lebensdauer: Komponenten, die lichtbogenfest sind, haben eine längere Lebensdauer, da sie weniger anfällig für Schäden durch Überschläge sind.
Zuverlässigkeit: Hochleistungsanwendungen profitieren von Materialien mit hoher Lichtbogenfestigkeit, da sie die Wahrscheinlichkeit von Ausfällen verringern und die Gesamtzuverlässigkeit der Systeme erhöhen.
Fazit
Die Lichtbogenfestigkeit ist ein entscheidender Faktor für die Auswahl von Materialien in der Leiterplattentechnologie und anderen elektrischen Anwendungen. Eine sorgfältige Berücksichtigung dieser Eigenschaft kann dazu beitragen, die Sicherheit, Zuverlässigkeit und Lebensdauer elektronischer Komponenten zu gewährleisten. In einer Welt, in der elektrische Systeme zunehmend komplexer und leistungsfähiger werden, bleibt die Lichtbogenfestigkeit ein zentrales Anliegen für Ingenieure und Designer.
Vgl. auch → Lötauge
Ein Lötauge ist eine wichtige Komponente in der Leiterplattentechnologie, die als Verbindungspunkt für die Löten von Bauteilen auf der Leiterplatte dient. Es handelt sich dabei um eine metallische Fläche, die auf der Oberfläche der Leiterplatte aufgebracht ist, um eine zuverlässige elektrische Verbindung zwischen dem Bauteil und der Leiterbahn herzustellen. Hier sind einige wesentliche Aspekte des Lötauges:
Definition und Struktur
Definition: Ein Lötauge ist ein Bereich auf einer Leiterplatte, der mit einer Lötmasse versehen ist und in der Regel einen Durchmesser von 1 bis 3 mm hat. Es wird verwendet, um Anschlüsse von elektronischen Bauteilen (wie Widerständen, Kondensatoren oder ICs) an die Leiterbahnen der Leiterplatte zu verbinden.
Struktur: Lötaugen sind in der Regel aus Kupfer gefertigt und können zusätzlich mit einer Schutzschicht aus Zinn, Gold oder Nickel überzogen sein, um die Lötbarkeit und Korrosionsbeständigkeit zu verbessern.
Funktionen
Verbindung: Die Hauptfunktion des Lötauges besteht darin, eine elektrische Verbindung zwischen dem Bauteil und der Leiterplatte herzustellen, sodass elektrische Signale und Strom fließen können.
Mechanische Unterstützung: Lötaugen bieten auch mechanische Stabilität für die Bauteile, die auf der Leiterplatte montiert sind. Sie verhindern, dass die Bauteile durch Vibration oder andere mechanische Einflüsse herausgezogen werden.
Lötprozess
Löten: Beim Löten wird eine Lötlegierung (z. B. bleifreies Lot oder Zinn-Blei-Lot) erhitzt und auf das Lötauge aufgetragen, um eine feste Verbindung zwischen dem Bauteil und der Leiterplatte herzustellen. Der Lötprozess kann durch verschiedene Techniken erfolgen, wie Wellenlöten, Reflow-Löten oder Handlöten.
Qualität: Die Qualität des Lötauges und des Lötvorgangs ist entscheidend für die Zuverlässigkeit der elektrischen Verbindung. Eine unzureichende Lötung kann zu schlechten Verbindungen, Signalverlust oder sogar zu Ausfällen der gesamten Leiterplatte führen.
Designüberlegungen
Lötaugenlayout: Bei der Planung von Leiterplatten müssen die Lötaugen sorgfältig dimensioniert und positioniert werden, um eine optimale Lötbarkeit und Funktionalität zu gewährleisten. Faktoren wie der Durchmesser des Lötauges, der Abstand zwischen den Bauteilen und die Platzierung der Leiterbahnen spielen eine Rolle.
Thermische Überlegungen: Da das Löten Hitze erfordert, müssen die Lötaugen so entworfen sein, dass sie die beim Löten erzeugte Wärme effizient abführen, um eine Überhitzung der Bauteile zu vermeiden.
Fazit
Lötaugen sind essentielle Elemente in der Leiterplattenfertigung und -montage. Sie gewährleisten die elektrische Verbindung und mechanische Stabilität von Bauteilen und spielen eine entscheidende Rolle für die Funktionalität und Zuverlässigkeit elektronischer Geräte. Eine sorgfältige Gestaltung und Durchführung des Lötprozesses ist notwendig, um die Qualität der Lötverbindungen zu maximieren und die Lebensdauer der Leiterplatte zu erhöhen.
Vgl. auch → Pad
Löten ist ein wichtiger Prozess in der Elektronikfertigung, der verwendet wird, um elektrische Verbindungen zwischen Bauteilen auf Leiterplatten herzustellen. Dabei wird eine Lötlegierung, die in der Regel aus Zinn und Blei oder bleifreiem Material besteht, erhitzt und auf die Verbindungspunkte aufgetragen, um eine feste, elektrische Verbindung zu schaffen. Hier sind einige wesentliche Aspekte des Lötens:
Definition und Prozess
Definition: Löten ist ein Verfahren, bei dem zwei oder mehr metallische Teile durch Erhitzen und Aufbringen eines geschmolzenen Lötmetalls verbunden werden. Das Lötmetall fließt in die Lücken zwischen den Teilen und erstarrt, wodurch eine dauerhafte Verbindung entsteht.
Prozess: Der Lötprozess umfasst mehrere Schritte:
- Vorbereitung: Die Oberflächen der zu verbindenden Teile werden gereinigt, um Oxidation und Verunreinigungen zu entfernen.
- Erhitzen: Die Teile werden auf eine Temperatur erhitzt, die hoch genug ist, um das Lötmetall zu schmelzen, aber nicht so hoch, dass sie beschädigt werden.
- Auftragen des Lötmetalls: Das geschmolzene Lötmetall wird auf die Verbindungspunkte aufgetragen.
- Abkühlung: Das Lötmetall kühlt ab und erstarrt, wodurch die Verbindung stabil wird.
Arten des Lötens
Handlöten: Bei dieser Methode wird ein Lötkolben verwendet, um das Lötmetall manuell aufzutragen. Handlöten ist flexibel und wird häufig für Reparaturen und Prototypen eingesetzt.
Wellenlöten: Hierbei wird eine Leiterplatte über eine Welle aus geschmolzenem Lötzinn geführt. Diese Methode ist effizient für die Massenproduktion von Leiterplatten.
Reflow-Löten: Bei dieser Methode wird das Lötmetall auf die Leiterplatte aufgebracht, gefolgt von einem Erhitzen im Ofen, um das Lötmetall zu schmelzen. Diese Technik wird oft für Oberflächenmontage-Bauteile verwendet.
Qualitätskontrolle
Lötstellen: Die Qualität der Lötstellen ist entscheidend für die Funktionalität der elektrischen Verbindung. Eine gute Lötstelle sollte gleichmäßig und glänzend sein und eine ausreichende Verbindung zwischen den Bauteilen bieten.
Fehlerprüfung: Häufige Lötfehler sind kalte Lötstellen, Lötbrücken (unabsichtliche Verbindungen zwischen benachbarten Lötstellen) und unzureichende Benetzung. Diese Fehler können zu Ausfällen oder Fehlfunktionen führen.
Umweltaspekte
Bleifreies Löten: Aufgrund von Umwelt- und Gesundheitsbedenken wird in vielen Anwendungen bleifreies Lot verwendet. Diese Materialien erfordern häufig höhere Temperaturen und spezielle Verfahren, um eine optimale Lötqualität zu gewährleisten.
REACH- und RoHS-Vorgaben: Viele Länder haben Vorschriften zur Verwendung von gefährlichen Substanzen in elektronischen Geräten erlassen, was die Auswahl der Lötmaterialien beeinflusst.
Fazit
Löten ist ein unverzichtbarer Prozess in der Elektronik, der die Grundlage für die Herstellung von zuverlässigen und langlebigen elektrischen Verbindungen bildet. Die Wahl der richtigen Löttechnik und -materialien sowie die Durchführung gründlicher Qualitätskontrollen sind entscheidend, um die Funktionalität und Zuverlässigkeit von elektronischen Geräten zu gewährleisten.
Vgl. auch → Lötpaste → Selektivlöten → SMD Schablone SMT→ Wellenlöten
Lötstopplack ist eine spezielle Beschichtung, die auf Leiterplatten aufgebracht wird, um unerwünschte Lötverbindungen zu verhindern und die Haltbarkeit der Platine zu erhöhen. Diese Schicht ist entscheidend für die Qualität und Zuverlässigkeit von elektronischen Bauteilen. Hier sind einige wichtige Aspekte des Lötstopplacks:
Definition und Funktion
Definition: Lötstopplack ist eine farbige, meist grüne Beschichtung, die auf die Leiterplatte aufgetragen wird, um Bereiche zu schützen, die nicht gelötet werden sollen.
Funktion: Die Hauptfunktionen des Lötstopplacks sind:
- Schutz der Kupferoberflächen vor Oxidation und Korrosion.
- Verhinderung von Lötbrücken zwischen benachbarten Leiterbahnen.
- Reduzierung der Kontaktflächen, die beim Löten benetzt werden, was die Lötqualität verbessert.
Arten von Lötstopplacken
Photolithografische Lötstopplacke: Diese Lötstopplacke werden in einem fotolithografischen Prozess aufgebracht. Das bedeutet, dass lichtempfindliche Chemikalien verwendet werden, um das Design der Lötstopplacke präzise auf die Platine zu übertragen.
Selbstklebende Lötstopplacke: Diese Variante wird als Folie auf die Leiterplatte aufgebracht und dann mit Hitze oder Druck aktiviert.
Eigenschaften
Wärmebeständigkeit: Lötstopplacke müssen hohen Temperaturen standhalten, die beim Löten auftreten. Daher sind sie so formuliert, dass sie während des Lötprozesses stabil bleiben.
Chemische Beständigkeit: Lötstopplacke sind so konzipiert, dass sie gegen chemische Einflüsse, wie etwa Lösungsmittel und Reinigungsmittel, resistent sind.
Leitfähigkeit: Lötstopplacke sind nicht leitend, was wichtig ist, um elektrische Verbindungen nur an den gewünschten Stellen zu ermöglichen.
Anwendung
Prototypen und Massenproduktion: Lötstopplacke werden in verschiedenen Phasen der Leiterplattenherstellung angewendet, sowohl in der Prototypenfertigung als auch in der Serienproduktion.
Oberflächenmontage: In modernen Leiterplatten mit Oberflächenmontage (SMT) wird der Lötstopplack häufig eingesetzt, um die Genauigkeit der Lötverbindungen zu erhöhen und unerwünschte Lötverbindungen zu vermeiden.
Fazit
Lötstopplack ist ein wesentlicher Bestandteil der Leiterplattenfertigung, der die Qualität und Zuverlässigkeit elektronischer Geräte verbessert. Die richtige Auswahl und Anwendung von Lötstopplack können entscheidend sein, um Fehler zu vermeiden und die Lebensdauer von Leiterplatten zu verlängern.
Vgl. auch → Stopplack
Lotpaste ist ein wesentlicher Bestandteil in der Elektronikfertigung, insbesondere bei der Bestückung von Leiterplatten mit Oberflächenmontage (SMT). Sie besteht aus einer Mischung aus Lötmetall, Flussmittel und anderen Additiven und wird verwendet, um die Verbindung zwischen elektronischen Bauteilen und Leiterplatten herzustellen. Hier sind einige wichtige Aspekte der Lotpaste:
Definition und Zusammensetzung
Definition: Lotpaste ist eine viskose Substanz, die aus feinen Lötmetallpartikeln, meist aus Zinn, und Flussmittel besteht. Sie wird auf die Leiterplatte aufgetragen, um beim Löten die erforderlichen Verbindungen herzustellen.
Zusammensetzung: Die Hauptbestandteile der Lotpaste sind:
- Lötmetall: Die Metalllegierung, die die elektrische Verbindung herstellen soll, typischerweise Zinn-basiert (bleifrei oder bleihaltig).
- Flussmittel: Chemikalien, die Oxidation verhindern und das Löten erleichtern, indem sie die Oberflächenspannung des Metalls senken.
- Zusatzstoffe: Diese können verschiedene Eigenschaften beeinflussen, wie die Viskosität, die Trockenzeit und die Haftfähigkeit.
Eigenschaften
Viskosität: Lotpaste muss eine geeignete Viskosität haben, um eine präzise Anwendung zu ermöglichen, ohne dass sie beim Auftragen verläuft.
Haftfähigkeit: Die Paste sollte gut an den Bauteilen und der Leiterplatte haften, um ein Verrutschen während des Lötprozesses zu verhindern.
Lötverhalten: Eine gute Lotpaste sollte während des Lötvorgangs eine gleichmäßige Schmelze und Benetzung der Lötverbindungen gewährleisten.
Anwendung
Drucken: Lotpaste wird meist durch ein Siebdruckverfahren oder ein Stencil-Druckverfahren auf die Leiterplatte aufgebracht. Dies ermöglicht präzise und kontrollierte Mengen an Paste auf die spezifischen Pads der Leiterplatte.
Bestückung: Nach dem Auftragen der Lotpaste werden die Bauteile auf die beschichteten Bereiche platziert. Die Paste hält die Bauteile an Ort und Stelle, bis sie in den Reflow-Ofen gelangen.
Reflow-Löten: Im Reflow-Ofen wird die Lotpaste erhitzt, wodurch das Lötmetall schmilzt und eine feste Verbindung zwischen den Bauteilen und der Leiterplatte bildet.
Fazit
Lotpaste ist entscheidend für die Qualität und Zuverlässigkeit der Lötverbindungen in elektronischen Geräten. Ihre Eigenschaften und die richtige Anwendung beeinflussen direkt die Leistung und Haltbarkeit der Endprodukte. Daher ist es wichtig, hochwertige Lotpaste auszuwählen und sorgfältig anzuwenden, um optimale Ergebnisse in der Leiterplattenbestückung zu erzielen.
Vgl. auch → RoHS
- MASSE
- MASSEFLÄCHE
- MICROVIA
- MISCHBESTÜCKUNG
In der Elektronik und speziell bei Leiterplatten bezieht sich „Masse“ (englisch „Ground“ oder „GND“) auf einen Bezugspunkt im elektrischen Schaltkreis, der als Nullpotenzial definiert ist. Die Masse dient als gemeinsamer Rückführungspfad für elektrische Ströme und spielt eine wichtige Rolle in der Schaltungssicherheit und Signalverarbeitung. Hier sind einige wichtige Aspekte der Masse:
Definition und Funktion
Definition: Masse ist der Bezugspunkt oder das Nullpotenzial einer Schaltung, an den alle negativen Anschlüsse der Bauteile oder Spannungsquellen angeschlossen sind. In vielen Schaltungen wird die Masse auch als Referenz für andere Spannungen verwendet.
Funktion:
- Stromrückführung: Masse dient als Rückführungspfad für den elektrischen Strom. Alle Stromflüsse kehren durch die Masse zur Stromquelle zurück.
- Stabilität: Eine gut konzipierte Masse sorgt für stabile Spannungspegel und verhindert Störungen.
- Schirmung: Masse kann auch als Abschirmung verwendet werden, um empfindliche Signale vor elektromagnetischen Störungen (EMI) zu schützen.
Arten von Masseverbindungen
Analogmasse und Digitalmasse: In komplexen Schaltungen, insbesondere bei Mixed-Signal-Schaltungen, wird die Masse oft in Analog- und Digitalmasse unterteilt. Diese werden meist nur an einem Punkt verbunden, um Interferenzen zwischen den Signalen zu minimieren.
Schutzmasse (PE): Diese Masseart ist in Geräten mit Netzspannung wichtig und dient als Sicherheitsmaßnahme, um im Falle eines Fehlers Ströme abzuleiten und so einen elektrischen Schlag zu verhindern.
Bedeutung der Masseführung
Masseflächen: Eine große, zusammenhängende Massefläche (Ground Plane) auf der Leiterplatte sorgt für eine gute Signalrückführung und reduziert elektromagnetische Störungen. Es minimiert auch den elektrischen Widerstand und die Induktivität im Rückführungspfad.
Sternförmige Masseführung: Bei sternförmigen Masseverbindungen laufen alle Masseleitungen zu einem zentralen Punkt, um sogenannte „Masseschleifen“ zu vermeiden, die zu Störungen führen können.
Herausforderungen und Best Practices
Masseschleifen: Wenn eine Masseverbindung eine Schleife bildet, kann dies zu Störungen und Signalverzerrungen führen. Es ist wichtig, Masseschleifen durch geeignete Layout-Techniken zu vermeiden.
Signalstörungen: Eine schlechte Masseführung kann zu elektrischen Störungen und fehlerhaften Signalen führen. Deshalb muss die Masseverbindung besonders in Hochfrequenz- oder empfindlichen Analogschaltungen sorgfältig gestaltet werden.
Fazit
Masse ist eine grundlegende Komponente jeder elektronischen Schaltung. Eine sorgfältige Masseführung trägt erheblich zur Funktionalität, Zuverlässigkeit und Stabilität von Schaltungen bei. Fehler bei der Masseführung können Störungen verursachen und die Leistung der Schaltung beeinträchtigen.
Vgl. auch → GND
Die Massefläche (Ground Plane) ist eine großflächige, zusammenhängende Kupferschicht auf einer Leiterplatte, die als Referenzpotenzial (Masse oder GND) dient. Sie spielt eine entscheidende Rolle bei der Signalqualität, der elektromagnetischen Verträglichkeit (EMV) und der allgemeinen Funktionalität von elektronischen Schaltungen. Hier sind die wichtigsten Aspekte der Massefläche:
Definition und Funktion
Definition: Eine Massefläche ist eine ausgedehnte Kupferfläche, die auf einer oder mehreren Lagen einer Leiterplatte zu finden ist. Diese Fläche ist mit der Masse verbunden und bietet einen niederohmigen Rückführungspfad für elektrische Ströme.
Funktion:
- Signalrückführung: Die Massefläche stellt den Rückführungspfad für alle Signale in der Schaltung bereit. Sie minimiert den Widerstand und die Induktivität im Stromrückfluss.
- Schirmung: Sie hilft dabei, elektromagnetische Interferenzen (EMI) zu reduzieren, indem sie Signale von Störungen abschirmt.
- Stabilität: Eine gut gestaltete Massefläche verbessert die elektrische Stabilität der Schaltung und sorgt für konstante Spannungspegel.
Vorteile der Massefläche
Reduzierung von Störungen: Eine große, durchgehende Massefläche minimiert unerwünschte elektromagnetische Störungen, da sie eine effektive Abschirmung gegen äußere Einflüsse bietet.
Niedrige Impedanz: Eine Massefläche bietet einen niederohmigen Pfad für Rückströme, wodurch Spannungsverluste und Störungen im Rückweg minimiert werden.
Optimierung der Signalintegrität: Da die Rückströme in unmittelbarer Nähe der Signalleitungen fließen, werden Signalreflexionen und -verzerrungen reduziert. Dies ist besonders bei Hochfrequenzanwendungen entscheidend.
Design-Aspekte
Lagenanzahl: In mehrlagigen Leiterplatten kann eine ganze Lage als Massefläche genutzt werden. Dies verbessert die Signalqualität, indem sie eine durchgehende Masseverbindung über die gesamte Leiterplatte ermöglicht.
Durchkontaktierungen (Vias): Durchkontaktierungen verbinden verschiedene Masseflächen auf unterschiedlichen Lagen der Leiterplatte, um eine gleichmäßige Masseverbindung zu gewährleisten.
Vermeidung von Masseschleifen: Beim Design einer Massefläche ist es wichtig, Masseschleifen zu vermeiden, die Störungen verursachen können. Dazu werden alle Masseflächen sternförmig oder mit ausreichend Verbindungen gestaltet.
Anwendungsbereiche
Hochfrequenzschaltungen: In Hochfrequenzschaltungen ist eine kontinuierliche Massefläche entscheidend, um Signalreflexionen und Verluste zu minimieren.
Leistungselektronik: Hier dient die Massefläche zur effizienten Stromrückführung und zur Verbesserung der Wärmeableitung, was die Lebensdauer und Leistung der Komponenten erhöht.
Fazit
Eine gut gestaltete Massefläche ist unverzichtbar für die Funktion und Zuverlässigkeit von Leiterplatten, insbesondere in anspruchsvollen Hochfrequenz- und Leistungsschaltungen. Sie verbessert die Signalqualität, reduziert Störungen und trägt zur elektrischen Stabilität bei.
Vgl. auch → GZD → Masse → Multilayern → Stackup → Via → Wärmefallen
Microvias sind winzige, lasergebohrte Löcher auf Leiterplatten (PCBs), die elektrisch leitende Verbindungen zwischen verschiedenen Lagen herstellen. Sie werden hauptsächlich in Hochdichte-Leiterplatten (HDI-PCBs) eingesetzt, um eine hohe Packungsdichte von Komponenten und Leiterbahnen zu ermöglichen. Hier sind die wichtigsten Aspekte zu Microvias:
Definition und Eigenschaften
Definition: Ein Microvia ist ein Durchgangsloch mit einem Durchmesser von weniger als 150 µm. Im Gegensatz zu herkömmlichen Vias sind Microvias kleiner und flacher, da sie oft nur eine oder zwei Lagen verbinden.
Eigenschaften:
- Größe: Der Durchmesser eines Microvias beträgt typischerweise 50 bis 150 µm.
- Tiefe: Microvias sind flacher als herkömmliche Vias und verbinden in der Regel nur benachbarte Lagen.
- Verbindung: Sie können zwischen den äußeren und inneren Lagen sowie zwischen mehreren Innenlagen verwendet werden.
Typen von Microvias
Blind Vias: Diese verbinden die äußeren Lagen einer Leiterplatte mit den inneren Lagen, ohne durch die gesamte Platine hindurchzugehen.
Buried Vias: Diese befinden sich vollständig im Inneren der Leiterplatte und verbinden nur die inneren Lagen, ohne an die Außenseiten der Platine zu gelangen.
Herstellung
- Laserbohren: Microvias werden mit einem Laser gebohrt, der präzise, kleine Löcher in die Leiterplatte bohrt. Anschließend werden die Wände der Microvias typischerweise durch galvanische Beschichtung mit Kupfer ausgekleidet, um die elektrische Verbindung herzustellen.
Vorteile von Microvias
Höhere Packungsdichte: Durch ihre geringe Größe ermöglichen Microvias eine höhere Dichte von Leiterbahnen und Komponenten auf einer Leiterplatte, was besonders in modernen, kompakten elektronischen Geräten wichtig ist.
Verbesserte Signalqualität: Da Microvias flacher sind, verringern sie Signalverzögerungen und verbessern die Hochfrequenzleistung.
Platzersparnis: Microvias helfen dabei, Platz auf der Leiterplatte zu sparen, was die Miniaturisierung von Elektronikgeräten unterstützt.
Anwendungen
Smartphones und Tablets: Microvias sind in der Miniaturisierung von Mobilgeräten entscheidend, da sie den Platzbedarf auf der Leiterplatte reduzieren und die Dichte der Komponenten erhöhen.
Hochfrequenztechnik: In Hochfrequenzanwendungen verbessern Microvias die Signalintegrität durch geringere Verluste und kürzere Verbindungen.
Automobil- und Luftfahrtelektronik: Diese Branchen profitieren von der höheren Zuverlässigkeit und Platzersparnis, die Microvias bieten.
Fazit
Microvias sind ein wesentlicher Bestandteil moderner Leiterplattentechnologie, die es ermöglicht, leistungsfähige und kompakte elektronische Geräte herzustellen. Ihre Fähigkeit, Platz zu sparen, die Signalintegrität zu verbessern und hohe Packungsdichten zu ermöglichen, macht sie unverzichtbar in fortschrittlichen Technologien.
Vgl. auch → Aspect-Ratio → Blind Via → HDI→ Stacked Vias
Die Mischbestückung bezieht sich auf die Bestückung von Leiterplatten (PCBs) mit einer Kombination aus oberflächenmontierten Bauteilen (SMD) und durchsteckmontierten Bauteilen (THT). Diese Technik wird eingesetzt, wenn die Anforderungen an die Leiterplatte eine Mischung aus beiden Bestückungsarten erfordern, um sowohl kompakte, leistungsfähige elektronische Schaltungen als auch mechanisch stabile Verbindungen zu realisieren.
Arten von Bauteilen
SMD-Bauteile (Surface-Mounted Devices): Diese werden direkt auf die Oberfläche der Leiterplatte gelötet und sind kompakter als THT-Bauteile. Sie bieten Vorteile in Bezug auf Bauraum, Gewicht und elektrische Leistung.
THT-Bauteile (Through-Hole Technology): Diese Bauteile werden durch Löcher in der Leiterplatte gesteckt und auf der Rückseite verlötet. Sie bieten eine höhere mechanische Stabilität und werden oft für größere, schwere oder leistungshungrige Komponenten verwendet.
Vorteile der Mischbestückung
Flexibilität im Design: Die Mischbestückung ermöglicht es, eine Vielzahl von Komponenten auf einer Leiterplatte unterzubringen, um sowohl hochdichte SMD-Technologie als auch mechanisch stabile THT-Komponenten zu nutzen.
Kosteneffizienz: Für bestimmte Anwendungen, bei denen sowohl Miniaturisierung als auch mechanische Robustheit erforderlich sind, kann die Mischbestückung eine kosteneffiziente Lösung darstellen.
Leistungsfähigkeit: Die Kombination von SMD- und THT-Komponenten kann zu einer besseren Wärmeableitung und höheren Stromtragfähigkeit führen, da THT-Bauteile oft für Hochstromanwendungen verwendet werden.
Anwendungen
Industrieelektronik: Oft werden leistungsstarke Bauteile wie Transformatoren oder Relais in THT-Technologie und empfindlichere, kleinere Bauteile in SMD-Technologie bestückt.
Automobiltechnik: Hier ist oft eine robuste mechanische Stabilität durch THT-Komponenten erforderlich, während gleichzeitig platzsparende SMD-Bauteile verwendet werden, um kompakte Steuergeräte zu bauen.
Telekommunikation und Consumer-Elektronik: Die Mischbestückung ermöglicht die Integration hochdichter Elektronik mit mechanisch stabilen Bauteilen, um z.B. tragbare Geräte und Kommunikationssysteme zuverlässig und leistungsfähig zu machen.
Herstellung und Herausforderungen
Die Fertigung von Leiterplatten mit Mischbestückung erfordert spezielle Produktionsschritte:
Zwei Lötverfahren: Typischerweise wird zunächst die SMD-Bestückung in einem Reflow-Lötprozess durchgeführt, gefolgt von der THT-Bestückung, die durch Wellenlöten oder selektives Löten erfolgt.
Komplexe Fertigungsprozesse: Da beide Technologien unterschiedliche Fertigungsmethoden erfordern, ist eine genaue Planung des Produktionsprozesses entscheidend.
Fazit
Die Mischbestückung bietet eine optimale Lösung für die Integration von hochdichten SMD-Komponenten und mechanisch stabilen THT-Bauteilen auf einer Leiterplatte. Sie wird vor allem in Bereichen eingesetzt, in denen Flexibilität, Leistung und Robustheit gefragt sind.
Vgl. auch → Bestückung → SMD → THT
- MISCHNUTZEN
- MULTILAYER
- MULTINUTZEN
in Mischnutzen bezeichnet in der Leiterplattenproduktion eine Nutzentafel, die mehrere verschiedene Leiterplattentypen enthält. Im Gegensatz zu einem klassischen Nutzen, bei dem identische Leiterplatten auf einer Tafel angeordnet sind, enthält der Mischnutzen unterschiedliche Layouts und Schaltungen, um verschiedene Leiterplatten gleichzeitig zu fertigen.
Vorteile des Mischnutzens
Effizienzsteigerung: Der Mischnutzen ermöglicht es, verschiedene Leiterplatten in einem einzigen Produktionsschritt zu fertigen. Dies spart Zeit, da Maschinen nicht für jede Leiterplatte einzeln eingerichtet werden müssen.
Kostensenkung: Da mehrere Leiterplattentypen gemeinsam produziert werden, können die Produktionskosten pro Einheit reduziert werden. Besonders bei Kleinserien oder Prototypen ist der Mischnutzen wirtschaftlich attraktiv.
Materialoptimierung: Der Platz auf dem Rohmaterial wird effizienter genutzt, was Abfall und Kosten reduziert.
Anwendungsbereiche
Prototypenfertigung: Bei der Entwicklung neuer Produkte ist es häufig notwendig, verschiedene Prototypen oder Varianten einer Leiterplatte gleichzeitig zu fertigen. Der Mischnutzen ermöglicht dies in einem Arbeitsschritt.
Kleinserienproduktion: Wenn nur kleine Stückzahlen mehrerer unterschiedlicher Leiterplatten benötigt werden, ist der Mischnutzen eine kosteneffiziente Lösung.
Herausforderungen
Planung und Design: Die Erstellung eines Mischnutzens erfordert eine sorgfältige Planung, um sicherzustellen, dass die unterschiedlichen Leiterplattendesigns kompatibel sind und die Produktion reibungslos abläuft.
Verschiedene Anforderungen: Unterschiedliche Leiterplatten im Mischnutzen können unterschiedliche Produktionsanforderungen haben (z.B. verschiedene Lötstopplackfarben oder Oberflächenbehandlungen), was den Fertigungsprozess komplexer macht.
Fertigungsprozess
Der Fertigungsprozess eines Mischnutzens ist grundsätzlich ähnlich wie bei einem Standardnutzen. Dabei werden die verschiedenen Leiterplattenlayouts auf einem großen Panel arrangiert und gemeinsam gefertigt. Nach der Produktion werden die einzelnen Leiterplatten mechanisch oder manuell vereinzelt.
Fazit
Der Mischnutzen ist eine effiziente und kostensparende Methode, um verschiedene Leiterplattentypen gleichzeitig zu fertigen. Er ist besonders nützlich für Prototypen, Kleinserien oder Anwendungen, bei denen mehrere Designs in kleiner Stückzahl benötigt werden.
Vgl. auch → Nutzen
Ein Multilayer bezeichnet eine mehrlagige Leiterplatte, die aus mehreren Schichten besteht, die übereinander gestapelt und durch elektrisch leitende Verbindungen miteinander verbunden sind. Diese Technologie wird verwendet, um komplexe Schaltungen auf begrenztem Raum unterzubringen und die Leistung und Zuverlässigkeit elektronischer Geräte zu verbessern.
Aufbau eines Multilayers
Ein Multilayer besteht aus einer abwechselnden Schichtung von leitenden und isolierenden Schichten. Die leitenden Schichten bestehen aus Kupfer und sind für die elektrischen Verbindungen und Signalwege zuständig. Die isolierenden Schichten bestehen in der Regel aus Dielektrikum (meist FR4) und dienen als Träger für die Kupferschichten.
- Innenlagen: Diese enthalten die inneren Leiterbahnen, die in das Multilayer-Design integriert sind. Sie werden durch eine Isolationsschicht getrennt.
- Außenlagen: Die äußersten Schichten des Multilayers, die ebenfalls Kupferbahnen für elektrische Verbindungen enthalten, aber direkt mit der Bestückungsebene verbunden sind.
- Durchkontaktierungen (Vias): Die Vias verbinden die Kupferbahnen zwischen den Schichten. Diese Verbindungen können als blinde (blind vias), vergrabene (buried vias) oder Durchsteiger (through-hole vias) ausgeführt sein.
Vorteile von Multilayer-Leiterplatten
Platzersparnis: Multilayer-Leiterplatten bieten die Möglichkeit, komplexe Schaltungen auf engem Raum unterzubringen, was besonders in kleinen Geräten wie Smartphones oder Laptops von Vorteil ist.
Verbesserte elektrische Eigenschaften: Durch die Möglichkeit, Strom- und Signalleitungen auf verschiedenen Schichten zu trennen, können elektromagnetische Störungen reduziert und die Signalintegrität verbessert werden.
Erhöhte Design-Flexibilität: Multilayer ermöglichen die Integration von mehr Komponenten und Verbindungen auf einer Leiterplatte, was zu kompakteren und leistungsfähigeren Designs führt.
Anwendungsbereiche
Multilayer-Leiterplatten werden häufig in hochkomplexen elektronischen Geräten eingesetzt, darunter:
- Computer und Laptops
- Mobiltelefone und Tablets
- Medizinische Geräte
- Luft- und Raumfahrt
- Automobilindustrie
Fertigungsprozess
Die Herstellung eines Multilayers beginnt mit dem Laminieren der einzelnen Kupfer- und Isolationsschichten. Anschließend werden die Schichten mit Durchkontaktierungen miteinander verbunden. Dies erfolgt meist durch Bohren und Galvanisieren. Nach der Verbindung der Schichten werden Ätzprozesse und Oberflächenbehandlungen angewendet, um die gewünschte Schaltung zu formen.
Herausforderungen
Kosten: Multilayer-Leiterplatten sind teurer in der Herstellung als einfache, ein- oder doppelseitige Leiterplatten.
Design-Komplexität: Das Design eines Multilayers erfordert präzise Planung, um sicherzustellen, dass die verschiedenen Schichten richtig miteinander verbunden sind und keine Signalstörungen auftreten.
Fazit
Multilayer-Leiterplatten sind entscheidend für die Entwicklung moderner, leistungsfähiger Elektronik. Sie ermöglichen eine höhere Dichte an Schaltungen und Verbindungen und bieten Flexibilität bei der Integration von komplexen Systemen.
Vgl. auch → Durchkontaktierung→ Laminieren → Via
Synonym für Mischnutzen. Vgl. → Mischnutzen.
- NDK/NPT
- NETZLISTE
- NICHT DURCHKONTAKTIERTE BOHRUNG
Steht für nicht durchkontaktierte Bohrung. Im engl. für Non-Plated Through Hole. Vgl. auch → Nicht durchkontaktierte Bohrung
Die Netzliste (auch Netlist genannt) ist eine zentrale Datei in der Elektronikentwicklung, die eine logische Beschreibung der Verbindungen zwischen den Bauteilen auf einer Leiterplatte enthält. Sie listet alle elektrischen Knotenpunkte (Netze) und beschreibt, wie die Pins der verschiedenen Bauteile miteinander verbunden sind.
Merkmale:
- Die Netzliste wird üblicherweise aus einem Schaltplan generiert.
- Sie enthält Verbindungsinformationen zwischen den Pins der Bauteile und den entsprechenden Netzen.
- Wird in der Layoutphase der Leiterplattenentwicklung verwendet, um sicherzustellen, dass die physischen Verbindungen mit dem Schaltplan übereinstimmen.
Typische Informationen in einer Netzliste:
- Netzname: Die Bezeichnung des elektrischen Netzwerks, z. B. „GND“ für Masse.
- Bauteil-Pin-Zuordnungen: Welcher Pin eines Bauteils mit welchem Netz verbunden ist.
- Bauteilreferenz: Die Referenznummern der Bauteile, die verbunden sind (z. B. R1, C3).
Anwendung:
- Verifikation des Layouts: Sie wird verwendet, um sicherzustellen, dass das PCB-Layout den Verbindungen im Schaltplan entspricht.
- Automatisierte Entflechtung: Netzlisten sind für Autorouter und Entflechtungssoftware erforderlich.
- Simulationen: Netzlisten können auch in Simulationstools verwendet werden, um die Funktionsweise einer Schaltung zu testen.
Die Netzliste ist damit ein wichtiges Bindeglied zwischen Schaltplanerstellung und Leiterplattendesign.
Vgl. auch → Schaltplan
Eine nicht durchkontaktierte Bohrung (auch NPT-Bohrung für „Non-Plated Through Hole“) ist eine Bohrung in einer Leiterplatte, die nicht mit einer leitenden Kupferschicht beschichtet wird. Im Gegensatz zu durchkontaktierten Bohrungen, die elektrische Verbindungen zwischen verschiedenen Leiterbahnen oder Lagen einer Leiterplatte herstellen, dienen nicht durchkontaktierte Bohrungen oft rein mechanischen Zwecken, wie etwa zur Befestigung von Bauteilen oder zur Ausrichtung.
Merkmale:
- Keine elektrische Verbindung zwischen den Lagen der Leiterplatte.
- Wird häufig für Montagezwecke oder als Ausrichtungshilfe verwendet.
- Kann auch zur Wärmeableitung oder für mechanische Stabilität eingesetzt werden.
Anwendungsbereiche:
- Zur Befestigung von Bauteilen.
- Als Lüftungs- oder Entgasungslöcher.
- NICKEL
- NPTH
- NUTZEN
- NUTZENRAHMEN
Nickel wird in der Leiterplattentechnik häufig als Schutzschicht und als Haftvermittler zwischen der Kupferschicht und einer abschließenden Goldschicht verwendet. In diesem Zusammenhang spricht man oft von der Nickel-Gold-Beschichtung, die für Lötfähigkeit, Korrosionsschutz und Kontaktfestigkeit sorgt.
Anwendungen von Nickel auf Leiterplatten:
Galvanische Nickel-Gold-Beschichtung (ENIG):
- Nickel dient als Barriere zwischen dem Kupfer und der Goldoberfläche.
- Die Goldschicht wird oft als Endschicht verwendet, da sie eine gute elektrische Leitfähigkeit und hohe Korrosionsbeständigkeit bietet.
- Nickel verbessert die Lötbarkeit und schützt das darunterliegende Kupfer vor Oxidation.
Schutzschicht:
- Nickel wird als Schutzschicht aufgetragen, um das Kupfer vor Umwelteinflüssen zu schützen.
- Es bietet eine harte und verschleißfeste Oberfläche, die mechanische Belastungen besser widersteht.
Haftvermittler:
- Nickel dient als Haftvermittler zwischen Kupfer und Gold oder anderen Oberflächen, die auf die Leiterplatte aufgebracht werden.
- Es verhindert eine Diffusion von Kupfer in das Gold, was die langfristige Zuverlässigkeit der Verbindungen sicherstellt.
Vorteile von Nickel in der Leiterplattentechnik:
- Erhöhte Haltbarkeit der Kontakte und Lötstellen.
- Korrosionsschutz, insbesondere in feuchten oder aggressiven Umgebungen.
- Langlebigkeit der elektrischen Verbindungen durch die Nickelschicht als Diffusionssperre.
Nickel ist somit ein unverzichtbares Material in der Herstellung hochwertiger und langlebiger Leiterplatten.
Vgl. auch → Chemisch-Nickel-Gold → Diffusionssperre
Ein NPTH ist eine nicht durchkontaktierte Bohrung in einer Leiterplatte. Im Gegensatz zu PTH (Plated Through Hole), bei denen die Bohrlöcher mit einer leitfähigen Metallschicht, meist Kupfer, überzogen werden, um elektrische Verbindungen zwischen den verschiedenen Lagen der Leiterplatte herzustellen, haben NPTH-Bohrungen keine metallische Beschichtung.
Eigenschaften von NPTH:
- Keine elektrische Verbindung zwischen den Schichten: Diese Bohrungen werden nicht mit Kupfer ausgekleidet und dienen daher nicht der elektrischen Kontaktierung zwischen den verschiedenen Lagen.
- Mechanische Funktion: Häufig dienen NPTHs rein mechanischen Zwecken, z. B. zur Befestigung von Bauteilen, zur Ausrichtung oder für Schraubverbindungen.
- Isoliert: Da sie nicht beschichtet sind, verhindern NPTH-Bohrungen den elektrischen Kontakt und werden oft verwendet, wenn eine mechanische Verbindung ohne elektrische Leitfähigkeit benötigt wird.
Anwendungen:
- Befestigungslöcher für Schrauben oder andere mechanische Verbindungen.
- Montagelöcher zur Fixierung von Bauteilen oder zur Befestigung der Leiterplatte im Gehäuse.
- Passstifte für die Ausrichtung von Bauteilen oder Modulen.
NPTHs spielen eine wichtige Rolle in der mechanischen Stabilität und Struktur von Leiterplatten, während sie elektrische Funktionen nicht beeinflussen.
Vgl. auch → PTH
Nutzen (englisch: „panel“ oder „array“) bezeichnet in der Leiterplattenherstellung eine Anordnung mehrerer einzelner Leiterplatten auf einem größeren Träger oder Bogen, der zur besseren und effizienteren Produktion dient. Statt einzelne Leiterplatten herzustellen und zu verarbeiten, werden mehrere kleine Leiterplatten auf einem Nutzen zusammengefasst und gemeinsam bearbeitet.
Vorteile des Nutzen:
- Effizienzsteigerung: Durch die gleichzeitige Verarbeitung mehrerer Leiterplatten wird der Produktionsaufwand reduziert und die Auslastung der Maschinen optimiert.
- Besseres Handling: Kleine Leiterplatten wären in einzelnen Produktionsschritten schwer zu handhaben. Der Nutzen bietet größere Flächen, die einfacher automatisiert bearbeitet werden können.
- Kosteneinsparungen: Weniger Maschinenumrüstungen und kürzere Durchlaufzeiten bedeuten reduzierte Produktionskosten.
- Erleichterte Bestückung: Der Bestückungsprozess kann so optimiert werden, dass mehrere Platinen in einem Durchgang mit Bauteilen bestückt werden.
Nach der Produktion:
Nach der Bearbeitung und Bestückung werden die einzelnen Leiterplatten aus dem Nutzen herausgetrennt, in der Regel durch Fräsen oder Ritzen. Dies ermöglicht eine genaue Trennung, ohne die Qualität der einzelnen Leiterplatten zu beeinträchtigen.
Typen von Nutzen:
- V-Nut-Nutzen: Hierbei werden die Trennlinien zwischen den einzelnen Leiterplatten als V-Nuten vorbereitet, sodass die Platinen nach der Fertigung einfach herausgebrochen werden können.
- Fräsnutzen: Hier werden die Leiterplatten durch Fräskanten voneinander getrennt und häufig durch kleine Stege im Nutzen zusammengehalten.
Der Nutzen ist ein entscheidender Faktor für die Massenproduktion von Leiterplatten und wird in der Elektronikfertigung häufig eingesetzt.
Vgl. auch → Panel
Ein Nutzenrahmen ist der äußere Rand um einen Nutzen (eine Anordnung mehrerer Leiterplatten auf einem größeren Träger), der zur Stabilisierung und zum besseren Handling während der Produktion und Bestückung dient. Der Rahmen sorgt dafür, dass der Nutzen bei verschiedenen Fertigungsschritten sicher und präzise verarbeitet werden kann.
Funktionen des Nutzenrahmens:
- Stabilität: Der Rahmen verleiht dem Nutzen während der Bearbeitung Festigkeit und verhindert Verformungen oder Schäden an den einzelnen Leiterplatten.
- Ausrichtungshilfen: Oft werden in den Rahmen Ausrichtungsmarkierungen oder Fiducials (optische Referenzmarken) integriert, die Maschinen helfen, den Nutzen exakt zu positionieren und auszurichten.
- Transport und Handling: Der Nutzenrahmen erleichtert den Transport durch automatische Produktionssysteme, wie etwa Bestückungsautomaten oder Lötmaschinen.
- Schutz der Leiterplatten: Der Rahmen schützt die empfindlichen Leiterplatten am Rand des Nutzens vor mechanischen Beschädigungen während des gesamten Herstellungsprozesses.
Aufbau:
- Der Nutzenrahmen umgibt die eigentlichen Leiterplatten im Nutzen und ist oft mit Haltestegen mit diesen verbunden. Diese Stege ermöglichen es, die Leiterplatten nach der Produktion einfach herauszutrennen, ohne dass die Stabilität des gesamten Nutzens während der Bearbeitung beeinträchtigt wird.
Typen von Nutzenrahmen:
- Einfacher Rahmen: Umgibt den Nutzen vollständig und kann zusätzliche Komponenten wie Ausrichtungsmarkierungen enthalten.
- Mehrere Nutzen auf einem Rahmen: Manchmal enthält der Rahmen nicht nur einen Nutzen, sondern mehrere, um größere Produktionsmengen in einem Durchgang zu bearbeiten.
Der Nutzenrahmen spielt eine wesentliche Rolle, um eine reibungslose, präzise und fehlerfreie Fertigung von Leiterplatten zu gewährleisten.
Vgl. auch→ Fiducials → Nutzen
- OBERFLÄCHE
- ODB++
- OPTISCHE KONTROLLE
- OSP
Arten von Oberflächenbeschichtungen:
HAL (Hot Air Leveling): Eine weit verbreitete Methode, bei der die Kupferoberfläche mit Zinn überzogen und anschließend durch heiße Luft geglättet wird. HAL sorgt für gute Lötbarkeit, hat aber eine relativ raue Oberfläche.
Chemisch Nickel-Gold (ENIG): Diese Methode bietet eine glatte und langlebige Oberfläche, bei der eine Nickelschicht auf das Kupfer aufgetragen wird, gefolgt von einer dünnen Goldschicht. ENIG bietet ausgezeichneten Korrosionsschutz und hohe Zuverlässigkeit.
Chemisch Zinn: Hierbei wird eine Zinnschicht auf die Kupferoberfläche aufgebracht, die für einen guten Lötprozess sorgt und das Kupfer vor Oxidation schützt. Diese Beschichtung ist jedoch empfindlich gegenüber mechanischen Belastungen.
OSP (Organic Solderability Preservative): Eine organische Schutzschicht, die auf das Kupfer aufgetragen wird, um es vor Oxidation zu schützen. OSP ist eine kostengünstige Methode, bietet jedoch im Vergleich zu anderen Beschichtungen eine kürzere Lebensdauer.
Chemisch Silber: Diese Beschichtung sorgt für eine hohe Leitfähigkeit und eine sehr glatte Oberfläche. Sie eignet sich gut für Anwendungen, bei denen eine präzise elektrische Leistung erforderlich ist, kann jedoch bei längerer Lagerung oxidieren.
Eigenschaften der Oberfläche:
Lötbarkeit: Die Wahl der Oberfläche beeinflusst, wie gut die Bauteile auf die Leiterplatte gelötet werden können. Oberflächen wie ENIG oder chemisch Zinn bieten eine gute Lötbarkeit.
Korrosionsbeständigkeit: Eine geeignete Oberflächenbehandlung schützt das Kupfer vor Oxidation und anderen äußeren Einflüssen.
Elektrische Eigenschaften: Einige Oberflächen wie ENIG bieten stabile elektrische Eigenschaften, die bei Hochfrequenzanwendungen oder komplexen Schaltungen von Vorteil sind.
Anwendung:
Die Wahl der richtigen Oberflächenbeschichtung hängt von der Anwendung der Leiterplatte ab. Faktoren wie Kosten, Lötanforderungen, Lebensdauer der Produkte und Umweltbedingungen spielen eine Rolle bei der Auswahl.
Fazit:
Die Oberflächenbehandlung ist entscheidend für die Leistungsfähigkeit und Zuverlässigkeit von Leiterplatten. Eine sorgfältige Auswahl der geeigneten Beschichtung trägt zur Optimierung des Fertigungsprozesses und zur Langlebigkeit elektronischer Geräte bei.
Vgl. auch → Carbon → Chemisch-Nickel-Gold → Chemisch Silber → Chemisch Zinn → Kupfer
ODB++ ist ein standardisiertes Austauschformat, das in der Elektronikfertigung, insbesondere bei Leiterplatten (PCBs), verwendet wird, um Daten zwischen Design- und Fertigungsprozessen zu übertragen. Es enthält alle erforderlichen Informationen für die Herstellung, Prüfung und Montage einer Leiterplatte in einem einzigen Datensatz.
Hauptmerkmale von ODB++:
Integriertes Format: ODB++ kombiniert alle Informationen, die für die Fertigung einer Leiterplatte notwendig sind, wie Schaltpläne, Layouts, Stücklisten, Bohrdaten und Gerber-Dateien, in einem einzigen Format. Dies reduziert die Notwendigkeit, mehrere Dateiformate zu verwenden.
Datenkompression: Das Format komprimiert die erforderlichen Daten, wodurch weniger Speicherplatz benötigt wird und die Übertragung der Daten schneller erfolgt.
Fehlerreduktion: Da ODB++ ein konsolidiertes Format ist, werden mögliche Missverständnisse oder Fehler, die durch mehrere verschiedene Datenquellen entstehen könnten, minimiert.
Kompatibilität: ODB++ wird von vielen Design- und Fertigungssoftwaretools unterstützt, was es zu einem weit verbreiteten Standard in der Elektronikindustrie macht.
Inhalt von ODB++:
Geometrie: Informationen zu den Layoutstrukturen der Leiterplatte, wie Lagenaufbau, Leiterbahnen, Pads und Durchkontaktierungen (Vias).
Schichtinformationen: Details zu den verschiedenen Lagen einer Multilayer-Leiterplatte, einschließlich Kupferlagen, Lötstoppmasken und Siebdruck.
Bohrdaten: Daten zu den Durchkontaktierungen, deren Position, Größe und Tiefe.
Stückliste (BOM): Eine Liste aller benötigten Bauteile für die Bestückung der Leiterplatte.
Netzliste: Elektrische Verbindungen und die Zuordnung der Bauteile auf der Leiterplatte.
Lötmaske und Bestückungsdruck: Informationen zur Platzierung der Lötstopplacke und des Bestückungsdrucks, um sicherzustellen, dass die Bauteile korrekt platziert und gelötet werden.
Vorteile von ODB++:
Vereinfachung des Fertigungsprozesses: Durch die Integration aller relevanten Daten in einem Format wird die Kommunikation zwischen Designern und Herstellern vereinfacht.
Zeitersparnis: Das konsolidierte Format verringert den Zeitaufwand, der normalerweise für die Umwandlung und Verwaltung mehrerer Dateiformate erforderlich ist.
Erhöhte Genauigkeit: Da alle Design- und Fertigungsdaten in einem einzigen Datensatz enthalten sind, wird die Wahrscheinlichkeit von Fehlern oder Diskrepanzen reduziert.
Fazit:
ODB++ bietet eine effiziente Möglichkeit, die Datenintegrität in der Leiterplattenfertigung sicherzustellen, den Austausch zwischen Design und Produktion zu optimieren und den gesamten Prozess von der Entwicklung bis zur Fertigung zu vereinfachen. Es ist ein weit verbreiteter Standard, der dazu beiträgt, die Effizienz und Genauigkeit in der Elektronikproduktion zu verbessern.
Vgl. auch → PCB
Optische Kontrolle ist ein wichtiger Prozess in der Fertigung von Leiterplatten (PCBs) und elektronischen Bauteilen, um die Qualität und Integrität der hergestellten Produkte sicherzustellen. Dabei wird die Oberfläche der Leiterplatten oder Baugruppen mithilfe von Kameras und visuellen Inspektionssystemen überprüft, um Fehler zu erkennen.
Arten der optischen Kontrolle:
Manuelle visuelle Inspektion (MVI): Ein Bediener überprüft die Leiterplatte manuell mit bloßem Auge oder durch ein Vergrößerungsglas. Diese Methode ist einfach und kostengünstig, aber zeitaufwendig und anfällig für menschliche Fehler.
Automatische optische Inspektion (AOI): Diese Methode verwendet Kameras und Bildverarbeitungstechnologien, um die Leiterplatten automatisch zu prüfen. AOI-Systeme vergleichen das tatsächliche Bild der Leiterplatte mit einem Referenzbild und erkennen Abweichungen wie fehlerhafte Lötstellen, fehlende Bauteile oder falsche Bauteilplatzierungen.
Einsatzbereiche:
Fertigungsprüfung: In der Leiterplattenfertigung wird die optische Kontrolle verwendet, um sicherzustellen, dass die Leiterbahnen korrekt geätzt, die Bauteile richtig bestückt und die Lötstellen einwandfrei sind.
Fehlererkennung: AOI-Systeme erkennen typische Fehler wie Kurzschlüsse, offene Verbindungen, unsaubere Lötstellen, Bauteilverschiebungen oder falsche Bauteile.
Qualitätsmanagement: Optische Kontrollsysteme sind ein wichtiger Bestandteil des Qualitätsmanagements, da sie eine hohe Genauigkeit und Reproduzierbarkeit bieten. Sie tragen dazu bei, den Ausschuss zu reduzieren und die Zuverlässigkeit der Endprodukte zu erhöhen.
Vorteile der optischen Kontrolle:
Automatisierung: Die automatische optische Kontrolle spart Zeit und Kosten im Vergleich zu manuellen Verfahren und erhöht die Effizienz der Prüfung.
Fehlererkennung in Echtzeit: AOI-Systeme erkennen Fehler sofort, sodass Probleme frühzeitig behoben werden können, bevor sie die Produktion verzögern oder zu größeren Qualitätsproblemen führen.
Hohe Präzision: Mit hochauflösenden Kameras und leistungsfähiger Bildverarbeitungstechnologie können selbst kleinste Defekte zuverlässig erkannt werden.
Herausforderungen:
Komplexität von Bauteilen: Bei sehr komplexen oder dicht bestückten Baugruppen kann es schwierig sein, bestimmte Fehler optisch zu erkennen, was den Einsatz von anderen Inspektionsmethoden wie Röntgeninspektion notwendig machen kann.
Kamerakalibrierung: Die genaue Kalibrierung der Kameras und Systeme ist erforderlich, um präzise Messergebnisse zu liefern.
Fazit:
Die optische Kontrolle ist ein unverzichtbarer Bestandteil des Fertigungsprozesses von Leiterplatten und elektronischen Baugruppen. Sie ermöglicht eine schnelle, effiziente und präzise Qualitätskontrolle, die für die Fehlerreduktion und die Sicherstellung der Produktzuverlässigkeit entscheidend ist. Insbesondere automatische optische Inspektionssysteme tragen erheblich zur Steigerung der Produktionsqualität bei.
Vgl. auch → AOI
OSP (Organic Solderability Preservative) ist eine Oberflächenbehandlung, die auf Leiterplatten (PCBs) angewendet wird, um die Lötbarkeit der Kupferoberfläche zu schützen und zu verbessern. Diese Methode ist besonders wichtig für die Herstellung von Leiterplatten, da sie die Qualität und Zuverlässigkeit von Lötverbindungen beeinflusst.
Eigenschaften und Vorteile von OSP:
Umweltfreundlich: OSP ist eine umweltfreundliche Lösung, da sie keine giftigen Chemikalien enthält, die in anderen Oberflächenbehandlungen wie chemischem Zinn oder Nickel-Gold enthalten sein können. Es ist ein wasserlösliches, organisches Material, das beim Löten vollständig verbrennt.
Lötbarkeit: OSP schützt die Kupferoberfläche vor Oxidation und sorgt dafür, dass die Lötverbindungen eine hohe Qualität aufweisen. Dies ist besonders wichtig für die mechanische Stabilität und elektrische Leitfähigkeit der Bauteile.
Einfache Anwendung: Der OSP-Beschichtungsprozess ist einfach und kann in der Regel in die bestehende Produktionslinie integriert werden. Die Behandlung erfolgt typischerweise nach dem Ätzprozess und vor der Bestückung.
Prozess der OSP-Anwendung:
Reinigung: Die Leiterplatte wird gründlich gereinigt, um Verunreinigungen und Oxide von der Kupferoberfläche zu entfernen.
Anwendung der OSP-Lösung: Die OSP-Lösung wird auf die gereinigte Kupferoberfläche aufgetragen. Dies geschieht in der Regel durch Eintauchen, Sprühen oder Walzen.
Trocknung: Nach der Anwendung wird die Leiterplatte getrocknet, um eine gleichmäßige und homogene Beschichtung zu gewährleisten.
Anwendungsbereiche:
Baugruppen mit hoher Dichte: OSP eignet sich besonders für Leiterplatten mit dichter Bauteilbestückung, da es eine flache, gleichmäßige Oberfläche hinterlässt, die die Montage und das Löten erleichtert.
Reflow-Löten: OSP wird häufig in Verbindung mit Reflow-Lötprozessen verwendet, da es eine gute Lötbarkeit und thermische Stabilität bietet.
Herausforderungen:
Lagerfähigkeit: OSP-behandelte Leiterplatten haben eine begrenzte Lagerfähigkeit, da die OSP-Beschichtung mit der Zeit abgebaut werden kann. Es wird empfohlen, die bestückten Platinen innerhalb von 6 bis 12 Monaten nach der Beschichtung zu löten.
Empfindlichkeit: Die OSP-Beschichtung ist empfindlicher gegenüber mechanischen Beschädigungen als andere Oberflächenbehandlungen wie verzinnte oder galvanisch beschichtete Oberflächen.
Fazit:
OSP ist eine effektive und umweltfreundliche Oberflächenbehandlung für Leiterplatten, die eine hohe Lötbarkeit gewährleistet und gleichzeitig die Kupferoberfläche vor Oxidation schützt. Durch ihre einfache Anwendung und die Möglichkeit, sie in bestehenden Produktionsprozesse zu integrieren, hat sich OSP zu einer beliebten Wahl in der Leiterplattenfertigung entwickelt.
- PACKAGE
- PAD
- PAD-REDUKTION
- PANEL
- PASSERMARKEN
Package bezeichnet in der Elektronik den physischen Gehäusetyp eines elektronischen Bauteils, wie z.B. eines Chips oder eines Halbleiters, der es ermöglicht, das Bauteil auf einer Leiterplatte (PCB) zu montieren und elektrisch zu verbinden. Das Package schützt den Chip vor äußeren Einflüssen und stellt die elektrischen Anschlüsse für den Betrieb und die Verbindung mit der Leiterplatte bereit.
Wichtige Aspekte eines Packages:
Schutzfunktion: Das Package schützt die empfindlichen elektronischen Komponenten im Inneren vor mechanischen Belastungen, Feuchtigkeit, Staub und anderen Umwelteinflüssen.
Elektrische Verbindungen: Das Package enthält metallische Verbindungen (Pins, Anschlüsse oder Kontakte), die den Stromfluss zwischen der Leiterplatte und der elektronischen Komponente sicherstellen.
Thermische Eigenschaften: Viele Packages sind so ausgelegt, dass sie die Wärme, die von den Bauteilen erzeugt wird, ableiten können, um Überhitzung zu vermeiden.
Typische Package-Arten:
DIP (Dual In-line Package): Ein Gehäusetyp mit zwei parallelen Reihen von Anschlüssen (Pins), die vertikal durch die Leiterplatte gesteckt und verlötet werden.
SOIC (Small Outline Integrated Circuit): Ein kleineres, flaches Package mit zwei Reihen von Pins, die zur Oberflächenmontage (SMD) auf Leiterplatten verwendet werden.
QFP (Quad Flat Package): Ein flaches Package mit Pins auf allen vier Seiten, das für SMD-Technologie verwendet wird und häufig bei hochintegrierten Schaltkreisen zum Einsatz kommt.
BGA (Ball Grid Array): Ein Package, das Lötperlen (Balls) auf der Unterseite verwendet, um eine hohe Dichte an elektrischen Anschlüssen für moderne Hochleistungsbauteile wie Mikroprozessoren zu ermöglichen.
Anwendungen:
Mikroprozessoren und Speicherchips: Moderne CPUs, GPUs und RAM-Module verwenden fortschrittliche Packages wie BGA oder LGA (Land Grid Array), um die vielen notwendigen elektrischen Verbindungen zu realisieren.
Passive Bauteile: Widerstände, Kondensatoren und Induktivitäten können ebenfalls in verschiedenen Package-Typen vorliegen, abhängig von der Anwendung und den Platzanforderungen auf der Leiterplatte.
Fazit:
Das Package eines elektronischen Bauteils spielt eine entscheidende Rolle für die Zuverlässigkeit, die elektrische Leistung und die Handhabung der Komponente. Die Wahl des richtigen Packages ist wichtig, um die Funktionalität und Effizienz eines Systems sicherzustellen.
Vgl. auch → BGA → PCB → QFP
Pad bezeichnet in der Elektronik einen definierten Bereich auf einer Leiterplatte (PCB), der für die elektrische und mechanische Verbindung von Bauteilen genutzt wird. Pads sind im Wesentlichen die Punkte, an denen die Bauteile auf die Leiterplatte gelötet oder angebracht werden.
Wichtige Eigenschaften von Pads:
Elektrische Verbindung: Pads bieten eine Kontaktfläche, um elektronische Bauteile mit den Leiterbahnen der Leiterplatte zu verbinden. Sie stellen sicher, dass der Strom von den Bauteilen zu den Leiterbahnen und umgekehrt fließen kann.
Mechanische Befestigung: Abgesehen von der elektrischen Verbindung sorgen Pads auch dafür, dass die Bauteile physisch sicher auf der Leiterplatte verankert sind.
Verschiedene Formen: Pads können je nach Art des Bauteils verschiedene Formen und Größen haben, wie runde, rechteckige oder ovale. SMD-Pads sind typischerweise rechteckig, während Durchsteckkomponenten (THT) oft runde oder ovale Pads verwenden.
Arten von Pads:
SMD-Pads (Surface Mount Device Pads): Diese Pads befinden sich auf der Oberfläche der Leiterplatte und sind für die Oberflächenmontage von Bauteilen (SMDs) vorgesehen. Hier wird das Bauteil direkt auf das Pad gesetzt und verlötet.
THT-Pads (Through-Hole Technology Pads): Diese Pads haben ein Loch (durchkontaktiert oder nicht durchkontaktiert), durch das ein Anschluss des Bauteils gesteckt wird, um dann auf der Unterseite verlötet zu werden.
Anwendungen:
Leiterplattenherstellung: In der Fertigung werden Pads in Kombination mit Lötstopplack (Solder Mask) verwendet, um sicherzustellen, dass beim Löten nur die gewünschten Bereiche Lötmittel erhalten.
Automatisierte Bestückung: Maschinen verwenden die Position und Ausrichtung der Pads, um elektronische Bauteile präzise auf der Leiterplatte zu platzieren und zu löten.
Fazit:
Pads sind entscheidende Elemente in der Leiterplattenherstellung, da sie die Verbindungspunkte für elektrische Bauteile darstellen. Ihre richtige Gestaltung und Positionierung sind essenziell für die Funktionalität und Zuverlässigkeit einer Schaltung.
Pad-Reduktion bezieht sich auf die Verringerung der Größe von Pads auf einer Leiterplatte. Diese Technik wird hauptsächlich angewendet, um Platz auf der Leiterplatte zu sparen, die Dichte der Schaltung zu erhöhen und die Kosten zu reduzieren. Pad-Reduktion kann in bestimmten Situationen vorteilhaft sein, bringt jedoch auch einige Herausforderungen mit sich.
Gründe für Pad-Reduktion:
Platzersparnis: In modernen, hochkomplexen Schaltungen wird immer mehr Funktionalität auf kleinem Raum untergebracht. Kleinere Pads schaffen mehr Raum für zusätzliche Bauteile und Leiterbahnen, insbesondere bei hochdichten Designs wie HDI (High-Density Interconnect) Leiterplatten.
Reduzierte Produktionskosten: Durch kleinere Pads kann Material eingespart werden, was bei der Massenproduktion von Leiterplatten zu Kostenvorteilen führen kann.
Verbesserte Entflechtung: Mit kleineren Pads lassen sich Leiterbahnen leichter um und zwischen den Pads führen, was die Entflechtung der Leiterplatte erleichtert.
Herausforderungen und Risiken der Pad-Reduktion:
Schwierigere Lötbarkeit: Kleinere Pads können die Lötbarkeit erschweren, da weniger Oberfläche zur Verfügung steht, um eine zuverlässige Lötverbindung herzustellen.
Geringere mechanische Stabilität: Kleinere Pads bieten weniger Halt für Bauteile, insbesondere für größere oder schwerere Komponenten, was die mechanische Stabilität beeinträchtigen kann.
Elektrische Eigenschaften: Die Verkleinerung der Pads kann sich negativ auf die elektrischen Eigenschaften auswirken, insbesondere bei Hochfrequenzanwendungen, da der Kontaktwiderstand höher sein kann und die Zuverlässigkeit der Verbindung beeinträchtigt werden kann.
Anwendung:
SMD-Technologie: Besonders bei der Oberflächenmontage (Surface Mount Technology, SMT) wird oft eine Reduktion der Pad-Größe durchgeführt, um die Miniaturisierung von elektronischen Schaltungen voranzutreiben.
Finepitch-Bauteile: Bei sehr feinen Rastermaßen (Pitch) ist die Pad-Reduktion notwendig, um ausreichend Abstand zwischen den Pads zu erhalten und Kurzschlüsse zu vermeiden.
Fazit:
Die Pad-Reduktion ist eine nützliche Technik zur Optimierung von Leiterplattenlayouts, vor allem in der Hochfrequenztechnik und bei kompakten Designs. Allerdings muss sorgfältig abgewogen werden, ob die mechanischen und elektrischen Anforderungen trotz kleinerer Pads noch erfüllt werden können.
Panel bezeichnet in der Leiterplattenherstellung ein größeres Trägerstück oder eine Arbeitsfläche, auf der mehrere Leiterplatten gleichzeitig hergestellt oder bearbeitet werden. Ein Panel dient dazu, die Produktionsprozesse effizienter zu gestalten, indem mehrere Leiterplatten auf einmal gefertigt, bestückt und getestet werden können.
Aufbau und Verwendung von Panels:
Mehrere Leiterplatten in einem Panel: Ein Panel kann mehrere Leiterplatten enthalten, die durch Fräsungen oder Sollbruchstellen voneinander getrennt sind. Diese Vorgehensweise ermöglicht eine rationellere Produktion und spart Material- und Bearbeitungskosten.
Größe des Panels: Die Größe eines Panels variiert je nach Hersteller und spezifischen Anforderungen der Anwendung. Übliche Standardgrößen sind zum Beispiel 18 x 24 Zoll oder 20 x 24 Zoll, aber kundenspezifische Formate sind ebenfalls möglich.
Nutzen und Nutzenrahmen: Der Begriff Nutzen bezieht sich auf das Layout der einzelnen Leiterplatten auf dem Panel. Die Leiterplatten sind oft in einem sogenannten Nutzenrahmen untergebracht, der für die Stabilität während der Verarbeitung sorgt. Am Ende des Herstellungsprozesses werden die einzelnen Leiterplatten aus dem Panel herausgebrochen oder herausgefräst.
Vorteile der Panelisierung:
Effizienzsteigerung: Durch die Bearbeitung mehrerer Leiterplatten in einem Panel können Arbeitsschritte wie Belichtung, Ätzen, Bestückung und Testen gleichzeitig für mehrere Leiterplatten durchgeführt werden, was den Fertigungsprozess beschleunigt.
Kostenreduktion: Die gleichzeitige Verarbeitung mehrerer Leiterplatten reduziert den Materialverbrauch und die Arbeitskosten, da Maschinen und Arbeitskräfte effizienter eingesetzt werden.
Einfachere Handhabung: Panels erleichtern die Handhabung während der automatisierten Produktionsschritte, insbesondere bei der Bestückung und beim Lötprozess. Sie bieten eine stabile Arbeitsfläche, die das Risiko von Schäden während der Fertigung reduziert.
Herausforderungen:
Restmaterial: Nach dem Heraustrennen der Leiterplatten aus dem Panel bleibt oft überschüssiges Material zurück, das entsorgt werden muss.
Paneldesign: Das Design des Panels und der Nutzen muss sorgfältig geplant werden, um eine optimale Ausnutzung des Materials und der Produktionsressourcen zu gewährleisten. Ungünstige Designs können zu Materialverschwendung oder ineffizienten Produktionsschritten führen.
Fazit:
Die Panelisierung ist ein wesentlicher Bestandteil der Leiterplattenproduktion, der dazu beiträgt, die Effizienz zu steigern und Kosten zu senken. Ein gut gestaltetes Panel kann den gesamten Fertigungsprozess optimieren, erfordert jedoch präzise Planung und Ausführung.
Vgl. auch → Nutzen→ Mischnutzen → Multinutzen
Passermarken sind spezielle Markierungen auf Leiterplatten oder anderen gedruckten Schaltungen, die als Referenzpunkte für Ausrichtungs- und Positionierungsprozesse während der Herstellung dienen. Diese Markierungen sind entscheidend für die Präzision in der Produktion und Bestückung von Leiterplatten.
Funktionen der Passermarken:
Ausrichtung: Passermarken helfen Maschinen, sich präzise an der Leiterplatte auszurichten. Sie werden in verschiedenen Produktionsphasen genutzt, wie zum Beispiel beim Bestücken der Bauteile oder beim Bohren und Fräsen.
Optische Erkennung: Maschinen, die optische Systeme verwenden, erkennen Passermarken, um die exakte Position der Leiterplatte zu bestimmen. Dies ist besonders wichtig bei hochpräzisen Arbeiten wie dem Platzieren von Bauteilen oder dem Anbringen von Lötmasken.
Reduzierung von Toleranzfehlern: Passermarken verringern die Wahrscheinlichkeit von Toleranzfehlern, die auftreten können, wenn Bauteile oder Schichten einer Multilayer-Leiterplatte nicht exakt ausgerichtet sind. Sie sorgen dafür, dass alle Arbeitsschritte korrekt aufeinander abgestimmt sind.
Arten von Passermarken:
Global Fiducials: Diese Passermarken befinden sich am Rand der Leiterplatte und dienen als globale Referenzpunkte für die gesamte Platine.
Local Fiducials: Diese werden in der Nähe spezifischer Bauteile oder Baubereiche platziert und dienen dazu, die genaue Position einzelner Komponenten zu bestimmen, insbesondere bei hochpräzisen Bauteilen wie BGAs (Ball Grid Arrays).
Platzierung von Passermarken:
Symmetrische Anordnung: Passermarken werden normalerweise symmetrisch platziert, um eine genaue Ausrichtung in zwei Achsen (X und Y) zu ermöglichen. Oft werden mindestens zwei Passermarken auf einer Leiterplatte verwendet.
Freie Umgebung: Passermarken sollten in einem Bereich platziert werden, der frei von anderen Leiterbahnen, Pads oder Komponenten ist, damit sie von den Maschinen leicht erkannt werden können.
Anforderungen an Passermarken:
Form und Größe: Passermarken sind in der Regel kreisförmig und haben eine definierte Größe, damit sie von den optischen Systemen gut erkannt werden können. Übliche Durchmesser liegen zwischen 1 mm und 3 mm.
Kontrast: Um eine klare Erkennung zu gewährleisten, sollten Passermarken einen hohen Kontrast zur umgebenden Fläche haben, z. B. durch einen freien Kupferbereich um die Marke oder eine lötstoppfreie Zone.
Fazit:
Passermarken spielen eine entscheidende Rolle in der Leiterplattenfertigung, indem sie für eine präzise Ausrichtung der Maschinen sorgen. Sie tragen wesentlich zur Genauigkeit und Zuverlässigkeit der Produktion bei, insbesondere bei modernen, komplexen Designs, die eine hohe Präzision erfordern.
- PCB
- PERTIMAX®
- PICK & PLACE
- PIH
- PIN
PCB ist die Abkürzung für Leiterplatte (engl.: Printed Circuit Board)
Vgl. auch → Leiterplatte
Pertinax® ist eine Handelsbezeichnung für Hartpapier, ein Schichtpressstoff, der aus Papier und Phenolharz besteht. Es wird häufig als Isoliermaterial in der Elektronik- und Elektrotechnik verwendet, insbesondere bei der Herstellung von Leiterplatten in einfachen oder kostengünstigen Anwendungen. Hier sind einige wichtige Informationen zu Pertinax®:
Eigenschaften von Pertinax®:
- Gute mechanische Stabilität: Pertinax® hat eine hohe Festigkeit und Steifigkeit, was es zu einem stabilen Trägermaterial macht.
- Elektrische Isolierung: Es besitzt ausgezeichnete isolierende Eigenschaften, weshalb es häufig in elektrischen und elektronischen Anwendungen eingesetzt wird.
- Wärmebeständigkeit: Pertinax® hält moderaten Temperaturen stand, ist aber im Vergleich zu moderneren Materialien wie FR4 weniger hitzebeständig.
- Leichte Bearbeitbarkeit: Das Material lässt sich relativ einfach schneiden, bohren und fräsen, was es für die Herstellung von Leiterplatten und anderen mechanischen Komponenten geeignet macht.
Verwendung von Pertinax®:
- Leiterplatten: Pertinax® wurde früher in großem Umfang als Trägermaterial für einfache Leiterplatten verwendet. Heutzutage wird es noch in einigen kostengünstigen und wenig anspruchsvollen Elektronikanwendungen eingesetzt, obwohl es zunehmend durch leistungsfähigere Materialien wie FR4 ersetzt wurde.
- Isolierteile: Abgesehen von Leiterplatten wird Pertinax® auch für die Herstellung von mechanischen Isolierbauteilen verwendet, z. B. in Transformatoren, Schaltgeräten und anderen elektrischen Systemen.
Vorteile von Pertinax®:
- Kostengünstig: Es ist preisgünstiger als moderne Materialien wie Glasfaser-basierte Verbundstoffe.
- Leichtgewichtig: Pertinax® ist relativ leicht und daher für Anwendungen geeignet, bei denen Gewicht eine Rolle spielt.
Nachteile von Pertinax®:
- Geringe Hitzebeständigkeit: Im Vergleich zu FR4 oder anderen modernen Materialien kann Pertinax® bei höheren Temperaturen versagen oder sich verformen.
- Weniger haltbar: Pertinax® ist weniger robust gegenüber Feuchtigkeit und mechanischen Belastungen, was seine Lebensdauer in anspruchsvollen Umgebungen einschränkt.
Fazit:
Pertinax® ist ein traditionelles Material in der Elektronikfertigung, das aufgrund seiner Isolierfähigkeit und Kosteneffizienz genutzt wurde. Während es in anspruchsvollen modernen Anwendungen zunehmend durch leistungsfähigere Materialien ersetzt wird, bleibt es in weniger komplexen Elektronikanwendungen ein wirtschaftlicher Werkstoff.
Vgl. auch → FR4
Pick & Place bezieht sich auf den automatisierten Prozess, bei dem elektronische Bauteile auf eine Leiterplatte (PCB) positioniert werden. Dieser Prozess wird in der modernen Elektronikfertigung eingesetzt, um die Komponenten präzise und effizient auf der Leiterplatte zu platzieren. Hier sind die wichtigsten Aspekte des Pick & Place-Verfahrens:
Funktionsweise des Pick & Place-Prozesses:
Bauteilaufnahme (Pick): Die Pick & Place-Maschine verwendet Vakuumdüsen oder mechanische Greifer, um Bauteile aus einem Vorratsbehälter oder einer Spule aufzunehmen.
Positionierung (Place): Die Maschine bewegt die Bauteile zu den vorbestimmten Positionen auf der Leiterplatte, die durch einen vorher erstellten Bestückungsplan festgelegt sind. Diese Positionierung erfolgt mit sehr hoher Präzision.
Optische Ausrichtung: In vielen modernen Maschinen wird eine Kamera verwendet, um die exakte Position des Bauteils und der Leiterplatte zu überprüfen, sodass die Platzierung möglichst genau erfolgt.
Platzieren des Bauteils: Das Bauteil wird auf die mit Lotpaste vorbereiteten Pads der Leiterplatte positioniert, sodass es anschließend im Reflow-Lötverfahren oder anderen Lötverfahren befestigt werden kann.
Vorteile des Pick & Place-Verfahrens:
- Hohe Geschwindigkeit: Die Maschine kann mehrere tausend Bauteile pro Stunde positionieren, was die Produktion erheblich beschleunigt.
- Präzision: Durch die Automatisierung werden Bauteile äußerst genau auf der Leiterplatte platziert, wodurch Fehlplatzierungen minimiert werden.
- Flexibilität: Die Maschinen können eine Vielzahl von Bauteiltypen und -größen handhaben, von winzigen SMD-Bauteilen (Surface Mounted Devices) bis zu größeren Komponenten.
Anwendungen:
- SMT-Fertigung (Surface-Mount Technology): Pick & Place ist ein wesentlicher Bestandteil des SMT-Fertigungsprozesses, bei dem Bauteile direkt auf die Oberfläche der Leiterplatte montiert werden.
- Massenproduktion: In der Elektronikfertigung wird das Pick & Place-Verfahren für die Serienproduktion von Leiterplatten in der Automobilindustrie, Unterhaltungselektronik, Medizintechnik und vielen weiteren Bereichen eingesetzt.
Fazit:
Pick & Place ist ein zentrales Element in der modernen Elektronikfertigung, das eine schnelle, präzise und effiziente Bestückung von Leiterplatten ermöglicht. Der Einsatz dieser Technologie reduziert manuelle Fehler und steigert die Produktivität in der Herstellung von Elektronikgeräten.
PIH ist die Abkürzung für Durchsteck- oder Einsteck-Montage (engl.: Pin In Hole Technology).
Vgl. auch → THT
Pin bezieht sich in der Elektronik auf ein einzelnes elektrisches Verbindungselement eines Bauteils oder einer Komponente, das zur Kontaktaufnahme mit einer Leiterplatte (PCB) dient. Pins sind entscheidend für die elektrische Verbindung zwischen Bauteilen und der Leiterplatte und kommen in verschiedenen Formen und Anordnungen vor. Hier sind einige wichtige Aspekte zu Pins:
Arten von Pins:
Through-Hole-Pins (THT): Diese Pins werden durch Bohrlöcher auf der Leiterplatte geführt und auf der Rückseite der Platine verlötet. Diese Technik wird häufig bei größeren Bauteilen verwendet, die mechanische Stabilität benötigen.
Surface-Mount-Pins (SMD): Diese Pins sind direkt auf der Oberfläche der Leiterplatte angebracht, ohne durch Löcher geführt zu werden. Diese Technik ist platzsparend und wird häufig bei kleineren, modernen Bauteilen verwendet.
Stiftleisten (Pin Header): Eine Reihe von Pins, die in einer Leiste angeordnet sind und verwendet werden, um Komponenten miteinander zu verbinden oder programmierbare Verbindungen zu schaffen.
Funktionen von Pins:
Signalübertragung: Pins dienen der Übertragung von elektrischen Signalen zwischen einem Bauteil und der Leiterplatte.
Spannungsversorgung: Einige Pins sind speziell dafür vorgesehen, die Stromversorgung sicherzustellen.
Masse (GND): Ein Pin kann auch als Masseanschluss fungieren und den Stromkreis schließen.
Anwendungsbereiche:
ICs (Integrierte Schaltkreise): ICs besitzen oft viele Pins, die für unterschiedliche Funktionen wie Datenübertragung, Stromversorgung und Steuerung verwendet werden.
Steckverbinder: Pins werden auch in Steckverbindern verwendet, um eine Verbindung zwischen zwei Leiterplatten oder zwischen einer Leiterplatte und einem externen Gerät herzustellen.
Fazit:
Pins sind zentrale Elemente in der Elektronik, die elektrische Verbindungen zwischen Bauteilen und Leiterplatten ermöglichen. Ihre Anordnung und Funktion hängen von der jeweiligen Anwendung und den Anforderungen der Schaltung ab.
Vgl. auch → Einsrecktechnik → THT → SMD
- PITCH
- PLATINE
- PLUGGED VIAS
- POLYIMID
- POSITIONSDRUCK
Pitch bezieht sich in der Elektronik auf den Abstand zwischen den Mittelpunkten benachbarter Pins oder Leiterbahnen auf einer Leiterplatte. Der Pitch ist ein wichtiger Faktor im Design von Leiterplatten und elektronischen Komponenten, da er die Packungsdichte und die Platzanforderungen beeinflusst. Hier sind einige wichtige Aspekte zum Pitch:
Bedeutung des Pitch:
Packungsdichte: Ein kleinerer Pitch ermöglicht es, mehr Pins oder Leiterbahnen auf einer gegebenen Fläche unterzubringen, was zu kompakteren Designs führt. Dies ist besonders wichtig bei hochintegrierten Schaltungen (ICs) und feineren Strukturen.
Herstellungstoleranzen: Ein kleinerer Pitch erfordert präzisere Herstellungsverfahren, um sicherzustellen, dass die Pins korrekt positioniert sind und Kurzschlüsse oder offene Verbindungen vermieden werden.
Lötbarkeit: Bei einem kleinen Pitch ist das Löten schwieriger, da der Platz zwischen den Pins reduziert ist. Dies erfordert spezielle Techniken wie Oberflächenmontage (SMD) oder Fine-Pitch-Löten.
Typische Pitch-Werte:
Standard-Pitch: In traditionellen Designs beträgt der Pitch oft 2,54 mm (0,1 Zoll), was bei vielen klassischen Komponenten wie Widerständen oder ICs verwendet wird.
Fine-Pitch: In modernen, miniaturisierten Elektronikbauteilen liegt der Pitch oft bei 0,8 mm, 0,5 mm oder sogar kleiner, was speziell bei Mikroprozessoren und Speicherchips vorkommt.
Ball Grid Array (BGA): Bei BGAs, die viele Pins auf kleiner Fläche haben, kann der Pitch sogar unter 0,5 mm liegen.
Einfluss auf das Design:
Layout: Der Pitch beeinflusst das Layout der Leiterplatte, insbesondere bei Komponenten mit vielen Pins, da er die Breite der Leiterbahnen und die Abstände zwischen ihnen bestimmt.
Testbarkeit: Bei sehr kleinem Pitch können Tests und Inspektionen komplizierter werden, da es schwieriger ist, die einzelnen Pins zu kontaktieren.
Fazit:
Der Pitch ist ein kritischer Faktor im Leiterplattendesign, der die Größe, Komplexität und Fertigbarkeit von elektronischen Bauteilen beeinflusst. Je kleiner der Pitch, desto anspruchsvoller sind die Herstellungsprozesse und desto wichtiger ist die Präzision bei der Produktion.
Vgl. auch → Finepitch
Der Begriff Platine ist ein Synonym für Leiterplatte
Vgl. auch → Leiterplatte
Plugged Vias sind gefüllte Durchkontaktierungen auf einer Leiterplatte (PCB), bei denen die Hohlräume von Vias (Durchkontaktierungen) mit einem speziellen Material, oft Epoxidharz, gefüllt werden. Dies geschieht, um die mechanische Stabilität zu verbessern und um bestimmte elektrische Anforderungen zu erfüllen. Hier sind die wichtigsten Aspekte von Plugged Vias:
Zweck von Plugged Vias:
Vermeidung von Lötfehlern: Offene Vias können während des Lötprozesses Lötpaste aufsaugen, was zu unsachgemäßen Lötverbindungen führen kann. Das Füllen der Vias verhindert dies.
Mechanische Stabilität: Durch das Füllen der Vias wird die mechanische Festigkeit erhöht, was besonders bei feinen Pitch-Komponenten wichtig ist, die enge Toleranzen erfordern.
Vermeidung von Luftblasen: Bei Anwendungen, bei denen hermetische Dichtheit entscheidend ist, verhindert das Füllen der Vias, dass Luftblasen oder Feuchtigkeit eingeschlossen werden.
Materialien zum Füllen:
Epoxidharz: Am häufigsten verwendetes Material, das nach dem Einfüllen aushärtet und eine robuste, feste Struktur bildet.
Leitfähige Materialien: In bestimmten Anwendungen können auch leitfähige Materialien zum Füllen verwendet werden, wenn elektrische Eigenschaften durch das Via verbessert werden sollen.
Vorteile von Plugged Vias:
Erhöhte Zuverlässigkeit: Gefüllte Vias verhindern Defekte während des Lötprozesses und sorgen für eine gleichmäßigere Oberfläche, was die Gesamtzuverlässigkeit der Leiterplatte erhöht.
Geeignet für HDI-Technologie: Besonders in High-Density-Interconnect (HDI)-Platten werden Plugged Vias verwendet, da sie die Packungsdichte erhöhen und eine bessere Kontrolle über Signalwege ermöglichen.
Anwendung:
Leiterplatten mit hohen Anforderungen: Plugged Vias werden oft in High-End-Elektronikprodukten verwendet, wie Mobiltelefonen, medizinischen Geräten oder Automobilkomponenten, wo Zuverlässigkeit und Lötqualität entscheidend sind.
HDI-Leiterplatten: In HDI-Platten, wo Platz knapp ist und viele Durchkontaktierungen nahe beieinander liegen, helfen Plugged Vias, Kurzschlüsse oder mechanische Defekte zu verhindern.
Fazit:
Plugged Vias sind eine wichtige Technik in der Leiterplattenherstellung, um die mechanische Festigkeit zu erhöhen, Lötfehler zu vermeiden und die Gesamtzuverlässigkeit der Platine zu verbessern. Sie spielen eine besondere Rolle bei hochdichten Leiterplattendesigns und in Anwendungen, die hohe Präzision und Beständigkeit erfordern.
Polyimid ist ein hochleistungsfähiges Polymermaterial, das in der Elektronik- und Leiterplattenindustrie weit verbreitet ist. Es zeichnet sich durch eine Kombination von hervorragenden Eigenschaften aus, die es ideal für Anwendungen machen, die hohe Temperaturen, chemische Beständigkeit und elektrische Isolation erfordern. Hier sind die wichtigsten Aspekte von Polyimid:
Eigenschaften von Polyimid:
Hohe Temperaturbeständigkeit: Polyimid kann Temperaturen von bis zu 260 °C (500 °F) oder mehr standhalten, ohne seine physikalischen Eigenschaften zu verlieren. Diese Eigenschaft macht es besonders nützlich für Anwendungen, die thermische Belastungen erfordern.
Chemische Beständigkeit: Polyimid ist resistent gegen viele Chemikalien, einschließlich Lösungsmittel, Säuren und Basen. Diese Beständigkeit ist wichtig in Umgebungen, in denen aggressive Chemikalien eingesetzt werden.
Exzellente elektrische Isolation: Polyimid hat eine hohe Durchschlagfestigkeit und einen niedrigen Dielektrizitätsverlust, was es zu einem hervorragenden Isoliermaterial für elektrische Anwendungen macht.
Gute mechanische Eigenschaften: Polyimid hat eine hohe Festigkeit und Zähigkeit, was es für mechanisch beanspruchte Anwendungen geeignet macht.
Anwendungen in der Leiterplattenindustrie:
Flexible Leiterplatten: Polyimid wird häufig in flexiblen Leiterplatten (FPCs) verwendet, da es sich leicht in verschiedene Formen bringen lässt und gleichzeitig die erforderliche mechanische Stabilität und elektrische Leistung bietet.
Thermisch beanspruchte Anwendungen: In Hochtemperaturumgebungen, wie in der Luft- und Raumfahrt oder in der Automobilindustrie, wird Polyimid häufig als Trägermaterial für Leiterplatten eingesetzt.
Isolationsschichten: Polyimid kann als Dielektrikum in mehrlagigen Leiterplatten oder als Isolationsschicht zwischen Kupferlagen eingesetzt werden.
Vorteile von Polyimid:
Langlebigkeit: Die hohe Temperatur- und chemische Beständigkeit trägt zu einer verlängerten Lebensdauer von Bauteilen bei, die Polyimid verwenden.
Kosteneffizienz: Trotz der hohen Leistung und der vorteilhaften Eigenschaften kann Polyimid kosteneffizient in der Massenproduktion eingesetzt werden.
Fazit:
Polyimid ist ein vielseitiges und leistungsstarkes Material, das in der Elektronik- und Leiterplattenindustrie aufgrund seiner außergewöhnlichen Eigenschaften geschätzt wird. Es bietet eine zuverlässige Lösung für Anwendungen, die hohe Temperaturen, mechanische Belastungen und chemische Einflüsse erfordern, und ist damit ein entscheidender Bestandteil moderner elektrischer und elektronischer Geräte.
Vgl. auch → Flexible Leiterplatte
Positionsdruck bezieht sich auf den Druck von Symbolen oder Markierungen auf einer Leiterplatte, die zur Kennzeichnung der Position von Bauteilen, Lötaugen und anderen wichtigen Elementen dienen. Dieser Druck ist entscheidend für die Herstellung, Montage und Wartung von Leiterplatten. Hier sind die wichtigsten Aspekte des Positionsdrucks:
Funktionen des Positionsdrucks
Identifikation von Bauteilen: Der Positionsdruck enthält Informationen über die Platzierung von Bauteilen auf der Leiterplatte, einschließlich Bauteilnummern, Werte und Typen.
Hilfestellung bei der Montage: Der Positionsdruck erleichtert den Bestückungsprozess, indem er den Technikern hilft, die Bauteile an den richtigen Stellen zu platzieren.
Fehlervermeidung: Durch klare Markierungen und Hinweise können Fehler während der Montage und späteren Wartung minimiert werden.
Typen des Positionsdrucks
SILK-Screen-Druck: Diese Technik verwendet einen Siebdruckprozess, um die Markierungen auf die Oberfläche der Leiterplatte aufzubringen. Sie ist weit verbreitet und ermöglicht eine präzise Platzierung von Text und Symbolen.
Tampondruck: Diese Methode wird häufig für unregelmäßig geformte Oberflächen verwendet und kann auch für den Positionsdruck eingesetzt werden.
Laserdruck: In einigen Fällen wird der Positionsdruck auch mit Lasertechnologie erstellt, um dauerhafte und präzise Markierungen zu gewährleisten.
Material und Farbe
Druckfarbe: Häufig verwendete Farben für den Positionsdruck sind Weiß, Schwarz, Gelb oder andere gut sichtbare Farben. Die Wahl der Farbe hängt von den spezifischen Anforderungen der Anwendung und der Kontrasteigenschaften ab.
Druckmaterialien: Der Druck erfolgt auf der äußeren Schicht der Leiterplatte, die oft mit einem schützenden Überzug versehen ist, um die Markierungen vor Abnutzung und Umwelteinflüssen zu schützen.
Standards und Normen
- IPC-Normen: Der Positionsdruck muss bestimmten Standards entsprechen, die von der IPC (Institute for Printed Circuits) festgelegt wurden. Diese Standards definieren die Qualität und Lesbarkeit des Drucks sowie die Anordnung und Größe der Markierungen.
Fazit
Der Positionsdruck ist ein wesentlicher Bestandteil der Leiterplattenfertigung und -montage. Er verbessert die Benutzerfreundlichkeit und trägt dazu bei, die Qualität und Zuverlässigkeit der elektrischen Verbindungssysteme sicherzustellen. Durch präzise und gut sichtbare Markierungen wird der gesamte Prozess der Herstellung und Wartung von Leiterplatten optimiert.
Vgl. auch → Bestückungsdruck
- PREPREG
- PRINTED CIRCUIT BOARD
- PROTOTYP
- PTH
Prepreg bezieht sich auf ein vorimprägniertes Material, das in der Leiterplattenherstellung verwendet wird. Es handelt sich um eine Kombination aus einer Trägerschicht (normalerweise aus Glasfaser oder anderen Verbundwerkstoffen) und einem Harz, das bereits vor der Anwendung teilweise oder vollständig polymerisiert ist. Hier sind die wichtigsten Aspekte von Prepreg:
Zusammensetzung und Eigenschaften
Materialien: Prepreg wird häufig aus Glasfasergeweben oder -matten hergestellt, die mit einem thermoplastischen oder thermohärtenden Harz imprägniert sind. Diese Materialien bieten eine hervorragende Festigkeit, Leichtigkeit und thermische Stabilität.
Harztypen: Die verwendeten Harze können Epoxidharze, Polyesterharze oder phenolische Harze sein, wobei Epoxidharze aufgrund ihrer guten elektrischen Eigenschaften und Chemikalienbeständigkeit am häufigsten eingesetzt werden.
Viskosität: Die Viskosität des Harzes ist entscheidend für die Verarbeitung. Ein niedrigviskoses Harz ermöglicht eine bessere Durchdringung des Gewebes und eine gleichmäßigere Verteilung der Eigenschaften.
Verwendung in der Leiterplattenherstellung
Schichtenaufbau: Prepreg wird in der Multilayer-Leiterplattenfertigung verwendet, um die verschiedenen Schichten miteinander zu verbinden. Es wird zwischen den Kupferlagen platziert und dann unter Hitze und Druck verpresst, um eine feste Verbindung zu erzeugen.
Imprägnierung: Durch die Imprägnierung des Gewebes mit Harz wird die mechanische Festigkeit der Leiterplatte erhöht, und sie erhält die notwendigen elektrischen Isoliereigenschaften.
Vorteile von Prepreg
Leichtgewicht: Prepreg-Materialien sind in der Regel leichter als herkömmliche Leiterplattenschichten, was sie ideal für Anwendungen im Bereich der Luftfahrt, Raumfahrt und tragbaren Elektronik macht.
Thermische Stabilität: Die thermische Stabilität von Prepreg ermöglicht den Einsatz in Hochtemperaturanwendungen, ohne dass es zu Verformungen oder Materialversagen kommt.
Anpassungsfähigkeit: Prepreg kann in verschiedenen Dicken und Fasermustern hergestellt werden, um spezifische Anforderungen in Bezug auf Flexibilität und Festigkeit zu erfüllen.
Herstellungsprozess
Laminierung: Der Prozess der Laminierung umfasst das Schichten von Prepreg mit Kupferfolien und anderen Materialien, gefolgt von einer thermischen Aushärtung, um eine dauerhafte Verbindung zu schaffen.
Aushärtung: Die Aushärtung erfolgt in der Regel in einem Autoklav, wo Druck und Temperatur kontrolliert werden, um die bestmöglichen Eigenschaften des Materials zu erreichen.
Fazit
Prepreg ist ein entscheidender Bestandteil der modernen Leiterplattenherstellung. Es bietet eine Kombination aus mechanischer Festigkeit, elektrischen Isoliereigenschaften und thermischer Stabilität, die für die Leistung und Zuverlässigkeit elektronischer Geräte unerlässlich sind. Die Wahl des richtigen Prepreg-Materials (i.d.R. gerne FR4) kann die Effizienz und Haltbarkeit von Leiterplatten erheblich beeinflussen.
Vgl. auch → Multilayer → FR4
PCB ist die Abkürzung für Leiterplatte (engl.: Printed Circuit Board)
Vgl. auch → Leiterplatte
Prototyp bezieht sich auf ein erstes, oft vorläufiges Modell oder eine erste Version eines Produkts, das zur Demonstration, Prüfung oder Validierung von Konzepten, Designs oder Funktionen entwickelt wird. In der Elektronik- und Leiterplattenherstellung hat der Prototyp eine entscheidende Bedeutung. Hier sind die wichtigsten Aspekte des Prototyps:
Definition und Zweck
Erste Version: Ein Prototyp ist in der Regel eine frühe Version eines Produkts, die dazu dient, das Konzept zu veranschaulichen und die Machbarkeit zu überprüfen.
Test und Validierung: Prototypen werden verwendet, um das Design zu testen, Funktionen zu validieren und potenzielle Probleme frühzeitig zu identifizieren. Dies hilft, teure Änderungen in späteren Produktionsphasen zu vermeiden.
Typen von Prototypen
Funktionale Prototypen: Diese Prototypen sind darauf ausgelegt, die grundlegenden Funktionen und Merkmale des Endprodukts zu demonstrieren. Sie können aus Standardkomponenten bestehen und sind oft nicht für die Massenproduktion gedacht.
Ästhetische Prototypen: Diese Prototypen konzentrieren sich auf das Design und die Benutzererfahrung. Sie dienen dazu, das äußere Erscheinungsbild und die Benutzeroberfläche zu visualisieren.
Technische Prototypen: Diese Modelle beinhalten technische Details, die für die endgültige Produktion wichtig sind. Sie können spezifische Materialien und Prozesse darstellen, die in der Massenproduktion verwendet werden sollen.
Vorteile von Prototypen
Frühe Identifizierung von Fehlern: Prototypen ermöglichen es den Entwicklern, potenzielle Probleme im Design oder in der Funktionalität frühzeitig zu erkennen, bevor in die Massenproduktion investiert wird.
Kosteneffizienz: Durch die Identifizierung und Behebung von Problemen in der Prototypenphase können die Gesamtkosten für das Projekt gesenkt werden.
Feedback von Benutzern: Prototypen können an Benutzer oder Testgruppen weitergegeben werden, um Feedback zur Benutzerfreundlichkeit und Funktionalität zu erhalten. Dies kann wertvolle Informationen für die Verbesserung des Designs liefern.
Herstellungsprozess
Rapid Prototyping: Moderne Techniken wie 3D-Druck, CNC-Bearbeitung und andere additive Fertigungsverfahren ermöglichen die schnelle Herstellung von Prototypen. Dies verkürzt die Entwicklungszeit erheblich.
Iterativer Prozess: Der Prototypenprozess ist oft iterativ, was bedeutet, dass Designs mehrfach überarbeitet und getestet werden, um das beste Endprodukt zu erzielen.
Fazit
Prototypen spielen eine wesentliche Rolle in der Produktentwicklung, insbesondere in der Elektronik und Leiterplattenherstellung. Sie ermöglichen es Entwicklern, Konzepte zu testen, Feedback zu sammeln und Designs zu optimieren, bevor sie in die Massenproduktion gehen. Die Investition in Prototypen kann langfristig zu Kosteneinsparungen und einer höheren Produktqualität führen.
PTH steht für Plated Through Hole, was sich auf eine Art von Bohrung in Leiterplatten bezieht, die mit einer metallischen Schicht überzogen ist. Diese Technik wird verwendet, um elektrische Verbindungen zwischen den verschiedenen Schichten einer Leiterplatte herzustellen. Hier sind einige wichtige Aspekte von PTH:
Definition und Merkmale
Durchkontaktierung: PTH bezeichnet Bohrungen, die durch die gesamte Dicke der Leiterplatte gehen und auf beiden Seiten mit einer Kupferschicht versehen sind. Diese Schichten werden galvanisch aufgebracht, um eine zuverlässige elektrische Verbindung zu gewährleisten.
Verbindungen: PTH ermöglicht die Verbindung von Bauteilen, die auf verschiedenen Seiten der Leiterplatte angebracht sind, sowie die Übertragung von Signalen und Strom zwischen den inneren und äußeren Schichten einer multilayer Leiterplatte.
Vorteile von PTH
Zuverlässige Verbindungen: Durch die metallische Beschichtung werden stabile elektrische Verbindungen gewährleistet, die den Anforderungen an verschiedene Anwendungen standhalten.
Einfache Montage: PTH-Bauteile können einfach in die Bohrungen eingesetzt und gelötet werden, was die Herstellung und Montage von Leiterplatten erleichtert.
Höhere mechanische Festigkeit: PTH bietet aufgrund der Verbindung zwischen der Bohrung und der Leiterplatte eine höhere mechanische Stabilität im Vergleich zu nicht metallisierten Durchbohrungen.
Anwendungen
Standardanwendungen: PTH wird häufig in der Herstellung von herkömmlichen Leiterplatten verwendet, insbesondere in der Konsumerelektronik, der Automobilindustrie und der Telekommunikation.
Hochleistungsanwendungen: In Anwendungen, die hohe elektrische Lasten erfordern, wie z.B. in Leistungselektronik und Industriegeräten, sind PTH-Verbindungen besonders wichtig.
Herstellung
Bohrung: Die PTH-Bohrung wird im Herstellungsprozess der Leiterplatte vorgenommen, in der Regel durch mechanisches Bohren.
Galvanische Beschichtung: Nach dem Bohren wird die Innenoberfläche der Bohrung galvanisch mit Kupfer beschichtet, um die elektrische Verbindung herzustellen.
Fazit
PTH ist eine wesentliche Technologie in der Leiterplattenherstellung, die eine zuverlässige elektrische Verbindung zwischen den verschiedenen Schichten einer Leiterplatte ermöglicht. Durch ihre Robustheit und Flexibilität finden PTH-Bohrungen breite Anwendung in vielen elektronischen Geräten und Systemen.
Vgl. auch → Durchkontaktierung → NPTH
- QFN
- QFP
QFN steht für Quad Flat No-lead Package und ist ein beliebtes Gehäusedesign für integrierte Schaltungen (ICs). Es handelt sich um eine flache Bauform ohne sichtbare Anschlussdrähte, die sich durch ihre kompakte und effiziente Bauweise auszeichnet. Hier sind einige wichtige Aspekte des QFN-Gehäuses:
Definition und Merkmale
Flachbauweise: QFN-Gehäuse sind relativ flach und haben eine quadratische oder rechteckige Form. Die geringen Abmessungen machen sie ideal für Anwendungen, in denen der Platz auf der Leiterplatte begrenzt ist.
Kein Anschlussdraht: Im Gegensatz zu traditionellen Gehäusen wie TQFP (Thin Quad Flat Package) haben QFN-Gehäuse keine sichtbaren Anschlussdrähte, sondern Flächenanschlüsse (Pads) auf der Unterseite. Dies ermöglicht eine bessere thermische Leistung und Signalintegrität.
Vorteile von QFN
Kompakte Größe: QFN-Gehäuse sind sehr kompakt und sparen Platz auf der Leiterplatte, was besonders in tragbaren und miniaturisierten Geräten von Vorteil ist.
Gute Wärmeableitung: Das Design der QFN-Pakete ermöglicht eine effiziente Wärmeableitung über die Pads auf der Unterseite, was die thermische Leistung verbessert.
Verbesserte elektrische Eigenschaften: Die kurzen Verbindungslängen zwischen Chip und Leiterplatte verringern die Induktivität, was zu besseren Hochfrequenzeigenschaften führt.
Anwendungen
Mobilgeräte: QFN-Gehäuse werden häufig in Smartphones, Tablets und anderen tragbaren Geräten verwendet, wo der Platz begrenzt ist.
Automobiltechnik: Aufgrund ihrer Robustheit und Effizienz finden sie auch Anwendung in der Automobilindustrie, insbesondere in Steuergeräten und Sensoren.
Industrielle Anwendungen: In der Industrie werden QFN-Gehäuse für verschiedene Anwendungen eingesetzt, einschließlich Steuerungen und Kommunikationsmodulen.
Herstellung und Montage
Bauprozess: QFN-Gehäuse werden in der Regel durch ein Molding-Verfahren hergestellt, bei dem das Silizium-Die in ein Kunststoffgehäuse eingeformt wird.
Montage: Die Montage erfolgt oft durch Reflow-Löten, wobei das Gehäuse direkt auf die Pads auf der Leiterplatte platziert und anschließend erhitzt wird, um eine Verbindung herzustellen.
Fazit
QFN-Gehäuse bieten eine kompakte und effiziente Lösung für die Integration von Schaltungen in elektronischen Geräten. Mit ihren Vorteilen in Bezug auf Größe, Wärmeableitung und elektrische Leistung sind sie eine beliebte Wahl in verschiedenen Anwendungen, von Mobilgeräten bis hin zu industriellen Steuerungssystemen.
Vgl. auch → QFP
QFP steht für Quad Flat Package und ist ein weit verbreitetes Gehäusedesign für integrierte Schaltungen (ICs). Es handelt sich um ein flaches Gehäuse mit Anschlussdrähten auf allen vier Seiten, das häufig in der Elektronikindustrie eingesetzt wird. Hier sind einige wichtige Aspekte des QFP-Gehäuses:
Definition und Merkmale
Flachbauweise: QFP-Gehäuse sind flach und quadratisch oder rechteckig. Sie zeichnen sich durch eine geringe Bauhöhe aus, was sie ideal für Anwendungen mit Platzbeschränkungen macht.
Anschlussdrähte: Die Anschlussdrähte sind an den vier Seiten des Gehäuses angeordnet, was eine einfache Montage auf der Leiterplatte ermöglicht. Die Drähte sind in der Regel dünn und können entweder im BGA- oder im TQFP-Stil verlötet werden.
Vorteile von QFP
Kompakte Größe: QFP-Gehäuse benötigen weniger Platz auf der Leiterplatte als herkömmliche DIL-Gehäuse, was sie ideal für Anwendungen in tragbaren Geräten und anderen kompakten Designs macht.
Gute thermische Leistung: Die flache Bauweise ermöglicht eine effektive Wärmeableitung, wodurch die Temperatur des ICs während des Betriebs gesenkt wird.
Vielseitigkeit: QFP-Gehäuse sind in verschiedenen Größen und Pin-Anzahlen erhältlich, was sie für eine breite Palette von Anwendungen geeignet macht.
Anwendungen
Mobilgeräte: QFP-Gehäuse finden sich häufig in Smartphones, Tablets und anderen tragbaren Geräten, in denen der Platz auf der Leiterplatte begrenzt ist.
Automobiltechnik: Sie werden auch in der Automobilindustrie eingesetzt, insbesondere in Steuergeräten und Sensoren.
Industrielle Elektronik: In der Industrie finden QFPs Anwendung in Steuerungen, Kommunikationsmodulen und anderen elektronischen Systemen.
Herstellung und Montage
Bauprozess: QFP-Gehäuse werden in der Regel durch ein Molding-Verfahren hergestellt, bei dem das Silizium-Die in ein Kunststoffgehäuse eingeformt wird.
Montage: Die Montage erfolgt oft durch Reflow-Löten, bei dem das Gehäuse auf die Pads auf der Leiterplatte platziert und erhitzt wird, um eine Verbindung herzustellen.
Fazit
QFP-Gehäuse bieten eine vielseitige und kompakte Lösung für die Integration von Schaltungen in elektronischen Geräten. Mit ihren Vorteilen in Bezug auf Größe, thermische Leistung und Flexibilität sind sie eine beliebte Wahl für eine Vielzahl von Anwendungen in der Elektronikindustrie.
Vgl. auch → QFPN
- RATSNEST
- REFERENZMARKEN
- RESIST
- RESTRING
- RIGID FLEX
Ratsnest ist ein Begriff aus der Leiterplatten-Design-Software und beschreibt eine Darstellung aller ungerouteten Verbindungen (Luftlinien) zwischen den Pads oder Bauteilen einer Leiterplatte. Diese Linien zeigen, wie die elektrischen Verbindungen zwischen den Bauteilen hergestellt werden müssen, bevor die endgültigen Leiterbahnen entworfen und verlegt werden.
Wichtige Aspekte des Ratsnests
Visuelle Darstellung: Ein Ratsnest sieht oft wie ein chaotisches Netz aus, da es alle Verbindungen in Form von geraden Linien darstellt. Diese Linien symbolisieren den kürzesten Weg zwischen den zu verbindenden Pads oder Bauteilen.
Routing-Hilfe: Das Ratsnest dient als Hilfsmittel im Designprozess, um sicherzustellen, dass alle Verbindungen vorhanden sind und der Designer sie nach Bedarf auf der Leiterplatte routen kann.
Optimierung des Layouts: Durch das Anzeigen des Ratsnests kann der Designer erkennen, wie die Bauteile optimal platziert werden können, um möglichst kurze Leiterbahnen zu erhalten und Kreuzungen zu vermeiden.
Routingschritt: Nachdem das Ratsnest angezeigt wurde, beginnt der Designer mit dem tatsächlichen Routing, bei dem die Luftlinien in reale Leiterbahnen umgewandelt werden. Das Ziel ist es, die Verbindungen so zu verlegen, dass elektrische Signalintegrität gewährleistet ist und dabei möglichst wenig Platz verbraucht wird.
Fazit
Das Ratsnest ist ein unverzichtbares Tool während der Leiterplattenentwicklung. Es erleichtert die Planung und Optimierung der Platzierung und des Routings, um eine funktionale und effiziente Leiterplatte zu erstellen.
Siehe→ Passermarken
Resist ist ein lichtempfindliches Material, das in der Leiterplattenherstellung eingesetzt wird, um bestimmte Bereiche einer Leiterplatte während des Herstellungsprozesses zu schützen oder zu definieren. Es dient als Maske, um Bereiche entweder vor Ätz- oder Galvanikprozessen zu schützen oder sie selektiv diesen Prozessen auszusetzen. Es gibt zwei Hauptarten von Resist: Fotolack (Photoresist) und Lötstopplack.
Arten von Resist
Photoresist (Fotolack):
- Ein lichtempfindliches Material, das auf die Leiterplatte aufgetragen wird.
- Durch Belichtung mit UV-Licht durch eine Fotomaske oder direkt durch einen Laserdirektbelichter werden gezielt Bereiche des Photoresists aktiviert oder deaktiviert.
- Je nach Resist-Typ (positiver oder negativer Resist) werden entweder die belichteten oder unbelichteten Bereiche im nachfolgenden Entwicklungsschritt entfernt.
- Genutzt, um während des Ätzvorgangs die Kupferschichten in den gewünschten Bereichen zu schützen.
Lötstopplack:
- Wird verwendet, um Bereiche der Leiterplatte vor Lötzinn zu schützen und nur die Lötstellen (Pads) freizuhalten.
- Dieser Lack verhindert Kurzschlüsse zwischen eng beieinanderliegenden Leiterbahnen und schützt die Kupferschicht vor Korrosion.
Funktionen des Resist
Schutz vor Ätzen: Beim Ätzprozess schützt der Resist bestimmte Bereiche der Kupferschicht, sodass nur ungeschützte Bereiche weggeätzt werden.
Schutz beim Galvanisieren: In galvanischen Prozessen kann der Resist dafür sorgen, dass nur bestimmte Bereiche durch zusätzliche Metallschichten verstärkt werden, während andere Bereiche unberührt bleiben.
Definierung von Leiterbahnen: Der Resist hilft, die gewünschten Leiterbahnen und Pads auf der Leiterplatte zu erzeugen, indem er die zu schützenden Bereiche während des Ätzprozesses abdeckt.
Schutz der Leiterplatte: Der Lötstopplack verhindert unerwünschte Brückenbildung zwischen Bauteilen und schützt die Kupferleiterbahnen vor Umwelteinflüssen.
Fazit
Resist ist ein zentrales Material in der Herstellung von Leiterplatten und spielt eine entscheidende Rolle bei der Präzision und Qualität der Schaltungen. Es ermöglicht das gezielte Ätzen und Galvanisieren und schützt die Leiterplatte in wichtigen Produktionsschritten.
Restring bezeichnet in der Leiterplattentechnik den Kupferring, der die Bohrlöcher (Pads) einer durchkontaktieren oder nicht durchkontaktierten Bohrung auf einer Leiterplatte umgibt. Der Restring ist wichtig, um eine stabile mechanische Verbindung und gute elektrische Leitfähigkeit zwischen den Leiterbahnen und den durchkontaktierten Bohrungen zu gewährleisten. Er spielt eine zentrale Rolle bei der Montage und Funktion von Bauteilen auf der Leiterplatte.
Wichtige Aspekte des Restrings
Definition und Funktion:
- Der Restring ist der Ring aus Kupfer, der um das Bohrloch auf der Leiterplatte bleibt, nachdem das Loch gebohrt wurde.
- Er stellt sicher, dass das Bohrloch eine ausreichende Kupferfläche aufweist, um eine elektrische Verbindung zwischen den Schichten der Leiterplatte herzustellen.
- Besonders wichtig bei vias (Durchkontaktierungen), die verschiedene Schichten einer Multilayer-Leiterplatte elektrisch verbinden.
Größe und Design:
- Der Durchmesser des Restrings ist ein kritischer Faktor, da er genügend Fläche bieten muss, um eine stabile elektrische und mechanische Verbindung zu gewährleisten.
- Der Restring darf nicht zu klein sein, da dies zu Ausbrüchen führen kann, bei denen die Durchkontaktierung beschädigt wird.
- Andererseits muss der Restring kompakt genug sein, um Platz auf der Leiterplatte zu sparen und dichte Schaltungen zu ermöglichen.
- Der Restring-Durchmesser setzt sich aus dem Bohrlochdurchmesser und einem Sicherheitsabstand (Kupferring) zusammen.
Probleme bei zu kleinen Restrings:
- Breakout: Dies tritt auf, wenn der Bohrlochdurchmesser fast so groß wie der Restring ist und dieser auf einer Seite ausbricht, was die elektrische Verbindung gefährden kann.
- Herstellungsprobleme: Zu kleine Restrings können zu Toleranzproblemen bei der Produktion führen und die Zuverlässigkeit der Leiterplatte beeinträchtigen.
Designregeln:
- Die genauen Abmessungen des Restrings hängen von den Design-Richtlinien des jeweiligen Leiterplattenherstellers ab.
- Übliche Richtwerte sind: Der Restring sollte mindestens 0,15 mm Breite haben, abhängig von der Art der Leiterplatte und den spezifischen Anforderungen der Anwendung.
Fazit
Der Restring ist ein unverzichtbarer Bestandteil der Leiterplattentechnik und trägt maßgeblich zur elektrischen Verbindung und mechanischen Stabilität bei. Seine Größe und Platzierung müssen sorgfältig geplant werden, um eine hohe Zuverlässigkeit der Leiterplatte sicherzustellen, insbesondere in komplexen Multilayer-Designs.
Vgl. auch → Durchkontaktierung
Wichtige Merkmale von Rigid-Flex-Leiterplatten
Aufbau und Struktur:
- Starre Bereiche bestehen aus herkömmlichen starren Materialien (z. B. FR4), die für mechanische Stabilität und Robustheit sorgen.
- Flexible Bereiche bestehen aus flexiblen Materialien wie Polyimid, die Biegung und Bewegung ermöglichen.
- Die flexiblen Abschnitte verbinden die starren Teile und bieten Flexibilität für Anwendungen, bei denen Bauteile bewegt oder gefaltet werden müssen.
Vorteile von Rigid-Flex-Leiterplatten:
- Platzersparnis: Durch die Integration starrer und flexibler Teile in einer einzigen Leiterplatte können Bauteile platzsparender angeordnet werden.
- Zuverlässigkeit: Weniger Steckverbindungen und Kabelverbindungen bedeuten weniger potenzielle Fehlerquellen und höhere Zuverlässigkeit.
- Dynamische Flexibilität: Die flexiblen Bereiche können wiederholte Biegungen und Bewegungen überstehen, ohne die elektrische Integrität zu beeinträchtigen.
- Leichter und kompakter: Rigid-Flex-Designs ermöglichen leichtere und kompaktere Baugruppen, was in vielen modernen Geräten wichtig ist.
Anwendungen:
- Medizinische Geräte: In tragbaren oder implantierbaren medizinischen Geräten, wo Zuverlässigkeit und Platzoptimierung entscheidend sind.
- Luft- und Raumfahrt: In Bereichen, in denen geringe Größe, Gewicht und hohe Zuverlässigkeit wichtig sind.
- Verbraucherelektronik: In mobilen Geräten wie Smartphones, Laptops oder Wearables, bei denen ein schlankes Design erforderlich ist.
Design und Herstellung:
- Rigid-Flex-Leiterplatten erfordern spezielle Designregeln, um sicherzustellen, dass sowohl die starren als auch die flexiblen Bereiche ordnungsgemäß funktionieren.
- Die Herstellung ist komplexer als bei herkömmlichen starren oder flexiblen Leiterplatten, da mehrere Materialien und Fertigungstechniken kombiniert werden müssen.
Fazit
Rigid-Flex-Leiterplatten bieten eine optimale Lösung für Anwendungen, die sowohl mechanische Festigkeit als auch Flexibilität erfordern. Sie sind besonders geeignet für platzsparende Designs in hochkomplexen und anspruchsvollen Anwendungen, wie in der Luft- und Raumfahrt, Medizintechnik und modernen Konsumgütern.
Vgl. auch → Starrflex
- RITZEN
- RoHS
- ROUTING
- RTI
- RÜSTKOSTEN
Ritzen in der Leiterplattenfertigung bezeichnet einen mechanischen Bearbeitungsprozess, bei dem V-förmige Kerben oder Einkerbungen in die Leiterplatte geschnitten werden, um sie später leicht in kleinere Teile trennen zu können. Dieser Prozess wird auch als V-Scoring bezeichnet und ist eine übliche Methode, um Leiterplatten effizient zu panelisieren und anschließend zu vereinzeln.
Wichtige Aspekte des Ritzens
V-förmige Kerben: Beim Ritzen werden die Ober- und Unterseite der Leiterplatte durch eine präzise Schneidmaschine angeritzt, sodass eine schwächer strukturierte Verbindung entsteht. Diese ermöglicht es, die Platten später manuell oder maschinell zu brechen.
Tiefe des Ritzens: Die Tiefe der V-Kerben ist entscheidend und wird so angepasst, dass die Platten fest zusammengehalten werden, aber dennoch leicht gebrochen werden können. Üblicherweise bleiben etwa 1/3 bis 1/4 der ursprünglichen Materialdicke erhalten.
Vermeidung von Abfällen: Im Gegensatz zu anderen Trennverfahren wie Fräsen, bei dem Material verloren geht, entsteht beim Ritzen kaum Materialabfall. Dies macht es besonders für Leiterplatten mit dichter Bauteilanordnung oder bei geringen Toleranzen vorteilhaft.
Anwendung bei Panelisierung: Das Ritzen wird häufig bei der Produktion von Leiterplatten verwendet, die in einem größeren Panel gefertigt und erst nach der Bestückung in einzelne Platinen getrennt werden. Dies spart Platz in der Fertigung und erleichtert die automatisierte Bestückung.
Vorteile des Ritzens
Effizienz: Es ermöglicht eine schnelle und kostengünstige Trennung von Leiterplatten.
Geringer Platzbedarf: Da beim Ritzen keine breiten Trennränder erforderlich sind, können die Leiterplatten sehr dicht aneinander angeordnet werden, was die Materialnutzung maximiert.
Saubere Trennlinien: Die V-Kerben sorgen für saubere Trennstellen ohne großen mechanischen Aufwand.
Einschränkungen
Beschränkung der Formen: Das Ritzen eignet sich nur für rechteckige oder quadratische Leiterplatten, da die geraden Schnitte keine komplexen Formen ermöglichen.
Strukturelle Schwächung: Das Ritzen schwächt die Struktur der Leiterplatte, was bei sehr dünnen oder flexiblen Materialien problematisch sein kann.
Fazit
Das Ritzen ist eine effektive Methode zur Trennung von Leiterplatten mit hoher Präzision und minimalem Materialverlust. Es ist besonders nützlich für die Serienfertigung, wo eine hohe Produktionsrate und eine effiziente Materialnutzung erforderlich sind.
Vgl. auch → Fräsen
RoHS steht für „Restriction of Hazardous Substances“ und ist eine Richtlinie der Europäischen Union, die die Verwendung bestimmter gefährlicher Stoffe in Elektro- und Elektronikgeräten einschränkt. Ziel dieser Richtlinie ist es, die Umwelt zu schützen und die menschliche Gesundheit zu fördern, indem die Menge gefährlicher Chemikalien in Elektrogeräten reduziert wird.
Wesentliche Aspekte von RoHS
Eingeschränkte Stoffe: Die RoHS-Richtlinie begrenzt die Verwendung von sechs gefährlichen Stoffen, die in Elektro- und Elektronikgeräten verwendet werden:
- Blei (Pb)
- Quecksilber (Hg)
- Cadmium (Cd)
- Sechswertiges Chrom (Cr6+)
- Polybromierte Biphenyle (PBB)
- Polybromierte Diphenylether (PBDE)
Eine aktualisierte Version von RoHS, genannt RoHS 2, hat zusätzliche Stoffe hinzugefügt und erlaubt nur sehr geringe Konzentrationen dieser Substanzen in Produkten.
Zulässige Grenzwerte: Die meisten dieser Stoffe dürfen nur in Konzentrationen von bis zu 0,1 % (1000 ppm) in homogenen Materialien eines Produkts enthalten sein. Cadmium ist mit einer Konzentration von maximal 0,01 % (100 ppm) noch stärker reguliert.
Anwendungsbereiche: RoHS gilt für eine breite Palette von Elektro- und Elektronikgeräten, einschließlich:
- Haushaltsgeräte
- Unterhaltungselektronik
- IT- und Telekommunikationsausrüstung
- Beleuchtung
- Elektrowerkzeuge
- Spielzeug
Kennzeichnung: Produkte, die den RoHS-Vorgaben entsprechen, tragen häufig ein spezielles RoHS-Zertifikat oder eine Kennzeichnung, die ihre Konformität signalisiert.
Vorteile von RoHS
Umweltschutz: Die Beschränkung gefährlicher Stoffe reduziert die Belastung durch Elektronikschrott, der oft unsachgemäß entsorgt wird und die Umwelt schädigen kann.
Gesundheit: Weniger gefährliche Substanzen in elektronischen Produkten tragen zum Schutz der Gesundheit von Verbrauchern und Arbeitern bei, die mit der Herstellung und Entsorgung dieser Geräte in Kontakt kommen.
Internationale Norm: Viele andere Länder und Regionen haben ähnliche Vorschriften wie RoHS übernommen, was es zu einem global anerkannten Standard macht.
Herausforderungen
Produktentwicklung: Die Umstellung auf RoHS-konforme Materialien kann für Hersteller kostspielig und technisch anspruchsvoll sein, insbesondere in Bezug auf die Umstellung auf bleifreie Lötprozesse.
Überwachung und Konformität: Hersteller müssen sicherstellen, dass alle Materialien und Komponenten ihrer Produkte die RoHS-Vorschriften einhalten, was umfangreiche Tests und Zertifizierungen erfordert.
Fazit
Die RoHS-Richtlinie ist ein wesentlicher Bestandteil globaler Bemühungen, die Umweltauswirkungen von Elektronikprodukten zu reduzieren und die menschliche Gesundheit zu schützen. Sie stellt hohe Anforderungen an Hersteller, um sicherzustellen, dass ihre Produkte den geltenden Vorschriften entsprechen.
Routing bezieht sich in der Leiterplattentechnologie auf den Prozess des Entwerfens und Erstellens der elektrischen Verbindungen (Leiterbahnen) zwischen den verschiedenen Bauteilen einer Leiterplatte (PCB). Der Routing-Prozess ist entscheidend für die Funktionalität, Leistung und Zuverlässigkeit der elektronischen Schaltungen. Hier sind einige wesentliche Aspekte des Routings:
Aspekte des Routings
1. Design- und Layout-Tools
Moderne PCB-Design-Software bietet eine Vielzahl von Werkzeugen für das Routing, die es den Designern ermöglichen, die Leiterbahnen effizient zu platzieren und zu optimieren. Diese Tools können automatisch Leiterbahnen generieren oder dem Designer helfen, manuelle Anpassungen vorzunehmen.
2. Leiterbahnen und Abstände
Die Breite der Leiterbahnen wird basierend auf den elektrischen Anforderungen, der Stromstärke und der Wärmeableitung gewählt. Auch die Abstände zwischen den Leiterbahnen müssen eingehalten werden, um Kurzschlüsse und andere elektrische Probleme zu vermeiden. Design-Rules-Checks (DRC) helfen dabei, diese Abstände automatisch zu überprüfen.
3. Schichten und Layer
In Mehrschicht-PCBs wird das Routing über mehrere Schichten durchgeführt, wobei bestimmte Schichten für die Signalleitungen und andere für die Masse oder die Versorgungsspannung verwendet werden. Das Design muss so gestaltet sein, dass Signale effizient zwischen den verschiedenen Schichten geroutet werden können, oft unter Verwendung von Durchkontaktierungen (Vias).
4. Signalintegrität
Die Gestaltung des Routings hat direkte Auswirkungen auf die Signalqualität. Faktoren wie die Länge der Leiterbahnen, die Art der verwendeten Materialien und die Anordnung der Bauteile müssen berücksichtigt werden, um Signalverluste, Übersprechen und Reflexionen zu minimieren.
5. Thermisches Management
Richtiges Routing kann dazu beitragen, die Wärmeableitung zu verbessern. Bei Hochstromanwendungen kann es erforderlich sein, bestimmte Leiterbahnen breiter zu gestalten oder zusätzliche Masseflächen zu integrieren, um die Wärme effizient abzuleiten.
6. Design für die Fertigung (DFM)
Ein gutes Routing berücksichtigt auch die Anforderungen und Möglichkeiten der Fertigung. Durch ein optimiertes Routing können Produktionsfehler reduziert und die Fertigungskosten gesenkt werden.
Fazit
Routing ist ein kritischer Schritt im PCB-Designprozess, der die Leistung und Zuverlässigkeit elektronischer Schaltungen maßgeblich beeinflusst. Es erfordert sorgfältige Planung und Berücksichtigung verschiedener Faktoren, um eine effektive und effiziente elektrische Verbindung zwischen den Bauteilen herzustellen.
Vgl. auch → Autorouter
Aspekte des RTI
1. Bedeutung des RTI
Der RTI ist entscheidend für die Auswahl von Materialien in Anwendungen, die hohen Temperaturen ausgesetzt sind, wie z.B. in der Automobil- oder Luftfahrtindustrie. Ein höherer RTI-Wert bedeutet, dass das Material bei höheren Temperaturen eingesetzt werden kann, ohne dass es zu einer signifikanten Verschlechterung der Eigenschaften kommt.
2. Testmethoden
Der RTI wird normalerweise durch standardisierte Tests bestimmt, bei denen Materialien in einer kontrollierten Umgebung bei verschiedenen Temperaturen getestet werden. Die Bestimmung erfolgt häufig unter Verwendung von Prüfstandards wie UL 746B, die spezifische Prüfmethoden zur Bewertung der thermischen Leistung von Kunststoffen und anderen Materialien festlegen.
3. Anwendungsbereiche
- Leiterplattenmaterialien: Der RTI ist ein entscheidendes Kriterium für die Auswahl von Epoxidharzen und anderen Materialien, die in der Herstellung von Leiterplatten verwendet werden, insbesondere in Anwendungen, die hohe thermische Belastungen aufweisen.
- Elektronische Bauteile: Auch bei der Auswahl von Bauteilen, die in Hochtemperaturumgebungen arbeiten, spielt der RTI eine wichtige Rolle.
4. Zusammenhang mit anderen Werten
Der RTI steht im Zusammenhang mit anderen thermischen Kennwerten, wie dem Glass Transition Temperature (Tg) und der Thermal Decomposition Temperature (Td). Ein höherer RTI-Wert ist oft ein Indikator für ein Material mit einer höheren Tg, was bedeutet, dass es bei höheren Temperaturen stabiler ist.
Fazit
Der RTI ist ein wichtiger Parameter zur Bewertung der Temperaturbeständigkeit von Materialien in der Leiterplattentechnologie. Die Auswahl von Materialien mit einem geeigneten RTI ist entscheidend für die Zuverlässigkeit und Leistung von elektronischen Geräten, insbesondere in Anwendungen, die extremen thermischen Bedingungen ausgesetzt sind.
Die Rüstkosten in der Leiterplattenfertigung beziehen sich auf die Kosten, die für die Einrichtung und Vorbereitung der Maschinen und Werkzeuge anfallen, um eine Leiterplattenproduktion zu starten. Diese Kosten sind unabhängig von der Stückzahl und treten vor allem bei der Produktion von Prototypen, Kleinserien oder bei häufigen Wechseln der Leiterplattenlayouts auf. Im Vergleich zur Massenfertigung wirken sich Rüstkosten bei kleinen Chargen stärker auf den Stückpreis aus.
Wichtige Aspekte der Rüstkosten in der Leiterplattenproduktion
Maschineneinrichtung: Dies umfasst das Einrichten von Bohrmaschinen, Ätzmaschinen, Druckern für Bestückungsdruck und Lötstopplack, sowie von Bestückungsautomaten. Jede Maschine muss auf das spezifische Layout der Leiterplatte abgestimmt werden.
Werkzeugwechsel und Anpassungen: Unterschiedliche Werkzeuge, wie z. B. Fräser und Bohrer, müssen je nach Design der Leiterplatte und den Materialien, die verwendet werden, gewechselt und angepasst werden.
Testläufe und Kalibrierung: Vor dem eigentlichen Produktionslauf sind oft Testläufe notwendig, um sicherzustellen, dass die Maschinen korrekt arbeiten und das Design einwandfrei umgesetzt wird. Dies ist besonders wichtig, um mögliche Fehler im Produktionsprozess zu identifizieren.
Vorbereitung der Materialien: Materialien wie Kupferlaminate, Lötstopplacke oder Bauteile müssen bereitgestellt und für den Produktionsprozess vorbereitet werden. Dies kann ebenfalls zusätzliche Zeit und Ressourcen in Anspruch nehmen.
Software-Setup und Programmierung: Je nach Komplexität des Designs müssen CAD-Daten eingelesen und Maschinenprogramme erstellt oder angepasst werden, um die spezifischen Leiterplattenlayouts zu fertigen.
Maßnahmen zur Reduzierung von Rüstkosten
Optimierung der Prozesse: Durch die Einführung standardisierter Verfahren und die Optimierung von Rüstzeiten können die Kosten reduziert werden. Methoden wie SMED (Single-Minute Exchange of Die) zielen darauf ab, Rüstzeiten signifikant zu verkürzen.
Batch-Produktion: Das Zusammenfassen von Aufträgen ähnlicher Designs oder das Nutzen von Mischnutzen kann helfen, die Rüstkosten auf mehrere Produkte zu verteilen.
Automatisierung: Der Einsatz von automatisierten Systemen zur Einrichtung und zum Materialhandling kann die Rüstzeiten verkürzen und menschliche Fehler minimieren.
Fazit
Die Rüstkosten spielen in der Leiterplattenfertigung, insbesondere bei kleinen Produktionsmengen, eine entscheidende Rolle. Durch eine gute Planung und die Implementierung effizienter Rüstprozesse können diese Kosten minimiert werden, was die Wettbewerbsfähigkeit und Rentabilität der Produktion steigern kann.
- SACKLÖCHER
- SCHABLONE
- SCHALTPLAN
- SCHEMATIC
- SCHLIFFBILD
Sacklöcher sind spezielle Bohrungen auf Leiterplatten, die nur von einer Seite der Platine ausgeführt werden und nicht vollständig durch die gesamte Leiterplatte hindurchgehen. Sie enden innerhalb einer oder mehrerer Zwischenschichten und werden häufig in Multilayer-Leiterplatten verwendet, um Platz zu sparen und komplexere Schaltkreise zu ermöglichen.
Merkmale und Einsatzbereiche von Sacklöchern
Definition und Struktur
Sacklöcher sind Bohrungen, die nur in eine bestimmte Tiefe innerhalb der Leiterplatte reichen, ohne die gesamte Dicke der Platine zu durchdringen. Sie verbinden die äußere Lage der Platine mit einer oder mehreren Innenlagen, jedoch nicht die gegenüberliegende Seite, wie es bei Durchgangsbohrungen der Fall ist.
Vorteile von Sacklöchern
- Platzersparnis: Da sie nicht durch die gesamte Platine gehen, bieten Sacklöcher eine höhere Dichte für Leiterbahnen und Bauteile auf komplexen Multilayer-Leiterplatten.
- Verbesserte elektrische Leistung: Die Reduktion der Lochanzahl durch Sacklöcher reduziert das Signalrauschen und kann die Übertragungsqualität in Hochfrequenzanwendungen verbessern.
- Gewichtseinsparung: Im Vergleich zu durchgehenden Vias verringern Sacklöcher das Materialvolumen, was das Gewicht der Platine reduziert.
Herstellungsverfahren
Sacklöcher werden oft durch Laserbohren erstellt, da diese Methode eine präzise Kontrolle der Bohrtiefe ermöglicht. Nach dem Bohren werden sie typischerweise galvanisiert, um eine leitfähige Verbindung zu schaffen.
Anwendungsbereiche
Sacklöcher kommen oft in HDI (High-Density Interconnect)-Leiterplatten zum Einsatz, die in kompakten und komplexen Anwendungen wie Mobilgeräten, Luft- und Raumfahrt sowie Automobil-Elektronik verwendet werden. Auch bei Leiterplatten, die hohe Schaltungsdichte erfordern und nur begrenzten Platz haben, sind sie üblich.
Fazit
Sacklöcher sind eine spezielle Bohrtechnik, die es ermöglicht, die Effizienz und Leistung von Multilayer-Leiterplatten zu steigern. Sie tragen zu einer platzsparenden und leistungsfähigen Bauweise bei, insbesondere bei Anwendungen, die eine hohe Bauteildichte und verbesserte elektrische Leistung erfordern.
Vgl. auch → Blind Via
Schablonen (Stencil) werden in der Leiterplattenfertigung zur präzisen Platzierung von Lötpaste auf Pads verwendet. Sie spielen eine wesentliche Rolle im Bestückungsprozess, indem sie sicherstellen, dass die Lötpaste genau auf die Stellen aufgetragen wird, an denen die elektronischen Bauteile befestigt werden sollen.
Merkmale und Herstellung von Schablonen
Definition und Funktion
Schablonen sind dünne Folien, meistens aus Edelstahl oder Nickel, die speziell für jede Leiterplatte gefertigt werden. Durch präzise ausgestanzte Öffnungen an den Positionen der Pads kann die Lötpaste durch die Schablone hindurch auf die Leiterplatte aufgebracht werden.
Herstellungsverfahren
Es gibt verschiedene Verfahren zur Herstellung von Schablonen, je nach Anforderungen an Präzision und Auflösung:
- Laser-Cutting: Häufigste Methode, bei der ein Laser die Öffnungen präzise ausschneidet.
- Ätzen: Eignet sich für größere Öffnungen, ist jedoch weniger genau.
- Galvanisierung (Electroforming): Verwendet für sehr feine Pitch-Schablonen, die höchste Präzision erfordern.
Einsatz von Schablonen im Produktionsprozess
Schablonendruck
Beim Schablonendruck wird die Schablone auf die Leiterplatte gelegt, und die Lötpaste wird mit einem Rakel über die Schablone gestrichen. Die Paste füllt die Öffnungen und verbleibt beim Entfernen der Schablone auf den Pads. Dieser Prozess ist schnell und effizient, besonders bei der Massenproduktion.
Vorteile von Schablonen
- Präzision und Konsistenz: Schablonen ermöglichen einen gleichmäßigen Auftrag der Lötpaste, was die Qualität der Lötverbindungen verbessert.
- Produktionsgeschwindigkeit: Der Schablonendruck ist ein schneller Prozess, der den Fertigungsdurchlauf beschleunigt.
- Kosteneffizienz: Einmal erstellte Schablonen können für viele Platinen derselben Bauart wiederverwendet werden.
Anpassung an verschiedene Bauteilgrößen
Für Leiterplatten mit Bauteilen verschiedener Größen können Schablonen angepasst werden, um die Lötpaste in der jeweils benötigten Menge aufzutragen. Spezielle Schablonen für Fine-Pitch-Bauteile haben besonders präzise Öffnungen, um kleine Mengen der Paste an präzise Stellen zu bringen.
Fazit
Schablonen sind essenziell für eine effiziente und präzise Produktion von Leiterplatten. Sie garantieren eine gleichmäßige Verteilung der Lötpaste und tragen so zu hochwertigen Lötverbindungen bei, die die Zuverlässigkeit und Haltbarkeit elektronischer Bauteile verbessern. Die Wahl der richtigen Schablonentechnik und -herstellungsmethode ist dabei entscheidend, um den spezifischen Anforderungen einer Baugruppe gerecht zu werden.
Vgl. auch → SMD-Schablone
Ein Schaltplan ist eine grafische Darstellung einer elektronischen Schaltung, die zeigt, wie verschiedene elektronische Komponenten wie Widerstände, Kondensatoren, Transistoren und integrierte Schaltkreise miteinander verbunden sind. Schaltpläne werden von Entwicklern genutzt, um die Funktion einer Schaltung zu entwerfen, zu analysieren und später auch für die Fertigung von Leiterplatten vorzubereiten.
Funktionen und Nutzen eines Schaltplans
Struktur und Funktionalität der Schaltung
Ein Schaltplan stellt die elektrische Struktur der Schaltung dar und hilft, das Zusammenspiel der einzelnen Komponenten zu verstehen. Er zeigt die logische Anordnung und Verbindungen zwischen den Komponenten, was sowohl beim Design als auch beim Testen und Fehlersuchen wichtig ist.
Basis für die Leiterplattenentwicklung
Der Schaltplan dient als Grundlage für das Layout der Leiterplatte (PCB). CAD-Software überträgt die im Schaltplan definierten Verbindungen auf die Platine, sodass die tatsächlichen Verbindungen und Lötstellen entsprechend des Schaltplans erstellt werden können.
Aufbau eines Schaltplans
Symbole für Bauteile
In einem Schaltplan werden die verschiedenen Komponenten durch standardisierte Symbole dargestellt:
- Widerstand: Rechteck oder Zickzack-Linie.
- Kondensator: Zwei parallele Linien, wobei eine Seite oft gekrümmt ist, wenn es sich um einen Elektrolytkondensator handelt.
- Transistoren, Dioden und ICs: Spezielle Symbole, die Polarität und Anschlüsse kennzeichnen.
Verbindungen (Netzliste)
Die Leitungen, die Bauteile verbinden, werden durch Linien dargestellt und zeigen die elektrischen Verbindungen. Diese Verbindungen bilden die sogenannte Netzliste, die für die Leiterplattenherstellung entscheidend ist.
Referenzbezeichnungen und Werte
Jedes Bauteil hat eine Referenzbezeichnung (z. B. R1 für den ersten Widerstand) und oft auch einen Wert (z. B. 10 kΩ), die im Schaltplan angegeben sind. Diese Details sind essenziell, um die Komponenten richtig zu identifizieren und korrekt in die Schaltung einzubauen.
Vorteile des Schaltplans
- Planung und Analyse: Schaltpläne ermöglichen es, die Funktionsweise der Schaltung zu analysieren, mögliche Fehler zu erkennen und das Design zu optimieren.
- Kommunikation: Schaltpläne dienen als gemeinsame Grundlage für alle Beteiligten in der Elektronikentwicklung, vom Design bis zur Fertigung und Wartung.
- Dokumentation: Ein Schaltplan dokumentiert die Schaltung, was für zukünftige Reparaturen und Wartungsarbeiten nützlich ist.
Erstellung eines Schaltplans
Software zur Schaltplanerstellung
Zur Erstellung eines Schaltplans wird häufig CAD-Software (z. B. Altium Designer, Eagle, KiCad) verwendet. Diese Software ermöglicht die präzise Platzierung von Bauteilen und das Erstellen einer korrekten Netzliste, die anschließend für das Layout und die Produktion genutzt werden kann.
Simulationsmöglichkeiten
Moderne CAD-Software bietet oft Simulationsfunktionen, die die Verhaltensanalyse der Schaltung ermöglichen, bevor sie physisch gebaut wird. Dies hilft, Fehler frühzeitig zu erkennen und Kosten zu sparen.
Fazit
Ein Schaltplan ist ein unverzichtbares Werkzeug im Designprozess elektronischer Schaltungen. Er bietet eine klare und detaillierte Darstellung der elektrischen Verbindungen und ermöglicht eine reibungslose Überführung der Ideen in eine physische Schaltung. Ein gut durchdachter Schaltplan hilft, Kosten und Fehler in der Produktion zu minimieren und die langfristige Wartung und Fehlerbehebung zu erleichtern.
Engl. Bezeichnung für → Schaltplan
Ein Schliffbild ist eine Querschnittsaufnahme einer Leiterplatte oder eines elektronischen Bauteils, das bei der Qualitätsprüfung und Fehleranalyse verwendet wird. Es zeigt die innere Struktur, Schichten und mögliche Defekte des Bauteils, wie Lötverbindungen, Durchkontaktierungen (Vias) und die Materialzusammensetzung. Das Schliffbild wird durch Präparieren und Schleifen eines Probenstücks erzeugt, sodass ein vertikaler Schnitt durch alle Schichten und Leiterbahnen sichtbar wird.
Vorgehensweise zur Erstellung eines Schliffbilds
Probenentnahme:
Ein kleines Stück der Leiterplatte oder des Bauteils wird als Probe entnommen. Dabei wird darauf geachtet, dass die relevanten Bereiche wie Vias oder Lötstellen enthalten sind.
Einbetten und Schleifen:
Die Probe wird in einen speziellen Kunststoff eingebettet, um sie für die weitere Bearbeitung stabil zu machen. Anschließend wird die Oberfläche der Probe geschliffen und poliert, bis die gewünschten Schichten sichtbar sind.
Mikroskopische Analyse:
Das Schliffbild wird unter dem Mikroskop analysiert. So können Details wie Schichtdicken, die Struktur der Durchkontaktierungen und Lötstellen, mögliche Hohlräume und Delaminationen sichtbar gemacht werden.
Nutzen eines Schliffbilds
- Qualitätsprüfung: Überprüfen der Schichtdicken, der Beschichtung (z. B. Kupferdicke) und der Durchkontaktierungen.
- Fehleranalyse: Identifikation von Fehlern wie Rissen, Lunker, Delaminationen oder mangelhafter Haftung zwischen Schichten.
- Prozesskontrolle: Das Schliffbild ermöglicht Rückschlüsse auf den Fertigungsprozess und kann zur Optimierung der Herstellungsverfahren genutzt werden.
Typische Anwendungsbereiche
- Leiterplattenfertigung: Überprüfung der mechanischen und elektrischen Verbindungen in Multilayer-Leiterplatten.
- Halbleitertechnik: Kontrolle der Bondverbindungen und der Schichtdicken in Halbleitern.
- Materialprüfung: Untersuchung von Beschichtungen, um die Haltbarkeit und die Verarbeitungsqualität sicherzustellen.
Fazit
Das Schliffbild ist ein wichtiges Werkzeug zur Qualitätssicherung und Fehleranalyse in der Elektronikfertigung. Es liefert wertvolle Einblicke in die innere Struktur und Qualität von Bauteilen, wodurch die Fertigungsprozesse verbessert und die Zuverlässigkeit elektronischer Produkte sichergestellt werden können.
- SCHWALLLÖTEN
- SELEKTIVLÖTEN
- SENKUNG
- SIGNALINTEGRITÄT
Schwalllöten ist ein Verfahren zum Löten von elektronischen Bauteilen auf Leiterplatten. Beim Schwalllöten wird die Unterseite der bestückten Leiterplatte über eine Welle (Schwall) aus flüssigem Lötzinn geführt. Die Lötwelle benetzt die freiliegenden Anschlussstellen und Lötflächen, sodass die Bauteile durch das geschmolzene Lot fest und elektrisch verbunden werden.
Ablauf des Schwalllötens
Vorbereitung und Bestückung: Die Leiterplatte wird mit den zu lötenden Bauteilen bestückt und durch eine Flussmittelauftragsmaschine geführt. Das Flussmittel sorgt dafür, dass sich das Lötzinn gut auf den Oberflächen verteilen kann und hilft dabei, Oxidschichten zu entfernen.
Vorwärmung: Die Leiterplatte wird auf eine bestimmte Temperatur vorgewärmt, um thermische Spannungen zu reduzieren und die Benetzbarkeit zu verbessern.
Lötwelle (Lötbad): Die Leiterplatte wird über eine Lötwelle geführt, bei der flüssiges Zinn an die Lötflächen und Anschlusspins gelangt. Die Bewegung sorgt dafür, dass alle Lötstellen gleichmäßig mit Lötzinn benetzt werden.
Abkühlung und Reinigung: Nach dem Lötprozess wird die Leiterplatte abgekühlt, sodass das Lötzinn fest wird und die Lötverbindungen stabil sind. Anschließend erfolgt oft eine Reinigung, um Flussmittelreste zu entfernen.
Vorteile des Schwalllötens
- Hohe Effizienz und Geschwindigkeit: Das Schwalllöten ist ein schnelles Verfahren, das sich besonders für die Serienfertigung eignet.
- Gleichmäßige Lötverbindungen: Durch die Lötwelle wird das Lot gleichmäßig verteilt, was zu konsistenten Lötstellen führt.
- Kostengünstig: Insbesondere bei doppelseitig bestückten Leiterplatten ist das Schwalllöten eine wirtschaftliche Option.
Einschränkungen
- Begrenzung auf bedrahtete Bauteile: Dieses Verfahren wird vor allem für bedrahtete Bauteile (Through-Hole Technology, THT) genutzt und eignet sich weniger für oberflächenmontierte Bauteile (SMD), da diese bei der Lötwelle verrutschen könnten.
- Empfindlichkeit gegenüber hohen Temperaturen: Nicht alle Bauteile sind für die hohen Temperaturen des Schwalllötens geeignet, sodass dieses Verfahren nicht universell einsetzbar ist.
Anwendungen
Schwalllöten wird häufig in der Herstellung von Elektronikplatinen angewendet, die aus durchkontaktierter Technologie bestehen und eine hohe Stückzahl erfordern, wie etwa in Haushaltsgeräten, Automobil- oder Industrieelektronik.
Fazit
Schwalllöten ist ein bewährtes, effizientes und kostengünstiges Lötverfahren, das sich besonders für die Serienfertigung von THT-Leiterplatten eignet. Es ermöglicht gleichmäßige und zuverlässige Lötverbindungen und wird in der Elektronikfertigung häufig verwendet.
Vgl. auch → Wellenlöten
Selektivlöten ist ein Verfahren zum Löten spezifischer Bereiche auf einer Leiterplatte, bei dem einzelne Bauteile oder Lötstellen gezielt bearbeitet werden, ohne die gesamte Leiterplatte einem Lötprozess auszusetzen. Dieses Verfahren eignet sich besonders für Leiterplatten mit Mischbestückung (THT- und SMD-Bauteile) und komplexen Layouts, die nicht vollständig durch Wellenlöten bearbeitet werden können.
Ablauf des Selektivlötens
Flussmittelauftrag: Zunächst wird Flussmittel auf die ausgewählten Lötstellen aufgetragen, um Oxidschichten zu entfernen und die Benetzbarkeit zu verbessern.
Vorwärmung: Die Leiterplatte wird auf eine moderate Temperatur erwärmt, um eine gleichmäßige Wärmeverteilung zu gewährleisten und thermische Spannungen zu minimieren.
Lötprozess: Ein computergesteuerter Lötroboter führt einen punktgenauen Lötvorgang durch, bei dem eine Lötspitze oder eine kleine Lötwelle gezielt an die einzelnen Lötstellen gebracht wird. Das Lot wird nur an den definierten Stellen aufgetragen, um eine präzise Verbindung herzustellen.
Abkühlung und Nachbearbeitung: Nach dem Lötvorgang kühlt die Leiterplatte ab. Je nach Anforderung kann eine Nachbearbeitung erfolgen, z. B. Reinigung von Flussmittelrückständen.
Vorteile des Selektivlötens
- Gezielte Lötstellenbearbeitung: Durch die präzise Positionierung eignet sich das Selektivlöten für komplexe und empfindliche Schaltungen, bei denen nur bestimmte Bereiche verlötet werden sollen.
- Schutz empfindlicher Bauteile: Das Verfahren reduziert das Risiko von Hitzeschäden, da nicht die gesamte Leiterplatte, sondern nur bestimmte Stellen erhitzt werden.
- Flexibilität: Selektivlöten ist ideal für Mischbestückung, bei der SMD- und THT-Komponenten auf einer Platine vorhanden sind.
- Hohe Präzision: Durch die robotergesteuerte Technik wird eine exakte Lötung auch bei kleinen, dicht gepackten Bauteilen ermöglicht.
Einschränkungen
- Längere Prozesszeit: Selektivlöten ist langsamer als Wellen- oder Reflow-Löten, da jede Lötstelle einzeln bearbeitet wird.
- Hoher Aufwand bei Programmierung: Die punktgenaue Steuerung erfordert eine präzise Programmierung des Lötroboters, was den Einrichtungsaufwand erhöht.
- Kostenintensiv: Die komplexe Technik und der erhöhte Programmieraufwand machen Selektivlöten kostenintensiver als andere Verfahren.
Anwendungsbereiche
Selektivlöten wird oft in der Elektronikfertigung für anspruchsvolle Leiterplatten eingesetzt, etwa in der Automobilindustrie, Medizintechnik und Luftfahrt. Auch in Kleinserien oder Prototypenfertigungen, wo Präzision und Flexibilität erforderlich sind, kommt dieses Verfahren häufig zum Einsatz.
Fazit
Selektivlöten ist ein hochpräzises Lötverfahren, das sich besonders für komplexe Leiterplatten mit empfindlichen und verschiedenen Bauteilen eignet. Es ermöglicht eine gezielte Lötstellenbearbeitung und schont empfindliche Bauteile durch die punktgenaue Wärmezufuhr.
Senkung bezeichnet in der Leiterplatten- und Mechanikfertigung die Bearbeitung einer Bohrung oder eines Lochs, sodass eine kegelförmige Vertiefung entsteht. Diese Vertiefung ermöglicht es, dass Schrauben, Nieten oder andere Befestigungselemente bündig mit der Oberfläche der Leiterplatte oder eines Bauteils abschließen. Das Senken sorgt für eine glatte, plane Oberfläche und verhindert, dass hervorstehende Befestigungselemente die Funktion oder das Design beeinträchtigen.
Arten von Senkungen
- Flachsenkung: Die Vertiefung hat eine geringe Tiefe und wird für flache Schraubenköpfe verwendet.
- Kegelsenkung: Eine klassische Senkung mit konischer Form, geeignet für konische Schraubenköpfe.
- Sondersenkungen: Spezifische Formen, die an besondere Schraubenkopfformen oder Bauteile angepasst sind.
Vorteile der Senkung
- Bündiger Abschluss: Schraubenköpfe schließen bündig mit der Oberfläche ab und verbessern so die Stabilität und das Erscheinungsbild der Leiterplatte.
- Verringerte Höhe: Die Senkung sorgt dafür, dass keine Teile über die Oberfläche hinausstehen, was wichtig ist für Bauteile mit geringen Toleranzen in der Höhe.
- Schutz empfindlicher Teile: Senkungen können die Leiterplatte vor mechanischen Schäden schützen, indem sie verhindern, dass sich Schrauben oder Nieten in empfindliche Schaltkreise bohren.
Anwendungen der Senkung
Senkungen werden häufig in der Elektronikfertigung, Mechanik und in der allgemeinen Produktion verwendet, vor allem in Bereichen, die eine glatte Oberfläche erfordern, wie beispielsweise im Gehäusebau oder bei Geräten mit festgelegtem Einbauraum. Auch in der Luft- und Raumfahrt sowie in der Automobilindustrie ist die Senkung ein Standardverfahren, um Bauteile effizient und sicher zu montieren.
Fazit
Senkungen bieten eine praktische Lösung, um Schrauben und Befestigungselemente bündig in die Oberfläche von Leiterplatten oder anderen Bauteilen zu integrieren. Sie tragen zur Funktionalität und Ästhetik bei und verhindern potenzielle Interferenzen mit anderen Bauteilen.
Signalintegrität (engl. Signal Integrity, SI) bezeichnet die Qualität und Stabilität elektrischer Signale auf einer Leiterplatte oder in einem Schaltkreis. Sie beschreibt die Fähigkeit der Signale, ohne Verzerrungen, Übersprechen oder andere Störungen zu ihren Zielpunkten zu gelangen. Eine gute Signalintegrität ist entscheidend für die Zuverlässigkeit und Leistung elektronischer Schaltungen, insbesondere in Hochgeschwindigkeits- und Hochfrequenzanwendungen.
Wichtige Aspekte der Signalintegrität
Reflexionen: Reflexionen treten auf, wenn Signale auf Impedanzänderungen entlang der Leiterbahnen treffen, z. B. an Übergängen oder Schnittstellen. Sie können Störungen und Signalverzerrungen verursachen.
Übersprechen: Übersprechen bezeichnet das unbeabsichtigte Kopplungseffekt zwischen benachbarten Leiterbahnen. Es tritt auf, wenn Signale durch elektrische oder magnetische Felder zwischen benachbarten Leitungen beeinflusst werden, was zu Signalstörungen führen kann.
Rauschen und Jitter: Rauschen sind zufällige elektrische Störungen im Signal, während Jitter zeitliche Schwankungen in der Signalübertragung beschreibt. Beide Faktoren beeinträchtigen die Genauigkeit und Zuverlässigkeit der Signalübertragung.
Impedanzanpassung: Eine gut kontrollierte und angepasste Impedanz der Leiterbahnen ist essenziell, um Reflexionen und Signalverluste zu minimieren. In Hochgeschwindigkeitsschaltungen ist die Impedanzanpassung besonders kritisch.
Skineffekt und Dämpfung: Bei hohen Frequenzen fließt der Strom vorwiegend auf der Oberfläche des Leiters (Skineffekt), was den effektiven Widerstand erhöht und zur Dämpfung des Signals führt.
Maßnahmen zur Verbesserung der Signalintegrität
Impedanzkontrolle: Die Leiterbahnen werden so gestaltet, dass die Impedanz über die gesamte Leiterbahnlänge konstant bleibt.
Optimale Layoutgestaltung: Leiterbahnen sollten möglichst kurz gehalten werden und sich nicht unnötig kreuzen. Sensible Signalbahnen sollten durch Schirmflächen getrennt und abgeschirmt werden.
Differenzielle Signalführung: Diese Technik verwendet Paare von Leiterbahnen, um Störungen durch gegensätzliche Signale zu minimieren. Dadurch wird das System resistenter gegen externe Störungen.
Verwendung von Entkopplungskondensatoren: Diese Kondensatoren helfen dabei, plötzliche Spannungsschwankungen auszugleichen und Rauschen zu reduzieren.
Vermeidung von scharfen Ecken in Leiterbahnen: Rundere Übergänge verringern Reflexionen und verbessern die Signalqualität.
Anwendungsbereiche der Signalintegrität
Die Sicherstellung der Signalintegrität ist besonders in Hochgeschwindigkeits- und Hochfrequenzschaltungen erforderlich, wie z. B. in:
- Telekommunikations- und Netzwerktechnik
- Computern und High-Performance-Computing
- Automobil- und Luftfahrtelektronik
- Medizinischen Geräten und präzisen Messtechniken
Fazit
Signalintegrität ist ein entscheidender Faktor für die Funktionsfähigkeit und Zuverlässigkeit elektronischer Systeme. Eine sorgfältige Planung und Umsetzung der Leiterbahnen sowie der Einsatz geeigneter Maßnahmen zur Signalstabilisierung tragen dazu bei, die Performance und Lebensdauer der Schaltung zu gewährleisten.
- SILBER
- SMD
- SMD-SCHABLONE
- SMT
- STACKED VIAS
Silber ist ein chemisches Element und wird in der Elektronik aufgrund seiner hervorragenden elektrischen Leitfähigkeit und anderen vorteilhaften Eigenschaften in verschiedenen Anwendungen eingesetzt. Es ist eines der wertvolleren Materialien, das in der Herstellung von Leiterplatten und elektronischen Bauteilen eine bedeutende Rolle spielt.
Wichtige Eigenschaften von Silber
Elektrische Leitfähigkeit: Silber ist das elektrisch leitfähigste Metall, was es zu einer bevorzugten Wahl für Anwendungen macht, bei denen hohe elektrische Leistung und geringe Verluste erforderlich sind.
Wärmeleitfähigkeit: Silber hat auch eine ausgezeichnete Wärmeleitfähigkeit, was es ideal für Anwendungen macht, bei denen Wärme effizient abgeführt werden muss.
Korrosionsbeständigkeit: Obwohl Silber anfällig für Oxidation ist, bildet es im Vergleich zu anderen Metallen eine dünne Schicht, die es vor weiterem Abbau schützt. Es ist dennoch weniger korrosionsbeständig als Gold, was es für bestimmte Anwendungen weniger geeignet macht.
Mechanische Eigenschaften: Silber ist relativ weich und kann in vielen Anwendungen leicht verformt werden. Dies macht es nützlich für die Herstellung von feinen Drähten und Lötmaterialien, aber weniger geeignet für Anwendungen, die hohe mechanische Festigkeit erfordern.
Anwendungen von Silber in der Elektronik
Lötmaterial: Silber wird häufig in Lötlegierungen verwendet, um die Lötbarkeit und die mechanische Festigkeit von Lötverbindungen zu verbessern. Silberhaltige Lote werden insbesondere in der Elektronikfertigung verwendet, um Bauteile wie Widerstände und Transistoren zu verbinden.
Leiterbahnen: In einigen hochleistungsfähigen Leiterplatten und in speziellen Anwendungen wird Silber als Beschichtungsmaterial verwendet, um die elektrische Leistung zu verbessern. Silber ist jedoch aufgrund der höheren Kosten und der geringen Korrosionsbeständigkeit weniger verbreitet als Kupfer.
Kontaktmaterialien: Silber wird oft in Schaltern, Relais und Steckverbindern eingesetzt, um eine hohe Leitfähigkeit zu gewährleisten und elektrische Verluste zu minimieren.
Dünnfilmtechnologie: In Dünnschichtbauelementen wie Solarzellen oder in der Displaytechnik wird Silber aufgrund seiner hervorragenden Leitfähigkeit verwendet.
Nachteile von Silber in der Elektronik
Kosten: Silber ist im Vergleich zu anderen Materialien wie Kupfer teurer, was es in Massenproduktionen weniger kosteneffektiv macht.
Oxidation: Silber neigt zur Bildung einer Oxidschicht, die die elektrische Leitfähigkeit beeinträchtigen kann. Daher werden oft spezielle Oberflächenbehandlungen oder Legierungen eingesetzt, um diese Wirkung zu minimieren.
Weichheit: Silber ist ein relativ weiches Metall, das in Anwendungen, die mechanische Belastung erfordern, nicht immer die beste Wahl ist.
Fazit
Silber ist aufgrund seiner exzellenten elektrischen und thermischen Leitfähigkeit sowie seiner Korrosionsbeständigkeit ein wichtiges Material in der Elektronik. Dennoch wird es aufgrund seiner Kosten und der Neigung zur Oxidation in den meisten Anwendungen durch Kupfer ersetzt, es sei denn, es sind besondere Anforderungen an die Leistung und Zuverlässigkeit erforderlich. Silber wird häufig in spezialisierten Anwendungen und in hochwertigen elektronischen Geräten eingesetzt.
Vgl. auch → Chemisch Silber
SMD (Surface-Mounted Device) bezeichnet eine Art von elektronischen Bauteilen, die direkt auf der Oberfläche einer Leiterplatte (PCB) montiert werden, anstatt durch Löcher in die Platine eingeführt zu werden, wie es bei traditionellen Durchlochbauteilen (THT) der Fall ist. Diese Bauweise hat die Herstellung und Miniaturisierung elektronischer Geräte revolutioniert, da sie eine höhere Bauteildichte und eine bessere Leistung ermöglicht.
Vorteile von SMD-Technologie
Kompakte Bauweise: SMD-Komponenten sind deutlich kleiner als ihre THT-Pendants, was die Platzierung auf der Leiterplatte effizienter macht und das Design von Geräten mit höherer Dichte ermöglicht.
Automatisierte Bestückung: Da SMD-Bauteile auf der Leiterplattenoberfläche montiert werden, können sie einfacher mit automatisierten Maschinen platziert werden. Dies reduziert die Produktionskosten und erhöht die Fertigungsgeschwindigkeit.
Bessere elektrische Leistung: Die geringeren Abmessungen von SMD-Komponenten führen zu kürzeren Leitungen und damit zu einer besseren elektrischen Leistung, da der Widerstand und die Induktivität minimiert werden.
Reduzierte Leiterplattenkosten: Da SMD-Komponenten weniger Platz benötigen, kann eine kleinere oder dünnere Leiterplatte verwendet werden, was die Materialkosten senkt.
Höhere Zuverlässigkeit: SMD-Bauteile sind weniger anfällig für mechanische Belastungen, da sie nicht durch Löcher in der Leiterplatte geführt werden. Dies erhöht die mechanische Stabilität und Zuverlässigkeit der Komponenten.
Typische SMD-Bauteile
Widerstände (SMD-Widerstände): Diese sind in verschiedenen Größen erhältlich, die häufigsten sind 0805, 0603 und 0402 (Größe in Zoll).
Kondensatoren (SMD-Kondensatoren): SMD-Kondensatoren gibt es in vielen Varianten, einschließlich Keramik-, Tantal- und Elektrolytkondensatoren.
Transistoren: SMD-Transistoren, wie FETs (Feldeffekttransistoren) und BJT (Bipolar Junction Transistor), sind ebenfalls weit verbreitet und bieten eine kompakte Lösung für verschiedene Schaltanwendungen.
Dioden: SMD-Dioden werden in einer Vielzahl von Anwendungen genutzt, von Gleichrichtung bis zum Schutz vor Überspannung.
Integrierte Schaltkreise (ICs): Viele ICs, einschließlich Mikrocontroller, Verstärker und Prozessoren, sind jetzt in SMD-Form erhältlich.
Verfahren zur Montage von SMD-Komponenten
Druck von Lotpaste: Zunächst wird eine dünne Schicht Lotpaste auf die Kontaktflächen der Leiterplatte aufgetragen.
Platzierung der Bauteile: Mit einem sogenannten Pick-and-Place-Roboter werden die SMD-Bauteile auf die Platine gesetzt. Diese Maschinen sind sehr präzise und können Bauteile millimetergenau positionieren.
Reflow-Löten: Nach der Platzierung wird die Platine durch einen Reflow-Ofen geführt, der die Lotpaste schmilzt und die SMD-Bauteile fest auf der Leiterplatte fixiert.
Inspektion und Test: Nach dem Löten wird die Leiterplatte auf Fehler überprüft, oft mit Hilfe von automatisierter optischer Inspektion (AOI) oder Röntgeninspektion.
Anwendungen von SMD-Technologie
Consumer Electronics: SMDs sind in fast allen modernen Unterhaltungselektronikgeräten wie Smartphones, Laptops, Fernsehern und Kameras zu finden.
Automobilindustrie: Viele moderne Fahrzeuge verwenden SMD-Komponenten in Steuergeräten, Sicherheitssystemen und Infotainment-Systemen.
Medizinische Geräte: Auch in der Medizintechnik finden SMD-Bauteile Anwendung, insbesondere in tragbaren Geräten und Diagnosetools.
Kommunikationsgeräte: SMD-Technologie wird häufig in Smartphones, Routern und Netzwerkausrüstung eingesetzt.
Fazit
SMD-Technologie hat die Entwicklung von Elektronikgeräten in vielerlei Hinsicht verändert. Sie ermöglicht kompaktere, leistungsfähigere und kostengünstigere Designs. Durch die Einführung automatisierter Fertigungstechniken können Hersteller die Produktionseffizienz und -genauigkeit steigern, was zu einer breiten Verwendung dieser Technologie in fast allen Bereichen der Elektronik geführt hat.
SMD-Schablone ist ein Werkzeug, das in der Elektronikfertigung verwendet wird, um Lotpaste präzise auf die Kontaktflächen von Leiterplatten (PCBs) aufzutragen, bevor SMD-Bauteile (Surface-Mount Devices) aufgebracht werden. Diese Schablonen sind entscheidend für die Herstellung von Leiterplatten, die mit Surface-Mount-Technologie (SMT) bestückt werden. Sie gewährleisten eine gleichmäßige Verteilung der Lotpaste und helfen, Lötfehler zu minimieren.
Funktionsweise der SMD-Schablone
Schablonenherstellung: Eine SMD-Schablone wird aus dünnem, rostfreiem Stahl oder anderen Materialien gefertigt. Die Schablone hat präzise Löcher (öffnungen), die mit den Kontaktflächen der Leiterplatte übereinstimmen. Diese Öffnungen sind an den Positionen platziert, an denen später die SMD-Bauteile aufgelötet werden.
Lotpaste auftragen: Die Schablone wird auf die Leiterplatte aufgelegt und in Position gehalten. Danach wird eine spezielle Lotpaste mit einem Rakel oder Spachtel über die Schablone gestrichen. Die Paste füllt die Öffnungen der Schablone, sodass nur die Kontaktflächen auf der Leiterplatte mit der Paste benetzt werden.
Entfernen der Schablone: Nach dem Auftragen der Lotpaste wird die Schablone vorsichtig entfernt. Die Paste bleibt nur an den Kontaktflächen der Leiterplatte haften, die für die Bauteile vorgesehen sind.
Bestückung der Leiterplatte: Nachdem die Lotpaste aufgetragen wurde, wird die Leiterplatte in einen Bestückungsautomaten (Pick-and-Place-Maschine) eingelegt, der die SMD-Bauteile auf die mit Lotpaste versehenen Kontaktflächen setzt.
Reflow-Löten: Nach der Bauteilbestückung wird die Leiterplatte in einen Reflow-Ofen geführt, wo die Lotpaste schmilzt und die SMD-Bauteile dauerhaft mit der Leiterplatte verbunden werden.
Vorteile der SMD-Schablone
Präzision: SMD-Schablonen ermöglichen eine sehr präzise Dosierung der Lotpaste, was zu einer hohen Qualität der Lötverbindungen führt.
Wiederholgenauigkeit: Die Schablonen bieten konsistente Ergebnisse, was besonders wichtig ist, wenn große Mengen Leiterplatten hergestellt werden.
Vermeidung von Lötfehlern: Durch die präzise Aufbringung der Lotpaste wird das Risiko von Lötfehlern wie kalten Lötstellen oder Brücken reduziert.
Zeiteinsparung: Der Prozess des Lotpastenauftragens ist durch den Einsatz von Schablonen schnell und effizient, was den gesamten Fertigungsprozess beschleunigt.
Materialien für SMD-Schablonen
Edelstahl: Am häufigsten wird Edelstahl verwendet, da es eine hohe Festigkeit und Haltbarkeit bietet. Es ist robust genug, um wiederholte Anwendungen ohne Verlust der Präzision zu überstehen.
Nickel: In einigen Fällen wird auch Nickel für die Schablonenproduktion verwendet, insbesondere wenn sehr dünne Schablonen benötigt werden.
Polymerbeschichtete Schablonen: In weniger anspruchsvollen Anwendungen werden auch Schablonen aus speziellen Polymermaterialien verwendet, die für kleinere Serien oder Prototypenfertigung geeignet sind.
Anwendungen von SMD-Schablonen
Prototypenfertigung: In der Prototypenphase werden SMD-Schablonen oft in kleineren Stückzahlen eingesetzt, um Musterleiterplatten mit SMD-Bauteilen zu bestücken.
Serienfertigung: Bei der Massenproduktion von Leiterplatten wird eine SMD-Schablone verwendet, um Lotpaste schnell und gleichmäßig auf viele Leiterplatten zu applizieren.
Reparatur und Nachbestückung: SMD-Schablonen werden auch bei der Reparatur von Leiterplatten verwendet, um sicherzustellen, dass Lotpaste genau auf den Kontaktflächen platziert wird.
Fazit
SMD-Schablonen sind unverzichtbare Werkzeuge in der SMT-Fertigung. Sie sorgen dafür, dass Lotpaste präzise und effizient auf die Leiterplatte aufgebracht wird, was zu einer hohen Qualität der Lötverbindungen führt und den Fertigungsprozess optimiert. Durch den Einsatz von SMD-Schablonen wird die Produktion von modernen Elektronikbauteilen schneller, zuverlässiger und kostengünstiger.
SMT (Surface-Mount Technology) ist eine Fertigungstechnik in der Elektronik, bei der Bauteile direkt auf der Oberfläche von Leiterplatten (PCBs) montiert werden, anstatt durch Löcher in der Platine hindurch. Diese Technologie hat die Elektronikfertigung revolutioniert, da sie eine höhere Bauteildichte und eine effizientere Produktionsweise ermöglicht.
Vorteile von SMT
Höhere Bauteildichte: SMT ermöglicht es, kleinere Bauteile zu verwenden, was die Dichte der Bauteile auf einer Leiterplatte erhöht. Dies führt zu kompakteren und leistungsfähigeren Geräten.
Automatisierung der Fertigung: Da die Bauteile direkt auf der Platine platziert werden, kann die Bestückung durch Maschinen (wie Pick-and-Place-Roboter) erfolgen, was die Produktionsgeschwindigkeit und -genauigkeit erhöht.
Bessere elektrische Leistung: SMT ermöglicht kürzere Verbindungsleitungen, wodurch die Widerstände und Induktivitäten in den Leiterbahnen reduziert werden, was die Signalqualität verbessert.
Kosteneffizienz: Die Möglichkeit zur automatisierten Fertigung senkt die Produktionskosten. Zudem kann die gleiche Leiterplatte mit verschiedenen Bauteilen bestückt werden, was Flexibilität in der Produktion bietet.
Bessere mechanische Stabilität: Bauteile, die durch SMT auf der Oberfläche montiert sind, sind weniger anfällig für mechanische Belastungen, da sie nicht durch Löcher in der Leiterplatte geführt werden.
SMT-Verfahren
Druck von Lotpaste: Zunächst wird auf die Kontaktflächen der Leiterplatte eine dünne Schicht Lotpaste aufgetragen, meist durch einen Siebdruckprozess.
Platzierung der Bauteile: Mit Hilfe von Pick-and-Place-Maschinen werden die SMD-Bauteile auf die mit Lotpaste versehenen Kontaktflächen gesetzt. Diese Maschinen sind hochpräzise und können Bauteile mit hoher Geschwindigkeit und Genauigkeit positionieren.
Reflow-Löten: Nach der Platzierung wird die Leiterplatte durch einen Reflow-Ofen geführt. In diesem Ofen wird die Lotpaste durch Erhitzen geschmolzen, wodurch die Bauteile an die Leiterplatte gelötet werden.
Inspektion und Test: Nach dem Löten wird die Leiterplatte auf mögliche Fehler überprüft. Dazu wird häufig automatisierte optische Inspektion (AOI) verwendet, um Fehler wie falsche Platzierung, schlechte Lötverbindungen oder fehlerhafte Bauteile zu erkennen.
SMD-Bauteile
Widerstände und Kondensatoren: Diese Bauteile gibt es in verschiedenen Größen, häufig in den Formaten 0805, 0603 und 0402.
Transistoren, Dioden und ICs: Auch diese Bauteile sind in SMT-Versionen erhältlich. Besonders ICs (Integrierte Schaltkreise) werden häufig in kompakter SMD-Bauweise verwendet.
Induktivitäten und Spulen: Auch diese werden häufig in SMD-Technologie gefertigt, um Platz auf der Leiterplatte zu sparen und die Montage zu vereinfachen.
Anwendungen von SMT
Consumer Electronics: SMT wird in fast allen modernen Geräten verwendet, einschließlich Smartphones, Tablets, Laptops und Fernsehern.
Automobilindustrie: In Fahrzeugen werden SMT-Komponenten in Steuergeräten, Sicherheitssystemen und Infotainment-Systemen eingesetzt.
Medizinische Geräte: In tragbaren medizinischen Geräten wie Herzschrittmachern oder tragbaren Diagnosetools finden SMT-Bauteile ebenfalls Anwendung.
Kommunikationsgeräte: Smartphones, Router und andere Netzwerkausrüstungen sind mit SMT-Bauteilen ausgestattet.
Fazit
SMT hat die Elektronikfertigung grundlegend verändert, indem es eine effizientere und kostengünstigere Produktion ermöglicht und gleichzeitig die Größe der Geräte minimiert. Die Technologie hat den Weg für die Entwicklung immer kleinerer, leistungsfähigerer und zuverlässigerer elektronischer Geräte geebnet.
Stacked Vias sind eine fortgeschrittene Technik in der Leiterplattenherstellung, bei der mehrere Durchkontaktierungen (Vias) übereinander auf einer Leiterplatte angeordnet sind, um Verbindungen zwischen verschiedenen Schichten einer mehrlagigen Leiterplatte (Multilayer PCB) herzustellen. Diese Technik ermöglicht die effiziente Nutzung des verfügbaren Raums und bietet mehr Flexibilität bei der Schaltungsgestaltung.
Funktionsweise von Stacked Vias
Bei Stacked Vias werden mehrere Vias übereinander gebohrt, wobei jede Bohrung eine Verbindung zu einer anderen Schicht der Leiterplatte herstellt. In der Regel wird der Bohrvorgang in mehreren Schichten durchgeführt, um die Vias in einer vertikal übereinander liegenden Anordnung zu realisieren. Die Vias werden dann mit einem leitfähigen Material, wie Kupfer, gefüllt, um elektrische Verbindungen zu schaffen.
Vorteile von Stacked Vias
Platzersparnis: Stacked Vias ermöglichen es, mehrere Verbindungen innerhalb eines kleineren Bereichs zu integrieren, was den Platz auf der Leiterplatte effizient nutzt. Dies ist besonders vorteilhaft bei komplexen Schaltungen oder miniaturisierten Designs.
Reduzierte Anzahl von Bohrungen: Durch die Verwendung von gestapelten Vias kann die Anzahl der Bohrungen auf der Leiterplatte reduziert werden, was den Fertigungsprozess vereinfacht und potenzielle Fehlerquellen verringert.
Erhöhte Designflexibilität: Mit Stacked Vias können Designer flexibler in der Platzierung von Schaltungen und Verbindungen sein, ohne den verfügbaren Raum zu überladen.
Erhöhte Signalintegrität: Die Verwendung von Stacked Vias kann helfen, die Signalintegrität zu verbessern, da kürzere Verbindungswege zwischen den Schichten verwendet werden. Dies kann insbesondere in Hochfrequenz- oder Hochgeschwindigkeitsanwendungen von Vorteil sein.
Verkürzung der Signalwege: Stacked Vias verkürzen die Verbindungslängen, was zu einer besseren Signalqualität und geringeren Signallatenzen führen kann.
Nachteile von Stacked Vias
Komplexität der Fertigung: Das Bohren und Füllen von gestapelten Vias ist ein komplexerer Prozess als bei traditionellen Vias, was zu höheren Produktionskosten und längeren Fertigungszeiten führen kann.
Höhere Fehleranfälligkeit: Wenn das Via-Füllmaterial nicht ordnungsgemäß aufgebracht wird oder die Schichten nicht präzise ausgerichtet sind, kann es zu Verbindungsproblemen oder Fehlfunktionen kommen.
Mechanische Belastung: Gestapelte Vias können die mechanische Festigkeit der Leiterplatte beeinträchtigen, da sie die Integrität der Schichten beeinflussen. Dies kann in Anwendungen, bei denen die Leiterplatte hohen mechanischen Belastungen ausgesetzt ist, ein Problem darstellen.
Anwendungen von Stacked Vias
High-Density Interconnect (HDI) Leiterplatten: Stacked Vias sind besonders nützlich in HDI-Leiterplatten, die aufgrund ihrer hohen Dichte und Komplexität auf platzsparende und effiziente Verbindungstechniken angewiesen sind.
Hochfrequenz- und Hochgeschwindigkeitsanwendungen: In Geräten wie Mobiltelefonen, Servern und Kommunikationssystemen, bei denen schnelle Datenübertragungen und hohe Signalqualität erforderlich sind, bieten gestapelte Vias eine effektive Möglichkeit, die Leistung zu verbessern.
Miniaturisierte Geräte: Bei der Entwicklung kleinerer Geräte wie tragbarer Elektronik oder Wearables, bei denen der Platz begrenzt ist, helfen gestapelte Vias, die Schaltung zu optimieren und den verfügbaren Platz effizient zu nutzen.
Fazit
Stacked Vias bieten eine wertvolle Lösung zur Verbesserung der Schaltungsdichte und Signalqualität in mehrlagigen Leiterplatten. Obwohl der Fertigungsaufwand und die Kosten höher sind, ermöglichen sie eine präzisere und platzsparendere Verbindungstechnik, die besonders in anspruchsvollen Elektronikdesigns und Hochleistungsanwendungen von Vorteil ist.
Vgl. auch → Microvia → Blind Via → Buried Via
- STACKUP
- STAGGERED VIAS
- STARRFLEX
- STECKERVERSTÄRKUNG
Stackup bezeichnet den Aufbau und die Anordnung der verschiedenen Schichten in einer mehrlagigen Leiterplatte (Multilayer PCB). Der Stackup umfasst die Reihenfolge der Materialien, die für die Leiterplatte verwendet werden, einschließlich der Kupferschichten, Isoliermaterialien (wie Prepregs oder Dielektrika), sowie der verwendeten Lötstopplack- und Schutzschichten.
Elemente eines Stackups
Signal-Schichten: Diese Schichten enthalten die elektrischen Leiterbahnen und Pads, die die Verbindungen zwischen den Bauteilen herstellen. In einer mehrlagigen Leiterplatte können mehrere Signal-Schichten vorhanden sein, und sie werden oft in einem alternierenden Muster mit der Erdungsschicht oder der Stromversorgungsschicht angeordnet.
Stromversorgungs- und Erdungsschichten: Diese Schichten sind entscheidend für die Stabilität der Leiterplatte. Sie bieten einen gemeinsamen Rückweg für die elektrischen Signale und tragen zur Verteilung der Stromversorgung bei. Eine gute Erdungsschicht ist besonders wichtig, um Störungen und Rauschen zu minimieren.
Isoliermaterialien (Prepregs): Diese Schichten bestehen aus einer Faserverstärkung (normalerweise Glasfaser) und einem Harz, das bei der Herstellung der Leiterplatte als Bindemittel fungiert. Prepregs werden zwischen den Kupferschichten aufgebracht, um die verschiedenen Ebenen zusammenzuhalten.
Lötstopplack-Schichten: Lötstopplack (Soldermask) ist eine Schutzschicht, die auf den Leiterplatten aufgebracht wird, um die Bereiche zu kennzeichnen, die nicht gelötet werden sollen. Diese Schicht schützt die Leiterbahnen vor Oxidation und Kurzschlüssen während des Lötprozesses.
Schutz- oder Dekorationsschichten: Diese Schichten können auf die Leiterplatte aufgebracht werden, um den mechanischen Schutz zu erhöhen, die Haltbarkeit zu verbessern oder ästhetische Ziele zu erreichen (z. B. durch Verwendung von Silkscreen-Drucken für die Bauteilkennzeichnung).
Typen von Stackups
Symmetrisches Stackup: Bei einem symmetrischen Stackup sind die Schichten gleichmäßig auf beiden Seiten der Leiterplatte verteilt, was bedeutet, dass die Signal-, Erdungs- und Stromversorgungsschichten gleichmäßig auf die Vorder- und Rückseite verteilt sind. Dieser Aufbau bietet eine gleichmäßige thermische und mechanische Belastung.
Asymmetrisches Stackup: Ein asymmetrisches Stackup hat eine ungleiche Verteilung der Schichten, wobei mehr Schichten auf einer Seite der Leiterplatte konzentriert sind. Dies kann notwendig sein, um bestimmte Designanforderungen zu erfüllen oder um eine bessere Signalintegrität zu erzielen.
Impedanzkontrolliertes Stackup: Hierbei wird die Dicke des Isoliermaterials und der Kupferschichten so gewählt, dass eine bestimmte Impedanz (z. B. 50 Ohm für Hochgeschwindigkeits-Signalleitungen) gewährleistet ist. Dies ist besonders wichtig bei der Übertragung von Hochfrequenzsignalen.
Gestaltung des Stackups
Die Gestaltung des Stackups ist ein kritischer Bestandteil des PCB-Designs und erfordert sorgfältige Überlegungen zu mehreren Faktoren:
Impedanzkontrolle: Um eine präzise Übertragung von Hochgeschwindigkeitssignalen zu gewährleisten, müssen die Impedanzen der Leiterbahnen innerhalb des Stackups kontrolliert werden.
Signalintegrität: Die richtige Anordnung der Schichten hilft, Signalstörungen und Rauschen zu minimieren, insbesondere bei hochfrequenten Signalen.
Thermisches Management: Die richtige Anordnung der Schichten trägt zur Wärmeableitung bei und sorgt dafür, dass sich die Temperatur auf der Leiterplatte gleichmäßig verteilt.
Kosten und Fertigung: Das Stackup beeinflusst auch die Kosten der Fertigung, da komplexere Stackups teurer und schwieriger zu produzieren sind.
Vorteile eines gut gestalteten Stackups
Verbesserte Signalintegrität: Ein korrektes Stackup minimiert elektromagnetische Interferenzen und Crosstalk zwischen den Schichten, was zu besseren elektrischen Eigenschaften und stabileren Signalen führt.
Thermisches Management: Die Schichtanordnung kann helfen, die Wärme von empfindlichen Bauteilen abzuleiten und die Leiterplatte effizienter zu kühlen.
Kompakte Bauweise: Durch das geschickte Stapeln der Schichten können Leiterplatten mit höherer Dichte und kleineren Abmessungen entwickelt werden, was für Miniaturgeräte und tragbare Anwendungen wichtig ist.
Zuverlässigkeit und Haltbarkeit: Ein richtiges Stackup sorgt für eine hohe mechanische Festigkeit und Haltbarkeit der Leiterplatte, sodass diese unter verschiedenen Umgebungsbedingungen zuverlässig funktioniert.
Fazit
Das Stackup ist ein wesentlicher Bestandteil des Leiterplattendesigns und beeinflusst direkt die Leistung, Fertigungskosten und Langlebigkeit eines Produkts. Die sorgfältige Planung des Stackups, basierend auf den spezifischen Anforderungen an Signalintegrität, Impedanzkontrolle, thermisches Management und mechanische Eigenschaften, ist entscheidend für den Erfolg eines Projekts.
Vgl. auch → Lagenaufbau
Staggered Vias bezeichnet eine spezielle Anordnung von Durchkontaktierungen (Vias) auf einer Leiterplatte, bei der die Vias in einer versetzten (gestaffelten) Position angeordnet sind. Diese Technik wird häufig verwendet, um den Platz auf der Leiterplatte effizienter zu nutzen, insbesondere bei sehr feinen und dichten Leiterbahnen. Staggered Vias tragen zur Verbesserung der Leiterplattenleistung und -zuverlässigkeit bei, indem sie den Platz für die Schaltungskomponenten optimieren und gleichzeitig die integrale Schaltung der Leiterplatte gewährleisten.
Merkmale von Staggered Vias:
Versetzte Anordnung: Bei Staggered Vias sind die Durchkontaktierungen nicht direkt übereinander angeordnet, sondern versetzt, um die Platzierung der Leiterbahnen und Pads zu maximieren. Dies ist besonders nützlich bei Leiterplatten mit hoher Dichte und kleinen Bauteilen.
Vermeidung von Konflikten mit Bauteilen: Die gestaffelte Anordnung kann verhindern, dass Vias in den Bereichen landen, in denen Bauteile oder andere wichtige Verbindungen auf der Leiterplatte platziert werden müssen.
Bessere Signalübertragung: Durch die versetzte Anordnung von Vias kann der Signalweg optimiert werden, wodurch die Möglichkeit von Störungen oder Signalverlusten verringert wird, die bei zu engen oder schlecht positionierten Vias auftreten könnten.
Effizienter Platzverbrauch: Diese Technik erlaubt eine bessere Nutzung des begrenzten Platzes auf der Leiterplatte und sorgt dafür, dass die Bauteile effizient und in einer kompakten Weise untergebracht werden können.
Vorteile von Staggered Vias:
- Platzoptimierung: Die gestaffelte Anordnung von Vias bietet mehr Flexibilität bei der Platzierung der Bauteile und ermöglicht eine dichtere und kompaktere Leiterplatte.
- Bessere Wärmeableitung: Bei höheren Leistungsanforderungen kann die Platzierung von Vias in gestaffelter Form die Wärmeableitung durch die Leiterplatte verbessern, da die Vias eine wichtige Rolle beim Wärmefluss spielen.
- Erhöhte Zuverlässigkeit: Durch die Vermeidung von Konflikten mit anderen Bauteilen oder Verbindungen wird die Leiterplatte stabiler und zuverlässiger.
Anwendung von Staggered Vias:
- Hochdichte Leiterplatten: Diese Technik wird häufig in Anwendungen eingesetzt, bei denen hohe Bauteildichte erforderlich ist, wie z. B. in Mobilgeräten, Computern und anderen kompakten elektronischen Geräten.
- Multilayer-PCBs: In mehrlagigen Leiterplatten, bei denen mehrere Vias erforderlich sind, ermöglicht die gestaffelte Anordnung eine effiziente Nutzung des verfügbaren Raums, ohne die elektrischen Eigenschaften zu beeinträchtigen.
Fazit
Staggered Vias sind eine wichtige Technik im Leiterplattendesign, die dazu beiträgt, den Platz auf der Leiterplatte zu optimieren und die Signalintegrität sowie die Zuverlässigkeit der Leiterplatte zu verbessern. Durch die versetzte Anordnung von Vias wird eine effektivere Nutzung des verfügbaren Raums ermöglicht, was besonders in hochdichten und mehrlagigen Leiterplatten von Vorteil ist.
Starrflex bezeichnet eine spezielle Art von Leiterplattenmaterial, das sowohl die Eigenschaften von starren als auch flexiblen Leiterplatten kombiniert. Starrflex-Leiterplatten bestehen aus einem starren Teil, der in der Regel aus einem klassischen Leiterplattenmaterial wie FR4 besteht, und einem flexiblen Teil, der meist aus einem flexiblen Polyimid-Material wie Kapton oder einem ähnlichen Material gefertigt wird.
Diese Technologie ermöglicht es, Leiterplatten in Anwendungen zu verwenden, bei denen sowohl die Vorteile von starren Leiterplatten (wie mechanische Festigkeit und Haltbarkeit) als auch die Flexibilität von flexiblen Leiterplatten (wie die Fähigkeit, sich zu biegen oder in begrenztem Raum zu passen) benötigt werden.
Merkmale von Starrflex-Leiterplatten:
Kombination von starren und flexiblen Bereichen: Starrflex-Leiterplatten enthalten sowohl starre als auch flexible Abschnitte, die nahtlos miteinander verbunden sind. Der starre Bereich wird für mechanische Stabilität und strukturelle Unterstützung verwendet, während der flexible Bereich es ermöglicht, die Leiterplatte in unregelmäßige oder komplexe Formfaktoren zu integrieren.
Platzersparnis und Designfreiheit: Diese Leiterplatten bieten Designern die Freiheit, Leiterplatten in kompakteren und ergonomischeren Formen zu erstellen, da der flexible Teil es ermöglicht, die Leiterplatte in engen oder ungewöhnlich geformten Gehäusen zu integrieren, ohne die Leistung oder Zuverlässigkeit zu beeinträchtigen.
Mehrlagige Konstruktion: Starrflex-Leiterplatten sind oft mehrlagig aufgebaut, wobei die flexiblen und starren Teile unterschiedliche Schichten innerhalb derselben Leiterplatte darstellen. Dies ermöglicht komplexe Designs mit höherer Dichte und verbesserter Funktionalität.
Zuverlässigkeit und Haltbarkeit: Die starre Komponente sorgt für strukturelle Integrität und Festigkeit, während die flexiblen Teile die Möglichkeit bieten, in beweglichen oder platzbegrenzten Bereichen eingesetzt zu werden. Diese Kombination erhöht die Zuverlässigkeit und Haltbarkeit der Leiterplatte in anspruchsvollen Anwendungen.
Anwendungen von Starrflex-Leiterplatten:
Medizinische Geräte: Starrflex-Leiterplatten werden oft in medizinischen Geräten eingesetzt, insbesondere in tragbaren Geräten oder Implantaten, die in begrenzte und flexiblen Bereiche integriert werden müssen.
Automobilindustrie: In modernen Fahrzeugen werden Starrflex-Leiterplatten für Anwendungen wie Steuergeräte, Sensoren und Airbag-Systeme verwendet, da sie sich an die Gegebenheiten im Fahrzeug anpassen können.
Mobiltelefone und tragbare Elektronik: Die Flexibilität von Starrflex-Leiterplatten macht sie ideal für kompakte Geräte wie Smartphones, Tablets und tragbare Wearables, bei denen die Leiterplatte in begrenztem Raum untergebracht werden muss.
Luft- und Raumfahrt: In der Luft- und Raumfahrtindustrie werden Starrflex-Leiterplatten verwendet, um Gewicht zu sparen und gleichzeitig die hohe Zuverlässigkeit zu gewährleisten, die in diesen kritischen Anwendungen erforderlich ist.
Vorteile von Starrflex-Leiterplatten:
- Raumoptimierung: Sie ermöglichen eine effektivere Nutzung des verfügbaren Raums, indem sie in Bereichen eingesetzt werden, die für starre Leiterplatten schwierig zu erreichen wären.
- Zuverlässigkeit: Sie kombinieren die mechanische Festigkeit von starren Leiterplatten mit der Flexibilität von flexiblen Leiterplatten, was zu einer hohen Beständigkeit und Zuverlässigkeit führt.
- Vielseitigkeit: Sie sind in einer Vielzahl von Anwendungen einsetzbar, von der tragbaren Elektronik bis hin zu Hochleistungsgeräten.
Fazit
Starrflex-Leiterplatten bieten eine praktische Lösung für anspruchsvolle Anwendungen, bei denen sowohl Stabilität als auch Flexibilität erforderlich sind. Ihre Fähigkeit, sich an komplexe Geometrien und enge Platzverhältnisse anzupassen, macht sie in vielen modernen Technologieanwendungen unverzichtbar.
Steckerverstärkung bezieht sich auf die Verstärkung oder Verstärkungsmaßnahmen, die an elektrischen Steckverbindern vorgenommen werden, um deren mechanische Festigkeit und elektrische Leistungsfähigkeit zu erhöhen. Dies ist besonders wichtig in Anwendungen, in denen Steckverbinder hohen mechanischen Belastungen, Vibrationen oder hohen Temperaturen ausgesetzt sind, oder wenn die Steckverbinder in kritischen Bereichen eingesetzt werden, in denen eine zuverlässige Verbindung notwendig ist.
Merkmale der Steckerverstärkung:
Mechanische Stabilität: Die Verstärkung von Steckverbindern sorgt dafür, dass sie auch unter Belastung stabil bleiben, z.B. bei wiederholtem Ein- und Ausstecken, Zug- oder Druckkräften oder Vibrationen. Dies erhöht die Haltbarkeit und Lebensdauer des Steckverbinders.
Erhöhte Zugfestigkeit: Steckverbinder werden oft durch spezielle Konstruktionen oder zusätzliche Materialien verstärkt, um die Zugfestigkeit zu erhöhen und zu verhindern, dass die Verbindung bei Zugbelastungen oder Erschütterungen gelöst wird.
Isolierung und Schutz: In einigen Fällen wird die Verstärkung auch durch zusätzliche Isolationsmaterialien oder spezielle Beschichtungen erreicht, die vor Feuchtigkeit, Korrosion und anderen äußeren Einflüssen schützen.
Thermische Belastung: Steckverbinder in Hochtemperaturanwendungen, wie in der Luft- und Raumfahrt oder Automobilindustrie, können durch spezielle Materialien oder Designanpassungen verstärkt werden, um thermischen Belastungen standzuhalten, ohne ihre Funktionalität zu beeinträchtigen.
Verfahren zur Steckerverstärkung:
Verwendung robuster Materialien: Steckverbinder können aus hochfesten Kunststoffen, Metallen oder Verbundmaterialien bestehen, die eine höhere Widerstandsfähigkeit gegenüber mechanischen Belastungen und Umwelteinflüssen bieten.
Verstärkte Kontaktflächen: Die Kontaktflächen der Steckverbinder können mit speziellen Legierungen oder Oberflächenbehandlungen versehen werden, um die elektrischen Eigenschaften zu verbessern und eine stabilere Verbindung zu gewährleisten.
Erhöhung der Kontaktanzahl: Durch Erhöhen der Anzahl der Kontakte oder durch Verstärkungen der Verbindungsmechanismen kann die Belastbarkeit der Steckverbindung verbessert werden, was zu einer höheren Strombelastung und besserer Stabilität führt.
Verwendung von Schraubverbindungen oder zusätzlichen Sicherheitsmechanismen: Einige Steckverbinder sind mit Schrauben oder Riegelmechanismen ausgestattet, um die Verbindung zusätzlich zu sichern und eine feste, dauerhafte Verbindung zu gewährleisten.
Anwendungen der Steckerverstärkung:
Automobilindustrie: In der Automobilindustrie müssen Steckverbinder besonders robust sein, da sie häufig extremen Temperaturen, Vibrationen und Feuchtigkeit ausgesetzt sind. Verstärkte Steckverbinder sorgen dafür, dass elektrische Verbindungen zuverlässig bleiben, auch unter diesen Bedingungen.
Luft- und Raumfahrt: In der Luftfahrt sind Steckverbinder auf Zuverlässigkeit und Festigkeit angewiesen, da sie in sicherheitskritischen Anwendungen eingesetzt werden, bei denen Fehler fatale Folgen haben könnten.
Industrie- und Maschinenbau: In Maschinen und Industrieanlagen müssen Steckverbinder hohen mechanischen Belastungen standhalten, weshalb eine Verstärkung der Steckverbindungen zur Vermeidung von Ausfällen oder Schäden erforderlich ist.
Medizinische Geräte: In der Medizintechnik ist es wichtig, dass Steckverbinder in Geräten, die für die Patientenversorgung entscheidend sind, besonders robust sind, um eine unterbrechungsfreie Funktion zu gewährleisten.
Fazit
Steckerverstärkungen sind eine wesentliche Maßnahme, um die Leistung und Zuverlässigkeit von Steckverbindern in anspruchsvollen Anwendungen sicherzustellen. Durch die Wahl der richtigen Materialien, Designanpassungen und zusätzliche Schutzmaßnahmen können Steckverbinder optimiert werden, um extremen mechanischen, thermischen und elektrischen Belastungen standzuhalten.
- STEG
- STENCIL
- STIFFENER
- STOPPLACK
- STROMBELASTBARKEIT
Steg bezeichnet in der Leiterplattenfertigung einen schmalen, unveränderten Bereich zwischen Leiterbahnen, Löchern oder anderen Strukturen auf einer Leiterplatte. Diese Bereiche werden häufig als Trennlinien verwendet, um bestimmte Teile der Leiterplatte voneinander zu isolieren, oder um mechanische Stabilität zu gewährleisten. Der Steg kann auch in anderen Bereichen der Elektronik, wie bei Bauteilen oder mechanischen Konstruktionen, verwendet werden.
Funktionen und Anwendungen des Stegs in der Leiterplattenfertigung:
Mechanische Stabilität: Der Steg sorgt für die notwendige Stabilität und verhindert das Absacken oder Brechen von Leiterbahnen oder Strukturen, die durch den Fertigungsprozess oder durch mechanische Belastungen während des Betriebs entstehen könnten.
Trennung von Leiterbahnen: Stege dienen dazu, Leiterbahnen voneinander zu trennen, besonders in Bereichen, in denen enge Abstände eingehalten werden müssen. Sie verhindern, dass es zu Kurzschlüssen oder unerwünschten elektrischen Verbindungen kommt.
Platzierung von Bauteilen: In einigen Fällen können Stege auch als Orientierungshilfen für die Platzierung von Bauteilen auf der Leiterplatte dienen, indem sie Bereiche abgrenzen, in denen Bauteile oder Verbindungen positioniert werden müssen.
Verhinderung von Durchkontaktierungen: Stege können auch dafür verwendet werden, um bestimmte Bereiche für Durchkontaktierungen (Vias) freizuhalten, die für die Signalübertragung und das Design der Leiterplatte von Bedeutung sind.
Arten von Stegen:
- Mechanische Stege: Diese dienen rein der strukturellen Unterstützung und Stabilität der Leiterplatte.
- Elektrische Stege: Diese verhindern elektrische Kurzschlüsse oder falsche Verbindungen, indem sie als Isolatoren zwischen benachbarten Leiterbahnen wirken.
Anwendungen:
- Mikroelektronik: In Anwendungen, bei denen präzise Leiterbahnen und enge Abstände zwischen elektrischen Verbindungen erforderlich sind, werden Stege verwendet, um eine saubere und stabile Struktur zu gewährleisten.
- Hochleistungsanwendungen: In Geräten, die großen mechanischen Belastungen oder Vibrationen ausgesetzt sind, tragen Stege zur Erhöhung der Robustheit bei.
Fazit:
Stege spielen eine wichtige Rolle in der Leiterplattenfertigung, indem sie mechanische Stabilität bieten, elektrische Isolierung ermöglichen und als Hilfsmittel bei der Platzierung von Bauteilen oder der Trennung von Leiterbahnen dienen. Sie tragen entscheidend zur Funktionalität und Haltbarkeit der Leiterplatte bei.
Stencil in der Leiterplattenfertigung ist eine dünne Metallfolie mit präzisen Löchern oder Öffnungen, die dazu verwendet wird, Lötpaste auf die Pads der Leiterplatte zu applizieren. Diese Technik wird insbesondere bei der SMD-Bestückung (Surface-Mounted Device) verwendet, um eine präzise Menge an Lötpaste an den richtigen Stellen der Leiterplatte aufzubringen, bevor die Bauteile bestückt und anschließend gelötet werden.
Funktionen und Anwendungen des Stencils:
Lötpaste auftragen: Die Hauptfunktion eines Stencils ist, die Lötpaste auf die Pads der Leiterplatte in einer kontrollierten Menge und Form aufzutragen. Die Öffnungen im Stencil entsprechen den Pads auf der Leiterplatte, auf denen die Bauteile später platziert werden.
Präzision und Konsistenz: Durch den Einsatz eines Stencils wird eine gleichmäßige Verteilung der Lötpaste erreicht, was die Qualität des Lötvorgangs verbessert. Eine gleichmäßige Schicht aus Lötpaste ist entscheidend für das Verhindern von Lötfehlern wie Kaltlötstellen oder Brücken.
Automatisierung: Stencils ermöglichen den automatisierten Lötpasteauftrag in der SMT-Fertigung (Surface Mount Technology). Sie werden häufig in Bestückungsautomaten eingesetzt, die das Stencil über die Leiterplatte platzieren und dann mit Schabern die Lötpaste durch die Öffnungen drücken.
Materialien: Stencils werden in der Regel aus rostfreiem Stahl, Messing oder auch Nickel gefertigt. Sie sind robust und können für hohe Stückzahlen verwendet werden, ohne die Präzision zu verlieren. Je nach Anwendung können die Löcher im Stencil verschiedene Größen und Formen haben.
Arten von Stencils:
Lasergefertigte Stencils: Diese werden mit einem Laser ausgeschnitten und bieten sehr präzise, feinere Öffnungen. Sie sind für Anwendungen mit sehr kleinen Bauteilen und engen Platzverhältnissen geeignet.
Chemisch geätzte Stencils: Diese werden durch ein chemisches Ätzverfahren aus einem dünnen Metallblech hergestellt und sind in der Regel kostengünstiger, bieten jedoch weniger Präzision bei sehr kleinen Bauteilen.
Anwendungen des Stencils:
SMD-Bestückung: In der oberflächenmontierten Bauweise wird das Stencil genutzt, um Lötpaste auf die Pads für die Bauteile aufzutragen, bevor diese automatisch platziert und anschließend verlötet werden.
Reflow-Löten: Nach dem Auftragen der Lötpaste und dem Bestücken der Bauteile wird die Leiterplatte durch einen Reflow-Ofen geführt, der das Lötmaterial aufschmilzt und die Bauteile auf den Pads befestigt.
Vorteile der Verwendung von Stencils:
- Hohe Präzision: Stencils ermöglichen eine sehr präzise Dosierung der Lötpaste, was eine hohe Lötqualität gewährleistet.
- Effizienz: Durch den Einsatz von Stencils wird der Lötprozess automatisiert und beschleunigt, was besonders bei großen Stückzahlen von Vorteil ist.
- Flexibilität: Stencils können für unterschiedliche Leiterplatten-Designs und -Größen angepasst werden.
Fazit:
Stencils sind ein unverzichtbares Werkzeug in der modernen Leiterplattenfertigung, insbesondere in der SMD-Technologie. Sie gewährleisten eine präzise und effiziente Anwendung von Lötpaste, was zu hochwertigen Lötverbindungen und fehlerfreien Leiterplatten führt.
Engl. Begriff für → SMD-Schablone
Stiffener (auch als Versteifungselement bekannt) bezieht sich auf ein Bauteil oder eine Schicht, die in Leiterplatten oder elektronischen Geräten eingebaut wird, um die mechanische Festigkeit und strukturelle Integrität zu erhöhen. Stiffener werden verwendet, um Verformungen zu verhindern, insbesondere bei flexiblen Leiterplatten oder in Bereichen, die mit mechanischen Belastungen, Vibrationen oder hohen Temperaturen konfrontiert sind.
Funktionen und Anwendungen von Stiffener:
Verhinderung von Verformung: Flexibele Leiterplatten oder Teile von Leiterplatten, die aufgrund ihrer Struktur oder Einsatzbedingungen mechanischen Belastungen ausgesetzt sind, können sich verformen. Ein Stiffener verhindert diese Verformung, indem er die nötige Steifigkeit hinzufügt.
Unterstützung bei der Bestückung: In der Fertigung von Leiterplatten werden Stiffener verwendet, um die Leiterplatte während des Bestückungsprozesses stabil zu halten. Das hilft, die Mechanik der Leiterplatte während der Handhabung und Montage zu schützen.
Verbesserung der thermischen und mechanischen Eigenschaften: Bei hochbelasteten Anwendungen, in denen mechanische und thermische Anforderungen hoch sind, können Stiffener die thermische Ausdehnung der Leiterplatte ausgleichen und deren Gesamtstabilität verbessern.
Arten von Stiffenern:
Versteifung durch zusätzliche Schichten (Laminierung): Ein häufiger Ansatz ist das Hinzufügen einer starren Schicht (meist aus Epoxidharz oder FR4) zu einer flexiblen Leiterplatte. Diese zusätzliche Schicht kann nur an bestimmten Bereichen der Leiterplatte (wie um Steckverbinder oder in Verbindung mit Bauteilen) hinzugefügt werden.
Versteifung durch Metall: Für Anwendungen, die hohe mechanische Festigkeit und Wärmeableitung erfordern, kann ein Metallstiffener verwendet werden. Diese Metallstreifen oder -platten werden auf der Leiterplatte positioniert, um die Festigkeit zu erhöhen, insbesondere in Hochstromanwendungen oder bei elektrischen Bauteilen, die viel Wärme erzeugen.
Versteifung durch Polymermaterialien: In flexiblen Leiterplatten kann ein polymeres Material als Stiffener eingesetzt werden. Diese Art von Material wird häufig in flexiblen Leiterplatten verwendet, die in Umgebungen eingesetzt werden, wo die Leiterplatte sowohl flexibel als auch stabil sein muss.
Anwendungen von Stiffenern:
Flexible Leiterplatten: In flexiblen Leiterplatten, die auf Biegen und Verdrehung angewiesen sind, werden Stiffener eingesetzt, um die Stabilität in bestimmten Bereichen zu gewährleisten, in denen hohe mechanische Belastungen auftreten, wie z.B. an Steckverbindern oder Schnittstellen.
Elektronische Geräte mit hoher Belastung: In Geräten, die Vibrationen oder Stöße ausgesetzt sind, wie zum Beispiel in der Automobilindustrie, Luft- und Raumfahrt oder bei tragbaren Elektronikgeräten, können Stiffener verwendet werden, um die mechanische Belastbarkeit der Platine zu erhöhen.
Hochleistungsanwendungen: In Hochstrom- oder Hochspannungsanwendungen, bei denen sowohl thermische Belastungen als auch mechanische Stabilität wichtig sind, kann ein Stiffener auch zur Verbesserung der Wärmeableitung und zur Vermeidung von Verformungen dienen.
Vorteile von Stiffenern:
- Erhöhte mechanische Stabilität: Verhindert das Verbiegen und die Beschädigung von empfindlichen Bauteilen.
- Bessere Handhabung in der Fertigung: Besonders bei flexiblen Leiterplatten ist eine Verstärkung erforderlich, um die Handhabung während des Herstellungsprozesses zu erleichtern.
- Erhöhung der Lebensdauer: Durch die Verringerung von mechanischen Belastungen und thermischen Spannungen verlängern Stiffener die Lebensdauer der Leiterplatten und Bauteile.
Fazit:
Stiffener sind ein wesentlicher Bestandteil in der Herstellung von Leiterplatten und elektronischen Geräten, die sowohl Stabilität als auch Flexibilität erfordern. Sie tragen zur Verbesserung der mechanischen Festigkeit, der Haltbarkeit und der thermischen Effizienz von Leiterplatten bei, insbesondere in Anwendungen, die extremen Bedingungen ausgesetzt sind.
Stopplack (auch Lötstopplack oder Soldermask) ist eine Beschichtung, die auf Leiterplatten aufgetragen wird, um unerwünschte Lötbrücken und Kurzschlüsse zu verhindern. Der Stopplack schützt die Leiterbahnen und andere nicht-lötbare Bereiche während des Lötprozesses. Hier sind die wichtigsten Aspekte des Stopplacks:
Funktionen des Stopplacks:
Schutz vor Lötfehlern: Stopplack wird auf den Bereichen der Leiterplatte aufgebracht, die nicht mit Lötpaste oder Lötzinn in Kontakt kommen sollen. Dies verhindert, dass während des Lötprozesses Lötzinn auf diese Bereiche gelangt, wodurch Lötbrücken und Kurzschlüsse vermieden werden.
Isolierung der Leiterbahnen: Die Schicht bietet eine Isolierung für die Kupferbahnen und verhindert Oxidation und Korrosion, die durch Umwelteinflüsse entstehen könnten. Sie schützt so die elektrischen Eigenschaften und die Langlebigkeit der Leiterplatte.
Visuelle Markierung: Der Stopplack ist häufig in einer grünen Farbe gehalten, kann aber auch in anderen Farben wie rot, blau oder schwarz vorkommen. Diese Farbcodierung hilft bei der Identifikation von Leiterplatten und erleichtert die Inspektion der Leiterplatte.
Mechanische Schutzfunktion: Der Stopplack bietet zusätzlichen mechanischen Schutz, indem er die Leiterbahnen vor Kratzern oder physischen Schäden während des Handhabens oder des Fertigungsprozesses schützt.
Arten von Stopplack:
Epoxidharz-basierter Stopplack: Diese Art von Stopplack ist die am häufigsten verwendete und bietet eine gute chemische Beständigkeit und Haltbarkeit. Sie härtet nach dem Auftragen durch Wärme oder UV-Licht.
UV-härtender Stopplack: Dieser Stopplack härtet durch UV-Strahlung und ermöglicht eine schnellere Verarbeitung. Er wird oft in modernen Fertigungsprozessen eingesetzt, da er schnelle Aushärtung bietet.
Lötdrahtbeständiger Stopplack: Für spezielle Anwendungen, bei denen die Leiterplatte nach dem ersten Lötvorgang noch nachgelötet wird, gibt es spezielle Stopplackarten, die auch eine höhere Beständigkeit gegenüber wiederholtem Löten bieten.
Anwendungen:
Standard-Leiterplatten: Der Stopplack wird auf die gesamte Leiterplatte aufgebracht, außer auf die Bereiche, auf denen Bauteile angebracht oder gelötet werden sollen.
Multilayer-Leiterplatten: Bei Leiterplatten mit mehreren Schichten wird Stopplack verwendet, um die äußeren Schichten zu schützen und eine Isolierung zwischen den Schichten zu gewährleisten.
Hochfrequenzanwendungen: In einigen Hochfrequenz-Leiterplatten wird der Stopplack so formuliert, dass er die Signalqualität nicht beeinträchtigt.
Vorteile des Stopplacks:
Vermeidung von Lötbrücken: Der Stopplack schützt vor ungewolltem Kontakt von Lötzinn auf nicht-lötbare Bereiche und verhindert so Lötbrücken und Kurzschlüsse.
Korrosionsschutz: Er schützt die Kupferbahnen vor Korrosion und oxidativen Prozessen.
Visuelle Erkennbarkeit: Die grüne Farbe des Stopplacks bietet eine klare visuelle Unterscheidung zwischen den gelöteten und nicht-gelöteten Bereichen der Leiterplatte.
Fazit:
Stopplack ist ein entscheidendes Element in der Leiterplattenfertigung, um die Lötbarkeit, die mechanische Stabilität und die langfristige Zuverlässigkeit der Leiterplatte zu gewährleisten. Er schützt die Leiterbahnen und ermöglicht die präzise Steuerung des Lötprozesses, was besonders bei komplexen, hochdichten oder multischichtigen Leiterplatten von großer Bedeutung ist.
Vgl. auch → Lötstopplack
Strombelastbarkeit bezieht sich auf die Fähigkeit eines Leiters (wie einer Leiterbahn auf einer Leiterplatte oder einem Draht), eine bestimmte Menge an elektrischem Strom zu tragen, ohne dass die Temperatur des Leiters gefährlich ansteigt oder er beschädigt wird. Sie ist ein entscheidender Faktor für die Gestaltung elektronischer Schaltungen und die Auswahl geeigneter Materialien und Komponenten. Hier sind die wichtigsten Aspekte der Strombelastbarkeit:
Faktoren, die die Strombelastbarkeit beeinflussen:
Leiterbahnbreite und -dicke: Die Breite und Dicke der Leiterbahn auf einer Leiterplatte bestimmen maßgeblich, wie viel Strom sie führen kann. Eine breitere oder dickere Leiterbahn hat eine größere Querschnittsfläche, die mehr elektrischen Strom transportieren kann, ohne dass die Temperatur signifikant ansteigt.
Material des Leiters: Das Material, aus dem die Leiterbahn besteht, hat einen großen Einfluss auf die Strombelastbarkeit. Kupfer ist das am häufigsten verwendete Material für Leiterbahnen, da es eine hohe elektrische Leitfähigkeit und gute Wärmeableitungseigenschaften hat. Andere Materialien wie Aluminium oder Silber könnten ebenfalls verwendet werden, aber mit unterschiedlichen Leistungsmerkmalen.
Temperaturanstieg: Wenn ein Leiter mehr Strom führt als seine maximale Strombelastbarkeit, wird er heißer. Wenn die Temperatur einen kritischen Punkt erreicht, kann dies zu einer Schädigung des Materials oder zu einer Verformung der Leiterbahn führen. Um dies zu verhindern, ist es wichtig, den Temperaturanstieg in den Designberechnungen zu berücksichtigen.
Länge der Leiterbahn: Längere Leiterbahnen haben mehr Widerstand, was zu mehr Wärme führt. In der Praxis bedeutet das, dass bei langen Verbindungen der Strom möglicherweise begrenzt werden muss, um eine Überhitzung zu verhindern.
Umgebungstemperatur: Die Temperatur der Umgebung, in der die Leiterplatte betrieben wird, beeinflusst die Strombelastbarkeit. Bei höheren Umgebungstemperaturen kann der Leiter weniger Strom führen, ohne dass eine gefährliche Erwärmung auftritt, da die Kühlung des Leiters weniger effektiv ist.
Kühlung: Eine effektive Wärmeableitung, etwa durch Wärmeabfuhrmechanismen wie Kühlkörper oder Belüftung, kann die maximale Strombelastbarkeit eines Leiters erheblich erhöhen, da die entstehende Wärme effizienter abgeführt wird.
Berechnung der Strombelastbarkeit:
Die Strombelastbarkeit kann durch verschiedene Ansätze und Formeln ermittelt werden. Eine häufig verwendete Faustregel basiert auf der maximalen Temperatur, die ein Material sicher erreichen kann, ohne Schaden zu nehmen. Hier ist ein allgemeiner Überblick über eine Berechnungsmethode für Leiterbahnen:
- Faustformel für Kupferleiterbahnen: Eine häufig verwendete Faustregel besagt, dass die Strombelastbarkeit einer Kupferleiterbahn bei einer Temperaturerhöhung von etwa 10 °C pro Ampere (A) und je nach Leiterbahnbreite (B) und -dicke (D) berechnet wird. Spezifische Tabellen und Softwaretools zur Berechnung der Strombelastbarkeit berücksichtigen diese Variablen und ermöglichen genauere Berechnungen.
Anwendungen der Strombelastbarkeit:
Leiterplatten: In der Leiterplattenfertigung ist es wichtig, die Strombelastbarkeit der Leiterbahnen korrekt zu bestimmen, besonders bei Anwendungen mit Hochstromlasten wie Leistungselektronik, Schaltnetzteilen oder Hochfrequenzanwendungen.
Stromversorgungen: Für die Schaltungen, die Strom an die Verbraucher liefern, muss die Strombelastbarkeit der Leitungen berücksichtigt werden, um Überhitzung und mögliche Fehler zu vermeiden.
Drahtleitungen und Kabel: In elektrischen Kabeln und Drähten muss die Strombelastbarkeit beachtet werden, um eine sichere Energieübertragung zu gewährleisten und Brandgefahr zu vermeiden.
Fazit:
Die Strombelastbarkeit ist ein kritisches Designkriterium in der Elektronik und Elektrotechnik. Sie sorgt dafür, dass elektrische Leitungen oder Leiterbahnen in Leiterplatten sicher und zuverlässig Strom führen können, ohne dass es zu einer Überhitzung oder Beschädigung kommt. Das richtige Verständnis und die korrekte Dimensionierung der Strombelastbarkeit sind für die Zuverlässigkeit und Sicherheit elektronischer Geräte und Schaltungen von entscheidender Bedeutung.
Vgl. auch → IPC
- TARGET 3001!
- TEARDROP
- TEFLON®
- TEMPERN
TARGET 3001! ist eine Software für das Design und die Erstellung von Leiterplatten (PCBs). Sie wird häufig in der Elektronikentwicklung eingesetzt und bietet eine umfassende Suite von Werkzeugen für Schaltplanerstellung, Layout und Simulation von elektronischen Schaltungen. Die Software ist besonders bei Ingenieuren, Entwicklern und Hobbyelektronikern beliebt und zeichnet sich durch ihre Benutzerfreundlichkeit und die Integration vieler Funktionen in einer Plattform aus. Hier sind die wichtigsten Funktionen und Merkmale:
Hauptmerkmale von TARGET 3001!:
Schaltplanerstellung: TARGET 3001! bietet eine intuitive Umgebung zum Erstellen von Schaltplänen. Mit einer umfangreichen Bibliothek an Bauteilen können Benutzer komplexe Schaltungen entwerfen und sie für das Layout vorbereiten. Die Schaltplanerstellung ist voll integriert, sodass Änderungen im Schaltplan sofort im Layout sichtbar sind.
Layout und PCB-Design: Die Software unterstützt das Design von Leiterplatten mit mehreren Lagen (Multilayer) und ermöglicht eine präzise Platzierung von Bauteilen, Leiterbahnen und Pads. Die Layout-Tools beinhalten Funktionen für die Anpassung der Leiterbahnbreite, das Routing von Leiterbahnen und die Gestaltung von Masseflächen.
3D-Darstellung: TARGET 3001! bietet eine 3D-Ansicht, in der Benutzer ihre Leiterplatten in einem räumlichen Modell betrachten können. Dies ist besonders hilfreich, um das Endergebnis zu visualisieren und mögliche Probleme wie Kollisionen zu erkennen, bevor die Platine physisch hergestellt wird.
Simulation und Analyse: Mit TARGET 3001! können Schaltungen simuliert und analysiert werden. So lassen sich beispielsweise Spannungsverläufe und Ströme in der Schaltung vorab prüfen. Die Simulation bietet Entwicklern die Möglichkeit, ihre Designs zu testen und Fehler frühzeitig zu erkennen.
Gerber-Export und Fertigungsdaten: TARGET 3001! unterstützt den Export von Gerber-Dateien und anderen Fertigungsdaten, die für die Herstellung von Leiterplatten erforderlich sind. Damit kann das Design direkt an Leiterplattenhersteller übermittelt werden.
Bibliotheken und Bauteilverwaltung: Die Software bietet eine umfangreiche Bibliothek mit zahlreichen Bauteilen. Anwender können eigene Bauteile erstellen oder Bibliotheken von Herstellern importieren, um die spezifischen Anforderungen ihrer Projekte zu erfüllen.
Automatisierte Funktionen: TARGET 3001! bietet automatische Funktionen wie Bauteilplatzierung, Routing und DRC (Design Rule Check), um den Entwicklungsprozess zu beschleunigen und die Genauigkeit des Designs zu erhöhen.
Zielgruppen und Anwendungen:
TARGET 3001! wird sowohl in der Industrie als auch im akademischen Umfeld und von Hobbyanwendern eingesetzt. Die Software ist für kleine bis mittelgroße Projekte geeignet, aber auch leistungsfähig genug für komplexe Anwendungen in der Leistungselektronik oder HF-Technik.
Fazit:
TARGET 3001! ist eine vielseitige, kosteneffiziente PCB-Design-Software mit einer benutzerfreundlichen Oberfläche und einer breiten Palette an Funktionen für die Entwicklung und Fertigung von Leiterplatten. Ihre integrierten Tools und die 3D-Darstellung machen sie zu einer beliebten Wahl für Entwickler, die eine umfassende Lösung für Schaltplanerstellung, Layout, Simulation und Fertigung suchen.
Teardrop bezeichnet in der Leiterplattentechnik eine spezielle Gestaltung von Leiterbahnen an kritischen Stellen, wie beispielsweise an den Übergängen zu Pads oder Durchkontaktierungen (Vias). Hierbei wird die Form der Leiterbahn an den Übergangspunkten nicht abrupt, sondern tropfenförmig („teardrop-förmig“) erweitert. Diese Anpassung hat mehrere Vorteile:
Vorteile von Teardrop-Formen
Mechanische Stabilität: Die sanfte Übergangsform reduziert die mechanische Belastung an der Schnittstelle zwischen Leiterbahn und Pad oder Via. Dadurch wird die Wahrscheinlichkeit von Rissen oder Brüchen, die durch thermische oder mechanische Beanspruchung entstehen könnten, verringert.
Elektrische Zuverlässigkeit: Teardrops minimieren die Gefahr von Unterbrechungen im elektrischen Signalfluss. Bei starker Beanspruchung bleibt die Leitfähigkeit stabiler, was die Gesamteffizienz der Schaltung verbessert.
Toleranz bei Fertigungsabweichungen: Bei der Fertigung von Leiterplatten kann es durch das Ätzen zu leichten Abweichungen kommen. Teardrops bieten eine zusätzliche Toleranz, die das Risiko verringert, dass Leiterbahnen zu schmal oder Pads unzureichend verbunden werden.
Signalintegrität: Insbesondere in Hochfrequenz-Anwendungen oder empfindlichen Schaltungen trägt die Teardrop-Form zur Aufrechterhaltung der Signalqualität bei, da scharfe Übergänge zu Problemen wie Impedanzabweichungen und Reflexionen führen könnten.
Anwendungsbereiche
Teardrops werden in der Regel in kritischen Designs eingesetzt, bei denen die Zuverlässigkeit und Stabilität der Verbindungen besonders wichtig ist. Dazu gehören unter anderem:
- Hochfrequenzschaltungen
- Leiterplatten für Automobilanwendungen
- Platinen, die hohen mechanischen oder thermischen Belastungen ausgesetzt sind
- PCB-Designs für die Luft- und Raumfahrttechnik
Fazit
Die Teardrop-Technik ist eine effektive Methode, um die Haltbarkeit und Zuverlässigkeit von Leiterbahnen und Verbindungen auf Leiterplatten zu verbessern. Indem sie mechanische Spannungen reduziert und elektrische Stabilität erhöht, trägt die tropfenförmige Gestaltung zu einer längeren Lebensdauer und besseren Leistung der elektronischen Geräte bei.
Teflon® ist ein Markenname für ein Polytetrafluorethylen (PTFE), ein synthetisches Polymer, das in der Leiterplattenfertigung vor allem für Hochfrequenzanwendungen und spezielle Einsatzgebiete verwendet wird. Aufgrund seiner einzigartigen Materialeigenschaften bietet Teflon® erhebliche Vorteile in bestimmten Anwendungen und ist ein gefragtes Material in der Elektronikindustrie.
Eigenschaften von Teflon® in der Leiterplattentechnik
Niedrige Dielektrizitätskonstante: Teflon® hat eine äußerst niedrige Dielektrizitätskonstante (etwa 2,1), was zu minimalen Signalverlusten führt. Diese Eigenschaft ist besonders vorteilhaft für Hochfrequenzanwendungen und Mikrowellenschaltungen, wo eine hohe Signalintegrität erforderlich ist.
Hervorragende Wärmebeständigkeit: Teflon® kann extrem hohen Temperaturen standhalten, was es ideal für den Einsatz in Umgebungen mit starken Temperaturschwankungen oder für Leiterplatten mit hoher Wärmebelastung macht.
Chemische Beständigkeit: Teflon® ist sehr widerstandsfähig gegen Chemikalien, was seine Lebensdauer auch in aggressiven Umgebungen verlängert.
Geringer Verlustfaktor: PTFE-Materialien wie Teflon® haben einen geringen Verlustfaktor, was bedeutet, dass sie besonders effektiv in Anwendungen sind, bei denen minimale Energieverluste gewünscht sind.
Anwendungen von Teflon® in Leiterplatten
Teflon® wird oft in Leiterplatten für anspruchsvolle Anwendungen eingesetzt, darunter:
- Hochfrequenzschaltungen und Mikrowellen-PCBs: Durch die niedrige Dielektrizitätskonstante und den geringen Verlustfaktor eignet sich Teflon® hervorragend für diese Anwendungen.
- Satelliten- und Raumfahrttechnik: Die Temperatur- und Strahlenbeständigkeit von Teflon® macht es für den Einsatz im All geeignet.
- Medizintechnik und Radar-Systeme: Die zuverlässigen Materialeigenschaften von Teflon® sind besonders in der Medizintechnik und bei hochpräzisen Radaranwendungen gefragt.
Verarbeitung und Herausforderungen
Teflon®-basierte Leiterplatten erfordern eine spezielle Verarbeitung und ein angepasstes Design, da Teflon® aufgrund seiner Glätte und Temperaturbeständigkeit schwieriger zu handhaben ist als andere Materialien wie FR4. Die Herstellung und Bearbeitung von Teflon®-Leiterplatten erfordert spezielle Verfahren wie besondere Bohr- und Frästechniken sowie angepasste Laminierverfahren.
Fazit
Teflon® ist ein wertvolles Material in der Leiterplattentechnik, insbesondere für Hochfrequenz- und Hochleistungsanwendungen. Seine hervorragenden thermischen und elektrischen Eigenschaften machen es zur bevorzugten Wahl für Anwendungen, die Präzision und Stabilität erfordern.
Tempern ist ein Wärmebehandlungsprozess in der Leiterplattenherstellung, der dazu dient, Spannungen im Material zu reduzieren und die Stabilität zu verbessern. Durch das Erwärmen der Leiterplatte auf eine kontrollierte Temperatur und das anschließende langsame Abkühlen können interne Spannungen abgebaut werden, die durch verschiedene Bearbeitungsschritte wie Bohren, Fräsen oder Laminieren entstanden sind. Tempern verbessert die mechanische Stabilität, verringert das Risiko von Delamination und sorgt für eine bessere Maßhaltigkeit der Leiterplatte, insbesondere bei hohen Betriebstemperaturen.
- TG
- THERMAL VIAS
- THROUGH HOLE VIA
- THT
Tg (Glasübergangstemperatur) bezeichnet die Temperatur, bei der das Harz im Leiterplattenmaterial von einem festen in einen gummiartigen Zustand übergeht. Diese Temperaturgrenze ist entscheidend für die mechanische und thermische Stabilität der Leiterplatte, insbesondere bei Anwendungen mit hohen Betriebstemperaturen.
Je höher die Tg-Temperatur, desto besser eignet sich das Material für Hochtemperaturanwendungen, ohne dass es seine strukturelle Integrität verliert. Typische Tg-Werte für Standardmaterialien liegen etwa bei 130–140 °C, während hochtemperaturbeständige Materialien Tg-Werte von 170 °C oder höher aufweisen.
Thermal Vias sind spezielle Durchkontaktierungen (Vias) auf Leiterplatten, die zur Ableitung von Wärme von hitzeempfindlichen Bauteilen genutzt werden. Diese Vias verbinden verschiedene Lagen einer Leiterplatte und sorgen dafür, dass Wärme effizient in kühlere Bereiche oder auf spezielle Kühlflächen abgeleitet wird. Sie sind besonders in Anwendungen mit hoher Leistungsdichte und Bauteilen, die viel Wärme erzeugen, wichtig.
Eigenschaften und Funktion von Thermal Vias
- Wärmeableitung: Die Vias transportieren die Wärme von heißen Bauteilen wie Leistungstransistoren oder Prozessoren in die darunter liegenden Kupferlagen oder Kühlkörper.
- Reduzierung der Betriebstemperatur: Sie tragen zur Verlängerung der Lebensdauer elektronischer Komponenten bei, indem sie deren Betriebstemperatur senken.
- Kupferfüllung: In manchen Fällen werden Thermal Vias mit Kupfer gefüllt, um die Wärmeleitfähigkeit zu verbessern.
Anwendung
Thermal Vias sind in der Leistungselektronik, LED-Technologie und in Hochfrequenzanwendungen weit verbreitet, wo effizientes Wärmemanagement entscheidend ist.
Through-Hole Vias sind durchgehende Durchkontaktierungen in einer Leiterplatte, die von der obersten bis zur untersten Kupferschicht verlaufen. Sie werden genutzt, um elektrische Verbindungen zwischen den verschiedenen Schichten der Leiterplatte herzustellen und tragen zur Stabilität der gesamten Struktur bei.
Eigenschaften und Anwendung von Through-Hole Vias
- Durchgehende Verbindung: Diese Vias verlaufen durch die gesamte Dicke der Leiterplatte, sodass alle Schichten miteinander verbunden werden können.
- Elektrische Leitfähigkeit: Sie bieten eine zuverlässige und starke elektrische Verbindung, was besonders in Schaltungen mit hohen Stromstärken wichtig ist.
- Mechanische Stabilität: Durch die Verbindung aller Lagen tragen Through-Hole Vias auch zur mechanischen Festigkeit der Leiterplatte bei.
Herstellung und Einsatzbereiche
Die Herstellung erfolgt durch Bohren und anschließende Metallisierung der Wände. Through-Hole Vias sind die am weitesten verbreitete Via-Art und finden in den meisten Standard-Leiterplatten Verwendung, insbesondere dort, wo zuverlässige elektrische und mechanische Verbindungen zwischen den Lagen erforderlich sind, wie in der Industrie- und Automobiltechnik.
THT (Through-Hole Technology) ist eine Montage- und Verbindungstechnologie, bei der elektronische Bauteile mit Drahtanschlüssen durch Löcher in der Leiterplatte gesteckt und dann auf der Gegenseite verlötet werden. Diese Technik wird häufig in Anwendungen eingesetzt, die eine hohe mechanische Stabilität erfordern, da die Lötstellen die Bauteile sicher in der Leiterplatte verankern.
Eigenschaften und Vorteile von THT
- Stabile Verbindungen: Da die Bauteilanschlüsse durch die gesamte Leiterplatte hindurch verlaufen und verlötet werden, ist die THT besonders robust und mechanisch belastbar.
- Widerstandsfähigkeit: THT-Bauteile sind in der Regel unempfindlicher gegenüber mechanischen Belastungen, was sie für industrielle Anwendungen und für Bauteile mit hoher Wärme- oder Strombelastung geeignet macht.
- Einfache Reparatur: Die größere Bauform und die gut sichtbaren Lötstellen ermöglichen eine einfache Reparatur und Austausch von Bauteilen.
Anwendungsbereiche
THT wird oft in Bereichen eingesetzt, die Langlebigkeit und Robustheit erfordern, wie z. B. in der Automobilindustrie, der Luft- und Raumfahrt sowie in Hochleistungselektronik. Auch in der Prototypenentwicklung wird THT aufgrund der leichteren Handhabung bevorzugt.
Nachteile gegenüber SMT
Im Vergleich zur Oberflächenmontagetechnologie (SMT) nimmt THT mehr Platz auf der Leiterplatte ein und ist daher weniger geeignet für Miniatur- oder Hochdichte-Schaltungen. SMT ermöglicht eine höhere Bauteildichte und ist die bevorzugte Technik für moderne, kompakte Elektronikprodukte.
- TIEFENFRÄSUNG
- TOMBSTONE-EFFEKT
- TOP
- TRACK/GAP
Tiefenfräsung bezieht sich auf einen Fertigungsschritt in der Leiterplattenherstellung, bei dem Material auf eine definierte Tiefe abgetragen wird, ohne die Leiterplatte vollständig zu durchbohren. Diese Technik wird verwendet, um spezielle Aussparungen, Vertiefungen oder mechanische Konturen zu erzeugen, die spezifische mechanische, thermische oder elektrische Anforderungen erfüllen.
Anwendungen der Tiefenfräsung
- Mechanische Anpassungen: Ermöglicht die Herstellung präziser Aussparungen und Profile, um Platz für Bauteile, Steckverbinder oder mechanische Befestigungen zu schaffen.
- Wärmemanagement: Vertiefungen können genutzt werden, um wärmeableitende Strukturen näher an hitzeempfindliche Komponenten zu bringen und die Wärmeableitung zu verbessern.
- Multilayer-Anpassungen: Bei Multilayer-Leiterplatten kann durch Tiefenfräsung die Dicke des Materials in bestimmten Bereichen reduziert werden, um spezifische Lagen leichter zugänglich zu machen.
Vorteile
- Präzision: Tiefenfräsung ermöglicht präzise, kontrollierte Bearbeitungstiefen, was besonders bei der Herstellung von komplexen Leiterplattenlayouts vorteilhaft ist.
- Flexibilität im Design: Erlaubt individuelle Anpassungen an die mechanischen Anforderungen und erleichtert die Integration von Bauteilen.
Herausforderungen
- Aufwendiger Herstellungsprozess: Tiefenfräsen erfordert spezialisierte Maschinen und erhöht die Produktionszeit und -kosten.
- Materialbelastung: Der Prozess kann zu Spannungen im Material führen, weshalb sorgfältige Planung und Qualitätskontrollen nötig sind.
Die Tiefenfräsung ist also ein wertvolles Verfahren in der Leiterplattenherstellung, um Designs präzise an spezielle mechanische und thermische Anforderungen anzupassen.
Vgl. auch → Z-Fräsung
Tombstone-Effekt bezeichnet ein Problem, das beim Bestücken von Leiterplatten mit oberflächenmontierten Bauteilen (SMDs) auftreten kann, insbesondere bei der Lötung von Bauteilen mit zwei Lötanschlüssen. Der Effekt führt dazu, dass ein Bauteil während des Lötprozesses nicht korrekt auf der Leiterplatte sitzt und sich wie ein „Tombstone“ (Grabstein) aufrichtet. Dies ist unerwünscht, da es zu Fehlfunktionen oder Verbindungsproblemen führen kann.
Ursachen des Tombstone-Effekts
- Ungleichmäßige Lötpastendosierung: Wenn eine Seite des Bauteils mehr Lötpaste enthält als die andere, kann die stärkere Lötung auf einer Seite das Bauteil anheben, während die andere Seite noch nicht vollständig verlötet ist.
- Ungleichmäßige Wärmeverteilung: Wenn die Wärme während des Lötprozesses ungleichmäßig verteilt wird, etwa durch eine falsche Einstellung im Reflow-Ofen, kann dies dazu führen, dass eine Seite des Bauteils schneller schmilzt und das Bauteil kippt.
- Fehlerhafte Bestückung: Eine falsche Platzierung des Bauteils auf der Leiterplatte kann ebenfalls den Tombstone-Effekt verursachen. Insbesondere bei Bauteilen mit nicht symmetrischen Anschlüssen oder bei schlechten Ausrichtungsprozessen.
- Verwendung von Bauteilen mit asymmetrischen Massen: Bauteile mit einer ungleichmäßigen Massenverteilung (z. B. Kondensatoren oder Bauteile mit größerem Gehäuse auf einer Seite) neigen ebenfalls dazu, den Tombstone-Effekt zu erzeugen.
Auswirkungen
- Verbindungsprobleme: Der Tombstone-Effekt kann dazu führen, dass eines der Lötfugen des Bauteils nicht richtig hergestellt wird, was die elektrische Verbindung unterbricht.
- Bauteilschäden: Der Bauteil könnte mechanisch beschädigt werden, wenn er sich während des Lötvorgangs hebt oder kippt.
- Zuverlässigkeitsprobleme: Bauteile, die durch den Tombstone-Effekt schlecht verlötet sind, könnten später in der Nutzung ausfallen, was die Zuverlässigkeit des gesamten Geräts beeinträchtigt.
Prävention des Tombstone-Effekts
- Gleichmäßige Lötpaste: Eine präzise Dosierung der Lötpaste ist entscheidend. Es sollte eine gleichmäßige Verteilung der Paste auf beiden Lötpads vorhanden sein.
- Optimierung der Wärmeprofile: Die Reflow-Lötprozesse sollten so eingestellt werden, dass die Wärme gleichmäßig auf das Bauteil und die Leiterplatte verteilt wird.
- Verwendung symmetrischer Bauteile: Bauteile mit symmetrischen Massen und Anschlüssen sind weniger anfällig für den Tombstone-Effekt.
- Exakte Bestückung: Das Bauteil sollte korrekt ausgerichtet und platziert werden, um eine gleichmäßige Lötung zu gewährleisten.
Der Tombstone-Effekt ist ein häufiges Problem in der SMD-Technologie, das durch sorgfältige Fertigungstechnik und Überwachung der Lötprozesse effektiv minimiert werden kann.
Top kann in der Elektronik- und Leiterplattenfertigung verschiedene Bedeutungen haben. Hier sind einige der häufigsten Verwendungen des Begriffs:
1. Top Layer (Oberste Schicht)
In der Leiterplattenfertigung bezeichnet „Top“ die oberste Schicht einer mehrlagigen Leiterplatte (Multilayer PCB). Diese Schicht ist oft die, auf der die meisten oberflächenmontierten Bauteile (SMD) und Leiterbahnen angeordnet sind. Der Begriff kann sich auch auf die oberste Schicht einer einfachen einseitigen Leiterplatte beziehen, auf der die elektrischen Verbindungen und Komponenten montiert werden.
- Top Layer im PCB-Design: Das Design auf der Top Layer ist entscheidend für die Funktion der Leiterplatte, da hier die Hauptverbindungen für die Bauteile verlaufen.
- Top und Bottom Layer: In vielen Multilayer-Leiterplatten gibt es sowohl eine „Top“ als auch eine „Bottom“ Layer, wobei zwischen diesen Schichten die inneren Lagen (z. B. Signal- oder Power-Layers) enthalten sind.
2. Top View (Ansicht von oben)
In der PCB-Designsoftware bezieht sich „Top View“ auf die Ansicht der Leiterplatte von oben, also von der Seite, die während der Bestückung sichtbar ist. Diese Perspektive hilft Designern, die Anordnung der Bauteile, die Leiterbahnen und die Verbindungen besser zu verstehen und zu optimieren.
3. Top Side (Oberseite)
In der Montage von elektronischen Geräten bezeichnet die „Top Side“ die obere Seite eines Bauteils oder einer Platine, die oft die Seite ist, die nach der Montage des Produkts sichtbar ist. Dies ist die Seite, auf der die meisten Komponenten, wie Chips oder SMD-Bauteile, montiert sind.
4. Top Coat (Oberflächenbeschichtung)
Manchmal wird der Begriff „Top“ auch verwendet, um sich auf die abschließende Beschichtung oder Versiegelung zu beziehen, die auf der Leiterplatte oder einem Bauteil aufgebracht wird. Dies könnte eine Schutzschicht wie eine Lötstopplackbeschichtung oder eine schützende Oberflächenbeschichtung wie OSP (Organic Solderability Preservative) sein, die das Bauteil vor Korrosion schützt.
Zusammenfassung:
Der Begriff „Top“ hat in der Leiterplattenfertigung unterschiedliche Bedeutungen, meistens aber eine Verbindung zur obersten Schicht, Ansicht oder Seite der Leiterplatte oder des Bauteils.
Track/Gap bezieht sich auf zwei wichtige Parameter im Design von Leiterplatten (PCBs), die für die Größe und den Abstand der elektrischen Verbindungen auf der Leiterplatte verantwortlich sind. Diese Parameter sind entscheidend für die elektrische Leistung, das Design und die Fertigung von PCBs. Hier sind die Details:
Track (Leiterbahn)
Die Track (oder Leiterbahn) ist die metallene Verbindung, die auf einer Leiterplatte verläuft und die verschiedenen Bauteile miteinander verbindet. Sie dient dazu, elektrische Signale und Energie zu transportieren. Die Breite der Leiterbahn hat einen direkten Einfluss auf den Widerstand, die Signalqualität und die Fähigkeit, Strom zu führen.
- Breite der Track: Die Breite der Leiterbahn wird durch verschiedene Faktoren bestimmt, wie den maximalen Strom, der durch sie fließt, die gewünschte Impedanz (bei Hochfrequenzdesigns) und die Fertigungskapazitäten.
- Maximale Strombelastbarkeit: Eine breitere Leiterbahn kann mehr Strom führen, während eine schmalere Leiterbahn weniger Strom vertragen kann, ohne dass sie überhitzt oder einen zu hohen Widerstand aufweist.
Gap (Abstand)
Der Gap bezieht sich auf den Abstand zwischen benachbarten Leiterbahnen oder zwischen einer Leiterbahn und einem Bauteil auf der Leiterplatte. Es ist entscheidend für die Isolierung und das Verhindern von Kurzschlüssen.
- Abstand zwischen Tracks: Der Gap muss ausreichend groß sein, um sicherzustellen, dass keine ungewollten elektrischen Verbindungen zwischen benachbarten Leiterbahnen entstehen. Dies ist besonders wichtig, wenn hohe Spannungen oder empfindliche Signale auf der Platine vorhanden sind.
- Fertigungstechnische Grenzen: Der Gap wird durch die Fertigungstechnologie und die verwendeten Materialien bestimmt. Zu kleine Abstände können zu Problemen bei der Produktion führen, wie z.B. Kurzschlüssen oder Defekten beim Ätzen.
Verhältnis von Track und Gap
Das Verhältnis von Track zu Gap ist ein entscheidender Faktor bei der Leiterplattenentwicklung. Es muss so gewählt werden, dass die Schaltung zuverlässig funktioniert und gleichzeitig die Fertigungskosten sowie die Produktionsanforderungen berücksichtigt werden.
- Designregeln: Im PCB-Design gibt es häufig festgelegte Regeln für die Mindestbreite der Leiterbahnen (Track) und den Mindestabstand (Gap), abhängig von der Fertigungstechnologie, die verwendet wird.
- Einfluss auf Leistung: Ein engerer Abstand zwischen den Leiterbahnen (kleiner Gap) kann zu einer höheren Kapazitivität und damit zu Signalverlusten oder Interferenzen führen, insbesondere bei Hochfrequenzsignalen.
Anwendungen und Einfluss
- Hochfrequenzdesigns: Bei Hochfrequenzanwendungen, wie in Kommunikationssystemen, sind das Verhältnis von Track zu Gap und die präzise Impedanzkontrolle sehr wichtig, um Signalverluste und Rauschen zu minimieren.
- Leistungsbauteile: In Hochstromanwendungen müssen die Track-Breiten so gewählt werden, dass sie den Strom sicher führen können, ohne dass es zu einer Überhitzung kommt.
Fazit
Das Track/Gap-Verhältnis ist ein kritischer Aspekt des PCB-Designs, der die elektrische Integrität und die Fertigungseffizienz beeinflusst. Eine sorgfältige Auswahl und Berücksichtigung dieser Parameter ist notwendig, um zuverlässige, leistungsfähige Leiterplatten zu erzeugen.
- UL
UL steht für Underwriters Laboratories, eine internationale Organisation, die Sicherheitsstandards entwickelt und Produkte auf ihre Sicherheit hin testet. UL ist besonders bekannt für ihre Arbeit im Bereich der elektronischen und elektrischen Geräte und Komponenten, darunter auch Leiterplatten und Materialien, die in der Elektronikindustrie verwendet werden.
UL in der Leiterplattenindustrie
In der Leiterplattenindustrie bezieht sich UL oft auf Zertifizierungen und Prüfungen von Materialien, die in der Fertigung von Leiterplatten verwendet werden. Eine UL-Zertifizierung stellt sicher, dass ein Produkt bestimmten Sicherheitsstandards entspricht, insbesondere in Bezug auf Brandschutz, elektrische Sicherheit und Haltbarkeit.
UL-Standards und -Zertifikate für Leiterplatten:
UL 94 – Diese Norm definiert die Brennbarkeitsklassifikationen von Kunststoffmaterialien. Sie ist besonders wichtig für die Materialwahl in der Leiterplattenherstellung, da sie garantiert, dass das Material im Brandfall sicher reagiert.
- V-0, V-1, V-2: Diese Klassifizierungen geben an, wie schnell sich das Material nach einer Entzündung wieder löschen kann. V-0 ist die höchste Klassifizierung.
UL 746A – Diese Norm betrifft die Materialien, die für elektronische Geräte und Leiterplatten verwendet werden. Sie definiert die Anforderungen für die thermischen, elektrischen und mechanischen Eigenschaften von Materialien, die für Elektronikgehäuse und Leiterplatten geeignet sind.
UL 796 – Diese Norm bezieht sich speziell auf Leiterplatten. Sie stellt sicher, dass Leiterplatten die Sicherheitsanforderungen für elektronische Geräte erfüllen, die in den USA verkauft werden. Sie umfasst Prüfungen für Brandschutz, mechanische Belastung und Elektrizität.
UL 50 – Diese Norm betrifft die Gehäuse für elektrische Geräte und kann auch für Leiterplattengehäuse gelten, die spezifische Schutzanforderungen in Bezug auf Temperatur, Feuchtigkeit und Staub erfüllen müssen.
UL-Logo und -Kennzeichnung
Ein UL-Logo auf einem Produkt zeigt an, dass das Produkt auf Sicherheitsstandards geprüft und zugelassen wurde. Für Leiterplattenhersteller bedeutet dies, dass ihre verwendeten Materialien und Fertigungstechniken die festgelegten Sicherheitskriterien erfüllen und die Produkte in bestimmten Märkten verkauft werden dürfen.
- UL-Zertifizierung für Leiterplatten: Ein Leiterplattenhersteller muss seine Materialien und Prozesse durch UL testen lassen, um sicherzustellen, dass sie den entsprechenden Sicherheitsstandards entsprechen. Dies ist besonders wichtig für den Einsatz in sicherheitskritischen Bereichen wie der Automobilindustrie, Medizintechnik und Luftfahrt.
Fazit
Die UL-Zertifizierung ist ein wesentlicher Aspekt der Qualitätssicherung in der Leiterplattenindustrie. Sie stellt sicher, dass die verwendeten Materialien und Produkte sicher und zuverlässig sind, was besonders in Anwendungen mit hohen Anforderungen an die Sicherheit, wie in elektronischen Geräten und Maschinen, entscheidend ist.
- VERWÖLBUNG/VERWINDUNG
- VIA
- VIA-ABDECKUNG/VERSCHLUSS
Verwölbung oder Verwindung sind Begriffe, die sich auf die physikalische Veränderung der Form von Leiterplatten (PCBs) während oder nach der Fertigung beziehen. Diese Probleme können die Funktionalität und Zuverlässigkeit der Leiterplatten beeinträchtigen, insbesondere bei der Montage von Bauteilen oder beim Lötprozess.
Verwölbung
Verwölbung bezeichnet eine unerwünschte Verformung der Leiterplatte, bei der sie in der Mitte nach oben oder unten gewölbt ist. Diese Formveränderung kann sowohl während des Herstellungsprozesses als auch während des Betriebs der Leiterplatte auftreten.
Ursachen:
- Unterschiedliche Materialausdehnung: Materialien, die in der Leiterplattenfertigung verwendet werden (z.B. FR4, Kupfer), dehnen sich bei Temperaturänderungen unterschiedlich aus. Wenn diese Materialien ungleichmäßig erhitzt oder abgekühlt werden, kann es zu einer Verwölbung der Leiterplatte kommen.
- Unzureichende Aushärtung von Prepreg: Wenn die Prepreg-Schicht (das Material, das als Isolator zwischen den Kupferschichten dient) nicht korrekt oder gleichmäßig ausgehärtet wird, kann dies die Spannung in der Leiterplatte erhöhen und zu einer Verwölbung führen.
- Unbalanced Copper Layers: Eine ungleichmäßige Verteilung von Kupfer auf den verschiedenen Schichten der Leiterplatte kann ebenfalls zu Spannungen führen, die die Leiterplatte verformen.
Auswirkungen:
- Bauteilmontage: Verwölbte Leiterplatten können dazu führen, dass Bauteile nicht korrekt auf den Pads sitzen, was Probleme bei der Bestückung und Lötung verursacht.
- Lötqualität: Eine gewölbte Leiterplatte kann dazu führen, dass Lötstellen unsauber oder unvollständig sind, was die Verbindung zwischen Bauteilen und Leiterbahnen schwächt.
Lösungen:
- Kontrollierte Temperaturprofile: Sorgfältige Überwachung und Steuerung der Temperatur während des Herstellungsprozesses, insbesondere beim Lötprozess, können helfen, Verwölbungen zu vermeiden.
- Verstärkungen und Stabilisatoren: Der Einsatz von Verstärkungen oder stiffen (Steg- und Riegel-Elementen) kann helfen, die Stabilität der Leiterplatte während der Fertigung und im Betrieb zu erhöhen.
Verwindung
Verwindung bezieht sich auf die Torsionsveränderung oder Verdrehung der Leiterplatte um ihre Achse. Eine verzwirbelte oder verdrehte Leiterplatte kann dazu führen, dass die Lötstellen und Bauteile nicht richtig ausgerichtet sind, was zu Fehlern in der elektronischen Schaltung führen kann.
Ursachen:
- Temperaturschock: Ein plötzliches Erhitzen oder Abkühlen der Leiterplatte kann Spannungen in den verschiedenen Schichten erzeugen, was zu einer Verdrehung führt.
- Fehlerhafte Lamination: Ungleichmäßige Schichtbildung oder Laminierungsfehler können zu Verwindung führen.
Auswirkungen:
- Bestückung: Bei einer verdrehten Leiterplatte ist es schwieriger, Bauteile korrekt auszurichten, was zu fehlerhaften Lötstellen und schlechter Verbindungsqualität führen kann.
- Bauteilverbindungen: Verwindung kann dazu führen, dass Bauteile nicht fest mit den Pads verbunden sind, was die elektrischen Eigenschaften der Schaltung negativ beeinflusst.
Lösungen:
- Optimierung des Laminierungsprozesses: Sorgfältige Kontrolle des Laminierungsprozesses, um die Schichten gleichmäßig zu verpressen.
- Verstärkungen: Der Einsatz von Stegen oder Verstärkungen auf der Leiterplatte kann helfen, Verwindungen zu verhindern.
Fazit
Verwölbung und Verwindung sind häufige Probleme in der Leiterplattenfertigung, die die mechanische Integrität und elektrische Leistung von PCBs beeinträchtigen können. Eine sorgfältige Materialauswahl, eine präzise Temperaturkontrolle und geeignete Fertigungstechniken sind notwendig, um diese Probleme zu minimieren und eine zuverlässige Leiterplatte zu gewährleisten.
Via bezeichnet in der Leiterplattenfertigung ein Loch, das durch die Schichten einer Leiterplatte (PCB) gebohrt wird, um elektrische Verbindungen zwischen verschiedenen Schichten herzustellen. Diese Löcher werden mit Kupfer beschichtet, um eine elektrische Verbindung zwischen den Leiterbahnen auf unterschiedlichen Schichten der Leiterplatte zu ermöglichen. Vias sind ein wesentlicher Bestandteil von Mehrschicht-Leiterplatten (Multilayer-PCBs) und ermöglichen eine komplexe Verdrahtung auf der Platine.
Arten von Vias:
Through-Hole Via (THV)
- Definition: Ein Through-Hole Via ist ein Loch, das die gesamte Dicke der Leiterplatte durchbohrt, also von der Oberseite bis zur Unterseite.
- Verwendung: Diese Vias werden verwendet, um Signale oder Strom zwischen den obersten und unteren Schichten der Leiterplatte zu verbinden. Sie sind die häufigste Art von Via und werden oft in Leiterplatten mit wenigen Schichten verwendet.
- Vorteil: Einfach zu fertigen und weit verbreitet in der PCB-Industrie.
Blind Via
- Definition: Ein Blind Via verbindet die obersten Schichten (z. B. die oberste Lötstoppmaske) mit einer inneren Schicht der Leiterplatte, ohne die unterste Schicht zu erreichen.
- Verwendung: Blind Vias werden in mehrschichtigen Leiterplatten verwendet, um Platz zu sparen und das Design effizienter zu gestalten.
- Vorteil: Reduziert den Platzbedarf und ermöglicht kompaktere Designs.
Buried Via
- Definition: Ein Buried Via verbindet zwei oder mehr innere Schichten der Leiterplatte miteinander, ohne von der obersten oder untersten Schicht sichtbar zu sein.
- Verwendung: Diese Vias kommen in komplexeren Leiterplatten mit vielen Schichten zum Einsatz, insbesondere in hochentwickelten elektronischen Anwendungen, bei denen jede Schicht und jede Verbindung optimiert werden muss.
- Vorteil: Bietet noch mehr Designfreiheit und optimiert den Platzbedarf in hochkomplexen Mehrschicht-PCBs.
Microvia
- Definition: Microvias sind extrem kleine Vias, die in der Regel mit Lasertechnologie gebohrt werden. Sie haben einen Durchmesser von weniger als 0,15 mm und sind für Hochleistungs-PCBs mit feinen Leiterbahnen und hoher Dichte ausgelegt.
- Verwendung: Microvias werden in modernen Elektronikdesigns wie Smartphones, Tablets und anderen kompakten Geräten eingesetzt, bei denen Platz und Leistung entscheidend sind.
- Vorteil: Ermöglicht sehr dichte Leiterbahnen und platzsparende Designs.
Via-Technologien:
HDI (High Density Interconnect)
- HDI-PCBs nutzen Microvias und Blind/Buried Vias, um eine hohe Dichte von Leiterbahnen und Verbindungen auf engstem Raum zu ermöglichen. Sie kommen in komplexen elektronischen Geräten zum Einsatz, die geringe Abmessungen und hohe Leistung erfordern.
Laserbohren
- Bei der Fertigung von Microvias und feinen Vias wird häufig Lasertechnologie eingesetzt, da diese eine hohe Präzision und geringe Bohrdurchmesser ermöglicht. Laserbohren bietet eine genaue Steuerung der Lochgröße und -position und wird in modernen PCBs mit hoher Dichte verwendet.
Vorteile der Verwendung von Vias:
- Platzersparnis: Vias ermöglichen es, dass Verbindungen in verschiedene Schichten einer Leiterplatte eingebaut werden, ohne dass die gesamte Fläche der Platine von Leiterbahnen bedeckt wird.
- Flexibilität: Sie erlauben komplexe Designs, die bei nur einer Schicht oder wenigen Schichten nicht möglich wären.
- Verbesserte Signalübertragung: Durch die Nutzung von Vias können Signale effizienter über verschiedene Schichten der Leiterplatte übertragen werden, was zu einer besseren Signalintegrität führt.
Fazit:
Vias sind unerlässlich für die Erstellung von Mehrschicht-Leiterplatten und ermöglichen die Verbindung von Schichten innerhalb einer komplexen Platine. Je nach Designanforderungen und Platzbedarf kommen unterschiedliche Via-Typen zum Einsatz, wie Through-Hole, Blind, Buried oder Microvias. Der Einsatz von Vias trägt zur Miniaturisierung und Effizienzsteigerung moderner elektronischer Geräte bei.
Vgl. auch → Durchkontaktierung → Blind Via → Buried Via → Stacked Via → Staggered Via
Via-Abdeckungsverschluss (auch bekannt als Via Plugging oder Via Sealing) bezeichnet den Prozess, bei dem die Vias auf einer Leiterplatte (PCB) nach dem Bohren und Behandeln mit einem Material (oft Epoxidharz oder einem ähnlichen Füllmaterial) verschlossen oder abgedeckt werden. Dieser Schritt dient der Verhinderung von unerwünschtem Kontakt, insbesondere wenn Vias als ungenutzte Verbindungen oder in bestimmten Bereichen, wie etwa der Lötstopplackmaske, isoliert werden müssen.
Gründe für den Einsatz von Via-Abdeckungsverschlüssen:
Vermeidung von Kurzschlüssen:
- Wenn Vias nicht richtig verschlossen werden, kann Feuchtigkeit oder Luft eindringen, was zu elektrischen Kurzschlüssen oder Korrosion führen kann. Der Verschluss schützt die Leiterplatte und ihre elektrischen Verbindungen.
Erhöhung der Robustheit:
- Ein Verschluss schützt die Platine vor mechanischen Belastungen und chemischen Angriffen, indem er die Vias versiegelt und deren Struktur stabilisiert.
Verhindern von Lötfehlern:
- Beim Löten könnte das Lot in die offenen Vias fließen, was zu Verunreinigungen und Lötfehlern führen kann. Ein verschlossenes Via verhindert dies.
Optische oder mechanische Anforderungen:
- In einigen Designs, bei denen optische Anforderungen oder spezifische mechanische Eigenschaften berücksichtigt werden müssen, können Vias verschlossen werden, um die Oberfläche glatt und einheitlich zu halten.
Verbesserung der elektrischen Performance:
- Durch das Verschließen der Vias können Strahlungs- oder Signalstörungen vermieden werden, da die geschlossenen Vias eine bessere Isolierung bieten und so die Signalqualität erhalten bleibt.
Methoden des Via-Abdeckungsverschlusses:
Abdecken mit Lötstopplack (Covered Via):
- Das Via wird mit Lötstopplack überdruckt. Diese Technik ermöglicht das zuverlässige Aufbringen von Lötstopplack über den Restring. Allerdings wird die Füllung des zugehörigen Lochs nicht zuverlässig garantiert, was die Verwendbarkeit in bestimmten Anwendungen einschränken kann.
Tented Via:
- Hier wird die Bohrung im Via zunächst mit einem Vakuum-laminierten Maskenmaterial überdeckt, auf das dann eventuell Lötstopplack aufgebracht werden kann. Diese Methode wird verwendet, um Vias zu verschließen, während gleichzeitig die Möglichkeit bleibt, diese für bestimmte Anwendungen zugänglich zu halten.
Plugged Via:
- Das Via wird ein- oder doppelseitig mit einem speziellen Material verschlossen, das nicht elektrisch leitet. Dies sorgt für eine vollständige Isolation des Vias von anderen Leiterbahnen und schützt vor Feuchtigkeit und anderen äußeren Einflüssen.
Filled Via:
- Bei dieser Technik wird das Via komplett mit einem nicht leitenden Material verschlossen. Diese Methode wird oft verwendet, um eine vollständige Isolierung und Stabilität zu gewährleisten.
Covered Vias und Tented Vias werden heute in der Branche nicht mehr empfohlen und von vielen Herstellern auch nicht mehr angeboten, da diese Methoden nicht immer die erforderliche Zuverlässigkeit bieten.
Normen und Standards:
Die verschiedenen Techniken der Via-Abdeckung und -Verschließung sind in IPC-4761 definiert, einem Standard der IPC, einer internationalen Organisation, die Standards für die Leiterplatten- und Elektronikindustrie entwickelt. Dieser Standard regelt die verschiedenen Methoden der Via-Verschließung und gibt Empfehlungen zur Auswahl der richtigen Technik, abhängig von den spezifischen Anforderungen der Leiterplatte und ihrer Anwendung.
Fazit:
Der Via-Abdeckungsverschluss ist eine wichtige Technik in der Leiterplattenfertigung, um die Funktionalität und Langlebigkeit von PCBs zu gewährleisten. Durch das Verschließen von Vias wird die Platine vor Kurzschlüssen, Korrosion und mechanischen Belastungen geschützt. Es bietet eine erhöhte Zuverlässigkeit und verbessert die elektrische Performance von Leiterplatten, insbesondere in komplexen und hochdichten Designs. Die Auswahl der richtigen Verschlussmethode hängt von der Anwendung und den spezifischen Anforderungen der Schaltung ab.
- WÄRMEFALLE
- WELLENLÖTEN
Wärmefalle bezieht sich auf einen Bereich auf einer Leiterplatte oder in einem elektronischen Gerät, der dazu dient, überschüssige Wärme von empfindlichen Bauteilen oder Komponenten abzuleiten, um eine Überhitzung zu verhindern und die Betriebsstabilität und Lebensdauer zu gewährleisten. Diese Technik ist besonders in Anwendungen mit hoher Leistung oder bei Bauteilen, die viel Wärme erzeugen, wie z.B. Leistungstransistoren, Prozessoren oder Hochleistungsdioden, von Bedeutung.
Funktion und Zweck der Wärmefalle:
Wärmeableitung:
- Die Hauptfunktion einer Wärmefalle ist es, die überschüssige Wärme von einem heißen Bereich zu einem kühleren Bereich zu leiten. Dadurch wird die Temperatur des Bauteils gesenkt, was seine Leistung stabilisiert und eine Beschädigung durch Überhitzung verhindert.
Vermeidung von Hotspots:
- In komplexen elektronischen Schaltungen entstehen häufig Hotspots, an denen sich die Wärme konzentriert. Eine Wärmefalle kann diese Hotspots gezielt abfangen und die Wärme gleichmäßiger verteilen, sodass keine einzelnen Komponenten überhitzen.
Schutz vor thermischem Stress:
- Elektronische Bauteile sind empfindlich gegenüber thermischem Stress, der zu Materialversagen oder einer verringerten Lebensdauer führen kann. Wärmefallen helfen, diesen Stress zu minimieren und die Bauteile langfristig funktionsfähig zu halten.
Arten von Wärmefallen:
Thermische Pads und Wärmeleitmaterialien:
- Diese Materialien werden zwischen Bauteilen und Kühlkörpern oder Leiterplattenpositionen eingesetzt, um die Wärmeübertragung zu verbessern. Sie sind in verschiedenen Formen und Materialien erhältlich, wie z.B. Silikonpads, Graphitfolien oder spezielle Wärmeleitpasten.
Wärmeleitplatten:
- Platten aus hoch wärmeleitfähigem Material (z.B. Kupfer oder Aluminium) können als Wärmefallen fungieren, indem sie Wärme von den heißen Bereichen aufnehmen und diese dann über eine größere Fläche abführen.
Kühlkörper:
- Ein häufig eingesetztes Mittel, um die Wärme abzuführen, sind Kühlkörper, die in Verbindung mit Wärmefallen verwendet werden, um die Wärme effizienter abzustrahlen.
Metallisierung und Leiterplattenstrukturen:
- In bestimmten Anwendungen können auch speziell gestaltete Leiterplattenstrukturen, wie z.B. Dickkupfertechnologie oder spezielle Kupferflächen auf der Platine, zur Wärmeableitung genutzt werden.
Anwendungen von Wärmefallen:
- Leistungsbauteile: Besonders in Leistungselektronik und Hochfrequenztechnik kommen Wärmefallen häufig zum Einsatz, um Bauteile wie Transistoren, Prozessoren und Dioden vor Überhitzung zu schützen.
- PCBs und Smartphones: Bei der Herstellung von Leiterplatten für elektronische Geräte werden Wärmefallen integriert, um die Effizienz von Geräten wie Computern, Smartphones und Konsolen zu erhöhen und deren Lebensdauer zu verlängern.
- LED-Technologie: In der LED-Technologie werden Wärmefallen eingesetzt, um die hohe Wärmeentwicklung bei LEDs abzuleiten und eine optimale Lichtausbeute sowie Lebensdauer zu gewährleisten.
Fazit:
Wärmefallen spielen eine entscheidende Rolle in der Elektronikfertigung, indem sie sicherstellen, dass Bauteile und Geräte auch bei hoher Leistungsabgabe stabil und effizient arbeiten. Durch die richtige Implementierung von Wärmefallen wird nicht nur die Lebensdauer der Komponenten verlängert, sondern auch die Gesamtleistung des Geräts verbessert.
Wellenlöten ist ein Fertigungsprozess, der in der Elektronikindustrie häufig verwendet wird, um elektronische Bauteile auf Leiterplatten (PCBs) zu löten. Es handelt sich um ein Verfahren, bei dem die Leiterplatte über eine Welle geschmolzenen Lotes geführt wird, um die Lötstellen der Bauteile auf der Platine zu erzeugen. Dieser Prozess ist besonders für die Bestückung von Bauteilen mit Durchkontaktierungen (THT – Through-Hole Technology) geeignet.
Funktionsweise des Wellenlötens:
Vorbereitung der Platine:
- Die Leiterplatte wird mit den zu lötenden Bauteilen bestückt. In der Regel handelt es sich dabei um Bauteile mit Drahtanschlüssen, die durch die Durchkontaktierungen in der Platine hindurchgeführt werden.
Flussmittelauftrag:
- Bevor die Platine in die Lötwelle eintritt, wird auf die zu lötenden Kontaktflächen ein Flussmittel aufgebracht. Dieses hilft, die Oxide von den Lötflächen zu entfernen und sorgt für eine bessere Verbindung zwischen Lötzinn und Leiterplatte.
Erwärmung der Platine:
- Die Platine wird auf eine geeignete Temperatur vorgewärmt, um die Temperaturgradienten während des Lötvorgangs zu minimieren und sicherzustellen, dass das Lötzinn gut fließt.
Lötwelle:
- Die Platine wird nun über eine Welle geschmolzenen Lotes geführt. Diese Welle wird aus einem Bad aus flüssigem Lötzinn gebildet, das konstant in Bewegung ist. Das Lötzinn wird durch die Kontaktflächen der Bauteile gezogen und verbindet die Pins der Bauteile mit den entsprechenden Leiterbahnen auf der Platine.
Abkühlung:
- Nach dem Kontakt mit der Lötwelle wird die Platine abgekühlt, wodurch das Lötzinn erstarrt und eine feste Verbindung zwischen den Bauteilen und der Leiterplatte entsteht.
Vorteile des Wellenlötens:
Effizienz:
- Wellenlöten ist ein schneller und automatisierter Prozess, der in großen Stückzahlen eingesetzt werden kann, was es ideal für die Massenproduktion von Leiterplatten macht.
Konsistente Qualität:
- Durch den kontrollierten Prozess kann eine gleichmäßige und zuverlässige Lötung erzielt werden, die zu stabilen elektrischen Verbindungen führt.
Geringe Arbeitskosten:
- Wellenlöten erfordert weniger manuelle Eingriffe und ist daher kostengünstig im Vergleich zu anderen Lötverfahren.
Eignung für THT-Bauteile:
- Wellenlöten eignet sich besonders gut für Bauteile, die Durchkontaktierungen haben, wie z.B. Widerstände, Kondensatoren oder ICs.
Nachteile des Wellenlötens:
Eingeschränkte Flexibilität:
- Das Verfahren ist weniger flexibel für Bauteile mit speziellen Anforderungen, z.B. für SMD-Bauteile (Surface-Mounted Devices), die auf der Oberseite der Leiterplatte montiert werden.
Kostspielig bei kleinen Serien:
- Für kleine Produktionsmengen kann Wellenlöten aufgrund der Einrichtungskosten und der Notwendigkeit spezieller Maschinen teuer sein.
Möglichkeit von Brückenbildung:
- Beim Wellenlöten kann es zu einer Brückenbildung zwischen benachbarten Lötpads kommen, was zu Kurzschlüssen führen kann. Dies erfordert eine präzise Prozesskontrolle.
Anwendungen des Wellenlötens:
Massenproduktion von THT-Bauteilen:
- Wellenlöten wird vor allem in der Serienfertigung von Leiterplatten verwendet, insbesondere bei Produkten, die viele THT-Bauteile enthalten.
Industrieelektronik:
- Es ist weit verbreitet in der Herstellung von Industrieelektronik, Fahrzeugkomponenten, Haushaltsgeräten und vielen anderen elektronischen Geräten.
Prototypenfertigung:
- In der Prototypenfertigung wird Wellenlöten oft genutzt, wenn größere Mengen von THT-Bauteilen auf Leiterplatten gelötet werden müssen.
Fazit:
Das Wellenlöten bleibt trotz modernerer Löttechniken wie Selektivlöten und Reflow-Löten eine der zuverlässigsten Methoden für das Löten von Durchkontaktierungen in der Elektronikfertigung. Es bietet eine kostengünstige und effiziente Möglichkeit zur Herstellung von Leiterplatten in großen Stückzahlen, eignet sich jedoch am besten für THT-Bauteile.
Vgl. auch → Schwalllöten
- X-OUT
- X-RAY
X-Out bezieht sich in der Elektronikfertigung auf eine Methode zur Identifikation und Kennzeichnung von defekten oder fehlerhaften Leiterplatten (PCBs) oder Bauteilen innerhalb eines Produktionsprozesses. Das X-Out-Verfahren wird häufig verwendet, um Platinen, die nicht den Qualitätsanforderungen entsprechen, aus der Produktion zu entfernen und nicht weiter zu verarbeiten. Der Begriff „X-Out“ kommt von der Markierung, die auf der defekten Platte gesetzt wird (häufig ein „X“), um sie eindeutig als fehlerhaft zu kennzeichnen.
Anwendung des X-Out-Verfahrens:
Fehlererkennung:
- Bei der Qualitätskontrolle in der Produktion werden Platinen auf verschiedene Fehler geprüft, wie etwa falsche Lötverbindungen, Kurzschlüsse, offene Verbindungen, fehlerhafte Bauteile oder unvollständige Bestückung. Wenn Fehler gefunden werden, wird die fehlerhafte Platine mit einem „X“ oder einer anderen Markierung versehen, um sie von den fehlerfreien Platinen zu unterscheiden.
Fehlerbehebung:
- Nachdem eine Platine als „X-Out“ markiert wurde, wird sie entweder aus der Produktion entfernt, um eine manuelle Reparatur oder Nacharbeit zu unterziehen, oder sie wird für die Aussortierung und Verschrottung vorbereitet. Der Zweck des X-Outs ist, sicherzustellen, dass fehlerhafte Platinen nicht versehentlich weiterverarbeitet oder ausgeliefert werden.
Vermeidung von Ausschuss:
- X-Out hilft, den Ausschuss zu reduzieren, indem fehlerhafte Bauteile frühzeitig erkannt und aus dem Produktionsfluss entfernt werden. Dies trägt zu einer höheren Produktqualität bei, da die fehlerhaften Teile nicht weiter in den Produktionsprozess eingehen.
Vorteile des X-Outs:
Früherkennung von Fehlern:
- Das X-Out-Verfahren hilft, Fehler frühzeitig zu identifizieren, was zu einer höheren Produktqualität und weniger Ausschuss führt.
Effiziente Aussortierung von defekten Bauteilen:
- Durch die Kennzeichnung der defekten Platinen können fehlerhafte Teile schnell und effizient aus der Produktion entfernt werden.
Vermeidung von weiteren Fehlern:
- Durch das Markieren und Aussortieren der defekten Teile wird verhindert, dass Fehler in späteren Produktionsstufen oder in den Endprodukten auftreten.
Fazit:
Das X-Out-Verfahren ist eine wichtige Maßnahme in der Qualitätssicherung der Elektronikproduktion, um fehlerhafte Platinen schnell zu identifizieren und den Ausschuss zu minimieren. Es ermöglicht eine präzise Fehlerbehandlung und hilft dabei, die Effizienz und Qualität in der Fertigung zu steigern.
Anwendung von X-Ray in der Elektronikfertigung:
Inspektion von Lötstellen:
- X-Ray-Systeme werden verwendet, um Lötstellen auf Leiterplatten zu überprüfen, insbesondere bei Bauteilen, die eine Verbindung zwischen mehreren Schichten benötigen, wie z.B. BGA (Ball Grid Array) und CSP (Chip-on-Board). Diese Bauteile sind nicht von oben sichtbar, sodass Röntgenstrahlen die Verbindungen durch die Leiterplatte durchdringen und detaillierte Bilder der Lötstellen und der inneren Strukturen liefern.
Fehlererkennung bei durchkontaktieren Bauteilen:
- X-Ray hilft, Defekte wie kalte Lötstellen, fehlende Lötverbindungen, Brückenbildung zwischen den Lötpads und fehlerhafte Durchkontaktierungen zu erkennen. Dies ist besonders wichtig, da solche Fehler die elektrische Funktion der Platinen beeinträchtigen können.
Untersuchung von Bauteilen im Inneren:
- Bei komplexen Bauteilen oder Multi-Chip-Modulen kann X-Ray verwendet werden, um sicherzustellen, dass keine inneren Schäden wie Risse, Luftblasen oder Fehler in der Verpackung vorliegen.
Verpackungsinspektion:
- Bei der Produktion von Chips und Bauteilen wird X-Ray auch verwendet, um die Qualität der Chipverpackungen und deren Dichte zu prüfen. Dies ist wichtig für die Sicherstellung der Haltbarkeit und Leistungsfähigkeit von Bauteilen in Geräten.
Aufdeckung von Mängeln in mehrlagigen Leiterplatten:
- X-Ray wird auch zur Überprüfung der Integrität von mehrlagigen Leiterplatten (Multilayer-PCBs) eingesetzt. Es hilft bei der Beurteilung der Qualität der Inneren Lötverbindungen und beim Aufspüren von Problemen wie fehlerhaften Bohrungen oder schlechten Verbindungen in den verschiedenen Schichten.
Vorteile von X-Ray in der Elektronikfertigung:
Nicht-invasive Inspektion:
- Röntgeninspektion ermöglicht eine gründliche Untersuchung der Platinen und Bauteile, ohne dass diese auseinandergebaut oder beschädigt werden müssen. Dies spart Zeit und reduziert den Ausschuss.
Präzise Fehlererkennung:
- X-Ray bietet eine detaillierte Ansicht von Fehlern, die mit anderen Inspektionsmethoden (wie optischen Verfahren) nicht erkennbar wären. Dies ist besonders nützlich bei Bauteilen mit verdeckten Lötstellen und Verbindungen.
Erhöhung der Produktqualität:
- Durch den Einsatz von X-Ray können Fehler frühzeitig im Produktionsprozess erkannt und behoben werden, was zu einer höheren Endproduktqualität führt.
Erhöhung der Effizienz der Qualitätskontrolle:
- X-Ray-Systeme können schnell und präzise mehrere Leiterplatten oder Bauteile gleichzeitig überprüfen, was die Effizienz der Qualitätskontrolle steigert.
Fazit:
Der Einsatz von X-Ray-Technologie in der Elektronikfertigung hat die Qualitätskontrolle erheblich verbessert, indem er eine präzise, schnelle und nicht-invasive Möglichkeit zur Inspektion von Bauteilen und Leiterplatten bietet. Durch die Entdeckung von Fehlern, die mit herkömmlichen Inspektionsmethoden nicht sichtbar wären, trägt X-Ray zur Optimierung der Produktion und zur Minimierung von Defekten in Endprodukten bei.
- YIELD
Yield ist ein Begriff, der in der Fertigung, insbesondere in der Elektronik- und Leiterplattenproduktion, verwendet wird und die Anzahl der fehlerfreien Einheiten oder Produkte im Verhältnis zur Gesamtproduktion beschreibt. Ein hoher Yield bedeutet, dass ein Großteil der hergestellten Teile den Qualitätsanforderungen entspricht, während ein niedriger Yield auf eine höhere Anzahl von Fehlern oder Ausschuss hinweist.
Wichtige Aspekte des Yields in der Elektronikfertigung:
Definition und Berechnung:
- Der Yield wird oft als Prozentsatz der fehlerfreien Einheiten im Verhältnis zur Gesamtproduktion berechnet. Eine einfache Formel lautet: Yield=(Fehlerfreie EinheitenGesamtproduktion)×100\text{Yield} = \left( \frac{\text{Fehlerfreie Einheiten}}{\text{Gesamtproduktion}} \right) \times 100Yield=(GesamtproduktionFehlerfreie Einheiten)×100
- Ein Yield von 95% bedeutet, dass 95% der produzierten Teile fehlerfrei sind und 5% Ausschuss darstellen.
Faktoren, die den Yield beeinflussen:
- Prozessfehler: Fehler, die während der Fertigung entstehen, wie ungenaue Bohrungen, Lötfehler oder Materialfehler.
- Designfehler: Fehler, die bereits in der Entwurfsphase einer Leiterplatte oder eines elektronischen Bauteils auftreten, wie unzureichende Leiterbahnbreiten oder falsche Bauteilplatzierung.
- Ausrüstungsgenauigkeit: Die Genauigkeit und Kalibrierung der Fertigungsmaschinen kann den Yield beeinflussen. Maschinenfehler oder Abnutzung können zu Defekten führen.
- Qualität des Materials: Niedrigwertige Materialien oder inkonsistente Materialchargen können ebenfalls zu Defekten und einem niedrigeren Yield führen.
Yield-Optimierung:
- Prozesskontrolle: Regelmäßige Überwachung und Optimierung der Fertigungsprozesse, um Fehler zu minimieren und die Konsistenz zu gewährleisten.
- Design for Manufacturability (DFM): Berücksichtigung der Fertigungsmöglichkeiten und -grenzen bereits in der Entwurfsphase, um die Produktionskosten zu senken und den Yield zu maximieren.
- Fehleranalyse und -behebung: Eine detaillierte Analyse von Fehlerquellen, wie etwa die Untersuchung von Fehlstellen in der Lötung oder die Prüfung der Schaltungsintegrität, um die Ursachen für Defekte zu verstehen und zu beseitigen.
Bedeutung des Yields in der Produktion:
- Ein hoher Yield ist entscheidend für die Reduzierung der Produktionskosten und den Erfolg eines Herstellers. Ein hoher Yield bedeutet weniger Ausschuss, weniger Nacharbeit und weniger Materialverschwendung, was die Gesamtkosten senkt.
- Ein niedriger Yield weist auf häufige Fehler hin, was zu höheren Produktionskosten und längeren Lieferzeiten führt.
Yield im Zusammenhang mit BGA und anderen modernen Bauteilen:
- Bei Bauteilen wie BGA (Ball Grid Array) oder CSP (Chip-on-Board) ist der Yield besonders kritisch, da diese Bauteile interne Lötstellen besitzen, die nicht mit bloßem Auge sichtbar sind und mit herkömmlichen optischen Inspektionsmethoden schwer zu überprüfen sind. Hier wird häufig auf Röntgeninspektion zurückgegriffen.
Fazit:
Der Yield ist ein zentraler Indikator für die Qualität und Effizienz der Produktion in der Elektronikfertigung. Ein hoher Yield stellt sicher, dass die Fertigung wirtschaftlich und qualitativ hochwertig ist, während ein niedriger Yield auf erhebliche Probleme im Fertigungsprozess hinweisen kann. Durch kontinuierliche Prozessverbesserung und präventive Maßnahmen zur Fehlervermeidung kann der Yield optimiert werden, was zu einer besseren Produktqualität und geringeren Produktionskosten führt.
- Z-FRÄSUNG
- ZINN-STRIPPEN
- ZWEISEITIGE LEITERPLATTE
Z-Fräsung bezeichnet ein Verfahren in der Fertigung, bei dem Material in vertikaler Richtung (Z-Achse) entfernt wird, um eine präzise Bearbeitung von Leiterplatten oder anderen Bauteilen zu erreichen. In der Elektronikfertigung wird die Z-Fräsung oft für bestimmte Anwendungen wie das Erzeugen von Vertiefungen, Konturen oder die Bearbeitung von Bohrungen in Leiterplatten verwendet.
Wichtige Aspekte der Z-Fräsung:
Funktionsweise der Z-Fräsung:
- Bei der Z-Fräsung wird ein Fräswerkzeug entlang der Z-Achse (vertikal) über das Werkstück geführt, um Material in eine bestimmte Tiefe zu fräsen. Dies kann entweder in einem einmaligen Schritt oder schrittweise erfolgen.
- Die Fräse bewegt sich dabei vertikal, während das Werkstück (die Leiterplatte) in der Regel auf einem Tisch oder einer Arbeitsplatte fixiert bleibt. Diese Technik ermöglicht eine präzise Bearbeitung, da die Tiefe und Form der Fräsung genau kontrolliert werden können.
Verwendungszwecke der Z-Fräsung in der Elektronikfertigung:
- Fräsen von Vertiefungen: Z-Fräsung wird verwendet, um Vertiefungen für Bauteile wie THT (Through-Hole Technology)-Pin-Verbindungen oder für Lötstopplack-Markierungen zu schaffen.
- Konturfräsen: Um die äußeren Konturen von Leiterplatten zu bearbeiten, vor allem bei der Herstellung von Prototypen oder bei der Bearbeitung von speziellen Leiterplattenformaten.
- Vias und Bohrungen: In einigen Fällen wird Z-Fräsung auch verwendet, um das Innere von Bohrungen oder Vias (Durchkontaktierungen) zu bearbeiten, um beispielsweise die Wandstärke oder Form zu optimieren.
Techniken und Tools:
- Die Z-Fräsung erfolgt typischerweise mit Fräsmaschinen, die speziell für die Bearbeitung von Leiterplatten ausgelegt sind. Diese Maschinen bieten eine hohe Präzision, die notwendig ist, um die kleineren Leiterbahnen und empfindlichen Bauteile zu schützen.
- Fräswerkzeuge für die Z-Fräsung variieren je nach Anforderung und Material. Für die Bearbeitung von Leiterplatten werden häufig spezialisierte Diamantfräser oder Hartmetallfräser eingesetzt, die eine hohe Standzeit und Genauigkeit bieten.
Vorteile der Z-Fräsung:
- Präzision: Z-Fräsung ermöglicht eine sehr genaue Materialabtragung, was besonders wichtig für die Herstellung von Leiterplatten mit engen Toleranzen und fein strukturierten Mustern ist.
- Flexibilität: Z-Fräsung eignet sich für eine Vielzahl von Anwendungen, sowohl für die Bearbeitung von Einzelstücken als auch für die Serienfertigung von Leiterplatten.
- Geringe Wärmeentwicklung: Im Vergleich zu anderen Bearbeitungsverfahren, wie dem Laserschneiden, erzeugt die Z-Fräsung weniger Wärme, was das Risiko von Materialveränderungen oder thermischen Beschädigungen reduziert.
Herausforderungen der Z-Fräsung:
- Materialverschwendung: Da Material abgetragen wird, können Z-Fräsprozesse zu einer gewissen Menge an Abfall führen, insbesondere bei komplexen Fräsungen.
- Langsame Bearbeitung: Je nach Komplexität und Tiefe der Fräsung kann der Prozess zeitaufwendig sein, was die Produktionsgeschwindigkeit beeinträchtigen kann.
Fazit:
Die Z-Fräsung ist eine präzise und vielseitige Methode zur Bearbeitung von Leiterplatten, die in der Elektronikfertigung eingesetzt wird, um Vertiefungen, Konturen und Bohrungen zu erstellen. Durch die Kontrolle der Frästiefe und die Wahl des richtigen Werkzeugs kann eine hohe Genauigkeit erreicht werden, was sie zu einem wichtigen Verfahren für die Herstellung hochwertiger und funktionaler Leiterplatten macht.
Vgl. auch → Tiefenfräsung
Zinn-Strippen bezieht sich auf einen Prozess in der Elektronikfertigung, bei dem Zinn, das auf Leiterplatten oder Bauteilen aufgetragen wurde, entfernt wird. Diese Technik wird häufig eingesetzt, um überschüssiges Zinn nach dem Lötprozess zu entfernen oder um ungewollte Zinnablagerungen zu beseitigen, insbesondere in Bereichen, in denen das Zinn die Funktionalität oder die optische Erscheinung beeinträchtigen könnte.
Wichtige Aspekte der Zinn-Strippen:
Prozessbeschreibung:
- Beim Zinn-Strippen wird das Zinn durch chemische oder mechanische Verfahren entfernt. In der Regel wird dies durch den Einsatz von Strippenmitteln (chemische Lösungen) oder durch elektrolytische Verfahren erreicht.
- Der Prozess kann nach dem Löten durchgeführt werden, wenn überschüssiges Zinn auf den Leiterplatten oder an den Lötstellen vorhanden ist, das nicht gewünscht wird oder die Qualität der Lötstellen beeinträchtigen könnte.
Methoden des Zinn-Strippen:
Chemisches Strippen: Hierbei wird ein chemisches Lösungsmittel eingesetzt, das das Zinn angreift und es von der Leiterplatte oder den Bauteilen löst. Dies kann durch ein spezielles Entzinnungsbad oder durch den Einsatz von speziellen Strippenlösungen erfolgen, die auf die betroffenen Stellen aufgetragen werden.
Elektrolytisches Strippen: Diese Methode nutzt eine elektrolytische Zelle, bei der das Zinn als Anode fungiert und unter Anwendung von elektrischem Strom vom Bauteil abgetragen wird. Diese Technik ist oft präziser und kontrollierbarer als chemische Methoden.
Mechanisches Strippen: In einigen Fällen kann das Zinn durch mechanische Bearbeitung wie Schleifen oder Bürsten entfernt werden, besonders bei größeren Zinnablagerungen oder bei der Entfernung von Zinn von Bauteilen wie Pins oder Anschlüssen.
Verwendung von Zinn-Strippen:
Nach dem Löten: Während des Lötens wird Zinn oft in Form von Lötzinn verwendet, um Bauteile auf der Leiterplatte zu verbinden. Zinn-Strippen wird verwendet, um überschüssiges oder ungewolltes Zinn zu entfernen, das möglicherweise Kurzschlüsse verursacht oder das Bauteil beschädigen könnte.
Vor der Wiederverwendung von Bauteilen: In der Reparatur- und Wiederverwendungsindustrie wird Zinn-Strippen verwendet, um Bauteile, insbesondere SMD– oder THT-Bauteile, von überflüssigem Zinn zu befreien, bevor sie erneut verwendet oder auf eine neue Leiterplatte gelötet werden.
Vorteile des Zinn-Strippen:
Saubere Lötstellen: Das Entfernen von überschüssigem Zinn trägt dazu bei, dass die Lötstellen sauber und frei von unerwünschten Zinnablagerungen bleiben, was die elektrische Leistung und Zuverlässigkeit der Leiterplatte verbessert.
Wiederverwendbarkeit: Bauteile können nach dem Zinn-Strippen wiederverwendet werden, was die Materialkosten reduziert und die Umweltauswirkungen der Fertigung minimiert.
Vermeidung von Kurzschlüssen: Überschüssiges Zinn kann unerwünschte Verbindungen zwischen benachbarten Leiterbahnen oder Bauteilen verursachen. Das Zinn-Strippen hilft, solche Kurzschlüsse zu verhindern.
Herausforderungen beim Zinn-Strippen:
Materialbeschädigung: Bei unsachgemäßer Anwendung von chemischen oder mechanischen Strippenverfahren kann es zu Beschädigungen der Leiterplatte oder Bauteile kommen. Daher muss der Prozess sorgfältig kontrolliert werden.
Umweltrisiken: Chemische Strippenmittel können gefährlich sein und müssen ordnungsgemäß gehandhabt und entsorgt werden, um Umweltschäden zu vermeiden.
Fazit:
Zinn-Strippen ist ein nützlicher Prozess in der Elektronikfertigung, um überschüssiges Zinn zu entfernen und sicherzustellen, dass Leiterplatten und Bauteile korrekt und funktional sind. Es trägt dazu bei, die Qualität der Lötverbindungen zu gewährleisten und die Lebensdauer von Bauteilen zu verlängern, indem es ungewollte Zinnablagerungen beseitigt.
Zweiseitige Leiterplatte bezieht sich auf eine Leiterplatte (PCB), die mit elektrischen Verbindungen (Leiterbahnen) auf beiden Seiten der Platine versehen ist. Diese Art von Leiterplatte wird häufig in der Elektronikindustrie verwendet, da sie eine größere Anzahl von Verbindungen und Schaltungen auf begrenztem Raum ermöglicht, ohne die Platine unnötig dick oder komplex zu gestalten.
Merkmale einer zweiseitigen Leiterplatte:
Leiterbahnen auf beiden Seiten: Eine zweiseitige Leiterplatte hat auf beiden Seiten der Platine Leiterbahnen, die die Bauteile miteinander verbinden. Dies ermöglicht die Verwendung von mehr Verbindungen, was vor allem bei komplexeren Schaltungen vorteilhaft ist.
Durchkontaktierungen (Vias): Um die Verbindungen zwischen den beiden Seiten der Platine herzustellen, werden Vias verwendet. Diese kleinen Bohrungen werden durch die gesamte Platine geführt und ermöglichen es, Leiterbahnen auf der einen Seite mit denen auf der anderen Seite zu verbinden. Vias können entweder als Durchgangs-Vias (THV) oder als Blind-Vias und Buried-Vias (je nach ihrer Position in der Platine) ausgeführt sein.
Bestückung: Zweiseitige Leiterplatten können mit Bauteilen auf beiden Seiten bestückt werden. Dies ermöglicht eine höhere Packungsdichte von Bauteilen, was besonders bei kleinen Geräten oder tragbaren Elektronikgeräten von Vorteil ist.
Verwendung von Lötstopplack: Auf den Leiterplatten wird in der Regel ein Lötstopplack aufgebracht, um sicherzustellen, dass nur die gewünschten Lötflächen (Pads) auf den Leiterplattenoberflächen freigelegt sind und keine ungewollten Verbindungen entstehen.
Vorteile einer zweiseitigen Leiterplatte:
Höhere Dichte und Komplexität: Da sowohl die Vorder- als auch die Rückseite genutzt werden können, bietet eine zweiseitige Leiterplatte mehr Platz für Leiterbahnen und Bauteile. Dies macht sie ideal für komplexe Schaltungen, bei denen der Platz begrenzt ist.
Kosteneffizienz: Zweiseitige Leiterplatten sind eine kostengünstigere Lösung im Vergleich zu mehrlagigen (Multilayer-)Platten, wenn die Schaltung eine höhere Komplexität erfordert, aber die Notwendigkeit für viele Schichten nicht besteht.
Flexibilität: Zweiseitige Leiterplatten bieten eine gute Balance zwischen Komplexität und Herstellkosten und ermöglichen es, die Schaltung auf beiden Seiten zu optimieren.
Geringere Platzanforderungen: Durch die Nutzung beider Seiten für Leiterbahnen und Bauteile können zweiseitige Leiterplatten eine größere Funktionalität auf kleinerem Raum bieten.
Herstellung einer zweiseitigen Leiterplatte:
Laminierung der Kupferschicht: Eine Kupferschicht wird auf beide Seiten eines Basismaterials (häufig FR4) laminiert. Diese Kupferschicht dient als Grundlage für die Leiterbahnen.
Fotolithografie und Ätzen: Wie bei einseitigen Leiterplatten wird auf beiden Seiten ein Fotolithografieprozess angewendet, bei dem unerwünschtes Kupfer entfernt wird, um die Leiterbahnen zu formen. Dieser Prozess erfolgt auf beiden Seiten der Platine.
Bohren der Vias: Die Bohrungen werden durchgeführt, um die elektrischen Verbindungen zwischen den beiden Seiten zu ermöglichen. Diese Vias können entweder manuell oder durch automatisierte Maschinen gebohrt werden.
Verkappung und Bestückung: Nachdem die Leiterbahnen und Vias bearbeitet wurden, wird die Platine mit Bauteilen bestückt, und der Lötprozess erfolgt.
Anwendungen:
Zweiseitige Leiterplatten sind weit verbreitet und finden Anwendung in:
- Consumer-Elektronik: In vielen elektronischen Geräten wie Handys, Computern und Haushaltsgeräten werden zweiseitige Leiterplatten eingesetzt.
- Medizinische Geräte: Diese Platinen sind auch in medizinischen Geräten, wie z.B. tragbaren Monitoren, zu finden.
- Automobilindustrie: Zweiseitige Leiterplatten werden häufig in der Automobiltechnik verwendet, um komplexe Schaltungen auf begrenztem Raum zu integrieren.
Fazit:
Zweiseitige Leiterplatten bieten eine ausgezeichnete Lösung für Anwendungen, die eine höhere Dichte an Bauteilen und Verbindungen erfordern, aber dennoch kostengünstig und einfach in der Herstellung sein sollen. Sie sind ein wichtiger Bestandteil der modernen Elektronikproduktion und ermöglichen es, leistungsstarke und kompakte Geräte zu schaffen.
Haben wir Ihr Interesse geweckt? Wir begleiten Sie gerne, geht es darum, die Integration von innovativer Elektronik in den Alltag zu ermöglichen.